Food Industry Inventory Management Best Practices
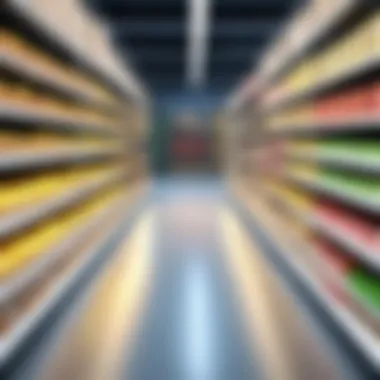
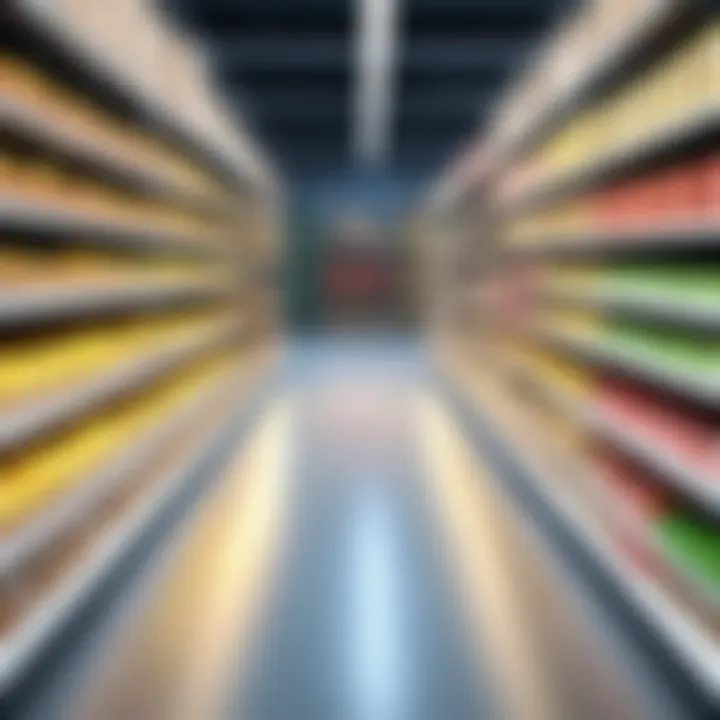
Intro
Inventory management is a pivotal component within the food industry, influencing not only operational efficiency but also cost control and customer satisfaction. The global nature of food distribution, coupled with stringent regulations, makes effective inventory practices essential. However, the challenge is significant. Stakeholders often contend with fluctuating demand, perishable goods, and the necessity for precise record-keeping. Moreover, innovative technologies have emerged, offering solutions to streamline and enhance inventory processes. Understanding these elements is crucial for decision-makers and entrepreneurs in the industry.
This detailed guide delves into best practices and technologies that can empower food industry players to optimize their inventory systems. The discussion will unfold the significance of accurate forecasting, regulatory compliance, and waste reduction. Moreover, it aims to illuminate the various software solutions available, providing clarity on their features and comparative advantages.
Software Category Overview
Definition and Importance
Inventory management software refers to tools designed to track inventory, manage orders, and provide analytics on stock levels. In the food sector, which is characterized by high turnover rates and strict compliance standards, such software becomes indispensable. It not only assists in maintaining optimal stock levels but also helps in enhancing visibility across the supply chain. Thus, proper inventory management tools can lead to reduced waste and improved customer satisfaction.
Key Characteristics
The effectiveness of inventory management software can be assessed through several key characteristics:
- Real-time Tracking: Immediate updates regarding stock quantities help prevent shortages and overstocking.
- Forecasting Tools: Advanced algorithms predict future inventory needs based on historical data and trends.
- Integration Capabilities: Seamless connection with other operational software like ERP or accounting systems is essential for efficiency.
- Regulatory Compliance Features: The software must assist in meeting industry-specific regulations, such as food safety protocols.
- User-Friendly Interface: An intuitive design helps staff engage with the system effectively, minimizing the chances of errors.
Comparative Analysis of Top Software Options
Feature Comparison
When examining different software options, it is crucial to compare features that align with food industry requirements. For instance:
- Fishbowl: Provides robust inventory tracking with real-time data. Ideal for medium to large businesses, it combines manufacturing and inventory management features.
- NetSuite: A comprehensive ERP solution that integrates all aspects of business operations, from order processing to financials, suitable for larger enterprises seeking a complete solution.
- MarketMan: Tailored specifically for the food industry, it offers inventory management with features like supplier management and recipe costing.
Pricing Models
Different software solutions adopt various pricing strategies. Some products charge a monthly subscription fee, while others may have a one-time licensing fee. For example:
- Fishbowl offers tiered pricing based on number of users and additional modules.
- NetSuite is typically known for a higher entry cost due to its comprehensive features, charging based on usage and additional functionalities.
- MarketMan uses a subscription model that varies by the size of the business and specific features chosen.
"Effective inventory management not only optimizes resources but also strengthens customer relationships and compliance frameworks."
In summary, understanding the nuances of inventory management software is vital for thriving in the food industry. By implementing robust systems, businesses can enhance efficiency, comply with regulations, and reduce waste.
Understanding Food Industry Inventory Management
Inventory management holds a critical position in the food industry, serving as the backbone of supply chain efficiency and operational excellence. The unique characteristics of food products, such as perishability and compliance with strict safety regulations, necessitate a nuanced approach to managing inventory. Effective inventory management not only ensures the availability of products but also minimizes waste and enhances profitability. This section will delve into the definition and importance of inventory management in the food industry, as well as its broad scope and applications.
Definition and Importance
Inventory management encompasses the processes and methodologies employed to oversee and control the flow of food products from suppliers to end customers. In the food industry, this domain is vital due to several factors. Perishable items require swift turnover, and mismanagement can lead to spoilage and financial losses. Moreover, the rapidly changing consumer demand necessitates precise forecasting to align inventory levels with market needs.
The importance of inventory management in the food sector can be summarized as follows:
- Waste Reduction: Efficient inventory practices directly diminish the volume of spoiled goods. This not only improves sustainability but also cuts costs.
- Cost Control: Through dynamic inventory assessments, businesses can optimize stock levels, reducing storage costs and improving cash flow.
- Regulatory Compliance: Strict regulations govern food safety. Proper inventory management aids in tracking product origins and expiry dates, ensuring compliance with health standards.
- Enhanced Customer Satisfaction: A well-maintained inventory ensures that food products are available when consumers want them, enhancing the overall customer experience.
"Good inventory management can make the difference between a successful food business and one that struggles with waste and inefficiency."
Scope and Applications
The scope of food industry inventory management is expansive, covering various aspects of product handling from production to consumption. The applications of inventory management in this sector are typically pragmatic and focuses on optimizing processes.
Key applications include:
- Supply Chain Coordination: Effective inventory management links different partners in the supply chain, ensuring timely deliveries and consistent product quality.
- Demand Planning: By utilizing historical data and market trends, businesses can forecast demand accurately, aligning their inventory with consumer purchasing patterns.
- Product Lifecycle Management: Monitoring the lifecycle of food products enables businesses to strategize when to introduce new items or phase out slow-moving ones.
- Technology Integration: Modern inventory management practices often involve sophisticated technology, such as software solutions that enable real-time tracking and data analysis.
In summary, understanding food industry inventory management involves recognizing its pivotal role in enhancing operational efficiency and meeting the demands of consumers and regulators alike.
Challenges in Inventory Management
The management of inventory within the food industry presents a variety of challenges that can significantly impact efficiency and profitability. Understanding these challenges is key to implementing effective practices and technologies. As stakeholders in this field pursue better inventory management solutions, they must be aware of the specific hurdles they may encounter. Addressing these challenges often requires tailored strategies that consider the unique attributes of the food sector.
Perishable Goods
Perishable goods pose one of the most pressing challenges in food inventory management. The limited shelf life of these items necessitates careful monitoring and control to prevent spoilage and waste. Proper handling from sourcing to distribution is crucial. Businesses must track expiration dates and manage turnover rates effectively. Failure to do so might lead to significant financial losses.
Effective management strategies include:
- Implementing FIFO: The First In, First Out method ensures that older stock is used before newer arrivals. This helps in reducing waste and maintaining product quality.
- Utilizing Inventory Alerts: Automated alert systems can notify managers about upcoming expiration dates, enabling timely action to either sell or discount products.
- Temperature Control Systems: For items sensitive to temperature changes, real-time monitoring systems can help maintain proper storage conditions. These approaches can significantly mitigate the risks associated with handling perishable items.
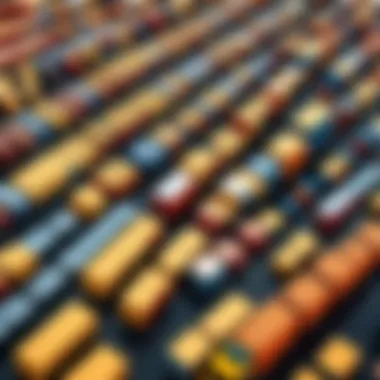
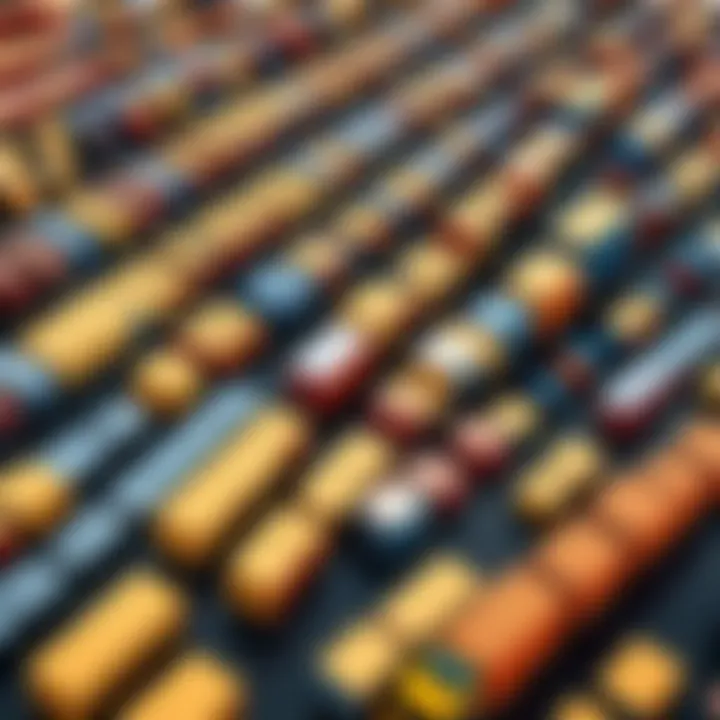
Supply Chain Disruptions
Supply chain disruptions are an ever-present risk within the food industry. Factors such as natural disasters, geopolitical issues, or even pandemics can impact the flow of goods from suppliers to consumers. These disruptions lead to unforeseen delays and can result in excess inventory or stock-outs.
To navigate these obstacles, businesses can utilize several strategies:
- Diversifying Suppliers: Relying on multiple suppliers can help mitigate risks associated with supply chain dependency.
- Agile Inventory Systems: Employing agile methodologies allows for quicker reactions and adaptations to changing circumstances.
- Regular Scenario Planning: Businesses should engage in regular assessments of their supply chain models, preparing for different scenarios that could impact operations. This forward-thinking approach can foster resilience and maintain inventory levels.
Regulatory Compliance
Regulatory compliance is another significant challenge. The food industry must adhere to stringent regulations regarding safety standards, labeling, and traceability. Non-compliance may result in serious penalties and damage to reputation. It is essential to integrate compliance measures into inventory management practices.
Key considerations include:
- Maintaining Documentation: Accurate and thorough record-keeping is vital. Documents should be easily accessible in case of audits or inspections.
- Regular Training: Continuous training programs for employees can help ensure that everyone stays updated on compliance standards and protocols.
- Investing in Compliance Technologies: Various software solutions are available that help track compliance requirements, thus reducing manual tracking errors.
Understanding these challenges is crucial for food industry stakeholders. Being proactive in addressing these issues not only enhances operational efficiency but also fosters sustainability and consumer trust.
Inventory Management Techniques
Effective inventory management techniques are crucial for maintaining order and efficiency in the food industry. These techniques help prevent stockouts, reduce waste, and ensure that businesses can meet customer demands. The selection of inventory management techniques can significantly impact a company's bottom line. By understanding and implementing these methods, stakeholders can optimize their operations and enhance their overall performance.
Just-In-Time (JIT) Inventory
Just-In-Time (JIT) inventory management is a methodology that aims to minimize inventory levels. The primary goal is to order and receive goods only as needed in the production process. This approach reduces storage costs and the risk of spoilage, which is particularly important in the food sector. By aligning orders closely with production schedules, businesses reduce waste and improve cash flow.
However, JIT demands precise coordination throughout the supply chain. Any disruption, such as delays from suppliers, can greatly affect production. Businesses must develop strong relationships with suppliers and utilize real-time data to monitor inventory levels accurately. The successful implementation of JIT leads to increased efficiency and lower operational costs.
First In, First Out (FIFO)
First In, First Out (FIFO) is a crucial method for managing perishable goods. In FIFO, the oldest inventory items are sold or used first. This method mitigates the risk of spoilage and ensures that products meet quality standards before they reach customers. For example, in a supermarket or restaurant, older ingredients are used first to maintain freshness and safety.
Utilizing FIFO requires regular monitoring of inventory. Firms must ensure that older stock is easily accessible. Automation tools that can track expiration dates and inventory aging can streamline FIFO management. Implementing FIFO not only prevents waste but also enhances customer satisfaction by guaranteeing fresh products.
Minimum Order Quantities
Minimum Order Quantities (MOQ) refer to the least amount of product a supplier is willing to sell to a buyer. Setting appropriate MOQs ensures that businesses can maintain sufficient stock levels without over-investing in inventory. In the food industry, where demand can fluctuate, MOQs play an essential role in balancing supply with consumer needs.
Adopting MOQs enables businesses to reduce order frequency, resulting in lower shipping costs. However, firms must analyze historical sales data to determine suitable MOQs. If set too high, businesses risk overstocking and potential waste, especially with perishable items. Conversely, if set too low, they may face stockouts, impacting sales and customer trust.
Technological Solutions for Inventory Management
Inventory management in the food industry increasingly relies on advanced technologies. These solutions streamline processes, create efficiencies, and minimize waste. Understanding the benefits and applications of such technologies is crucial for businesses aiming to optimize their inventory management.
Barcode Systems
Barcode systems provide a straightforward method for tracking inventory. Each product is assigned a unique barcode that can be scanned at various points in the supply chain.
Key benefits of barcode systems include:
- Quick data entry: Reduces human error and speeds up the process of inventory counts.
- Improved tracking: Allows for real-time updates on stock levels, helping prevent stockouts or overstock situations.
- Cost-effective: Generally low-cost to implement compared to other systems.
However, care must be taken when designing the layout of barcodes to ensure compatibility with scanning devices. Tracking needs to be regularly updated to maintain accuracy in inventory records.
Inventory Management Software
Inventory management software offers comprehensive solutions to manage stock levels, track orders, and forecast demand. These platforms integrate various operations within the supply chain.
Important features include:
- Centralized data management: Consolidates information from different departments, providing insights into purchasing and sales trends.
- Automated alerts: Notifies users when stock reaches predefined thresholds, optimizing reorder points.
- Historical data analysis: Enables businesses to identify patterns over time, improving future forecasting.
Selecting the right software involves assessing specific business needs, including the size of inventory and integration with existing systems. An appropriate choice can significantly enhance operational efficiency.
Real-Time Tracking Systems
Real-time tracking systems use technologies like RFID or IoT devices to monitor inventory levels instantly. This offers a sophisticated approach for businesses to keep tabs on their products throughout the supply chain.
Benefits of real-time tracking systems are:
- Immediate visibility: Provides accurate, up-to-date information about inventory status at any given moment.
- Enhanced accountability: Offers precise records of items, reducing losses and discrepancies.
- Better customer service: Fulfilling orders more efficiently leads to improved customer satisfaction.
When considering implementation, companies must evaluate their infrastructure and readiness to adopt such technologies. The investment in real-time systems can lead to significant long-term savings and advantages.
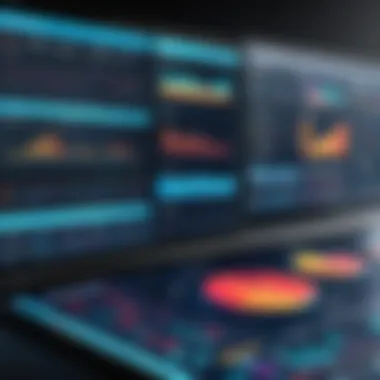
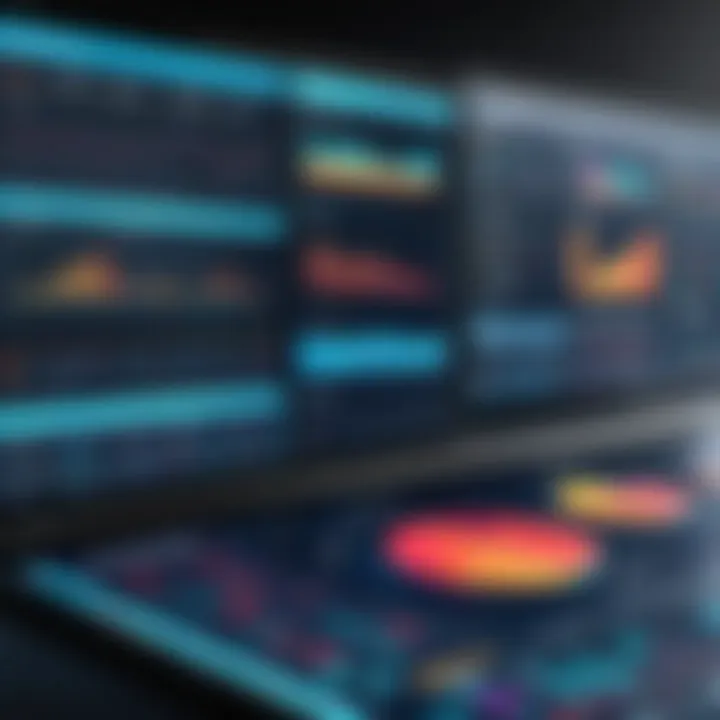
"Integrating technological solutions can make a profound difference in food industry inventory management, yielding both operational efficiencies and enhanced accuracy."
Key Metrics for Inventory Evaluation
In the food industry, effective inventory management is crucial for ensuring that products are stocked and rotated properly. Key metrics play a significant role in assessing the overall health and efficiency of inventory systems. By understanding these metrics, decision-makers can identify potential problems and optimize their inventory strategies. Evaluating these metrics enables businesses to make informed decisions while minimizing waste and maximizing profits.
Inventory Turnover Ratio
The Inventory Turnover Ratio is a fundamental metric that measures how often inventory is sold and replaced over a specific period. It is calculated by dividing the cost of goods sold (COGS) by the average inventory during that same period. A high turnover ratio indicates strong sales and effective inventory management, while a low ratio may suggest overstocking or stagnant sales.
In the food industry, where perishables must be sold quickly, this ratio is particularly important. It helps businesses maintain fresh stock and reduces losses due to spoilage. For example, if a company has a COGS of $1,000,000 and an average inventory of $200,000, the turnover ratio would be 5. This signifies that the company sells its inventory five times a year. Understanding and monitoring this metric can provide insights into product performance and aid in inventory forecasting.
Carrying Costs
Carrying costs represent the total expenses associated with holding inventory, including storage, insurance, spoilage, and opportunity costs. These costs can significantly impact a business's bottom line, especially in the food sector where perishability leads to increased spoilage. By calculating carrying costs, businesses can identify unnecessary expenditures and implement strategies to lower them.
It's vital to balance carrying costs with service levels. While keeping high inventory levels may reduce stock-outs, it also inflates carrying costs. Utilizing tools such as demand forecasting can aid in maintaining optimal inventory levels, thus minimizing carrying costs. Analyzing these expenses helps organizations manage their resources effectively while ensuring customer satisfaction.
Stock-Out Rates
Stock-Out Rates highlight the frequency at which items are unavailable for sale. This metric is essential for understanding customer service levels and assessing inventory strategies. High stock-out rates can lead to lost sales, damaged reputation, and customer dissatisfaction. In the food industry, stock-outs not only affect revenue but also can lead to further issues like wasted promotional efforts and supply chain disruptions.
To calculate the stock-out rate, divide the number of times a product was out of stock by the total number of times it was sold. Businesses should aim for a stock-out rate below an acceptable threshold, which varies according to the type of product and market demands. Monitoring this metric can inform restocking processes and improve forecasting accuracy, ultimately enhancing the customer experience.
Maintaining a balance in inventory metrics can significantly improve profitability and operational efficiency in the food industry. By concentrating on Inventory Turnover Ratios, Carrying Costs, and Stock-Out Rates, businesses can navigate challenges more effectively.
The Role of Forecasting in Inventory Management
Forecasting plays a pivotal role in effective inventory management within the food industry. It serves as the cornerstone of planning and decision-making. When companies accurately forecast demand, they can align their inventory levels effectively. This makes it easier to meet customer needs without overstocking or stockouts. Better forecasting reduces costs associated with excess inventory, such as storage and wastage.
Moreover, effective forecasting allows food businesses to optimize their supply chain. Accurate demand projections help in coordinating with suppliers, ensuring timely deliveries of fresh products. With fresh produce, this is especially vital due to limited shelf lives. Thus, it saves businesses from potential revenue loss due to unsold goods.
"Accurate demand forecasting is essential for maintaining an efficient inventory system in the food industry."
Demand Forecasting Techniques
There are several techniques used for demand forecasting. One popular method is historical sales analysis. This technique involves analyzing past sales data to identify patterns and trends. By understanding customer behavior during different seasons or events, businesses can make informed decisions about future inventory needs. For example, a spike in sales around holidays must inform businesses to stock up adequately.
Another effective technique is qualitative forecasting. This method depends on expert opinions and market research rather than solely on numerical data. Market conditions, customer preferences, and emerging trends inform these forecasts. Engaging with sales teams or conducting customer surveys helps gather qualitative insights, which can be immensely valuable.
Seasonal Trends and Adjustments
Understanding seasonal trends is key in managing inventory. Food demand often fluctuates with the seasons. Techniques like seasonal indexing can aid in adjusting forecasts. Seasonal indexing involves tracking sales data over different seasons to determine how demand changes.
For instance, ice cream sales rise in summer, while demand for baked goods often peaks during the winter holidays. By recognizing these patterns, businesses can adjust their inventory levels proactively.
Businesses should also stay flexible in their inventory management strategies. Adjustments may be necessary based on unforeseen factors like weather changes or global events. Continuously analyzing data and market conditions will enable firms to refine their approach, thus improving their overall forecasting accuracy.
Sustainability Considerations
Sustainability in the food industry is not just a trend but a critical framework aimed at ensuring that practices are environmentally sound and socially responsible. As consumers become increasingly aware of environmental issues, businesses within the food sector are recognizing the importance of sustainable inventory management. This involves minimizing waste, optimizing resource usage, and ensuring that operations have a positive impact on the environment. The drive towards sustainability helps to reduce operational costs in the long run, enhances brand reputation, and meets regulatory requirements.
One notable aspect of sustainability in inventory management is its potential to foster a circular economy, where practices are designed to minimize waste through continuous reuse and recycling. Companies that adopt sustainability considerations make strategic choices that positively impact both their bottom line and the environment.
Waste Reduction Strategies
Effective waste reduction strategies are vital. In the food industry, where products are often perishable, managing inventory without generating waste is a robust challenge. Employing an array of techniques can help businesses mitigate waste significantly. Strategies include:
- Strict Inventory Monitoring: Utilize advanced inventory management systems to track shelf life, ensuring stock rotation and reducing spoilage.
- Dynamic Demand Forecasting: Implementing tools that analyze historical sales data and customer trends, allows businesses to adjust orders proactively, avoiding overstocking.
- Smart Disposal: Develop plans for the proper disposal of food that cannot be salvaged, such as donating items near expiration to food banks.
These strategies require a commitment to regular reviews and adjustments as market conditions change. By embedding waste reduction in their practices, food companies can enhance both operational efficiency and sustainability.
Eco-Friendly Supply Chain Practices
Eco-friendly supply chain practices integrate sustainability at every stage of the inventory cycle. These practices focus on minimizing environmental impacts while ensuring that all aspects of the supply chain are efficient. Key components include:
- Sourcing Local Ingredients: This reduces transportation emissions and supports local economies.
- Energy-Efficient Storage Solutions: Utilizing technology that optimizes energy use in warehouses lowers carbon footprints significantly.
- Sustainable Packaging: Shifting to biodegradable or reusable packaging solutions reduces plastic waste and impacts on landfills.
According to estimates, businesses that implement eco-friendly practices may experience up to a 20% reduction in costs associated with waste and materials. Thus, a shift towards such practices not only addresses environmental concerns but also aligns with improving economic viability.
By fostering sustainable principles within inventory management, companies can deliver on their promise to consumers while enhancing their operational capabilities.
Inventory Management Best Practices
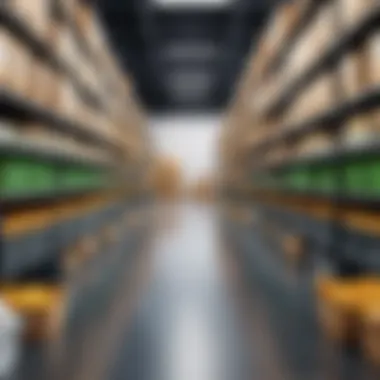
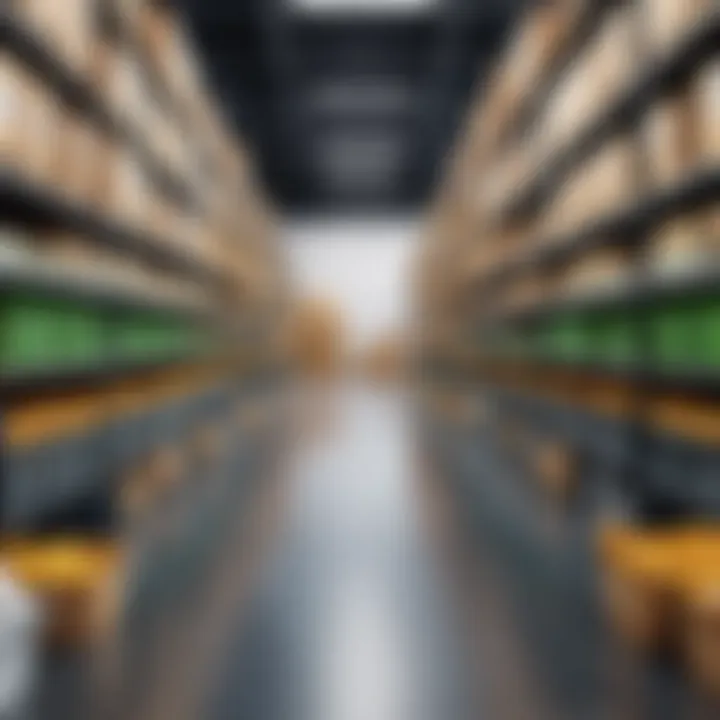
In the food industry, effective inventory management is crucial. It helps organizations maintain product quality, meet consumer demand, and comply with regulations. This section explores best practices that enhance inventory performance. It also identifies benefits that come from establishing disciplined practices. By adopting these strategies, stakeholders can better manage resources, minimize waste, and improve overall operational efficiency.
Regular Audits and Reviews
Conducting regular audits is an essential practice in inventory management. Audits help confirm that physical inventory matches documented records. This process allows organizations to detect discrepancies, which can arise from theft, spoilage, or mislabeling. Regular reviews also provide a chance to assess inventory turnover rates, ensuring products are moving as expected.
Additionally, audits enable managers to identify slow-moving items. This is critical in a sector where perishable goods dominate. By identifying these slow movers, companies can adjust their purchasing strategies. For instance, they might reduce orders or implement promotions to clear stock.
"Regular audits are not just about accuracy; they inform strategic decisions that can save costs and enhance customer satisfaction."
Moreover, conducting reviews involves evaluating suppliers' performance. Assessing supplier reliability and product quality ensures that only the best vendors are maintained. This, in turn, positively affects the overall supply chain efficiency.
- Benefits of Regular Audits:
- Identify discrepancies in stock levels
- Ensure compliance with industry regulations
- Recognize trends in inventory flow
- Facilitate informed decision-making
Employee Training and Engagement
Employee training is another vital aspect of effective inventory management. A knowledgeable workforce can significantly enhance inventory accuracy. Staff should be well-versed in utilizing management technologies, tracking systems, and maintaining compliance standards. Training programs should not only cover initial onboarding but also ongoing education to address new challenges.
Engaged employees also contribute to better inventory practices. When staff members understand the importance of their roles, they take ownership of their tasks. This can reduce errors and improve overall productivity. Effective communication fosters a collaborative environment where employees feel valued.
Regular workshops can reinforce training and update team members on the latest industry trends and technologies. Additionally, encouraging feedback from employees can lead to valuable insights. Those working on the front lines often identify areas for improvement that management might overlook.
In summary, fostering a culture of ongoing learning and engagement plays a pivotal role in shaping a strong inventory management framework. Ensuring employees are equipped with skills and are involved in processes enhances effectiveness.
- Key Elements of Employee Engagement:
- Comprehensive training programs
- Open lines of communication
- Recognition of contributions
- Opportunities for feedback and input
Incorporating these best practices can lead to sustainable improvement in inventory management within the food industry. Ultimately, the goal is to balance efficiency with an unwavering commitment to quality.
Case Studies in Food Industry Inventory Management
Case studies play a critical role in understanding effective inventory management practices within the food industry. They provide real-world examples that illustrate the challenges and successes encountered by various organizations. By examining diverse scenarios, stakeholders can gather insights, identify effective strategies, and adapt methodologies to their own operations.
The importance of case studies lies in their ability to highlight practical applications of theoretical concepts. They bridge the gap between academic learning and real-life execution. Each case brings unique aspects to light, allowing decision-makers to consider the nuances of inventory management in their specific contexts. Success stories can provide a blueprint, while lessons learned from failures can serve as cautionary tales. This dual perspective fosters a deeper comprehension of the intricacies involved in managing food inventories effectively.
Success Stories
Success stories from notable companies showcase innovative inventory management tactics that have led to significant improvements in efficiency and profitability. For instance, a prominent food retailer might implement a real-time inventory system that integrates with their supply chain. This change can result in optimized stock levels, reducing waste and ensuring product availability.
Another example is the use of advanced forecasting tools by a coffee manufacturer. By leveraging historical sales data, they can predict demand patterns accurately, allowing them to adjust production schedules proactively. This adaptability resulted in a marked decline in surplus inventory, which ultimately enhanced their bottom line.
Success stories demonstrate that with the right strategies and technologies, businesses can thrive, improving customer satisfaction while minimizing costs.
Lessons Learned from Failures
Conversely, analyzing failures in inventory management can unveil common pitfalls to avoid. For instance, a snack food company that depended solely on traditional inventory methods faced significant stock-out situations due to inaccurate demand forecasting. This led to dissatisfied customers and lost sales.
Additionally, a frozen food distributor that neglected to prioritize proper refrigeration during transport encountered severe product spoilage. The costs associated with these losses not only impacted finances but also tarnished their reputation.
These lessons emphasize the necessity of adopting a multifaceted approach. Investing in technology, implementing robust processes, and training staff are essential components that can prevent such failures. By reflecting on these experiences, other businesses can devise strategies to circumvent similar issues and implement more effective inventory management systems.
Future Trends in Inventory Management
The landscape of inventory management is evolving rapidly. In the food industry, adapting to these changes is crucial. Embracing future trends can provide efficiency, accuracy, and sustainability benefits. As technology becomes more integrated, it is vital for businesses to stay informed about innovations that could affect their operations. This section delves into two key trends: Artificial Intelligence and Machine Learning, as well as Blockchain technology, both of which offer immense potential to improve inventory management practices.
Artificial Intelligence and Machine Learning
Artificial Intelligence (AI) and Machine Learning (ML) are reshaping how inventory management is approached in the food industry. These technologies empower businesses to analyze vast amounts of data with speed and precision. One significant advantage is the ability to predict demand better. By using historical data, AI systems can forecast future inventory needs, reducing waste and increasing efficiency.
Another benefit lies in optimization. AI can help automate inventory replenishment levels based on real-time data. This ensures that stock levels are maintained without excess, which is particularly important for perishable goods. For instance, companies that implement AI-driven solutions can reduce spoilage, which is a common challenge in the food sector.
Moreover, these technologies facilitate enhanced decision-making. Businesses can assess market trends and consumer behavior more effectively. The insights gleaned from AI analyses can inform procurement decisions, pricing strategies, and promotional activities, ultimately allowing for a more nuanced approach to inventory management.
Adoption, however, requires careful consideration of integration with existing systems. Businesses need to invest in training personnel to manage and interpret AI outputs effectively.
Blockchain in Inventory Management
Blockchain technology is another emerging trend that holds promise for inventory management in food. It provides a decentralized ledger that ensures transparency and traceability throughout the supply chain. This feature is particularly relevant for the food industry, where safety and compliance are paramount.
With blockchain, every transaction—from the farm to the consumer—can be recorded securely. This transparency allows for real-time tracking of products, which is critical for recalling food items that may pose health risks. Additionally, stakeholders can verify the source of products, ensuring compliance with regulations and enhancing consumer trust.
Implementing blockchain can also streamline supply chain operations. By automating processes related to inventory management, companies can reduce delays and minimize errors. This innovation not only improves efficiency but also enhances the accuracy of inventory records.
However, the integration of blockchain technology requires collaboration across the industry. Various participants in the supply chain must agree on standards to realize its full potential.
Embracing these advancements is more than just a trend; it is a necessary evolution for decision-makers, IT professionals, and entrepreneurs looking to thrive in the food industry.