Advanced Inventory Management in the Food Industry
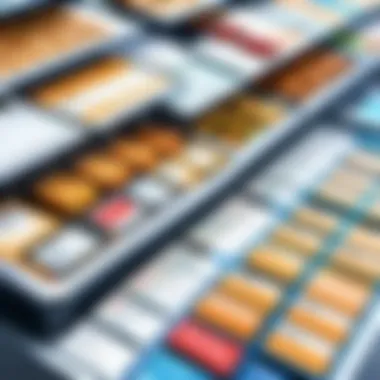
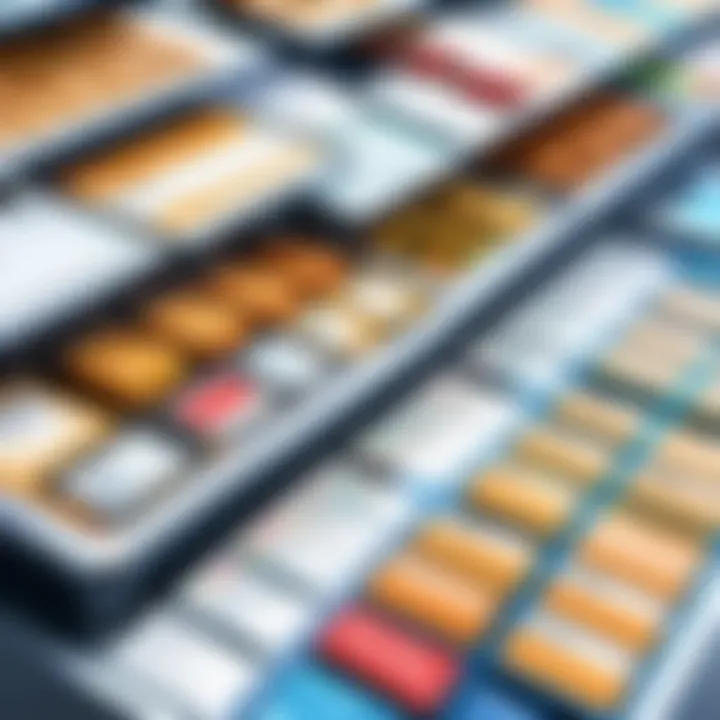
Intro
Inventory management plays a crucial role in the food industry. Efficient inventory systems ensure that businesses meet customer demands while minimizing waste. Understanding the dynamics of inventory management is essential for decision-makers aiming to adapt to changing market conditions. This section introduces the fundamental aspects of inventory management, emphasizing its importance within the context of the food industry.
In this article, we will delve into advanced strategies that enhance inventory efficiency. We will cover various aspects such as real-time data collection, tracking systems, and demand forecasting methods. Moreover, we will explore the technological advancements reshaping inventory management, backed by research and case studies relevant to industry professionals.
Software Category Overview
Definition and Importance
Software solutions for inventory management are designed to simplify and optimize stock control processes. These systems provide businesses with the tools needed to track inventory levels, monitor stock movements, and forecast demand accurately. The significance of using such software is evident in its ability to reduce human error, streamline operations, and improve overall decision-making within the business.
Key Characteristics
When evaluating inventory management software, several key characteristics should be considered. These include:
- Real-Time Tracking: Ensures up-to-date information on stock levels and location.
- Integration Capabilities: Ability to connect with other systems like POS or supply chain management tools.
- User-Friendly Interface: Designed for ease of use, enabling quick training and adoption by staff.
- Reporting and Analytics Tools: Provides insightful data for better decision-making.
- Scalability: Flexibility to adapt as the business grows or changes.
Comparative Analysis of Top Software Options
Feature Comparison
In selecting the right inventory management software, it is essential to compare features offered by different solutions. For example:
- Fishbowl Inventory: Known for its robust inventory tracking features, including integration with QuickBooks.
- TradeGecko: Encompasses detailed reporting and order management functionalities, catering to e-commerce needs.
- Square for Restaurants: Focuses on the urgent demands of the restaurant sector with real-time stock updates and menu management.
Pricing Models
Pricing can significantly impact the choice of inventory management software. Different models are available:
- Subscription-based Pricing: Monthly fees, usually with tiered plans based on features required.
- One-Time Purchase: A single payment for perpetual software usage.
- Freemium Models: Offers basic functionalities at no cost, with the option to upgrade for advanced features.
Choosing the right software requires careful consideration. It is vital to assess the unique needs of your business and how the software can address those requirements effectively.
Preamble to Inventory Management in the Food Industry
In the food industry, effective inventory management is crucial for ensuring sustainability, efficiency, and profitability. Proper inventory management allows businesses to track their stock levels accurately while minimizing waste and maintaining quality. Given the perishable nature of many food products, a robust system is essential to prevent losses and meet customer demand.
Additionally, businesses often face fluctuating demand based on seasons or trends. Thus, a dynamic inventory system helps organizations adjust accordingly. With food safety regulations and quality standards constantly evolving, maintaining an organized inventory is a fundamental part of compliance.
Ultimately, an optimized inventory management process can lead to reduced costs and boosted customer satisfaction. Companies can benefit from technologies that facilitate real-time insights, enabling smarter decision-making practices. As the industry continues to grow and diversify, understanding sophisticated inventory management becomes increasingly relevant for all stakeholders involved.
Significance of Inventory Management
Inventory management in the food industry has significant implications that can affect both operations and customer satisfaction. When inventory is mismanaged, it can lead to overstocking or understocking. Over time, this can increase costs associated with storage, waste, and spoilage. On the other hand, understocking leads to missed opportunities and dissatisfied customers when their orders cannot be fulfilled on time.
Furthermore, the effective tracking of food items ensures that businesses comply with food safety regulations. Knowing where products are in the supply chain helps organizations adhere to standards regarding recalls and traceability. Building a responsive inventory management framework allows companies to deliver quality products and maintain consumer trust. The benefits also extend to fiscal outcomes; less waste translates into higher profit margins.
Overview of Current Practices
Current practices in inventory management for the food industry largely focus on leveraging technology and data analytics. Many businesses utilize inventory management software platforms that provide comprehensive tracking and reporting capabilities. This technology allows companies to automate many processes that used to be manual and time-consuming.
Among common practices are:
- Just-In-Time (JIT) Inventory: This minimizes on-hand stock and reduces the risk of spoilage.
- First-In, First-Out (FIFO): This approach ensures older stock is sold before newer inventory, reducing waste.
- Real-Time Tracking: Scanning items with barcode or RFID technology enables real-time inventory updates, improving accuracy in stock levels.
Nevertheless, despite technological advancements, challenges persist in execution due to the inherent complexity of the food supply chain. Businesses continue to explore innovative solutions to tackle these hurdles, stressing the importance of ongoing improvement and adaptability in inventory management strategies.
Key Challenges in Food Inventory Management
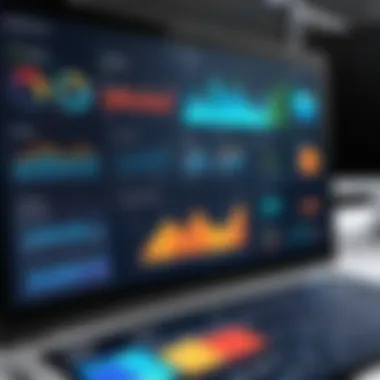
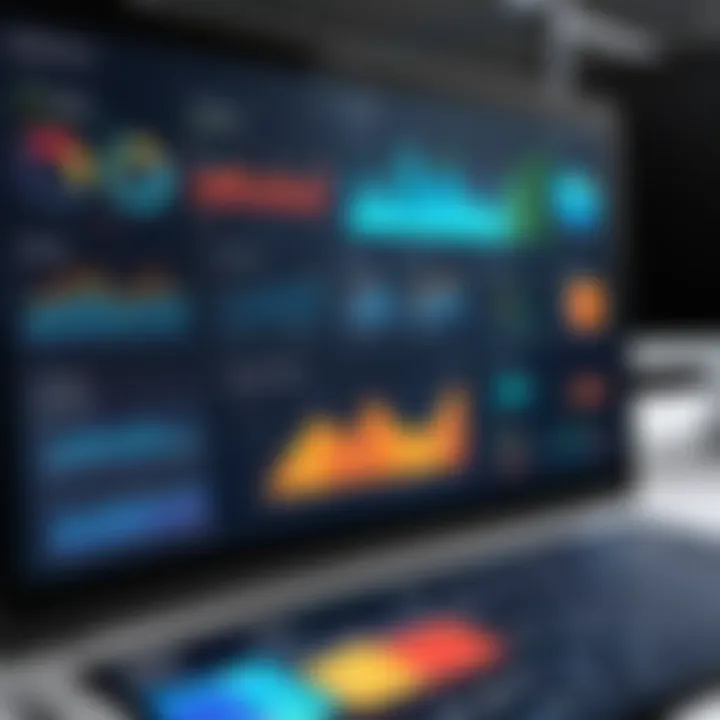
Understanding the key challenges in food inventory management is crucial for businesses seeking to enhance their operational efficiency and meet consumer demands. The food industry faces unique obstacles that can significantly impact the quality and availability of products. Addressing these challenges leads to better inventory control, decreased waste, and ultimately increased profitability. It is vital for decision-makers to comprehend the nuances of these issues, allowing them to implement effective strategies that mitigate risks and leverage opportunities in the marketplace.
Perishable Goods Management
Managing perishable goods is perhaps the most daunting challenge in inventory management within the food industry. Perishable items, such as fruits, vegetables, dairy products, and meats, require careful attention due to their limited shelf life. The risk of spoilage escalates if these items are not properly managed. To mitigate this risk, businesses should prioritize proper temperature control and effective inventory rotation practices. For instance, implementing the First In, First Out (FIFO) method can ensure that older products are sold before newer ones, maximizing freshness and minimizing waste.
Many companies invest in technology solutions that enable better tracking of perishable inventory. Real-time data analytics can provide insights into inventory levels, helping businesses to predict demand accurately. This can lead to smarter purchasing decisions that align with actual sales patterns.
Supply Chain Disruptions
Supply chain disruptions pose another significant threat to effective inventory management. This can stem from various factors such as natural disasters, geopolitical issues, or labor shortages. When disruptions occur, it can lead to product shortages or increased costs, affecting the entire supply chain from producers to retailers.
To combat this, companies must invest in a robust risk management strategy. Diversifying suppliers is one effective approach, as it mitigates the dependency on a single source. Companies should also establish strong communication channels with suppliers to quickly address any potential disruptions and prepare contingency plans. Maintaining safety stock can also provide a buffer against unpredictable events.
"Companies that proactively manage supply chain risks can better navigate disruptions and maintain supply continuity."
Regulatory Compliance Issues
Regulatory compliance is a critical challenge facing the food industry, particularly as regulations continue to evolve in response to health concerns and food safety standards. Businesses must ensure that their inventory management practices comply with food safety regulations to avoid legal issues and protect consumers.
This requires rigorous record-keeping and regular audits. Companies often turn to advanced inventory management software to help track compliance. Such systems can automate many processes, ensuring that critical data such as expiration dates, sourcing information, and storage conditions are continuously monitored. These tools not only simplify compliance but also enhance overall operational efficiency.
The Role of Technology in Inventory Management
Technology has increasingly become an integral part of inventory management in the food industry. The advancement in technological solutions offers a systematic approach to handle complex inventory challenges. By embracing technology, businesses can enhance their operational efficiency, reduce errors, and streamline processes. This transformation is particularly relevant given the perishable nature of food products, where the slightest delay or miscalculation can lead to significant waste and loss. Thus, technology not only supports the existing frameworks but also introduces innovative methodologies that align with contemporary business needs.
Inventory Management Software Solutions
Inventory management software is vital for businesses aiming to maintain control over their stock levels. Solutions like Fishbowl Inventory, NetSuite, and SAP Business One provide robust features that facilitate monitoring of products throughout their lifecycle. These tools enable users to track stock in real time, generate valuable reports, and manage orders effectively. They serve as a centralized hub where data is stored and analyzed, helping decision-makers understand stock trends and make informed choices.
Moreover, the integration of these software solutions with accounting systems maximizes productivity. Businesses can automate accounting processes related to inventory, reducing manual entry and the likelihood of human error. The ability to maintain accurate records of inventory levels and transactions is essential for efficient operations in a sector where discrepancy can lead to regulatory issues and customer dissatisfaction.
Importance of Real-Time Data
Real-time data plays a crucial role in managing inventory efficiently. Modern inventory systems gather and analyze data continuously. This immediate access to information allows businesses to react swiftly to changes in demand or supply chain fluctuations. For instance, if a product is running low, alerts can be sent out to procure more before stocks run dry.
Furthermore, by utilizing real-time data analytics, businesses can refine their demand forecasting techniques. Understanding customer preferences and seasonal trends aids in maintaining optimal stock levels, ensuring that popular items are always available while reducing excess inventory. The agility offered by real-time data directly influences a company's ability to respond to the dynamic market conditions characteristic of the food industry.
Automation and Efficiency
Automation is at the heart of increasing efficiency within the inventory management process. Implementing automated systems for order processing, stock tracking, and restocking helps eliminate manual tasks that can bog down operations. Tools such as automated replenishment systems, which reorder stock based on predefined thresholds, ensure smooth operation and reduce the burden on staff.
Additionally, automated inventory tracking using technologies like RFID and barcode scanning enhances accuracy and speed. Workers can focus on more valuable tasks, knowing that the tracking systems accurately reflect stock changes in real time.
"Automation in inventory management has reduced human error significantly while increasing processing speeds. Companies that leverage this technology can serve customers better and reduce operational costs."
In summary, technology has reshaped inventory management in the food industry. By leveraging sophisticated software, real-time data, and automation, businesses can navigate complexities with greater ease. This technological approach not only enhances efficiency but sets a solid foundation for adapting to future challenges in the food sector.
Strategies for Efficient Inventory Tracking
Efficient inventory tracking is crucial for the food industry. This sector deals with perishable goods, where tracking can determine profitability and minimize waste. With accurate tracking strategies, businesses can optimize stock levels and ensure freshness. Effective tracking methods support decision-making about purchasing and pricing. This section explores key approaches to tracking, including the utilization of barcode and RFID technologies, cycle counting methods, and inventory audits and controls. Each method offers unique benefits and considerations that can significantly impact inventory efficiency.
Barcode and RFID Technologies
Barcode and RFID (Radio Frequency Identification) technologies are essential for enhancing inventory tracking. Barcodes provide a straightforward method for labeling products, making identification easy with a scanner. This approach reduces human error and speeds up the checkout process. On the other hand, RFID goes a step further by allowing automatic tracking of inventory items through radio waves.
Key Benefits of Using Barcode and RFID Technologies:
- Speed: Automated scanning processes allow for quick inventory counts and item identification.
- Accuracy: Reduces chances of human errors compared to manual entry.
- Visibility: RFID technology gives a real-time view of inventory levels and location.
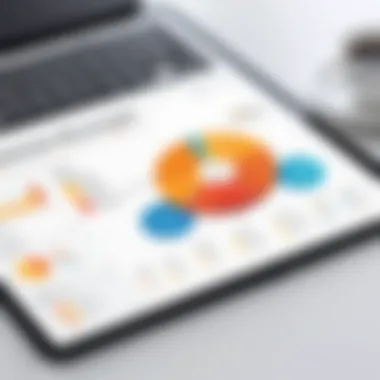
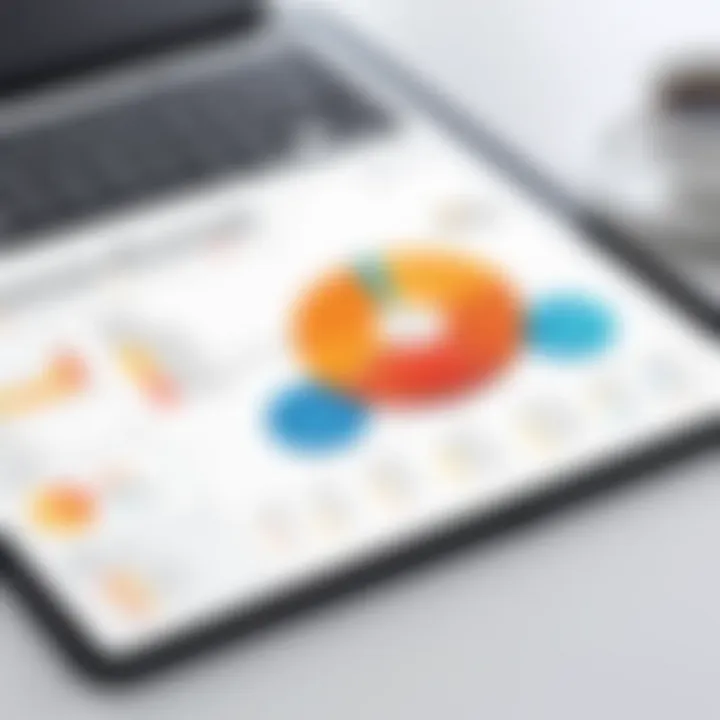
Nevertheless, implementing these technologies requires investment in equipment and training for staff to maximize efficacy.
Cycle Counting Methods
Cycle counting is a systematic inventory auditing process where a selected subset of inventory is counted on a specific day. This method is less disruptive than full inventory counts and leads to more accurate stock levels over time.
Benefits of Cycle Counting:
- Regular Updates: Frequent counts keep inventory data accurate, which helps in decision-making.
- Identification of Discrepancies: Cycle counting helps in spotting issues like theft, damage, or inaccurate records.
- Resource Efficiency: Reduces the labor and downtime needed for full inventory counts, thus leading to minimal disruption to operations.
Inventory Audits and Controls
Inventory audits are critical for ensuring the accuracy of stock levels. Regular audits help in validating inventory records against physical counts. Additionally, establishing strong inventory controls can safeguard against theft and ensure compliance with regulatory standards related to food safety.
Important Steps in Conducting Inventory Audits:
- Planning the Audit: Set clear objectives and timelines to keep the process organized.
- Gathering Data: Use technology to collect data effectively during audits.
- Analyzing Results: Compare findings against records and investigate discrepancies.
Implementing strict controls and regular audits can significantly enhance the reliability of inventory systems.
Demand Forecasting Techniques
Understanding demand forecasting techniques is essential for effective inventory management in the food industry. It allows businesses to predict customer demand accurately, enabling them to stock appropriate levels of inventory, minimize waste, and reduce costs. The insights gained through demand forecasting inform purchasing decisions and can lead to more efficient operational practices.
Historical Data Analysis
Historical data analysis serves as a foundation for demand forecasting. By examining past sales data, businesses can identify patterns and trends that help predict future demand. This analysis takes into account seasonal fluctuations, promotions, and other factors that may have influenced sales in the past.
- Data Sources: Businesses should gather data from different periods, ensuring that the dataset reflects various conditions, such as holidays or promotional periods. This comprehensive data helps in building a more accurate forecast.
- Quantitative Techniques: Techniques such as time series analysis allow businesses to apply statistical methods to historical data. These methods help identify trends and seasonality in sales.
- Benefits: Utilizing historical data leads to informed decisions about inventory levels, reducing the chances of overstocking or stockouts. A focused analysis helps businesses to align their inventory more closely with actual customer needs.
Market Trends and Customer Insights
Alongside historical data, market trends and customer insights are valuable components of demand forecasting. Understanding shifts in consumer preferences and industry trends allows businesses to adapt their inventory strategies accordingly.
- Market Research: Conducting market research is crucial. This can include surveys, focus groups, or analyzing social media trends. Gaining insights into customer preferences helps businesses to anticipate changes in demand.
- Economic Indicators: Businesses should consider external factors such as economic conditions, competitor actions, and market saturation. These indicators can greatly influence customer behavior and buying patterns.
- Benefits: By integrating market trends into the forecasting process, businesses can better position themselves within the market. It enables them to tailor their offerings, ensuring they stay competitive and responsive to consumer demands.
In summary, effective demand forecasting techniques bridge the gap between customer expectations and inventory levels. This strategic approach allows food industry professionals to enhance operational efficiency and respond adeptly to market dynamics.
Case Studies: Successful Implementation of Inventory Systems
The implementation of effective inventory systems is crucial for the food industry. Case studies provide practical insights into how companies have overcome challenges and enhanced their inventory management processes. These studies serve as examples of best practices and innovations that can inspire other businesses to adopt similar strategies. They emphasize the importance of real-world applications and the benefits derived from successful systems.
Leading Food Retailers
Leading food retailers, such as Walmart and Costco, have transformed their inventory management processes through advanced technologies and practices. Walmart, for instance, utilizes a sophisticated inventory management system that integrates real-time data and predictive analytics. This system enables them to optimize stock levels across thousands of stores and respond quickly to changing consumer demand.
Through their Just-in-Time (JIT) approach, Walmart minimizes storage costs and reduces waste. Their collaboration with suppliers allows for seamless replenishment of products based on sales data. This method not only improves operational efficiency but also enhances customer satisfaction by ensuring product availability.
Similarly, Costco employs a limited selection strategy. By offering fewer products, Costco can maintain higher inventory turnover. They rely heavily on data analytics to forecast demand accurately. This method enables them to keep shelves stocked with items that are most popular while minimizing excess inventory.
The success of these retail giants illustrates the potential of data-driven inventory strategies in the food sector. Implementing technology like RFID tracking and real-time monitoring can yield significant benefits, including reduced waste and improved cash flow.
Food Production Facilities
Food production facilities face unique challenges in inventory management, particularly due to perishability and quality control. A notable case study involves Nestlé, which has successfully implemented an integrated inventory system across their production lines. This system relies on advanced monitoring tools and software that provide detailed insights into production processes and inventory levels.
Nestlé utilizes machine learning algorithms to forecast demand for various products accurately. This enables them to adjust production schedules dynamically and minimize overproduction. Moreover, their inventory system incorporates sustainability metrics, allowing them to track waste and optimize sourcing. This dual focus on efficiency and sustainability is becoming increasingly vital in today’s market.
Another example is the implementation of lean manufacturing principles by companies like Unilever. They focus on reducing inventory levels through better production scheduling and waste management. By employing lean techniques, Unilever has achieved significant cost savings and improved their responsiveness to changing market conditions.
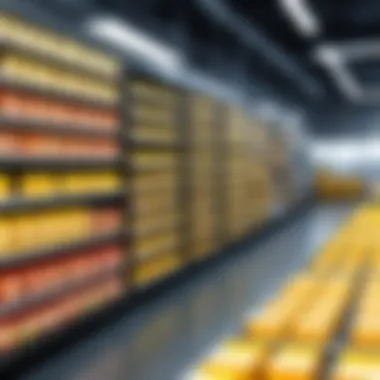
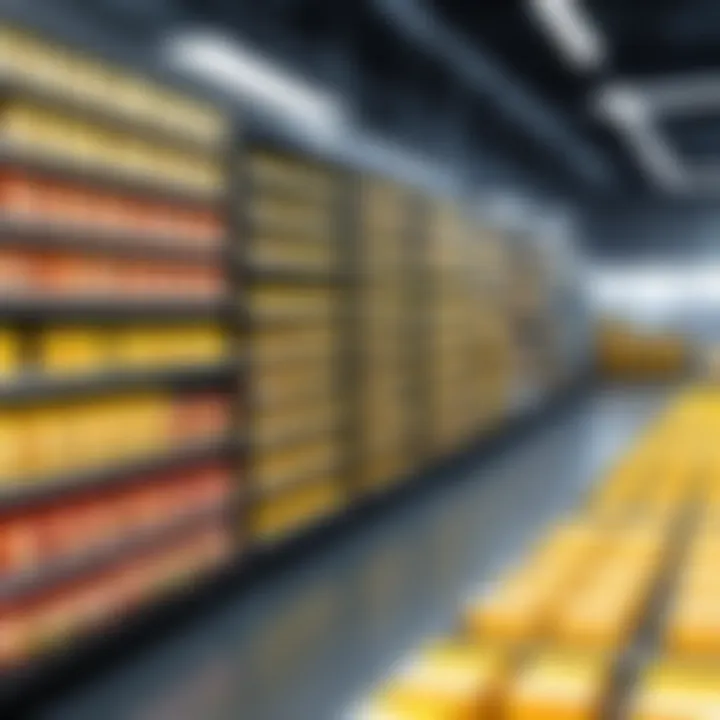
These case studies highlight the importance of a strategic approach to inventory management within food production facilities. The success stories of companies like Nestlé and Unilever emphasize not only the need for effective inventory systems but also the role of innovation and sustainability.
Successful implementation of inventory management systems leads to operational efficiency and substantial cost savings in the food industry.
The Impact of Sustainability on Inventory Management
Sustainability is increasingly becoming a fundamental aspect of business operations in the food industry. It goes beyond being a mere trend; organizations now recognize it as a core operational objective that enhances efficiency and profitability. Integrating sustainable practices into inventory management leads to multiple benefits, chiefly among them being the reduction of food waste, improved supply chain resilience, and enhanced brand reputation.
Reducing Food Waste
Food waste is a critical issue in the industry, not only for environmental reasons but also for financial ones. According to the Food and Agriculture Organization (FAO), approximately one-third of food produced globally is wasted. This waste not only represents lost revenue but also contributes significantly to greenhouse gas emissions.
To combat this, businesses must implement effective inventory strategies that focus on perishability and demand forecasting. Monitoring inventory levels in real-time aids organizations to minimize excess stock, thus preventing spoilage. Techniques such as FIFO (First In, First Out) can also help rotate products efficiently, ensuring older inventory is used before spoilage.
Moreover, engaging employees in training programs focused on food handling and inventory rotation practices can profoundly influence waste reduction. When staff are well-informed of sustainable practices, they are more likely to adhere to guidelines that promote efficiency.
"Reducing waste through effective inventory management is not just an ethical choice, it’s also an economic one."
Sustainable Sourcing Practices
Sustainable sourcing in inventory management entails selecting suppliers based not only on cost but also on their environmental and social practices. Companies are now recognizing the significance of sourcing local ingredients, which can reduce transportation emissions and align with consumer preferences for fresher products.
By working with local farmers and suppliers, businesses not only reduce their carbon footprint but also contribute to the local economy. Furthermore, establishing long-term relationships can yield reliability in supply and stable pricing.
In addition, it’s important for organizations to assess the sustainability credentials of their suppliers. This involves evaluating aspects such as ethical farming practices, use of chemicals, and overall sustainability certifications. By integrating these criteria into vendor selection processes, companies can enhance their overall supply chain sustainability.
Future Trends in Food Inventory Management
The food industry is undergoing significant transformations. These changes impact how inventory is managed. Adapting to future trends is crucial for businesses aiming to sustain their operations and maximize efficiency. Understanding these trends enables decision-makers to implement effective strategies and utilize available technologies.
Emerging Technologies
Technology is reshaping inventory management in the food sector. The rise of advanced software solutions and automation tools offers unmatched opportunities. Solutions like artificial intelligence and machine learning enhance forecasting accuracy and inventory control.
- Artificial Intelligence Precision: AI algorithms analyze vast data sets for more accurate demand forecasts. This results in fewer stockouts and reduced overstock situations. These capabilities lead to cost savings and better customer satisfaction.
- Internet of Things (IoT): IoT devices allow real-time tracking of products. Sensors in storage and transportation help monitor conditions like temperature and humidity. This management is especially critical for perishable goods.
- Blockchain Technology: This technology enhances supply chain transparency. With blockchain, every transaction is recorded, allowing companies to trace the origin of products. This builds consumer confidence in food safety and authenticity.
"The integration of technology in inventory management will not only streamline processes but also build resilience against disruption.”
Incorporating these technologies ensures that food businesses can respond promptly to market demands and mitigate risks.
Shifts in Consumer Behavior
Consumer expectations are evolving rapidly. Businesses must respond to these shifts to stay relevant. An increase in demand for transparency and sustainability is evident. Consumers are more informed and seek ethically sourced products.
- Demand for Local Products: There is a noticeable trend toward local sourcing. Consumers favor products that support local economies and have a smaller carbon footprint. Companies need to adjust their sourcing strategies accordingly.
- Health Consciousness: There is a growing awareness of health and wellness. Consumers now scrutinize labels and ingredients. Efficient inventory management must therefore include tracking for healthier options and allergen information.
- Sustainability Awareness: Customers are increasingly intolerant of waste. These practices push organizations to adopt methods that minimize waste. Education on sustainability becomes essential for brands wishing to connect with these values.
End and Recommendations
In the context of inventory management within the food industry, the conclusion serves as a crucial assessment of the strategies discussed throughout the article. It synthesizes the insights gained and emphasizes their importance for decision-makers who aim to optimize their inventory systems. Proper inventory management is vital, as it affects both efficiency and profitability. Food companies face a significant challenge in balancing stock levels, given the perishability of goods. Thus, an effective management approach not only helps to reduce waste but also ensures that the supply chain remains uninterrupted and compliant with regulations.
Key elements to consider include:
- The implementation of technology-driven solutions is essential. Real-time data aids in forecasting and helps businesses adapt to market demands swiftly.
- Sustainability in inventory practices can also yield long-term benefits, aligning with consumer preferences and reducing waste.
- Regular assessment and adjustments of inventory systems are necessary to maintain optimal performance.
By focusing on these areas, companies can enhance their operational capabilities, ensuring that they remain competitive in a constantly evolving landscape.
Key Takeaways
- Importance of Real-Time Data: Real-time data empowers food businesses to make informed decisions quickly. This reduces errors and enhances the accuracy of forecasts.
- Technological Integration: Adopting advanced inventory management software not only streamlines operations but also offers greater visibility on stock levels.
- Sustainability Initiatives: Sustainable practices are integral to modern inventory management, helping to meet consumer expectations while minimizing waste.
- Regular Review Processes: Periodic evaluations of inventory systems allow businesses to adapt to changes in demand and to optimize stock levels accordingly.
Actionable Steps for Implementation
Implementing advanced inventory management strategies requires a structured approach. Here are some actionable steps that organizations can take:
- Invest in Technology: Choose suitable inventory management software that aligns with your operational needs. Use tools like Fishbowl or QuickBooks Commerce to simplify inventory tracking.
- Train Employees: Provide comprehensive training for staff on new systems and practices. Ensure they understand the importance of real-time data.
- Conduct Regular Audits: Schedule routine audits to assess the accuracy of inventory records and identify any discrepancies.
- Implement Sustainable Practices: Introduce methods for reducing food waste, such as donating unsold goods and recycling packaging materials.
- Monitor Market Trends: Stay informed about consumer preferences and emerging trends. This can guide inventory adjustments and ensure alignment with market demand.
By following these steps, organizations can achieve a more efficient and effective inventory management system that contributes to their overall success.