A Comprehensive Guide to Business Work Orders
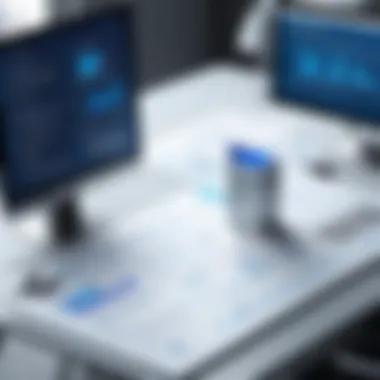

Intro
In the dynamic landscape of business operations, the use of work orders is paramount. A work order is a formal document that outlines tasks or requests to be completed in various organizational contexts. Its significance cannot be overstated, as it serves as a cornerstone for effective communication and process management within companies. Understanding the structure and role of work orders helps in refining workflows and enhancing overall productivity.
This guide aims to provide comprehensive insights into the world of business work orders, elucidating their key components and offering best practices for their management. Each segment will address different facets of work orders, catering to decision-makers, IT professionals, and entrepreneurs looking to optimize their operational systems.
Software Category Overview
Definition and Importance
Business work order software facilitates the creation, management, and tracking of work orders across various departments. It plays an essential role in coordinating tasks, allocating resources, and ensuring timely completion of jobs. The importance of such software lies in its ability to enhance productivity, reduce errors, and streamline communication among team members.
Key Characteristics
- User-Friendly Interface: Software should provide a clean and intuitive design that allows users to create and manage work orders effortlessly.
- Customizable Templates: Users need templates that can be tailored to specific tasks or projects, allowing for greater flexibility.
- Real-Time Tracking: Capability for tracking work orders in real-time ensures that all parties are updated, which is a key efficiency factor.
- Reporting Features: Comprehensive reporting tools provide insights into workflow efficiency and areas needing improvement.
- Integration Capabilities: The software should seamlessly integrate with other business tools and platforms, such as accounting software or CRM systems.
Effective work order management leads to increased accountability and better resource allocation.
As we progress through this guide, various types of work orders will be explored, along with best practices designed to maximize efficiency and improve service delivery.
Understanding Business Work Orders
Business work orders are essential tools in the operational framework of any organization. They serve to coordinate tasks and track progress, transforming abstract ideas into actionable items. This understanding is crucial for decision-makers and IT professionals, as it lays the foundation for enhanced productivity and workflow efficiency.
Definition of Business Work Orders
A business work order is a formal document or request that specifies the work to be done. It outlines tasks, responsibilities, and timelines, serving as a clear reference point for all involved parties. While they can vary across industries, they typically include key information such as:
- Task Description: A detailed account of the work to be completed.
- Assigned Personnel: Names of individuals responsible for executing the tasks.
- Time Frame: Estimated duration for the completion of the work.
- Resources Needed: Equipment or materials required to carry out the task.
By providing this level of detail, work orders help in minimizing ambiguity and ensuring that all stakeholders have a shared understanding of the responsibilities involved.
Importance in Business Operations
Work orders hold significant importance in business operations for several reasons. They not only enhance clarity and accountability among team members but also streamline communication within and across departments. Consider the following benefits:
- Efficiency: Work orders enable teams to prioritize tasks and allocate resources appropriately, thus maximizing productivity.
- Tracking Progress: By monitoring work orders, organizations can keep track of task completion and identify any delays or issues that may arise.
- Improved Service Delivery: Clear instructions and accountability lead to better quality outcomes, directly impacting customer satisfaction.
- Data Collection and Analysis: Work orders can serve as data points for performance analysis, enabling organizations to identify trends and areas for improvement.
"A well-structured work order can substantially impact the operational success of a business, creating a structured approach to managing tasks and responsibilities."
In summary, understanding business work orders is vital for anyone involved in the management and execution of organizational workflows. The clarity they provide helps ensure that operations run smoothly and efficiently.
Types of Work Orders
Understanding the different types of work orders is crucial to streamlining business operations. Each type serves a specific purpose and has its own set of processes, contributing to overall effectiveness and efficiency. By categorizing work orders, organizations can allocate resources better, anticipate needs, and enhance communication across departments.
Preventive Maintenance Work Orders
Preventive maintenance work orders are proactive measures taken to ensure systems and equipment function optimally. These orders are initiated based on a schedule, often guided by manufacturer recommendations or historical data. The goal is to prevent equipment failure before it occurs, thereby minimizing downtime.
Benefits include:
- Cost Efficiency: By maintaining equipment proactively, businesses save on more extensive repair costs.
- Extended Equipment Life: Regular maintenance can prolong the life of machinery and tools, increasing return on investment.
Considerations for implementing preventive maintenance include the timing of maintenance activities and tracking the lifecycle of equipment. Integrated software solutions can help manage these schedules effectively.
Corrective Maintenance Work Orders
In contrast, corrective maintenance work orders arise in response to failures or issues that need immediate attention. These reactive measures are essential when something goes wrong unexpectedly. Organizations must act swiftly to restore functionality, which typically involves:
- Assessment of the Issue: Diagnosing the problem accurately is crucial.
- Resource Allocation: Quickly assigning technicians to attend to urgent matters is necessary.
While corrective maintenance is often more costly due to its reactive nature, it is important for preserving operational continuity. Developing strategies to reduce the frequency of these work orders can benefit the overall productivity of the business.
Internal Request Work Orders


Internal request work orders originate within the organization. They often stem from various departments needing support or resources to execute their daily tasks. This type of work order might include requests for IT support, facility maintenance, or inventory management.
Internal requests typically facilitate:
- Streamlined Communication: A clear channel helps ensure that departments understand their needs are being addressed.
- Improved Efficiency: Centralizing requests allows for better prioritization and management of resources.
Creating a standardized process for these types of work orders can help eliminate confusion and ensure a smooth workflow.
External Service Work Orders
External service work orders involve coordination with third-party vendors or service providers. These can be for specialized tasks that internal teams may not be able to handle, such as heavy machinery repairs or technical installations.
Key aspects include:
- Vendor Management: Effective communication with external partners is vital to ensure timely completion of services.
- Assessment of Services: Regular evaluations of vendor performance contribute to maintaining quality outcomes.
This category requires careful planning and monitoring to ensure that service levels meet organizational standards.
Work Order Lifecycle
The work order lifecycle refers to the systematic series of stages a work order undergoes from initiation to closure. Understanding this lifecycle is crucial for businesses aiming for efficiency and seamless operations. It enhances clarity in processes, reduces bottlenecks, and fosters accountability among team members. Each phase of the lifecycle has specific roles and considerations that contribute to the overall effectiveness of work order management.
Initiation Phase
The initiation phase starts the work order process. In this stage, a need is identified, prompting the generation of a work order. This could stem from equipment issues, service requests, or scheduled maintenance. The importance of this phase cannot be understated as it sets the groundwork for all subsequent actions. A well-defined initiation includes clear descriptions of the work needed and the urgency of the request. This clarity helps prioritize tasks, ensuring that high-criticality items receive immediate attention. If mismanaged, this phase can lead to confusion, further complicating later stages of the lifecycle.
Approval Process
After initiation, the work order must go through an approval process before any action is taken. Depending on the organization's structure, this may involve various stakeholders, including managers and team leads. The purpose of this stage is to verify the validity of the work order and to allocate necessary resources. Approval is a checkpoint where costs, required time, and resource availability are evaluated. Robust approval processes help mitigate risks and misallocation. Furthermore, it provides a documentation trail for accountability and future reference.
Execution Stage
Once approved, the work order moves to the execution stage. This is where the actual work takes place. Teams mobilize, tools and resources are gathered, and tasks are conducted based on the prepared plans. Effective communication during this step is vital. Relevant team members must remain informed about timelines, responsibilities, and any changes that may arise. Tracking progress at this stage is crucial. Any delays or inefficiencies can impact subsequent processes and overall project delivery. Therefore, real-time updates and adjustments can enhance execution effectiveness.
Completion and Closure
The final phase is the completion and closure. Here, the work is verified against the original order to ensure all requirements have been met. It involves a review of the tasks completed, any outstanding issues, and overall performance evaluations. This phase also includes documentation of lessons learned and feedback gathering, providing valuable insights for future work orders. Closure is not just an end but a bridge to improve future processes. Without a well-defined closure stage, businesses risk losing critical information that could inform better practices down the line.
"Each stage of the work order lifecycle contributes uniquely to effective business operations. A clear understanding and execution can lead to significant efficiency gains."
In summary, each step of the work order lifecycle plays a distinct role in enhancing operational integrity. A focus on efficient management in these phases can drive better productivity and service delivery in any organization.
Key Components of a Work Order
In the realm of business operations, a detailed understanding of the key components of a work order cannot be overstated. These components serve as the backbone of effective work order management. They ensure that tasks are clearly defined, resources are allocated appropriately, and responsibilities are clearly understood. Without these essential elements, the risk of miscommunication and inefficiency becomes significantly heightened.
Detailed Description of Work
A comprehensive description of the work required is vital. This section should outline the specific tasks to be completed, the objectives of the work order, and any relevant background information. Clarity here helps eliminate ambiguity. For example, instead of stating "repair machinery," it would be more effective to specify, "replace the pump of the central heating system to ensure optimal performance." This level of detail allows all parties involved to have a unified understanding of what is expected. It makes coordination easier and improves the chances of successful task completion.
Resources Required
Identifying resources required for a specific work order is another critical aspect. This can include materials, tools, and personnel needed to accomplish the task. Listing resources ahead of time allows for better planning and predicts potential shortages. It also helps with budgeting, as knowing what is needed can prevent unexpected costs. For instance, if a maintenance task requires a special tool or a specific part, mentioning these in advance can avoid delays later on, ensuring a smoother workflow.
Time Estimates
Accurate time estimates are essential for planning and efficiency. Providing a realistic timeframe within which the work should be completed informs teams about scheduling and workload management. While it can be challenging to predict precise time frames, breaking tasks into smaller components can yield better accuracy. Having time estimates helps in managing expectations for both the team and stakeholders, allowing for better resource management and prioritization.
Assigning Responsibilities
Assignment of responsibilities is the final component. Clearly delineating who is accountable for each part of the work order fosters accountability and ownership. This can be an individual or a team. A structured approach, such as using roles like "lead technician" or "project manager," can clarify who is responsible for different tasks. This reduces confusion, especially in larger projects, and ensures that everyone knows their obligations and deadlines.
"Clear communication and defined responsibilities are paramount in work order management to ensure project success."
In sum, the key components of a work order—detailed descriptions, resource requirements, time estimates, and assignment of responsibilities—form an integrated framework that guides an organization's operational activities. These elements contribute to streamlining workflows, optimizing resource allocation, and enhancing overall productivity.
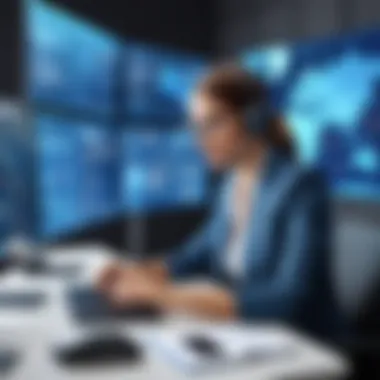

The Role of Technology in Work Order Management
Technology plays a crucial role in managing business work orders. It enhances efficiency, reduces human error, and improves communication within organizations. As businesses expand, the need for effective work order management becomes increasingly important. Modern technology addresses these needs by providing tools that streamline processes and offer insights to decision-makers. By integrating various technological solutions, companies can better manage their work orders and see noticeable improvements in operations.
Work Order Management Software
Work order management software is designed to automate and optimize the workflow associated with business work orders. It allows organizations to create, track, and manage work orders easily. One of the main benefits of using dedicated software is that it centralizes data. This centralization improves visibility for all team members. Everyone involved knows the status of each work order, which reduces miscommunication.
Another advantage is the ability to analyze data over time. Strategic decision-makers can view trends and utilization metrics. This data-driven approach enables companies to make informed adjustments to their operational strategies. Some software options also integrate with existing systems like accounting and inventory management, further improving efficiency. However, it’s crucial to choose software that aligns with the specific needs of the business to gain maximum benefit.
Mobile Applications for Field Operations
Mobile applications are becoming a fundamental part of work order management, especially for field operations. Technicians in the field can access work orders on mobile devices. This access allows for real-time updates. For instance, if a task is completed or if there is an issue, the technician can record the information immediately. Consequently, managers receive timely updates and can adjust resources accordingly.
These applications usually come equipped with features such as GPS tracking and photo uploads. GPS helps prioritize assignments based on proximity, while photo uploads provide visual documentation of tasks. The ease of use makes it more likely that field staff will accurately complete their work, thereby enhancing overall productivity.
Cloud-Based Solutions
Cloud-based solutions offer organizations flexibility and scalability in work order management. The primary advantage of these solutions lies in accessibility. Teams can access work order systems from any location with an internet connection. This feature is particularly beneficial for organizations with multiple sites or remote workers.
Data security is another important consideration. Cloud providers typically offer strong security measures. This protects sensitive data associated with work orders, ensuring compliance with company policies and industry regulations. Additionally, as business needs change, cloud solutions can be scaled up or down. This flexibility provides cost savings and helps manage resources efficiently.
Best Practices for Managing Work Orders
Managing work orders effectively requires a systematic approach. Adopting best practices can enhance efficiency, improve communication, and streamline processes. The significance of this section lies in its ability to offer actionable strategies that decision-makers can implement within their organizations to optimize work order management. This section covers critical elements such as standardization of processes, continuous monitoring and reporting, and the implementation of a feedback loop to foster ongoing improvement.
Standardization of Processes
Standardization plays a pivotal role in managing work orders. It involves creating uniform procedures that guide how work orders are initiated, approved, executed, and closed. By setting clear standards, organizations can ensure consistency across all work orders. This consistency reduces errors, saves time, and improves the overall quality of the service delivered.
Some key benefits of standardizing processes include:
- Clarity: Provides clear guidelines for team members, reducing misunderstandings.
- Efficiency: Streamlines workflows, allowing for quicker turnaround times.
- Scalability: Makes it easier to scale operations as the company grows without losing control over processes.
To effectively standardize processes, organizations should develop a comprehensive work order management manual. This document should provide step-by-step instructions for each stage of the work order lifecycle. Periodic training will ensure that all team members understand and adhere to these standards.
Monitoring and Reporting
Regular monitoring and reporting on work orders offer invaluable insights into operational performance. Effective tracking allows organizations to identify bottlenecks, assess workload distribution, and evaluate service quality.
The primary objectives of monitoring and reporting include:
- Performance Assessment: Enables managers to gauge how well the team is meeting its obligations and targets.
- Decision-Making Support: Data from reports aids in making informed decisions about resource allocation and process adjustments.
It is essential to employ suitable metrics when monitoring work orders. Key performance indicators (KPIs) such as turnaround time, completion rates, and resource utilization are crucial. They should be reviewed regularly to assess the effectiveness of the current management practices.
Continuous Improvement Feedback Loop
In any effective work order management system, a continuous improvement feedback loop is vital. This approach encourages organizations to gather feedback from all stakeholders involved in the work order process. Analyzing these insights helps in pinpointing issues and identifying areas for enhancement.
Implementing a feedback loop involves:
- Engaging Stakeholders: Actively seek opinions from team members, customers, and suppliers to gather diverse perspectives.
- Regular Review Sessions: Schedule sessions to discuss feedback and formulate action plans to address identified problems.
- Updating Processes: When issues are discovered, necessary adjustments to the processes should be made to prevent recurrence.
Through commitment to continuous improvement, organizations can build a more dynamic and agile work order management system, adapting to changes quickly and effectively.
"The effectiveness of managing work orders is not solely based on adherence to processes, but also on the constant pursuit of improvement."
Case Studies of Effective Work Order Implementation
Understanding effective work order implementation is vital for businesses aiming to enhance productivity and streamline processes. Case studies serve as excellent examples of how various organizations have successfully adopted work orders to optimize their operations. Through analyzing these case studies, business leaders can elucidate the specific elements that contribute to successful implementation.
Industry-Specific Examples
Different industries have unique requirements when it comes to work order management. Here are some examples:
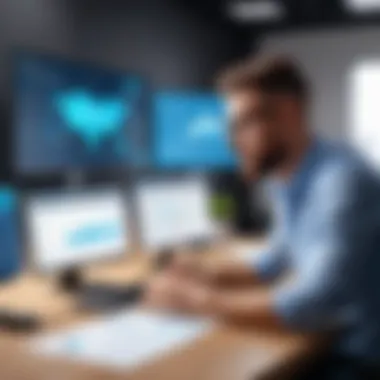

- Manufacturing: A major automotive company implemented a digital work order system which significantly reduced downtime. By connecting equipment sensors with their work order management software, they were able to predict maintenance needs, reducing unexpected breakdowns by 30%.
- Healthcare: A hospital integrated work orders into their facility management system. This change allowed maintenance teams to respond quickly to urgent issues, such as plumbing failures. As a result, patient satisfaction scores improved due to enhanced facility conditions.
- Construction: A large construction firm used a mobile work order system to manage field operations. This technology allowed site managers to submit requests in real-time. The firm saw a 40% increase in task completion speed due to better communication and rapid response times.
These examples show that case studies not only highlight effective strategies but also provide tangible benefits, such as improved efficiency and reduced costs. They underline the necessity for industry-specific solutions tailored to meet individual needs.
Lessons Learned from Failures
Not all implementations succeed, and studying failures offers valuable lessons:
- Lack of Training: A food service company launched a new work order system without providing adequate training. Employees were unsure how to use the new technology, leading to confusion and delays. This highlighted the importance of comprehensive training to ensure everyone understands the system.
- Poor Communication: A retail organization faced challenges because departments did not coordinate effectively. Work orders often overlapped or went unaddressed, causing frustration. This case underscores the need for clear communication channels among teams during implementation.
- Ignoring Feedback: An IT company launched a work order system but failed to collect user feedback post-implementation. As a result, crucial user concerns were overlooked, leading to low adoption rates. It's crucial to make adjustments based on feedback to meet users' needs effectively.
By learning from these failures, companies can avoid similar pitfalls and create a more effective work order management framework.
"The road to effective management is paved with both successes and lessons from failures. Understanding case studies ingrains valuable insights into the practical application of work orders across industries."
Future Trends in Work Order Management
Understanding future trends in work order management is essential for businesses looking to stay competitive. These trends highlight how technology can revolutionize operations and enhance efficiency. With the rise of automation and the Internet of Things (IoT), organizations can expect to see improvements in how they manage work orders. This section will explore the significance of these trends, their potential benefits, and important considerations for implementation.
Artificial Intelligence and Automation
Artificial intelligence (AI) plays a crucial role in shaping the future of work order management. AI technologies can analyze vast data sets to identify patterns and predict needs. This enhances decision-making significantly. For example, AI can prioritize work orders based on urgency and resource availability. It can streamline the approval process, reducing bottlenecks in the system.
Moreover, automated systems can handle routine tasks, like assigning work orders and updating statuses. This not only saves time but also minimizes human error. The integration of AI in work order management can lead to better resource allocation, optimizing workforce utilization. As a result, businesses can increase productivity and reduce operational costs.
Benefits of AI and Automation in Work Order Management:
- Enhanced efficiency through automation of repetitive tasks.
- Improved accuracy in data management and resource allocation.
- Faster processing of work orders, leading to quicker response times.
Integrating IoT with Work Orders
The integration of IoT devices into work order systems is another significant trend. IoT enables real-time data collection from devices and equipment. This capability allows businesses to monitor operational status continuously. When an issue arises, work orders can be generated automatically.
Through IoT, organizations can also track asset usage and performance. This data can inform maintenance schedules and preventive measures, reducing downtime. By connecting equipment and systems, companies can ensure that work orders are accurately aligned with operational needs.
Considerations for Integrating IoT with Work Orders:
- Ensure proper connectivity and communication among devices.
- Implement robust security measures to protect data.
- Train staff on how to leverage IoT data effectively for work order management.
"The future of work order management lies in leveraging technology to enhance productivity and streamline processes."
Challenges in Work Order Management
Managing work orders can present various challenges that impact the efficiency of business operations. These challenges, if not addressed, can lead to delays, miscommunication, and ultimately, increased operational costs. Understanding these challenges is crucial for decision-makers and professionals in optimizing work order processes. The elements of work order management, such as timely execution, clear communication, and resource allocation, can be significantly affected by these challenges. Identifying common pitfalls can help organizations avoid them, leading to better workflow and improved productivity.
Common Pitfalls
Organizations often face several pitfalls in work order management. Recognizing these can aid in preemptive action.
- Inadequate Documentation: This can lead to confusion over task requirements. If details are missing, it can delay execution.
- Delayed Approvals: Slow approval processes can stall work orders, causing inefficiencies and frustration within teams.
- Poor Communication: When teams do not communicate effectively, it can create misunderstandings regarding work priorities or responsibilities.
- Resource Mismanagement: Not using resources efficiently may cause cost overruns or delays in project completion.
- Lack of Training: Staff unacquainted with tools or processes find it hard to execute work orders efficiently.
Recognizing these pitfalls is essential for improving work order management.
Strategies for Overcoming Challenges
To enhance work order management, various strategies can be employed. Implementing these strategies can facilitate better management and execution of work orders.
- Streamlined Processes: Establishing clear workflows can reduce confusion and speed up approval times. It may involve creating standardized templates for work orders.
- Effective Communication Tools: Using platforms like Slack or Trello can improve communication among team members. This ensures everyone is on the same page regarding tasks.
- Training Programs: Regular training can keep staff updated on best practices and tools. This investment can lead to improved efficiency in handling work orders.
- Regular Performance Reviews: Conducting performance evaluations can identify bottlenecks. This allows teams to address specific issues and improve overall efficiency.
- Leveraging Technology: Utilizing work order management software can automate processes. Features like notifications and reminders can ensure timely actions are taken.
Finale
The conclusion serves as a crucial synthesis of the themes and insights presented throughout the article. It emphasizes the pivotal role that work orders play in the operational efficiency of a business. A well-managed work order system can enhance communication, streamline processes, and improve overall productivity. The various types of work orders, from preventive maintenance to external service requests, highlight the diversity and flexibility needed in modern organizational structures.
In practical terms, adopting effective work order management practices can yield significant benefits. These include minimizing downtime, optimizing resource allocation, and ensuring that tasks are completed on time and within budget. Decision-makers must recognize the importance of crafting clear work orders that detail every aspect of the task at hand. Clear specifications help in assigning the right responsibilities and managing expectations.
Furthermore, the integration of technology, such as work order management software and mobile applications, is vital in addressing the challenges faced in traditional work order processing. These tools contribute to real-time data sharing, thereby enhancing coordination among team members.
Key Considerations for Effective Work Order Management
- Standardization: Ensuring all work orders meet a minimum standard enhances consistency.
- Monitoring: Regular oversight of work order progress can identify and mitigate potential bottlenecks.
- Feedback Loops: Continuous improvement practices can be adopted based on the outcomes of previous work orders.
As businesses navigate the complexities of operational demands, work orders will continue to be an essential component. Focusing on efficient management of work orders not only positively impacts the bottom line but fosters a culture of accountability and transparency. Therefore, leaders and managers need to invest in refining their work order processes to reap these benefits.
"Effective management of work orders is not just about task completion; it’s about fostering better collaboration and operational excellence."