Exploring the FedEx Warehouse Management System
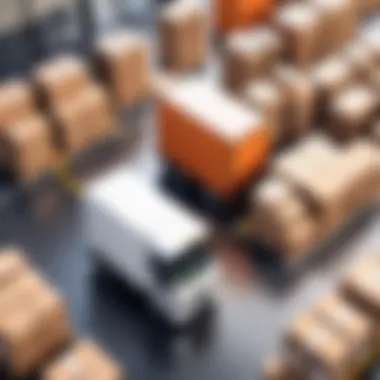
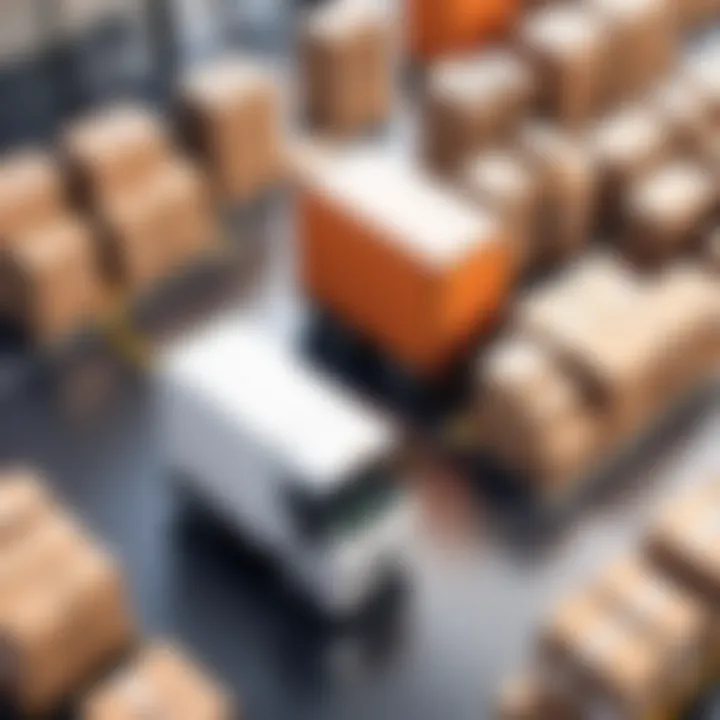
Intro
The FedEx Warehouse Management System (WMS) is designed to optimize warehouse operations. It integrates seamlessly into the broader supply chain management process. Understanding this system is essential for businesses aiming to improve their logistics efficiency. The WMS manages inventory, streamlines order fulfillment, and enhances customer satisfaction. As companies navigate a competitive landscape, the implications of adopting such systems cannot be overstated.
Software Category Overview
Definition and Importance
A Warehouse Management System is software that supports the daily operations of a warehouse. Its role is crucial in managing stock levels, order processing, and overall logistics. In today’s fast-paced economy, the significance of a robust WMS cannot be underestimated. It ensures accuracy and efficiency, preventing issues such as overstocks and stockouts.
Key Characteristics
The characteristics that define an effective WMS include:
- Real-Time Inventory Tracking: Live updates on inventory levels enhance decision-making.
- User-Friendly Interface: A simplified design improves usability across various warehouse staff.
- Integration Capability: Capability to connect with other systems, such as ERP software.
- Scalability: The ability to grow with the business, adapting to increased operational loads.
These features contribute towards an organized workflow. They enable firms to operate more efficiently, especially as demand fluctuates.
Comparative Analysis of Top Software Options
When considering the implementation of WMS solutions, comparing different software options is essential. FedEx’s WMS stands out due to its tailored features and adaptability for logistics.
Feature Comparison
Analyzing FedEx WMS in relation to competitors shows a few distinct advantages:
- Advanced Analytics: Provides insights into warehouse performance, inventory turnover, and operational bottlenecks.
- Mobile Accessibility: Employees can manage tasks from different mobile devices, providing flexibility.
- Robust Reporting Tools: Easy access to detailed reports aids in strategic planning.
These features can distinctly improve operational efficiency compared to rival systems like Oracle Warehouse Management or SAP Extended Warehouse Management.
Pricing Models
Understanding the pricing structure is critical to planning. FedEx typically follows a subscription-based model, which includes:
- Monthly License Fees: Based on the number of users and required features.
- Implementation Fees: One-time costs associated with deploying the system.
- Support and Maintenance Costs: Ongoing expenses for technical assistance and updates.
Investing in a comprehensive WMS like that of FedEx can yield substantial long-term benefits for businesses engaged in complex logistics.
"Adopting a warehouse management system is not just about keeping track of inventory; it's about creating a seamless and efficient operational flow that aligns with overall business strategy."
Prelims to FedEx Warehouse Management System
The FedEx Warehouse Management System (WMS) plays a pivotal role in streamlining operations and enhancing the efficiency of the supply chain. For decision-makers, IT professionals, and entrepreneurs, understanding this system is essential given the critical impact it has on logistics, inventory management, and customer satisfaction. Among industry leaders, FedEx has carved a niche for itself, and its WMS serves as a testament to their commitment to innovation and reliability in warehousing solutions.
Definition and Overview
A Warehouse Management System is a software application that supports day-to-day operations in a warehouse. This includes tracking inventory levels, orders, and deliveries. The FedEx WMS goes beyond basic functionalities, offering advanced features designed to optimize processes. Key components of the system include real-time inventory visibility, automated order processing, and comprehensive reporting tools. These elements facilitate informed decision-making and allow organizations to respond swiftly to changing demands in the marketplace.
Historical Context
The evolution of warehouse management technologies has been significant over the past few decades. Initially, warehouses relied on manual processes, which resulted in inefficiencies and errors. As globalization and e-commerce grew, the need for more sophisticated systems intensified. FedEx recognized this shift early on and developed its WMS to offer improved inventory control and order management solutions. Understanding this historical backdrop highlights not only the necessity of such systems but also the advantages FedEx has in an industry marked by rapid technological advancements.
With the introduction of FedEx WMS, businesses can now experience smoother operations through integrated warehousing capabilities. The system is designed to adapt and grow with the organization, ensuring that as logistics needs change, the necessary framework is in place to handle these transformations.
Core Features of the FedEx WMS
The core features of the FedEx Warehouse Management System are critical for understanding how it optimizes warehousing processes. These functionalities address various needs within inventory control, order processing, and shipping solutions. Companies aiming to enhance their logistics often start by evaluating these features. An effective WMS revolutionizes warehouse operations by ensuring accuracy and speed. In a highly competitive market, mastering these elements can distinguish a business from its peers.
Inventory Management
Inventory management is pivotal to the success of any supply chain. Within the FedEx WMS, this module provides real-time visibility into stock levels. It allows businesses to track merchandise from receipt to shipment. Key functionalities include:
- Stock Audits: Regular inventory checks to ensure accuracy.
- Automated Reordering: Triggers orders when stock levels drop below predetermined thresholds.
- Barcode Scanning: Uses scanning devices to quickly identify products, minimizing error.
These functions improve stock accuracy and prevent overstock situations, which can tie up capital. Better inventory management can lead to improved cash flow, as goods turn faster and reduce holding costs.
Order Fulfillment
Order fulfillment is another essential feature that the FedEx WMS excels in. This function guides the process from order entry to delivery. Efficient order fulfillment increases customer satisfaction and can lead to repeat business. The key aspects include:
- Pick and Pack Technology: Streamlines the picking process by directing warehouse employees to the most efficient paths.
- Multi-Order Processing: Enables workers to process multiple orders simultaneously.
- Real-Time Order Tracking: Provides updates on order status, fostering transparency with customers.
These processes reduce fulfillment times significantly. The faster a business can get products to customers, the more competitive it becomes.
Shipping Integration
Shipping integration is the final core aspect that ties together the entire system. FedEx WMS offers seamless connections with various shipping platforms. This integration ensures that packages are delivered efficiently while maintaining low shipping costs. Major features in this area include:
- Labeling Automation: Automatically generates shipping labels based on order data.
- Carrier Rate Comparison: Evaluates different shipping options to find the best rates.
- Tracking Capabilities: Integrates tracking information within the system, allowing staff and customers to receive status updates.
These features provide flexibility in shipping methods and can substantially enhance customer service. By allowing businesses to efficiently manage their entire logistics process, the FedEx WMS effectively addresses modern shipping demands.
Benefits of Implementing FedEx WMS
The implementation of the FedEx Warehouse Management System (WMS) brings numerous advantages to organizations involved in supply chain management. An effective WMS can significantly enhance logistical operations. Businesses can achieve better control, streamlined processes, and improved customer satisfaction. Understanding these benefits is essential for decision-makers when choosing a WMS.
Operational Efficiency
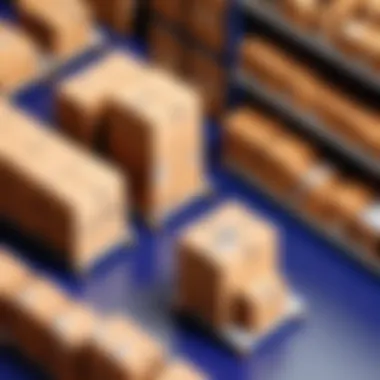
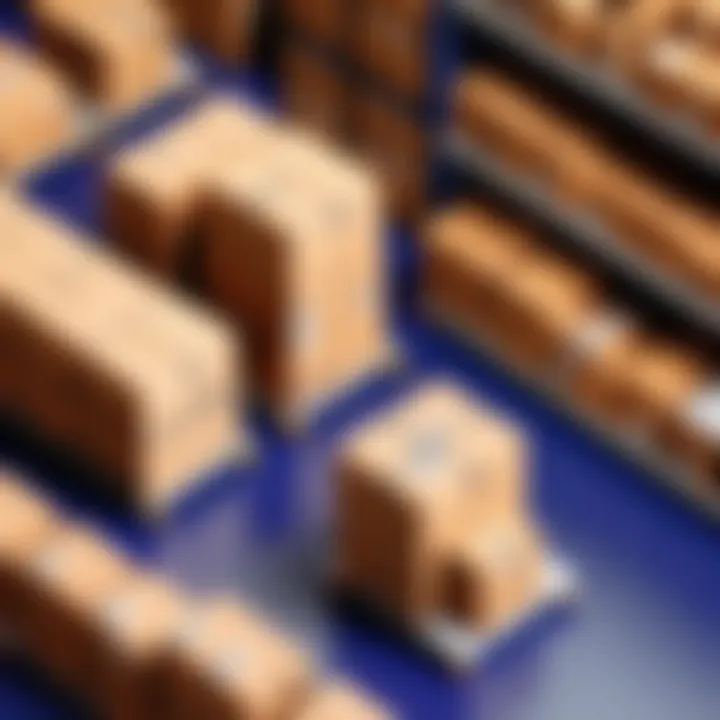
One of the primary benefits of the FedEx WMS is operational efficiency. By automating key processes, the system minimizes manual tasks and reduces the likelihood of human error. This automation leads to faster order processing and inventory management.
Consider the following aspects:
- Inventory Accuracy: With precise tracking systems, inventory levels can be monitored in real time. This reduces time spent searching for products, which can lead to delays.
- Streamlined Workflow: Operations such as picking, packing, and shipping can be optimized. Workers can prioritize tasks efficiently.
- Real-Time Data Insights: The WMS provides data on inventory movement, helping managers make informed decisions quickly. This capability is paramount during peak seasons.
Cost Reduction
Implementing the FedEx WMS can lead to substantial cost reduction for organizations. Here’s how:
- Labor Costs: By automating various processes, less manpower is needed for tasks like inventory checks and order fulfillment. Staff can focus on higher-value activities.
- Reduced Errors: Errors in order fulfillment can be expensive. The use of scanning technologies and automated systems significantly reduces these mistakes. This results in lower return rates and less associated costs.
- Space Optimization: Efficient inventory management can free up warehouse space. This can decrease overhead costs, translating to financial savings.
Enhanced Customer Satisfaction
Finally, enhancing customer satisfaction is crucial for any business, and the FedEx WMS excels in this area. Here are some reasons:
- Faster Delivery Times: With efficient warehouse processes, customers can expect quicker processing of their orders, leading to faster delivery.
- Accurate Order Fulfillment: Fewer mistakes in order shipments mean customers receive exactly what they ordered. This builds trust and encourages repeat business.
- Transparency and Communication: The FedEx WMS allows for improved communication with customers regarding order status. Knowing where their orders are enhances customer experience.
In summary, the benefits of implementing the FedEx WMS are significant. Operational efficiency, cost reduction, and enhanced customer satisfaction create a compelling case for businesses looking to improve their logistics.
"Implementation of an effective WMS not only streamlines operations but also significantly contributes to a company’s profitability and competitive advantage."
By carefully evaluating these benefits, businesses can make informed decisions while selecting the right WMS to suit their needs.
Integration with Existing Systems
Integrating the FedEx Warehouse Management System (WMS) with existing systems is a crucial aspect that can significantly influence the success of implementation. This process enables businesses to maintain their current workflows while benefiting from the advanced functionalities offered by FedEx. The integration ensures seamless data flow between various platforms, such as enterprise resource planning (ERP) software and customer relationship management (CRM) systems. This connectivity results in improved accuracy, efficiency, and overall performance of the supply chain management.
One major benefit of integration is enhanced data visibility. When WMS is integrated with existing systems, stakeholders can access real-time data across the supply chain. This transparency aids in making informed decisions, which can lead to optimized inventory levels and faster order fulfillment. For example, businesses can easily track product movements, identify trends, and adjust operations accordingly.
However, there are also considerations to keep in mind regarding integration. Compatibility between systems is paramount. Businesses need to ensure that the FedEx WMS can communicate effectively with their current software infrastructures. This often involves evaluating the technical specifications of both systems to confirm software compatibility.
Software Compatibility
Software compatibility plays a critical role in ensuring successful integration. Companies must assess their existing technology stack to determine whether the FedEx WMS can be smoothly incorporated. Incompatibilities can lead to data silos, where valuable information is not shared effectively across platforms.
To achieve effective integration, organizations should consider:
- System Requirements: Identify the hardware and software specifications needed for the FedEx WMS. Companies must evaluate their current infrastructure to see if upgrades are necessary.
- Flexibility: Check whether existing systems can be adapted to accommodate new functionalities offered by the FedEx WMS. This might involve additional investments in software development.
- Vendor Support: Support from FedEx for integration-related challenges can be essential. Evaluate the resources they provide, including documentation and technical assistance.
APIs and Custom Integrations
Application Programming Interfaces (APIs) and custom integrations are powerful tools that facilitate communication between FedEx WMS and existing systems. APIs enable different software applications to communicate, allowing for data exchange in real-time. This is particularly beneficial for businesses that require immediate updates on inventory levels or order status.
Custom integrations may also be necessary in some cases. Organizations may have unique processes or specific requirements that standard solutions do not address. In these situations, businesses can develop tailored solutions that meet their specific operational needs. Customization can ensure that:
- Business Processes Are Maintained: Integration with FedEx WMS does not disrupt existing workflows but rather enhances them.
- User Experience Is Improved: Employees can work with a unified system that reduces the complexity of navigating multiple platforms.
- Long-term Compatibility Is Achieved: As businesses grow, custom integrations can be adjusted and scaled to ensure continued alignment with evolving operational needs.
Integration with existing systems transforms how warehouses operate, making processes more efficient and data-driven. This pivotal step should not be overlooked during the planning phases.
Deployment Strategies
Deployment strategies are critical for organizations looking to implement the FedEx Warehouse Management System (WMS). These approaches determine how businesses will integrate the software into their existing logistics infrastructure. A well-thought-out deployment can significantly enhance the efficiency of warehouse operations, minimize disruptions, and ensure a smoother transition.
Businesses must consider their unique needs when choosing a deployment strategy. Factors such as scale, available resources, and long-term objectives play a vital role in decision-making. The two primary deployment options to consider are cloud-based solutions and on-premises installations. Both options come with specific advantages and considerations that can impact a company's operations and overall satisfaction with the system.
Cloud-Based Solutions
Cloud-based solutions offer various benefits, particularly for organizations that prioritize agility and scalability. With this deployment model, the FedEx WMS operates over the internet, allowing businesses to access their systems remotely. This presents several key advantages:
- Lower Initial Investment: There is typically no need for substantial hardware investments since the software is hosted online. This can be particularly beneficial for small to medium-sized enterprises.
- Scalability: Companies can easily scale their usage of the system according to their operational needs. This flexibility enables them to adjust resources without major disruptions.
- Automatic Updates: Providers often manage software updates and maintenance, relieving internal teams of this responsibility and ensuring users always have the latest features.
Nonetheless, cloud-based deployment has drawbacks. Organizations might face data security concerns. It’s essential to understand the provider’s security measures and compliance with data regulations. Additionally, internet outages could temporarily hinder access to the WMS, which is why a robust internet connection is crucial.
On-Premises Installation
Conversely, on-premises installations involve hosting the FedEx WMS on the organization’s own servers. This deployment strategy is often favored by larger enterprises or those with complex requirements. Here are some considerations:
- Control Over Data: On-premises solutions can provide a greater level of control over sensitive data. Companies can implement their own security protocols.
- Customization: Organizations can tailor the system to meet their specific operational needs more extensively. This can enhance the WMS's effectiveness in managing unique logistics challenges.
- Integration with Legacy Systems: Businesses with existing in-house systems may find that on-premises installations allow for smoother integration without relying on external web connections.
However, this deployment method comes with its own set of challenges. Initial costs can be high, given the need for dedicated servers and IT support. Furthermore, organizations must manage maintenance and software updates, which can strain internal resources.
In summary, the choice between cloud-based solutions and on-premises installations depends largely on an organization’s operational needs, budget, and long-term strategic goals. Understanding these nuances is crucial for decision-makers to optimize their warehouse management capabilities.
Scalability and Future-Proofing
Scalability is a vital component of any Warehouse Management System, including FedEx's WMS. For decision-makers and IT professionals, understanding its significance ensures the chosen system can grow alongside the business. This adaptability is crucial as it allows companies to respond to market dynamics without overhauling their entire infrastructure.
When considering scalability, it involves the ability of the WMS to handle increased transactions as business volumes rise. This means that as a company expands its operations, whether by increasing product lines or geographical reach, the WMS must manage larger inventories and heightened order fulfillment needs without performance degradation.
Adapting to Business Needs
Flexibility in a WMS allows it to serve varying operational demands. Businesses at different stages of growth have unique requirements. For instance, a startup may prioritize cost-effectiveness and basic features, while an established enterprise might need advanced analytics and additional functionalities.
The FedEx WMS accommodates this by providing customizable solutions. Users can select specific features and functionalities that align with their current needs, while also having the option to scale up as they grow. This is beneficial because it minimizes wasted resources, ensuring that businesses invest only in what they require at a given time.
Some of the factors affecting adaptability include:
- Volume Fluctuations: The system must efficiently handle peak seasons and fluctuations in orders, maintaining performance.
- Geographical Expansion: For companies entering new markets, the WMS should support additional warehouses without complicated integrations.
- Technology Trends: As advancements arise, a scalable WMS can integrate new technologies such as automation and data analytics without extensive retraining.
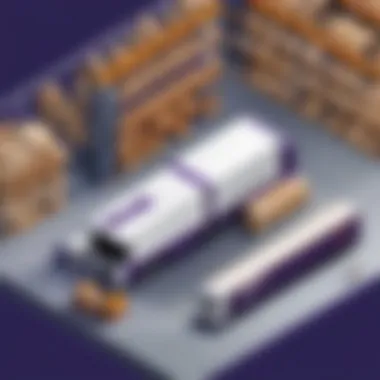
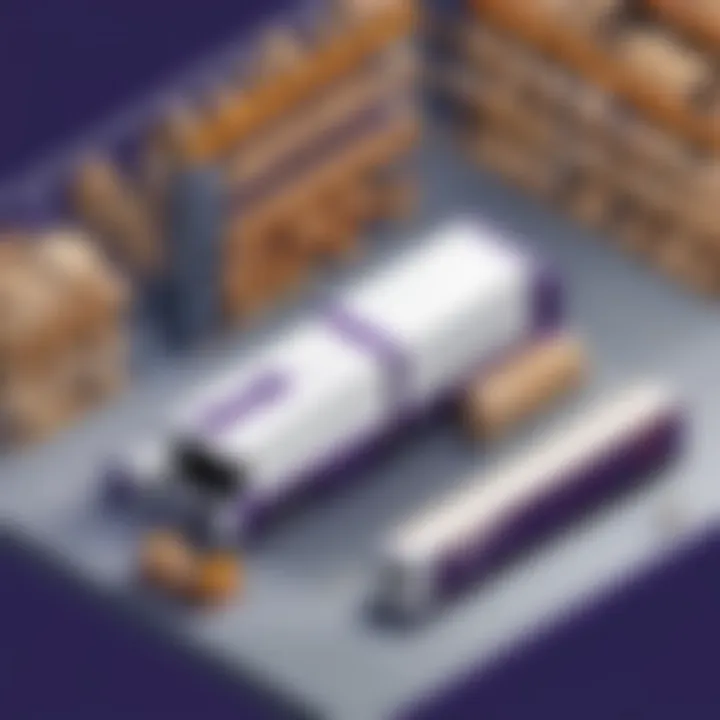
Long-Term Viability
Considering long-term viability, businesses should focus on solutions that will not only meet current needs but also anticipate future challenges. A future-proof WMS, like that offered by FedEx, is designed with foresight into technological changes and evolving market demands.
Being future-proof entails:
- Regular Updates: FedEx provides continuous improvements to its WMS, ensuring it remains competitive and efficient over time.
- Integration Capabilities: As new technologies emerge, the WMS must integrate seamlessly with these innovations, enhancing operational efficiency.
- Support Structures: Comprehensive support and training are crucial. Proper user training ensures that employees can leverage the system's full potential, minimizing disruptions during transitions or upgrades.
"Scalability and future-proofing are not just features; they are necessities for sustained operational success in a volatile market."
In summary, a scalable and future-proof WMS is essential for businesses aiming for long-term resilience and growth. FedEx's WMS stands out for its adaptability and forward-thinking design, capabilities that prepare companies for both current and future challenges in warehouse management.
Technical Requirements
The technical requirements for the FedEx Warehouse Management System (WMS) play a crucial role in ensuring its successful implementation and ongoing functionality. These requirements encompass both hardware and software aspects that businesses must consider before adopting the solution. Properly assessing these elements can help organizations minimize challenges and ensure a seamless integration process.
Hardware Specifications
When considering the hardware specifications for the FedEx WMS, businesses need to evaluate several components that will support the system's operations. Some key factors to contemplate include:
- Server Requirements: The WMS should be hosted on robust servers capable of handling the processing demands. This includes sufficient RAM, CPU power, and disk space to manage large datasets and facilitate real-time transactions.
- Network Infrastructure: A reliable network infrastructure is essential for ensuring smooth communications between the WMS and other systems. This means investing in high-speed internet connections and secure network protocols.
- RFID and Barcode Scanners: For real-time inventory tracking, RFID and barcode scanners are often required. These tools enhance the accuracy of inventory counts and expedite the picking and shipping processes.
- Workstation Devices: Employees will need to access the system through dedicated workstations or mobile devices. Organizations must ensure that these devices have the necessary specifications to run the WMS efficiently.
These hardware elements, when configured correctly, form a foundation for operational success. They contribute to faster processing times, reduced downtime, and overall improved efficiency in warehouse operations.
Software Prerequisites
In addition to hardware, the software prerequisites must be carefully examined to guarantee compatibility and functionality. The following points are important:
- Operating System Compatibility: The FedEx WMS may require a specific operating system. Organizations should check if their current systems align or if upgrades are necessary.
- Database Management Systems: A compatible database management system is crucial for data storage and retrieval. Businesses may need to ensure they utilize update-to-date versions that integrate well with the FedEx WMS.
- Integration Capabilities: The software must have the ability to easily integrate with existing systems, such as ERP or CRM software. Failing to achieve proper integration can lead to inefficiencies and data silos.
- Security Software: Given the sensitive nature of the data handled by the WMS, robust security measures are required. Firewalls, antivirus programs, and intrusion detection systems should be implemented to protect the infrastructure.
Evaluating the software prerequisites helps firms avoid integration pitfalls. A solid software foundation significantly contributes to enhanced workflow and improved data management capabilities, which are essential for effective warehouse operations.
Considerations in technical requirements are crucial. neglecting these can result in poor system performance and disrupt warehouse operations.
User Experience and Interface
User Experience (UX) and Interface are critical components in the functionality of the FedEx Warehouse Management System. A well-designed user interface ensures that the system is intuitive and accessible, which is particularly important for warehouse staff who may operate under time constraints. Understanding the user experience can drastically impact operational efficiency. Proper design decisions can streamline processes, reduce error rates, and lead to a more proficient workforce. Moreover, as the system is integrated into existing logistics frameworks, a positive user interface will smoothen the transition for employees.
User Interface Design
User interface design encapsulates the visual aspects and interactions of the warehouse management system. It encompasses everything from screen layouts, color schemes, to navigational elements. A clean and organized interface minimizes confusion, allowing team members to complete tasks with ease. For example, using larger buttons and clear labels can significantly improve response time in high-pressure scenarios.
Some key elements of effective user interface design include:
- Clarity: Users should understand their current task at a glance.
- Consistency: Similar functionalities should look and behave in the same manner.
- Feedback: Interactions should prompt immediate responses, ensuring users know their actions were registered.
Incorporating these elements leads to a swift adaptation to the system and enhanced productivity within the warehouse.
Training and Support
Training and support are essential in maximizing the utility of the FedEx Warehouse Management System. Even a highly efficient interface may not yield benefits without proper training. Tailored training programs can familiarize users with system features, reducing the learning curve.
Several considerations around training and support include:
- Availability: On-demand training resources should be accessible at any moment.
- Variety of Formats: Providing training via video, manuals, and interactive sessions can cater to differing learning styles among employees.
- Continuous Support: A dedicated helpdesk or a robust library of FAQs can assist users long after initial training.
"Investing in comprehensive training not only enhances user confidence but also ensures adherence to best practices in warehouse management."
By prioritizing these aspects of user experience and interface, companies can leverage the FedEx Warehouse Management System to its full potential, ensuring smoother operations and an overall enhanced experience for everyone involved.
Cost Considerations
When evaluating the FedEx Warehouse Management System, cost considerations play a vital role. Understanding the financial implications of adopting this system helps organizations to make informed decisions. Certain elements regarding costs can potentially shape the future success of supply chain operations.
Initial Investment
The initial investment in implementing the FedEx Warehouse Management System involves several factors. Firstly, one must consider the software licensing fees. These costs include the price for access to the system. In addition, there are hardware requirements to meet the operational demands of the WMS. Specific hardware might include servers, computers, and barcode scanning devices.
Integration costs may also arise. These costs relate to connecting the WMS with existing systems, such as Enterprise Resource Planning (ERP) software. Hiring specialized consultants for implementation can incur expenses. Thus, it’s essential to evaluate the total cost of ownership.
Initial training costs for staff should not be overlooked. Employees need to be well-versed in using FedEx’s system effectively. Therefore, allocating a budget for training sessions is crucial to ensure smooth operations from the start.
Operational Costs
Operational costs represent the recurring expenses related to running the FedEx Warehouse Management System. These costs can significantly affect a company’s budget and profitability. A few core elements comprise ongoing operational costs.
- Subscription Fees: If using a cloud-based solution, regular subscription fees will apply. These fees often depend on the level of service and support required.
- Maintenance Costs: Like any system, the WMS requires regular updates and maintenance. Allocating funds for maintaining system integrity and security is essential to prevent lapses.
- Staffing: The system may need dedicated staff or IT professionals for ongoing management. This need could add labor costs that organizations must consider.
- Support Services: Organizations often require technical support after implementation. Whether through FedEx or third-party providers, ongoing support costs should be factored into long-term budgeting.
Consideration: Thorough analysis of both initial and operational costs is critical for successful implementation and sustainability of the FedEx WMS. Without careful planning, unforeseen expenses may arise, impacting overall success.
Case Studies and Success Stories
The section on case studies and success stories serves a paramount role in understanding the FedEx Warehouse Management System. These real-life examples provide insights into the practical applications of the WMS in diverse contexts. They illustrate the tangible benefits that organizations can achieve through the deployment of this system. The analysis of case studies showcases how various companies have overcome challenges, streamlined operations, and improved customer satisfaction through the use of FedEx WMS.
High-Performance Warehouses
High-performance warehouses are often characterized by their efficient operations and ability to adapt quickly to changing market demands. FedEx WMS has been adopted by numerous high-performing warehouses, which leverage its capabilities to optimize inventory management, enhance order accuracy, and reduce lead times.
These warehouses typically have robust strategies and employ technology solutions that align with the features offered by FedEx WMS.
For instance, a major retailer implemented FedEx WMS to manage a growing volume of inventory across multiple locations. By doing so, they were able to achieve a 30% reduction in order processing time. This increase in speed not only improved operational efficiency but also elevated the overall customer experience. Efficient management of stock levels allowed for quicker shipping times and fewer backorders, key elements for high-performance warehouses.
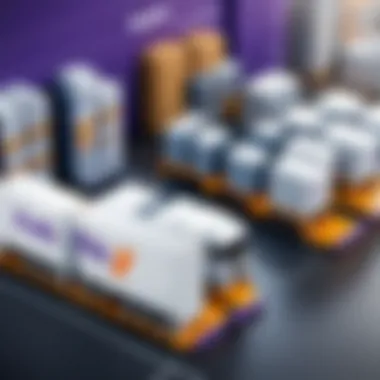
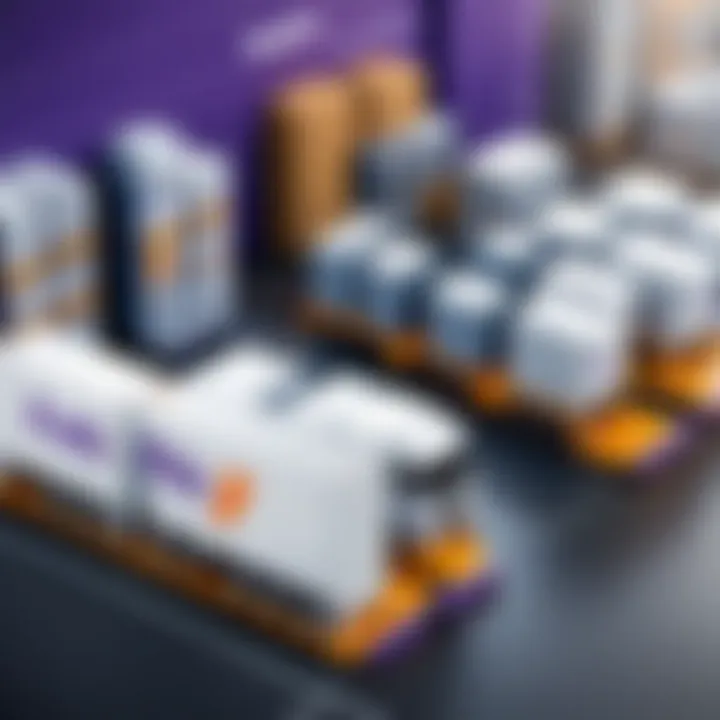
Customer Testimonials
Customer testimonials provide powerful endorsements for the FedEx Warehouse Management System. They serve as compelling evidence of the system's impact on productivity and overall operational effectiveness. Many users have reported significant improvements in areas such as inventory accuracy, shipping efficiency, and responsiveness to customer inquiries.
One notable testimonial from a logistics manager at an e-commerce firm highlights the benefits of using FedEx WMS. They noted, "After integrating FedEx WMS, our inventory accuracy improved from 85% to 98%. This change has been crucial in helping us meet our customer demands without excess stock. We can now fulfill orders much faster than we ever could before."
These testimonials underscore the reliability and efficiency of FedEx's WMS technology, affirming its value for businesses aiming to enhance their supply chain operations. Real-life success stories foster an understanding of the system's capabilities and align closely with the decision-making processes of IT professionals and business leaders.
Challenges and Limitations
Understanding the challenges and limitations of the FedEx Warehouse Management System (WMS) is crucial for organizations considering its implementation. Any system, regardless of its capabilities or reputation, can present various obstacles during and after its integration into existing workflows. This knowledge equips decision-makers and IT professionals to anticipate issues, allocate resources more effectively, and ensure smoother transitions. Moreover, recognizing the limitations helps businesses align their expectations with the system's actual performance.
Implementation Difficulties
Implementing FedEx WMS can pose several difficulties, primarily stemming from the need for comprehensive planning and proper resource allocation. A successful deployment requires a clear understanding of the organization's unique needs and the necessary configurations in the system.
- Customization Needs: Every warehouse has its own operational processes, which may necessitate customization of the FedEx WMS. This customization can slow down the implementation timeline and increase project costs.
- Integration with Legacy Systems: Many businesses rely on existing systems that may not be fully compatible with FedEx WMS. This incompatibility can cause disruptions and require additional technical work to enable seamless data transfer.
- Staff Training: Ensuring that staff are proficient in using the new system is another challenge. Lack of adequate training can lead to mistakes and inefficiencies.
These difficulties highlight the need for careful planning and execution during the implementation phase.
Ongoing Maintenance
Once FedEx WMS is successfully implemented, ongoing maintenance becomes a vital aspect of its usage. Regular updates and system checks are necessary to keep the system functioning optimally.
- Software Updates: FedEx continuously improves its WMS. Staying current with these updates is essential to leverage new features, enhance security, and avoid potential downtimes.
- User Support: Organizations need to provide continuous user support. Regular assistance can help address issues quickly before they escalate.
- Performance Monitoring: System performance should be monitored consistently to identify any degradation in efficiency. Setting up regular audits can assist in recognizing areas that require attention or improvement.
Efficient ongoing maintenance minimizes the chances of larger issues developing and ensures the system continues to meet the organization's evolving needs.
Proper planning surrounding both implementation and maintenance can significantly mitigate risks associated with adopting FedEx Warehouse Management System.
Regulatory Compliance
Regulatory compliance is a critical consideration for businesses utilizing the FedEx Warehouse Management System (WMS). As supply chains become increasingly complex, adhering to industry regulations ensures operational integrity, legal compliance, and protection of the organization’s reputation. Non-compliance can lead to significant legal and financial consequences, exposing companies to penalties, litigation, and reputational damage. Therefore, developers and users of the FedEx WMS must be aware of and integrate these regulatory requirements into their operational processes.
Meeting Industry Standards
Compliance with industry standards is essential for maintaining quality and consistency in warehouse operations. Warehouse management systems must align with various standards, such as the International Organization for Standardization (ISO) certifications and Occupational Safety and Health Administration (OSHA) regulations. These standards not only enhance operational efficiencies but also establish benchmarks for performance that can lead to industry recognition.
- ISO Certifications: Implementing processes that meet these international standards can improve product quality and operational efficiencies.
- OSHA Regulations: Compliance ensures safer workplace conditions, thereby reducing the risk of accidents and related costs.
Staying compliant with these standards can also provide a competitive advantage, as customers increasingly favor companies that demonstrate a commitment to quality and safety.
Data Security Regulations
In the digital age, data security regulations are paramount, especially for companies handling sensitive information. The FedEx WMS processes vast amounts of data, including customer information, shipping details, and inventory records. Compliance with data protection laws, like the General Data Protection Regulation (GDPR) and the Health Insurance Portability and Accountability Act (HIPAA), is necessary to safeguard this data. Failure to comply with these laws can result in severe consequences for both the organization and its clients.
Key considerations include:
- Data Encryption: Ensuring that data in transit and at rest is coded to prevent unauthorized access.
- Access Controls: Implement rigorous access protocols to ensure only authorized personnel can access sensitive information.
- Regular Audits: Conduct frequent assessments to identify and remedy any potential vulnerabilities in data management practices.
"Meeting regulatory requirements is not just about compliance; it fosters trust among clients, enhancing their overall experience and loyalty towards the brand."
In summary, failing to address regulatory compliance in the FedEx WMS landscape can have far-reaching consequences. By focusing on meeting industry standards and adhering to data security regulations, companies can position their operations for success in the competitive logistics and warehousing sector.
Future Trends in Warehouse Management
The landscape of warehouse management is undergoing significant transformation. As businesses seek to optimize their operations, understanding future trends becomes essential. This section will explore automation, robotics, and the utilization of artificial intelligence in warehouse management, and their implications for companies like FedEx. Leveraging these trends can foster efficiency, reduce errors, and ultimately enhance customer satisfaction.
Automation and Robotics
Automation is a cornerstone of modern warehouse management. This trend involves the use of technology to perform tasks with minimal human intervention. With the increase in e-commerce, the demand for faster and more accurate order fulfillment has grown.
Benefits of Automation:
- Efficiency Improvements: Automated systems can process orders and manage inventory quicker than manual methods. This can lead to higher throughput and reduced lead times.
- Reduced Labor Costs: Automation can decrease the need for manual labor, thereby lowering operational expenses over time.
- Minimized Errors: Automated systems often have built-in checks that ensure accuracy and consistency, reducing human error.
Robotic solutions in warehouse settings are also becoming more prevalent. Robots can handle various tasks, including picking, packing, and transporting goods within the warehouse.
"The integration of robotics can drastically change the efficiency and reliability of warehouse operations, leading to a significant competitive edge."
Artificial Intelligence Utilization
The integration of artificial intelligence (AI) into warehouse management systems is a promising trend that can revolutionize the logistics industry. AI technologies analyze vast sets of data to identify patterns and make informed decisions. This capability can optimize several aspects of warehouse operations.
Considerations with AI:
- Predictive Analytics: AI can foresee demand trends, allowing for more accurate inventory management and avoiding stock shortages or surpluses.
- Dynamic Routing: AI algorithms can determine the most efficient routes for product movement, reducing transit times within the warehouse and improving delivery efficiency.
- Enhanced Decision Making: By analyzing performance metrics, AI can assist managers in making more informed operational decisions, leading to better outcomes.
Finale
The conclusion of this article serves as a pivotal point to reflect on the insights gained throughout the examination of the FedEx Warehouse Management System. Understanding this system is crucial for businesses looking to enhance their supply chain processes. Several specific elements emphasize its importance.
Summarizing Key Points
The FedEx Warehouse Management System offers numerous advantages. Firstly, it supports operational efficiency and optimizes inventory management. Secondly, the system aims to decrease costs associated with warehousing and operations. Enhancing customer satisfaction is another vital aspect, as timely and accurate order fulfillment aligns with consumers' expectations.
Also, integrating the system with existing IT frameworks can lead to seamless operations. The adaptability of the WMS allows for scalability, suiting both small enterprises and large organizations, which needs continual growth. Ultimately, understanding these points can empower decision-makers to make informed choices about the software that will drive their warehousing success.
Final Thoughts on Implementation
Implementing the FedEx WMS is not just about adopting new software; it necessitates a strategic approach to change management. Companies need to consider their technical requirements and ensure their teams are prepared for any transitions. Training and support are essential components for successful implementation.
Businesses must evaluate the potential return on investment and operational improvements against the initial costs. This balance is critical for maintaining profitability while enhancing operational capabilities. With a clear plan and the right mindset, companies can leverage the FedEx WMS to achieve long-term benefits and remain competitive in a rapidly evolving market.
"Incorporating a sophisticated WMS like the one from FedEx is more than an upgrade—it's a transformative step towards streamlined logistics operations and improved service delivery."