Analyzing iqms Delmiaworks for Manufacturing Success
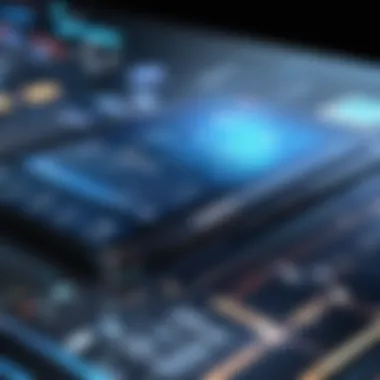

Intro
In the rapidly changing landscape of manufacturing technology, software solutions play a pivotal role in shaping operational success. As companies strive for efficiency and adaptability, iqms Delmiaworks stands out as an influential option designed specifically for the manufacturing sector. Understanding the functionalities of this software is crucial for decision-makers, IT professionals, and entrepreneurs aiming to enhance their operational framework.
The following sections will provide an in-depth exploration of iqms Delmiaworks, diving into its core features, integration potential, and real-world applications that demonstrate its effectiveness in driving operational optimization. This comprehensive analysis ultimately aims to furnish its readers with not only the merits of iqms Delmiaworks but also a comparative view against other software options in the realm of manufacturing.
Overview of iqms Delmiaworks
In today’s rapidly changing manufacturing environment, it is essential to grasp the nuances surrounding modern software solutions. iqms Delmiaworks stands out as a vital piece of technology within this landscape. By focusing on industry-specific needs, this software enables manufacturers to enhance productivity, ensure quality, and optimize processes. For decision-makers, this makes iqms Delmiaworks not just a tool but an essential partner in achieving operational success.
What is iqms Delmiaworks?
iqms Delmiaworks is a comprehensive manufacturing software solution designed to address the intricate demands of various industries. It merges enterprise resource planning (ERP) and manufacturing execution system (MES) functionalities into one seamless platform. This is particularly beneficial for companies looking to streamline operations and reduce the complexity often associated with using multiple disparate systems.
Understanding iqms Delmiaworks involves recognizing its role in integrating all facets of the manufacturing process, from planning and production to delivery and customer service. The software caters to an array of manufacturing sectors, including automotive, medical devices, and consumer products, making it a versatile option for firms aiming for continuous growth.
Key Features and Functionalities
The robustness of iqms Delmiaworks lies in its myriad features and functionalities that stand out in the competitive landscape. These include:
- Real-Time Visibility: Users gain access to real-time data across production facilities, allowing for swift decision-making and immediate insights into operational performance.
- Quality Management: The software includes tools for tracking and managing quality control processes, enabling manufacturers to meet standards and reduce reject rates effectively.
- Inventory Optimization: With built-in tools for inventory management, companies can efficiently manage stock levels, reducing waste and ensuring timely availability of materials.
- Custom Reporting: It allows users to generate customized reports, making it easier to analyze performance metrics and identify areas for improvement.
- Collaboration Tools: Having integrated communication features helps teams stay aligned, fostering better collaboration and project management.
"The flexibility and breadth of functionality that iqms Delmiaworks offers can make the difference in a competitive market environment."
These features work in concert to enhance operational efficiency, ultimately contributing to higher profitability and better customer satisfaction. Firms using iqms Delmiaworks often note that the software not only facilitates day-to-day operations but also provides a strategic advantage by enabling smarter manufacturing decisions.
The Evolution of Manufacturing Software
The journey of manufacturing software is much like a finely tuned assembly line—progressing through iterations, refining processes, and adapting to shifting needs. Understanding this evolution not only sheds light on where software like iqms Delmiaworks fits in today’s industry landscape, but also helps decision-makers grasp the foundational shifts that have led to sophisticated solutions tailored for modern challenges.
Historical Context
Back in the early days of manufacturing, processes were largely manual. Companies relied on physical paperwork, spreadsheets, and often a hefty amount of guesswork to manage production and inventory. The first steps towards automation began in the late 20th century when Computer-Aided Design (CAD) and Basic Manufacturing Resource Planning (MRP) systems were introduced. These tools provided manufacturers with a way to streamline operations and reduce human error, marking the dawn of a new era.
For example, General Motors and Ford, pioneers of industrialization, ventured into computer systems for production. As manufacturing grew in complexity, the limitations of these early systems became apparent. They often lacked real-time data capabilities, creating a lag between input and actionable output, which ultimately hampered decision-making.
As we moved into the 1990s, the industry started embracing enterprise resource planning (ERP) systems. These systems expanded on MRP functionalities, integrating various departments under one umbrella. It was an innovative leap, but many of these systems were cumbersome, not user-friendly, and costly. A notable instance was SAP’s foray into ERP, which, while groundbreaking, required significant investment and cultural change within organizations.
Advancements Over the Years
Fast forward to the early 21st century, manufacturing software witnessed a revolution spurred by technological advancements. The rise of the Internet and connectivity transformed the landscape. Companies began adopting cloud-based solutions, allowing for greater accessibility and real-time data sharing across geographic boundaries.
Several key advancements can be highlighted during this period:
- Cloud Computing: This marked a shift from traditional on-premise systems. With cloud solutions like iqms Delmiaworks, manufacturers can easily manage and access data from anywhere. It fosters collaboration and provides scalability without the need for intricate IT infrastructures.
- IoT Integration: The Internet of Things offered manufacturers the ability to connect machines and devices, providing rich streams of data. This integration helps in predictive maintenance, ensuring machines run efficiently, and reducing downtime. Imagine a factory where each machine communicates its health status live. It’s a game changer for operational efficiency.
- Data Analytics: Advanced analytics powered by artificial intelligence are allowing manufacturers to analyze vast amounts of data quickly. This transformation leads to data-driven decision-making rather than relying on instinct and historical data. As a result, companies can now forecast demands and optimize their operations proactively.
- User Experience Focus: Modern manufacturing software emphasizes user-friendly interfaces. No longer do users have to wade through complex menus. The design is key, particularly for industries grappling with a labor shortage and needing to train new employees quickly.
"The evolution of manufacturing software is not just about technology; it's about enabling manufacturers to embrace change efficiently and effectively."
As we look toward the future, the evolution doesn’t seem to be slowing down. Continuous enhancements in machine learning and automation will only further refine how manufacturers operate, paving the way for solutions like iqms Delmiaworks to shine in an ever-changing landscape.
Benefits of Using iqms Delmiaworks
The application of iqms Delmiaworks in modern manufacturing environments opens the door to numerous advantages that can significantly shape operational frameworks. This segment illustrates the impacts of this software on efficiency, cost management, and data oversight—essential elements that decision-makers and IT professionals cannot afford to overlook.
Operational Efficiency
Operational efficiency is the beating heart of any business, particularly in manufacturing. iqms Delmiaworks takes this notion to new heights by streamlining workflows and optimizing production processes. By integrating various functions, such as inventory management, quality control, and production scheduling, this software allows companies to eliminate redundancies and delays.
For instance, when Company X implemented iqms Delmiaworks, they reported a 30% reduction in time spent on manual data entry tasks. Automation means less room for human error and quicker turnaround times. As a consequence, productivity is enhanced, allowing manufacturers to focus on improving product quality and meeting customer demands.
In a practical sense, tools within iqms Delmiaworks can connect disparate parts of the operation, ensuring that everyone from the shop floor workers to top-level management works off a single source of truth. The result? A smoother operation that operates like a well-oiled machine.
Cost Reduction
Reducing costs is another critical advantage of iqms Delmiaworks. Operational streamlining doesn't just improve efficiency; it also trims unnecessary expenditures. The software allows manufacturers to closely monitor their resources, which leads to more informed decision-making and reduced waste.
To illustrate, let’s take Company Y. By utilizing iqms Delmiaworks, they identified overproduction patterns that bled resources. After adjusting their protocols based on data insights from the software, they realized annual savings of approximately $250,000. These savings emerged from lowering excess inventory levels and minimizing the carrying costs associated.
Moreover, the software aids in identifying the optimum production mix, enabling companies to produce goods that align more closely with market demand. This fine-tuning not only leads to lower operational costs but also maximizes the bottom line by enhancing the overall return on investment.
Improved Data Management
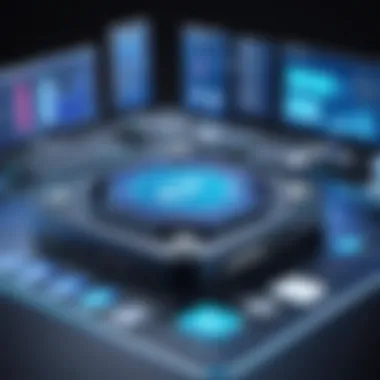
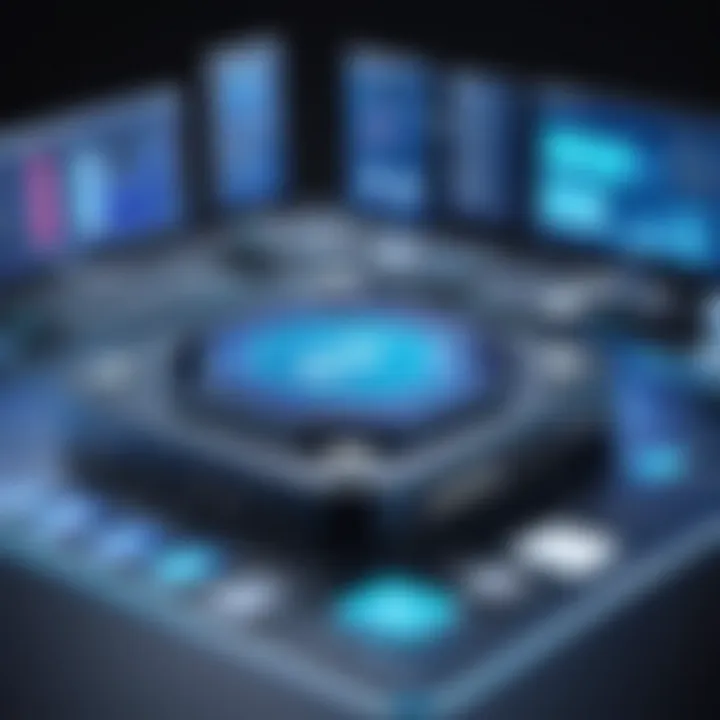
Data management is a buzzword that remains ever-relevant in today’s information-driven landscape. iqms Delmiaworks excels in elevating data control, offering a centralized platform for all relevant manufacturing data. This clarity transforms raw data into actionable insights.
The software features robust reporting capabilities, which means companies can generate detailed reports about various factors from production efficiency to product quality. Think of it as a compass that guides you through the treacherous waters of manufacturing decisions. An informed decision is often the best decision.
An example is Company Z, which leveraged iqms Delmiaworks for its data analysis functionalities. They noticed significant improvements in their quality management systems, leading to bolstered customer satisfaction and reduced defect rates. Over a year, they decreased defects by 15%, which solidified their market reputation.
Integration with Existing Systems
The ability to seamlessly integrate manufacturing software like iqms Delmiaworks with existing systems can make or break a company's operational efficiency. When a new tool ties into pre-existing frameworks, it's akin to finding the right puzzle piece that smoothens operations, allowing data to flow effortlessly from one program to another. In today's fast-paced market, where agility is key, ensuring synergies between software platforms is not just beneficial—it’s essential.
Integration can offer significant benefits that are hard to overlook. For one, it enhances data accuracy by minimizing manual entry errors, which can be costly over time. A streamlined integration means that data from various sources is synchronized, allowing decision-makers to rely on single-source information. This contributes to timely insights, enabling managers and executives to make informed decisions spontaneously rather than based on outdated or inaccurate data.
Furthermore, effective integration can lead to enhanced productivity. When systems communicate well, tasks that used to take hours can often be completed in a fraction of the time. Employees can focus on their core duties instead of getting bogged down by troubleshooting software inconsistencies or juggling multiple platforms that don't quite gel.
However, there are considerations when integrating iqms Delmiaworks into existing frameworks. Organizations often face hurdles such as compatibility issues, potential data loss, and the learning curve that comes with new technology. It's crucial to conduct a thorough assessment before initiating integration, ensuring that the necessary infrastructure is in place to support the cohesive operation of all systems.
"In the world of manufacturing software, the right integration can be the linchpin that transforms operational struggles into competitive advantages."
API Capabilities
A strong selling point of iqms Delmiaworks is its robust Application Programming Interface (API) capabilities. APIs serve as the backbone for integration efforts, allowing different software systems to communicate with one another seamlessly. These capabilities enable iqms Delmiaworks to pull data from external platforms, while also allowing other software to harness its functionalities.
For instance, consider a scenario where a manufacturing plant’s inventory management system requires real-time updates from iqms Delmiaworks regarding production output. By using APIs, these systems can exchange information continuously, leading to a more responsive supply chain. This not only reduces the chances of stockouts or overstock scenarios but also creates a more agile manufacturing process in the long run.
Compatibility with Other Software
Compatibility with a variety of other software platforms is another critical aspect for organizations considering the adoption of iqms Delmiaworks. In an age where businesses depend on an ecosystem of applications ranging from CRM tools to advanced analytics solutions, the ability of iqms Delmiaworks to play well with others is paramount.
When considering compatibility, organizations may look for seamless interoperability with tools like SAP, Salesforce, or even bespoke solutions tailored to their specific needs. Incompatibility issues can hinder productivity and lead to operational delays, hence choosing a system like iqms Delmiaworks, known for its flexible architecture, can uphold efficiency.
It's essential to research how iqms Delmiaworks fares with particular software. Comprehensive documentation and support forums can guide prospective users on how to effectively bridge the gap between their existing software and the new system. This requires not just technical knowledge but also a clear understanding of business processes.
In closing, fostering an environment where iqms Delmiaworks can sit comfortably alongside existing systems fortifies the entire manufacturing process. Deciding on such integrations should never be an afterthought; it matters as much as the software’s core capabilities itself.
User Experience and Interface
In the realm of manufacturing software, user experience (UX) and interface design stands as a crucial pillar. A well-crafted UX enhances productivity, minimizes the learning curve, and in many instances, can be the difference between a successful implementation and a complete failure in adoption. For decision-makers and IT professionals, the importance of these elements cannot be overstated. When evaluating iqms Delmiaworks, the focus on its user experience and interface reveals how effectively it bridges user needs with operational demands.
Ease of Navigation
An intuitive navigation system is at the heart of a robust user interface. If users find it easy to navigate the software, they are more likely to leverage its features fully. iqms Delmiaworks is formulated with user-friendly menus and clear pathways for task completion, which can lead to significant time savings. The layout typically presents information in a straightforward manner and processes are designed logically, allowing users to move seamlessly between functions.
- Prioritizing Workflow: Users can find critical functions quickly, which is essential in fast-paced environments where time is of the essence.
- Search Functionality: The inclusion of an efficient search tool helps users locate specific data or features without digging through multiple menus. This aspect boosts productivity and user satisfaction.
- Visual Consistency: A consistent design language across the platform helps to eliminate confusion. Users are less likely to overlook features when they are presented uniformly throughout the software.
Overall, ease of navigation enhances the overall user experience, ultimately ensuring that users can focus more on their tasks rather than their tools.
Customizability
In an age where one-size-fits-all solutions fall short, the ability to customize software according to individual or organizational needs can be a game-changer. For iqms Delmiaworks, this quality is particularly significant as it accommodates various sectors such as automotive and pharmaceuticals. Here are some key elements regarding its customizability:
- Flexible Dashboards: Users can modify their dashboards to display relevant KPIs and processes. This tailoring allows each user to create a workspace that reflects their priorities.
- User Preferences: iqms Delmiaworks lets users adjust settings according to personal preferences, which can enhance comfort and efficiency by using the software in a way that feels intuitive to them.
- Integration Options: Customizability isn't limited to appearance; it extends to how the software interacts with other systems. Users can set up connections that suit their workflows, making it possible to import and export data as needed.
While customizing software can demand some initial investment of time and effort, the payoff is significant. When users feel like their tools work for them rather than the other way around, they can deliver better results with less frustration.
"The ability to tailor one’s experience is not merely a luxury; it's a necessity in today's complex operational environments."
Collectively, both the ease of navigation and customizability significantly contribute to the efficacy of iqms Delmiaworks, ensuring that users can access, understand, and utilize the full capabilities of the software efficiently.
Industry Applications of iqms Delmiaworks
The significance of exploring iqms Delmiaworks across various industries lies in the software's ability to streamline operations and improve productivity. iQMS Delmiaworks is tailored to meet the specialized needs of sectors like manufacturing, pharmaceuticals, and automotive, each of which demands a unique approach to operational efficiency. By delving into these applications, decision-makers and IT professionals can gain insights into how this platform can address specific challenges inherent to their industries, paving the way for better customer satisfaction and increased profitability.
Manufacturing Sector
In the realm of manufacturing, iqms Delmiaworks stands as a beacon for enhancing operational workflows. This sector thrives on precision, and the software’s capacity to manage intricate processes like production scheduling and quality control makes it invaluable. Key features such as real-time data analytics and inventory management empower manufacturers to make informed decisions quickly. Moreover, seamless integration with machinery is a tremendous advantage, allowing for automated reporting and reduced downtime.
A few noteworthy aspects include:
- Enhanced Production Planning: Streamlining schedules down to the minute prevents bottlenecks.
- Quality Assurance: The software monitors each stage of production, ensuring compliance with industry standards.
- Scalability: Whether a small workshop or a large manufacturing plant, iqms Delmiaworks grows with your needs.
Pharmaceuticals
The pharmaceutical industry is characterized by stringent regulations and an unwavering commitment to safety and efficacy. Therefore, the implementation of iqms Delmiaworks in such an environment is crucial. The software supports compliance with FDA regulations through comprehensive documentation and robust audit trails.
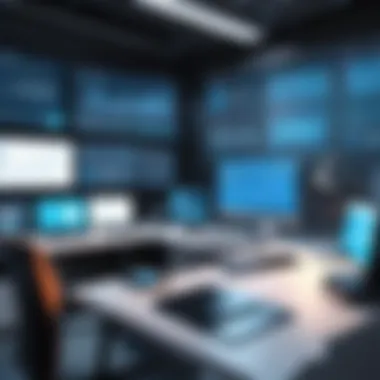
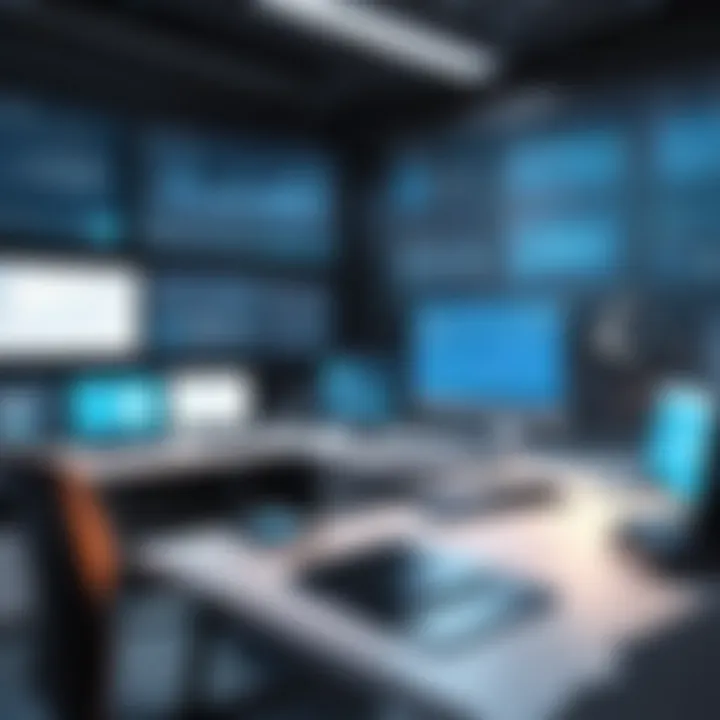
Additional benefits include:
- Batch Tracking: Knowing where every ingredient comes from and how it’s processed is essential for safety.
- Document Control: Managing Standard Operating Procedures (SOPs) becomes easier, enhancing overall quality management.
- Risk Management: With predictive analytics, potential issues can be identified before becoming significant setbacks.
The automation features significantly reduce human error, enhancing the speed and accuracy of pharmaceutical production.
Automotive Industry
The automotive sector has its own distinct set of challenges, including fluctuating consumer demands and a complex supply chain. Here, iqms Delmiaworks proves its worth through a range of functionalities that enhance flexibility and responsiveness. Its emphasis on lean manufacturing principles allows companies to eliminate waste and optimize processes, all while keeping costs down.
In this context, some pivotal advantages are:
- Supply Chain Management: Effectively tracking components ensures a smooth production line.
- Real-Time Reporting: Keeping tabs on vehicle production rates and inventory provides a competitive edge.
- Collaboration Tools: Facilitating better communication among departments leads to accelerated problem-solving.
In the fast-paced automotive industry, failing to adapt can spell disaster. iqms Delmiaworks provides tools designed to keep businesses ahead of the curve.
Overall, each industry provides a distinct lens through which to evaluate the capabilities of iqms Delmiaworks. By assimilating this knowledge, organizations can tailor the software’s functionalities to meet their needs, thereby unlocking unprecedented levels of operational efficiency.
Case Studies: Success Stories
Case studies provide real-world examples that deeply illustrate the capabilities and impact of iqms Delmiaworks. They’re not just examples but are critical narratives that turn abstract features into relatable successes. This section highlights how various companies transformed their operations using iqms Delmiaworks, providing a clearer picture for decision-makers and IT professionals.
Not only do these success stories highlight the functional benefits of the software, but they also reveal practical challenges and solutions encountered during implementation. The insights drawn from these cases allow potential users to better gauge the software's alignment with their operational goals, facilitating informed decisions. These narratives underscore the potential for operational efficiency, improved data management, and overall enhancements in productivity. The understanding gained here can spark ideas on how similar paths may be forged in other organizations.
Company A Implementation
Company A, a mid-sized manufacturer in the electronics sector, faced several inefficiencies due to disparate systems managing its production lines, inventory, and customer relationships. The disconnect resulted in communication lapses, delayed orders, and increased operational costs. After extensive research, they decided to implement iqms Delmiaworks.
The initial step involved a thorough assessment of their existing processes. Key stakeholders engaged in identifying specific pain points which led to a tailored implementation plan. The relationship with iqms Delmiaworks was marked by consistent training sessions and feedback mechanisms. Employees were involved throughout the process, which fostered a sense of ownership among the team.
"The integration was not just about installing software; it became an opportunity for us to rethink how we operate from the ground up."
In just six months post-implementation, Company A reported a remarkable reduction in order processing time by 40%, as well as improved accuracy in inventory management. Custom dashboards tailored to their needs allowed for real-time visibility into production, which improved their response times to market demands.
Company B Transformation
Company B, operating in the automotive supply chain, was looking to maintain a competitive edge in a tight market. The company was using an outdated suite that lacked the scalability required for their growing operations. They turned to iqms Delmiaworks after a careful analysis of their needs and the software's extensive functionality.
The transformation involved not merely technical changes; it demanded a shift in company culture to embrace data-driven decision-making. The software allowed seamless data integration across departments, ensuring that everyone, from procurement to sales, was equipped with the same insights.
Their implementation phase included a pilot program that ran parallel to existing systems for six months. This strategy allowed for testing the waters without disrupting everyday business. The result was overwhelming. They achieved a 30% cut in lead times and a substantial decrease in wastage due to better quality control mechanisms embedded within iqms Delmiaworks.
Furthermore, analytical tools provided by the software informed strategic decisions about product lines that resonated well with market demands. This led to the launch of a new line that captured a larger market share, setting a benchmark in their sector.
Through these case studies, it becomes evident that adopting iqms Delmiaworks can lead to transformative operational insights, justify investments, and catalyze growth. When companies invest in new software, they aren’t just upgrading technology; they're advocating for a better way of working that promotes long-term success.
Challenges and Limitations
When it comes to implementing sophisticated manufacturing software like iqms Delmiaworks, it’s not all smooth sailing. Understanding the challenges and limitations associated with this platform can be crucial for decision-makers and IT professionals. This section will delve into some critical aspects that organizations must consider before embarking on their integration journey with iqms Delmiaworks.
Technical Issues
Technical issues are often at the forefront during the adoption of any new software solution, including iqms Delmiaworks. Users may encounter compatibility problems with existing systems or hardware constraints that hinder performance. There are several factors to consider:
- Installation Complexity: Setting up the software can be intricate, requiring specialized knowledge. This could necessitate training or hiring additional personnel for effective implementation.
- Integration Problems: Existing systems might not integrate seamlessly with iqms Delmiaworks, leading to data silos or inconsistencies. Incompatibility can also arise from different data formats or communication protocols.
- Performance Bottlenecks: Some users have reported lagging performance, especially when dealing with larger datasets or high volume transactions. This can impede quick decision-making.
Feedback from the user community indicates that technical glitches can disrupt workflows substantially. So, investing time in preliminary assessments and creating a detailed integration plan often pays dividends down the line.
User Adoption Challenges
User adoption challenges present another layer of complexity when introducing iqms Delmiaworks into an organization’s workflow. It's essential to recognize that having a robust program in place does not guarantee successful implementation. Here’s what often comes into play:
- Resistance to Change: Employees accustomed to legacy systems may resist transitioning to a new platform. This can lead to pushback and a lack of engagement,
- Training Requirements: Adequate training is pivotal. If personnel do not fully understand how to leverage iqms Delmiaworks, they might underutilize its potential features. Effective change management strategies must be in place to ease this transition.
- Cultural Barriers: The company’s existing culture might clash with the new software processes. If the management isn’t fully bought in, it trickles down to the staff.
A smooth transition often relies on clear communication and an emphasis on the benefits the new system will bring. Furthermore, involving end-users early in the process can foster buy-in and reduce friction.
"Adopting new technology is not just a technical shift; it's a cultural one as well. Ensure your team is on board to navigate the choppy waters of change effectively."
In summary, thoroughly addressing these challenges and limitations is paramount. Knowing what hurdles lie ahead can prepare organizations to strategize adequately, ensuring that the implementation of iqms Delmiaworks is not only successful but also sustainable.
Competitive Analysis
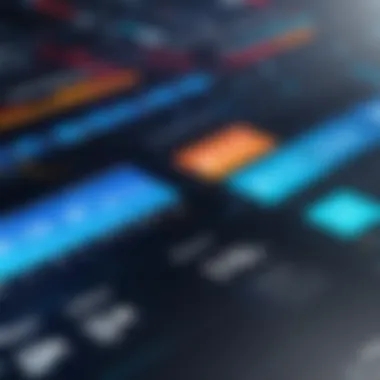
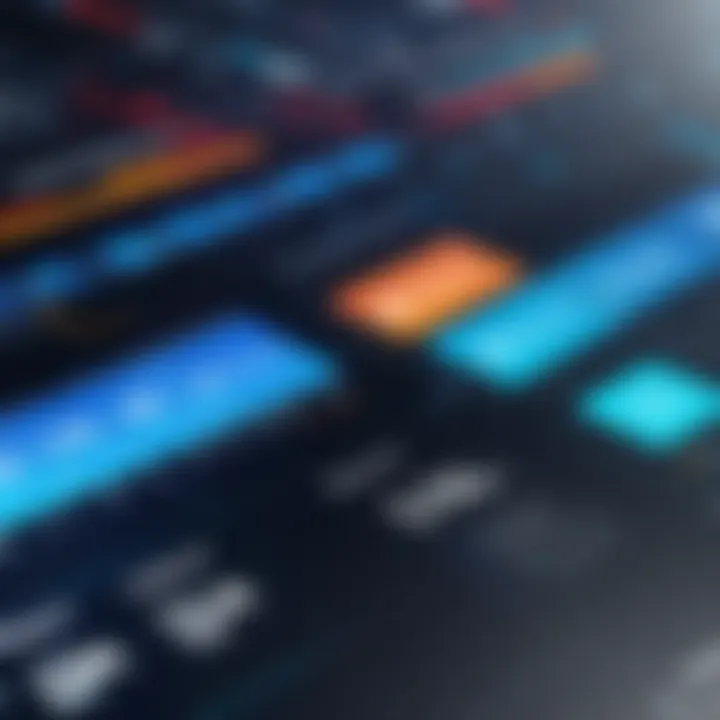
In today’s rapidly evolving industrial landscape, understanding the competitive environment is crucial for making informed decisions. A thorough competitive analysis of iqms Delmiaworks unveils not just its strengths but also its position relative to other manufacturing software solutions. This section aims to shed light on the critical elements of competitive analysis, its benefits, and key considerations when evaluating iqms Delmiaworks compared to its contemporaries.
Comparative Overview
A comparative overview serves as the backbone of any substantial competitive analysis. It assists stakeholders in identifying what sets iqms Delmiaworks apart from its peers. This evaluation involves looking into various factors:
- User Interface: iqms Delmiaworks prioritizes user experience, with a tailored interface that enhances productivity. Compared to competitors, its design feels intuitive, making training and onboarding easier.
- Integration: One clear advantage of iqms Delmiaworks is its extensive API capabilities. When pitted against other software, the ease with which it integrates with existing systems often emerges as a decisive factor.
- Industry Specificity: While many software options attempt to cover broad generalities, iqms Delmiaworks seems to thrive on its focus on specific sectors like manufacturing, pharmaceuticals, and automotive. This specialization often leads to enhanced functionality and results.
This analysis can help decision-makers weigh the distinct characteristics that could influence adoption. Users often report that when incorporating iqms Delmiaworks, the immediate return on investment feels tangible, an aspect not always reflected in its competition.
Market Positioning
Market positioning encompasses not only where iqms Delmiaworks stands regarding its rivals but also its perceived value in the industry. Analyzing its market stance reveals a few undeniable points:
- Brand Reputation: iqms Delmiaworks has built a reputation for reliability and performance, something that is crucial in the manufacturing sector. This trust often translates into sustained growth, as many companies prefer proven solutions.
- Customer Support: A robust customer support system enhances market positioning. Users frequently highlight the quality of support they receive when using iqms Delmiaworks, stating that prompt assistance can make all the difference during critical phases of operations.
- Pricing Strategy: While price isn't everything, it plays a pivotal role in customer decisions. iqms Delmiaworks strikes a balance between cost and feature richness. By offering various packages, it caters to different business sizes, ensuring accessibility without compromising quality.
- Future-Readiness: Today’s competitive landscape demands adaptability, and iqms Delmiaworks seems well-prepared for future tech trends, such as predictive analytics and IoT integration. This foresight keeps it one step ahead of competitors that may be slower to innovate.
"In competitive spaces like manufacturing, having the right tools makes a world of difference. iqms Delmiaworks stands as a notable example, blending efficiency with specific industry needs."
Feedback from the User Community
Understanding feedback from the user community holds a taunt of significance in analyzing iqms Delmiaworks. This section aspires to showcase how user opinions can shape the image of the software while elucidating the benefits of gathering such insights. Just like an artist refining their craft through critiques, software evolves through user experiences and feedback. Incorporating what users think contributes directly to the software's development, improvements, and, ultimately, its effectiveness in real-world scenarios.
User Ratings and Reviews
Delving into user ratings and reviews highlights an integral aspect of iqms Delmiaworks. These metrics serve as barometers of user satisfaction and operational success. High ratings typically suggest that users find the software reliable and beneficial, while lower ratings can indicate areas that need enhancement.
- Implementation Feedback: Users often discuss their on-boarding experiences. Smooth integration with existing systems eases the transition, whereas a rough start can impede productivity.
- Functionality Assessment: Are the promised features living up to expectations? Community reviews frequently mention usability, which is vital for user adoption. The smoother the user experience, the more likely they are to sing praises.
- Long-Term Value: Over time, users will express their thoughts on the software’s effectiveness in relieving pain points. This information is particularly precious for potential users weighing their options.
“User reviews are like pearls of wisdom; they guide the way forward.”
This perspective underscores the necessity of digesting feedback, as it might reveal insights no marketing brochure could cover.
Forum Discussions
Engaging in forum discussions offers a more dynamic platform for users to share their experiences regarding iqms Delmiaworks. These conversations often bring forth key aspects that reviews might overlook.
- Troubleshooting: Common problems surface here, along with solutions that users provide to each other, fostering a collaborative environment. For decision-makers, a robust community support network can be a game-changer.
- Updates and Changes: Users willingly share their take on recent updates or feature releases. This type of dialogue can signal whether new features enhance user experience or complicate workflows.
- Feature Requests: Forums are fertile grounds for idea generation, where users propose enhancements or new functionalities. Understanding these requests can provide valuable intelligence for the iqms development team.
This community engagement paints a broader picture of how iqms Delmiaworks is perceived in the market, revealing not just satisfaction levels but also areas ripe for development.
Future Trends in Manufacturing Software
The landscape of manufacturing software is continually evolving, reflecting advancements in technology and changing market demands. As industries push for greater efficiency and adaptability, understanding future trends becomes paramount for decision-makers, IT professionals, and entrepreneurs. These trends not only highlight new opportunities but also inform strategies for leveraging technology effectively to maintain a competitive edge.
Emerging Technologies
In today’s manufacturing climate, emerging technologies are not just buzzwords; they're essential tools for streamlining operations.
- Artificial Intelligence (AI): With its capability to automate processes, AI helps companies in predictive maintenance, enhancing product quality, and optimizing supply chain management. For instance, AI algorithms can predict equipment failures before they occur, minimizing downtime.
- Internet of Things (IoT): The integration of IoT devices enables real-time data collection and monitoring throughout the production process. This tech allows for a meticulous control over operations, enhancing transparency and responsiveness. For example, sensors can provide information on machine performance, facilitating timely interventions.
- Cloud Computing: The move towards cloud-based solutions allows for greater flexibility in data management. Companies can access and analyze vast amounts of data from anywhere, improving collaboration across teams. These solutions often offer scalability as per the firm's growth.
- 3D Printing: This technology is redefining production lines by offering rapid prototyping and customization. Businesses can quickly adapt to customer demands without the long lead times associated with traditional methods.
Embracing these technologies can significantly impact a company's agility and responsiveness, making it crucial for industries to stay ahead of the curve.
Predictive Analytics Integration
Predictive analytics represents a powerful shift in how manufacturing companies manage their operations. By analyzing historical data and identifying patterns, businesses can make informed decisions that foster growth and efficiency.
- Supply Chain Optimization: Through predictive analytics, organizations can anticipate demand fluctuations and optimize inventory levels accordingly. This minimizes waste and ensures that resources are utilized efficiently.
- Quality Control: Utilizing predictive models allows firms to catch potential quality issues before they escalate. By analyzing production metrics in real-time, manufacturers can implement corrective measures on the fly, preserving their product integrity.
- Workforce Management: Insights derived from predictive analytics can significantly enhance workforce allocation. Companies can predict busy periods and adjust staff levels accordingly, which means higher productivity and morale.
Incorporating predictive analytics into manufacturing operations aligns well with the movement towards digital transformation. Companies that harness these insights put themselves in a position to not only compete but thrive in the fast-paced market.
"The future belongs to those who prepare for it today." – Malcolm X
In summary, as manufacturers look toward the future, emerging technologies and predictive analytics integration will play crucial roles. Companies that adapt to these trends will likely find themselves well-positioned to navigate the complexities of modern manufacturing challenges.
Finale
When reflecting on the comprehensive insights provided throughout this article, it's essential to recognize the pivotal role that iqms Delmiaworks plays in modern manufacturing. It is not merely a software solution; it stands as a cornerstone for enterprises seeking to streamline operations and optimize their manufacturing processes. The advantages outlined in previous sections—from operational efficiency and cost reduction to enhanced data management—paint a vivid picture of its benefits.
Final Thoughts on iqms Delmiaworks
As we wrap up the discussion on iqms Delmiaworks, a few crucial elements merit special attention. First, the software's adaptability to various industry applications speaks volumes about its versatility. Whether one operates in pharmaceuticals, automotive, or general manufacturing, iqms Delmiaworks has tailored solutions to meet diverse needs.
Furthermore, the integration capabilities of this software are robust, allowing companies to harmonize it with existing infrastructures and creating a seamless flow of information. This is especially relevant in an era where efficiency is paramount and delays can be detrimental to success.
In terms of user experience, the interface is user-friendly, yet sophisticated enough to encapsulate complex functionalities. Ease of navigation and customization options empower users to tailor their experience to their unique workflows. This tailored approach not only Promotes user satisfaction but also contributes to the overall productivity of the organization.
To encapsulate the essence of iqms Delmiaworks, consider this:
"The right tool can transform not just processes, but the entire fabric of a manufacturing operation."
Ultimately, decision-makers, IT professionals, and entrepreneurs should view iqms Delmiaworks not just as a software, but as a strategic partner in their pursuit of operational excellence, competitive advantage, and long-term growth. With the ever-changing landscape of manufacturing, now is the time to assess whether iqms Delmiaworks aligns with your organizational goals and the future you envision.