Ingredient Management Software: Key Benefits and Trends
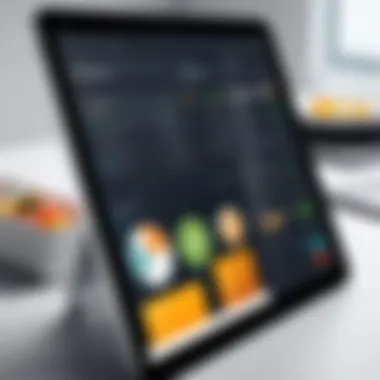
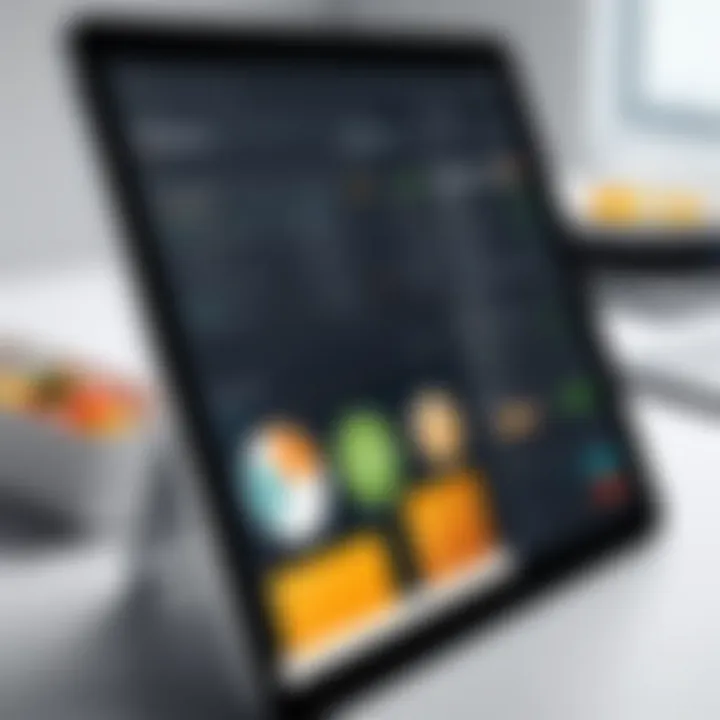
Intro
Ingredient management software has gradually emerged as a powerful ally in the food and beverage industry. It’s no secret that maintaining high standards of quality and compliance can be a logistical minefield. With regulations changing frequently, tracking ingredient origins, and managing inventory levels, it's a whirlwind for many professionals in this sector. Enter ingredient management software—a solution that promises to not just simplify, but revolutionize these processes.
In a landscape where every decision can impact both costs and consumer satisfaction, having a comprehensive view of ingredients is paramount. This software serves as a critical tool in providing insights into formulation management, ensuring that every batch meets quality standards, and complying with necessary regulations. With this in mind, we delve into the fascinating world of ingredient management software, examining its nuances, primary functions, and the distinct benefits it brings.
Software Category Overview
Definition and Importance
Ingredient management software can be seen as the backbone of operational efficiency in food-related businesses. It is designed to help organizations oversee their ingredient inventories—from raw materials to finished products—ensuring each element is accounted for and optimized.
This software is not just about maintaining records; it plays a crucial role in safeguarding against compliance issues that can lead to costly penalties. In an industry where precision is key, such tools offer a systematic approach to ingredient sourcing and supply chain management, allowing companies to focus on innovation and growth without getting bogged down by tedious paperwork.
Key Characteristics
When assessing ingredient management software, certain features stand out as essential:
- Real-time Inventory Tracking: This allows businesses to monitor their stocks and avoid running out or overstocking, leading to increased efficiency and reduced waste.
- Regulatory Compliance: Ensures that companies adhere to all local, national, and international food safety regulations. This can cover everything from labeling regulations to allergen control.
- Formulation Management: Helps in creating and adjusting recipes based on ingredient availability and cost, facilitating flexibility in production.
- Supplier Management: A robust supplier database can help in sourcing sustainable and high-quality ingredients while keeping track of supplier performance and compliance.
- Cost Management Tools: These are vital for analyzing ingredient costs and identifying opportunities for savings.
By incorporating these features, businesses can dramatically enhance their operational capabilities, meet consumer demands, and stay competitive.
Comparative Analysis of Top Software Options
Feature Comparison
With numerous software options lurking in the marketplace, selecting the right tool can feel like searching for a needle in a haystack. It's imperative to compare them based on features and not just price. Some notable platforms include Partie, V-Track, and TestJack, each offering distinct advantages:
- Partie: Known for its user-friendly interface and robust supplier management features, it's favored by companies focused on transparency in sourcing.
- V-Track: Offers advanced inventory management capabilities along with robust analytical tools for in-depth insights.
- TestJack: Excels in formulation management, allowing users to easily adjust recipes while keeping an eye on costs.
Pricing Models
Price is often a determining factor, but it shouldn't be the only thing one bases a decision on. Different software providers offer varying pricing structures:
- Subscription Models: Monthly or annual fees, typically based on features used.
- Tiered Pricing: Allows users to pick and choose capabilities, providing flexibility based on their needs.
- Pay-per-User Pricing: Charged based on the number of users accessing the software, which can be beneficial for smaller teams.
In making a choice, it’s essential to weigh the long-term benefits against initial costs to ensure that whatever solution is adopted aligns closely with business objectives.
"Choosing the right ingredient management software is not just about making a purchase; it’s about investing in the future of your business."
As we continue exploring ingredient management software, we will unfold the specifics of implementation and the exciting trends that shape its continuous evolution.
Understanding Ingredient Management Software
Ingredient management software stands as a cornerstone in the culinary and food processing sectors, playing a vital role in the direct handling of ingredients, assisting businesses in becoming more organized and efficient. Its significance extends far beyond merely logging stocks; it streamlines operations, fosters compliance, and enhances profitability, making it essential for companies of all sizes, especially those grappling with the complexities of food safety and inventory control.
When we dig deeper, understanding the intricacies of this software helps demystify its purpose and benefits. It’s not merely a tool for keeping track of the pantry but serves as a comprehensive solution to manage costs, assure quality, and maintain consistency in product offerings. This is crucial as failure to do so can lead to wastage, compliance failures, and ultimately, a dent in profits.
Definition and Purpose
Ingredient management software refers to specialized systems designed to oversee, track, and manage the various ingredients used within food production processes. Its purpose extends to various spheres, including inventory management, recipe formulation, and cost tracking. By doing so, it provides businesses with a clear roadmap of their ingredient utilization, which in turn facilitates better decision-making.
This software typically features modules that aid in managing stock levels, performing audits, and even integrating with larger enterprise systems to provide a holistic view of the business's operations. This integration is not just a buzzword; it represents a shift towards more data-driven decision-making processes within the industry.
Key Features
Ingredient management software encompasses several key features that contribute to its efficacy:
Inventory Tracking
Inventory tracking is arguably the heartbeat of ingredient management software. This feature enables users to keep a close watch on the availability of various ingredients. It allows businesses to minimize waste by ensuring that they only order what they need, when they need it.
One of the main characteristics of inventory tracking systems is real-time monitoring. This allows decision-makers to promptly respond to shortages or surpluses, effectively eliminating the guesswork that often leads to unnecessary expenses. With a unique aspect such as automated alerts, businesses can receive notifications when stock levels reach a certain threshold, ensuring they never run dry of essential ingredients. This can be particularly beneficial for businesses with fluctuating demand, where timing is everything.
Recipe Formulation
Recipe formulation is another crucial feature of ingredient management software, allowing users to create and modify recipes with precision. This capability enhances product consistency, which is critical in maintaining customer satisfaction. By providing tools to accurately measure ingredient ratios, the software ensures that variations in flavor or texture are minimized, leading to a more predictable outcome in product quality.
A significant characteristic of recipe formulation tools is their ability to integrate with inventory levels. This means that when a recipe is created, the software can automatically adjust the stock levels accordingly, streamlining the workflow. Additionally, this software can aid in nutritional analysis, thus supporting businesses in meeting dietary regulations which are increasingly important in today’s health-conscious market.
Cost Analysis
Cost analysis features within ingredient management software provide an extensive overview of how ingredient costs affect overall production expenses. This functionality allows users to not only track historical costs but also forecast future expenditures based on shifting supplier prices or changes in market demand.
One key characteristic is the ability to analyze cost by ingredient, recipe, or even by batch, giving businesses granular insights into their spending habits. A unique feature is its capacity to simulate cost impacts when altering a recipe, enabling companies to make informed decisions before they commit to any changes. The advantages here are clear—eliminating unnecessary expenses can lead to significantly improved profit margins. However, businesses must be cautious; overemphasis on cost may sometimes lead to quality compromises in ingredient selection, challenging the delicate balance between cost and quality.
"In today's fast-paced food industry, managing ingredients is not just about availability; it's a complex dance of costs, quality, and compliance that shapes a business's future."
In summary, ingredient management software serves as a critical tool for many food businesses. Its key features enable better management of inventory, recipe formulation, and cost analysis, all of which contribute to improved operational efficiency and better financial health.
The Importance of Ingredient Management
Ingredient management is more than just a method; it serves as a backbone for operational success within the food and beverage industry. When businesses embrace effective ingredient management practices, they unlock various advantages that resonate through every layer of their operations. Without these systems in place, inefficiencies creep in, compliance falters, and the bottom line can suffer.
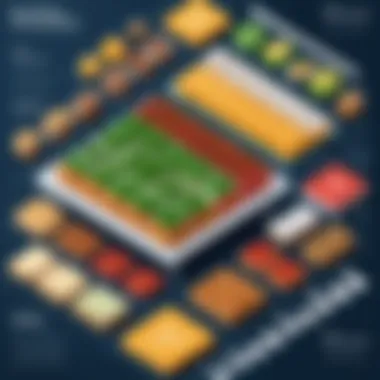
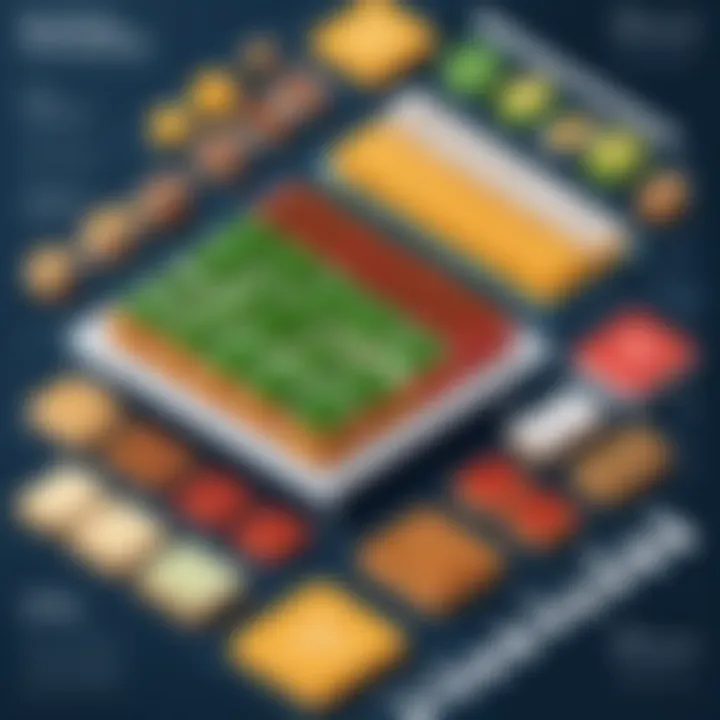
Operational Efficiency
One of the most glaring benefits of ingredient management is its ability to boost operational efficiency. Imagine having a well-oiled machine, where every component knows its role and tasks flow seamlessly. This level of operational efficiency simplifies inventory processes, allowing businesses to maintain the right ingredient levels and reduce waste.
When a restaurant utilizes software to monitor ingredient usage, they can swiftly adjust orders based on real-time data. This not only cuts down on surplus inventory but also helps in planning menus effectively according to what's available.
Moreover, a streamlined approach ensures that employees spend less time on manual tracking, focusing instead on enhancing customer satisfaction and other core activities.
Regulatory Compliance
In the world of food production, staying compliant with regulations is non-negotiable. Ingredient management software plays a pivotal role in ensuring adherence to various standards that the industry must meet.
Food Safety Standards
Food safety standards may sound dry, but they are indeed critical. These guidelines establish the necessary processes to guarantee that food products are safe for consumption. From proper ingredient handling to traceability, complying with these standards is vital for maintaining customer trust and avoiding legal troubles.
A standout characteristic of these standards is that they foster transparency throughout the supply chain. For instance, implemented tracking features in management software allow businesses to trace ingredients back to their source, an invaluable aspect during audits. In a landscape where food recalls can lead to substantial financial ramifications, ensuring compliance with safety standards is a wise investment for any food business.
Labeling Requirements
Equally important are the labeling requirements, which govern how products are presented to consumers. Clear and accurate labeling is not just a legal obligation but also a key factor in customer confidence. Implementing a labeling system that aligns with regulations can elevate a brand’s reputation.
What sets these labeling requirements apart is their focus on transparency. For example, ingredient management solutions can help automate bulk label production, ensuring that every package accurately reflects the contents. This not only minimizes errors but highlights a company's commitment to honest communication with its customer base.
"Effective ingredient management is not merely a strategy; it's the foundation upon which food quality and safety are built."
Benefits of Implementing Ingredient Management Software
In today’s fast-paced food and beverage industry, the stakes are higher than ever. Companies are not just contending with competition; they are also facing challenges related to cost management, compliance with regulations, and operational efficiency. Implementing ingredient management software can address these challenges head-on, fostering a more streamlined operation that ultimately enhances profitability and sustainability. Let us explore a few fundamental benefits that organizations stand to gain from this technology.
Cost Reduction
Efficient management of ingredients can be the difference between profit and loss. Ingredient management software significantly aids in reducing costs in several ways. First, by providing real-time inventory data, companies can avoid over-ordering or under-ordering. This fine-tuning of stock levels prevents excess spending on ingredients that might go unused. Furthermore, a thorough understanding of ingredient usage trends leads to better purchasing decisions.
For instance, think about a restaurant that often finds itself tossing expired ingredients. Not only does this waste money, but it also affects the overall inventory. With the right software, managers can track expiry dates and set alerts, thus minimizing waste. This kind of foresight is essential for maintaining a lean operational budget and improving the bottom line.
Enhanced Data Accuracy
In an age where data drives decisions, accuracy cannot be overstated. When ingredient data is entered and tracked manually, the potential for human error is immensely high. Mistakes in recipe formulation or inventory counts can lead to disastrous outcomes, including financial losses and customer dissatisfaction.
Ingredient management software mitigates these risks by automating data entry and management processes. The software ensures that records are kept consistently, reducing discrepancies and confusion. This accuracy extends not only to inventory counts but also to nutritional information, allergen data, and cost calculations.
Accurate data can empower businesses to make informed decisions regarding pricing, marketing, and product development.
Time Management
Time is a resource that often feels in short supply, particularly in busy commercial kitchens or large-scale production facilities. Each minute spent wrestling with paperwork or cumbersome spreadsheets is time that could be spent on food quality or service improvement. Ingredient management software simplifies repetitive tasks, allowing staff to focus on high-value work.
For example, this software can automate the creation of purchase orders, track supplier delivery schedules, and even generate reports with just a few clicks.
Automating these mundane processes means less time scrambling to keep things organized and more time dedicated to innovation and customer satisfaction. The overall improvement in efficiency can lead to shorter lead times, better service to customers, and enhanced employee satisfaction as staff can concentrate on more strategic tasks.
Features to Look for in Ingredient Management Software
Ingredient management software is essential for any food and beverage business aiming to refine its operations. Choosing the right software involves understanding the specific features that can streamline ingredient handling, enhance productivity, and ensure compliance. Given the complexity of the food industry, software must not merely function but also cater to unique needs of each enterprise. Here, we delve into two critical components: a user-friendly interface and the ability to integrate seamlessly with existing systems.
User-Friendly Interface
A user-friendly interface cannot be overstated in its importance. When it comes to ingredient management, a complicated interface can hinder rather than help. Users, whether they are managers or kitchen staff, need to access important information quickly. Imagine a scenario where the kitchen is bustling during a dinner service. A chef needs to adjust a recipe on the fly, but if the software is difficult to navigate, valuable time is lost.
Features like dashboards that provide critical data at a glance and intuitive navigation make all the difference. It leads to a smooth operation where no one is left scratching their heads. Therefore, an easy-to-use interface contributes not just to employee satisfaction but also to the overall efficiency of the business. Having visual charts, well-organized menus, and simple data input methods can significantly enhance productivity.
Integration with Other Systems
Integrating ingredient management software with other existing systems is a game changer. It allows for smoother operations within the organization and minimizes redundancy. When different parts of a business communicate effectively, a holistic view of operations emerges. There are two categories of systems worth discussing here: ERP systems and supply chain management tools.
ERP Systems
Enterprise resource planning (ERP) systems are crucial in today’s digital age. They consolidate various functions – from finance to human resources – into a unified system. Using an ERP system in combination with ingredient management software improves overall coherence across departments. For instance, incorporating real-time data on ingredient inventory can immediately impact procurement decisions by the finance team, ensuring that budgets are adhered to without depleting stock.
A key characteristic of ERP systems is their scalability. This means they can grow with the business, adapting to increased complexity over time. Such systems can be tailored to the specific requirements of each organization, which makes them a popular choice. One unique feature of many ERPs is their comprehensive reporting capabilities, presenting data visually to enhance interpretation and decision-making.
Though valuable, there are some challenges to consider. Integrating ERP with ingredient management software might require significant initial investment and training. Yet, the benefits usually outweigh these potential drawbacks.
Supply Chain Management Tools
On the other hand, supply chain management tools focus on optimizing the flow of goods and services. These tools ensure that ingredient procurement, storage, and distribution remain efficient. When integrated with ingredient management software, they contribute to precise tracking of ingredient origins, ensuring compliance with safety standards without much hassle.
A notable advantage of these tools is their capability to forecast demand based on historical data. This helps businesses avoid both shortages and overstocking, which can be detrimental in the food industry. A unique aspect is their ability to provide real-time updates about suppliers, helping decision-makers react swiftly to any supply chain disruptions.
However, depending on the sophistication of the tools chosen, there may be complexities in implementation. Smaller businesses, in particular, may find it overwhelming at first, but the long-term pay-off is often well worth it.
Sourcing Ingredients Effectively
Sourcing ingredients is a fundamental cornerstone of ingredient management, especially within the food and beverage sector. This process does not merely involve procuring raw materials; it also encompasses the strategic oversight of quality, price, and reliability of these resources. Effective sourcing can make a substantial difference in a company’s operational efficiency, cost management, and overall product quality. This section will unravel the essential aspects of sourcing ingredients effectively, highlighting the significance of valuable supplier relationships and rigorous quality assurance processes.
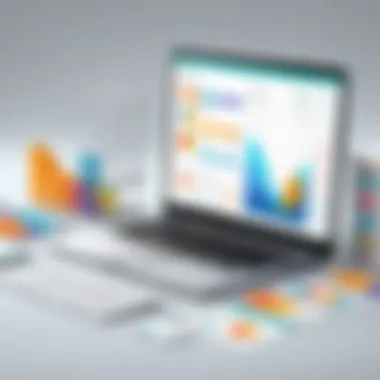
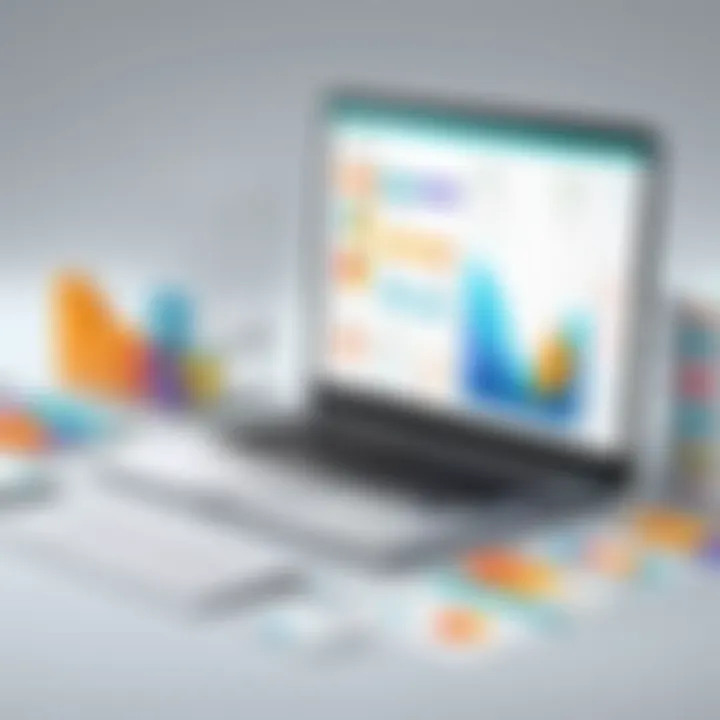
Supplier Relationship Management
An effective supplier relationship management strategy acts as a bridge between businesses and their ingredient suppliers. Strong relationships can facilitate more than just procurement; they can foster collaboration and innovation. By nurturing partnerships, companies often gain access to exclusive pricing, higher-quality ingredients, and better service.
- Long-term Partnerships: Companies that invest time in building lasting relationships with suppliers typically enjoy more favorable contract terms. This can translate into reduced costs and reliable deliveries, a significant advantage in a fluctuating market.
- Effective Communication: Open dialogue paves the way for transparency. Establishing clear channels for communication helps in tackling any issues that arise promptly, whether there are sudden price increases or quality discrepancies. This responsiveness can shield a business from supply shocks.
- Performance Evaluation: Regularly assessing supplier performance ensures that they meet your standards. Utilizing metrics like delivery times, quality scores, and responsiveness can provide insights into how well a supplier is doing, thus allowing businesses to make data-driven decisions.
Fostering quality relationships is about more than simply ensuring a steady supply of ingredients. It’s about creating a network of partners who are invested in your success, leading to better product offerings and reputational growth.
Quality Assurance Processes
To maintain excellence in ingredient sourcing, implementing robust quality assurance processes is non-negotiable. This ensures that every ingredient meets the safety, sustainability, and quality standards required by the industry. Quality assurance goes hand in hand with compliance, serving as a safeguard against potential hazards in food safety.
- Supplier Audits: Conducting audits helps verify that suppliers adhere to specified quality standards. This process not only highlights any existing lapses in quality but also encourages suppliers to uphold high standards in order to maintain their contracts.
- Testing and Documentation: Ingredient testing—a necessary protocol—should not be overlooked. Regular testing for contamination, spoilage, and nutritional content reinforces quality control. Documentation helps to keep a clear record of all tests, making it easier to ensure compliance with regulations.
- Traceability Systems: Implementing traceability systems allows companies to track ingredients from source to plate, which is particularly valuable if any quality issues arise. Consumers today are increasingly concerned about the origins of their food, and traceability meets that demand while bolstering confidence in the product.
Having a rigorous quality assurance process doesn’t just protect a company; it builds confidence among consumers. When businesses prioritize quality, they establish a reputation that can differentiate them in a crowded market.
"A successful sourcing strategy is not just about finding the cheapest ingredients; it’s about sourcing the right ingredients in the right way."
In sum, effective sourcing of ingredients is more than a logistical challenge; it is a strategic advantage that impacts everything from cost management to product quality. By focusing on supplier relationship management and maintaining rigorous quality assurance standards, businesses can enhance their ingredient sourcing capabilities, setting a firm foundation for operational success.
Challenges in Ingredient Management
Ingredient management is not just about keeping track of what’s on the shelf; it’s an intricate dance involving several moving parts. Businesses in the food and beverage industry face numerous challenges that can stifle their operations. Navigating these challenges is critical to ensuring success in this competitive landscape. Let's delve into two major hurdles: supply chain disruptions and the complexities of maintaining compliance.
Supply Chain Disruptions
Supply chain disruptions can rear their ugly heads when one least expects it. It could be anything, from natural disasters to sudden market shifts or even supplier issues. Such interruptions can throw a wrench in the works of ingredient management, leading to a cascading effect on production schedules and ultimately on customer satisfaction.
Here are some common causes of supply chain disruptions:
- Geopolitical Factors: Political instability and trade restrictions can mess with sourcing ingredients from specific regions.
- Natural Calamities: Floods, hurricanes, or fires can affect both suppliers and the transportation of goods.
- Market Fluctuations: Prices of key ingredients may fluctuate wildly due to demand spikes or supply shortages.
To mitigate these disruptions, it’s prudent for businesses to build a resilient supply chain. This might mean diversifying suppliers or developing strong relationships with multiple partners. That way, if one supplier runs into trouble, another can step in without skipping a beat. Utilizing ingredient management software can greatly enhance this process by providing real-time insights into inventory levels and supplier performance, ensuring companies stay one step ahead.
Maintaining Compliance
Compliance is one of the top concerns that businesses face in ingredient management. With regulations constantly evolving, staying abreast of food safety standards and labeling requirements is no small feat.
Here's a look at some critical aspects of ensuring compliance:
- Food Safety Standards: Regulations such as Hazard Analysis Critical Control Point (HACCP) or other local food safety protocols must be adhered to at all stages of food production. The aim is to identify and rectify potential hazards before products reach consumers.
- Labeling Requirements: Accurate labeling is crucial not just for regulatory compliance but also for consumer trust. Inaccurate or misleading labels can lead to significant legal repercussions and damage a brand's reputation.
Navigating compliance can be particularly tough for smaller enterprises, as they often lack the resources to keep pace with regulatory changes. However, implementing ingredient management software provides tools to automate compliance monitoring and can significantly reduce human error, ensuring adherence to required standards.
"In the food industry, compliance is not just an obligation; it's a commitment to quality and safety that resonates with informed consumers."
In summary, the challenges posed by supply chain disruptions and maintaining compliance require a proactive and strategic approach. By understanding these hurdles, businesses can develop robust strategies that leverage technology and provide a clear pathway through the complexities of ingredient management.
Future Trends in Ingredient Management Software
The landscape of ingredient management software is evolving, shaped by technological advancements and changing market needs. As industries become more competitive, the integration of innovative tools is no longer just a luxury but often a necessary strategy for success. Understanding future trends in this realm equips businesses with the insights needed to keep pace with competitors and meet consumer demands.
Artificial Intelligence and Automation
Artificial Intelligence (AI) is increasingly finding its way into ingredient management software, offering powerful capabilities to streamline processes. AI technologies can analyze vast amounts of data, providing insights that manual processes simply can't match. For example, AI can forecast demand for certain ingredients based on historical sales data, seasonality, and market trends. This allows businesses to proactively manage their inventories, reducing waste and ensuring that popular items are always in stock.
Automation, on the other hand, improves operational efficiency by minimizing human error and accelerating repetitive tasks. An example would be automated inventory updates when new products are received or used. Companies like Oracle and SAP have incorporated these technologies in their solutions, showcasing trends that highlight the potency of integration with day-to-day operations.
"In the world of ingredient management, the combination of AI and automation transforms data into decisions, turning chaos into order."
Sustainability Practices
As consumers become more environmentally conscious, sustainability in ingredient sourcing is gaining significant traction. Ingredient management software is being tailored to support environmentally friendly practices by providing tools to track the sustainability of ingredients throughout the supply chain. For instance, businesses can now assess suppliers on criteria such as carbon footprint or ethical farming practices.
By adopting sustainable practices, companies not only comply with regulations but also bolster their brand image. Using software solutions that feature sustainability tracking allows organizations to demonstrate their commitment to responsible sourcing. Notably, organizations like EcoVadis provide benchmarking services that assess corporate sustainability performance, which can be integrated into ingredient management solutions.
- Benefits of integrating sustainability practices within Ingredient Management Software:
- Improved supplier relationships through transparency.
- Real-time tracking and reporting of sustainability metrics, ensuring accountability.
- Enhanced customer loyalty among eco-conscious consumers.
As the shift towards sustainability continues, the software landscape will likely only deepen its integration of features aimed at supporting environmentally friendly practices. Companies that embrace these trends not only safeguard against potential regulatory pitfalls but also position themselves as leaders in their respective fields.
Implementation Strategies for Businesses
When adopting ingredient management software, having a solid implementation strategy is key. This isn’t just a suggestion; it's a necessity for maximizing the benefits of the software while mitigating risks. A well-structured approach allows businesses to align their operations seamlessly with the new system, ultimately leading to enhanced efficiency and streamlined processes.
Training Employees
Training employees is a fundamental component of rolling out any new software. The personnel who will interact with the ingredient management system need to understand its functionalities inside and out. This goes beyond a mere hands-on demo. It involves understanding how the software integrates into existing workflows, how to troubleshoot common issues, and recognizing the impact it has on daily tasks.
Making a comprehensive training program is crucial. This can include:
- Workshops and Seminars: Bringing in experts from the software provider to give in-depth sessions can be immensely beneficial.
- User Guides and Manuals: Providing easy-to-understand materials can serve as a reference during the learning process.
- On-the-Job Training: This allows employees to learn in real-time, just by using the software while a seasoned colleague can help.
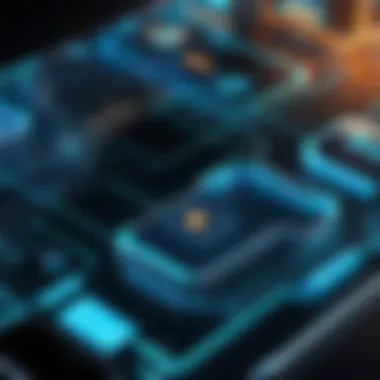
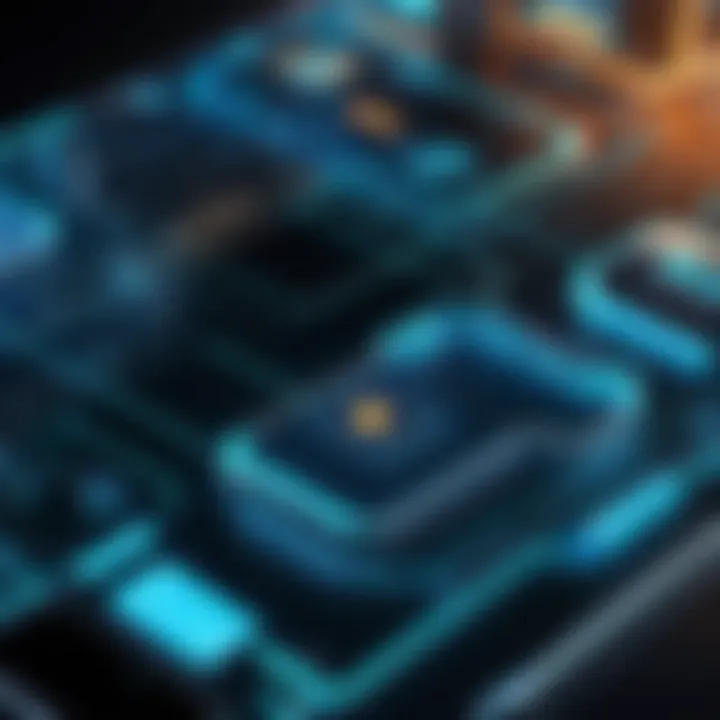
Consider that different teams may require different types of training. The sales team might need a particular focus on inventory tracking features, while culinary staff may find recipe formulation more relevant. Personalizing training helps ensure everyone is on the same page and can use the software to its full capacity.
Phased Rollout Approach
A phased rollout approach offers a systematic way to implement your new ingredient management software. Instead of flipping the switch all at once, you can gradually introduce the system, which helps identify hiccups and fix issues before they balloon into larger problems.
This method allows businesses to:
- Test and Refine: By launching the software in stages, teams can gather feedback and make necessary adjustments, enhancing user experience. It prevents overwhelming those who may be apprehensive about technological changes.
- Monitor Performance: With a controlled rollout, collecting data on system performance is easier, allowing decisions to be made based on actual usage rather than theory.
- Gradual Adaptation: Employees who may initially resist change can adjust at a comfortable pace, improving overall acceptance and utilization rates.
The phased approach could follow a pattern like this:
- Pilot Testing: Start by launching the software with a small group of users to gather insights and test functionalities.
- Departmental Rollout: Once the pilot is successful, begin implementation department by department, addressing concerns and sharing successes along the way.
- Company-Wide Adoption: Finally, after ironing out issues, roll the software out to the entire corporation.
"Taking the time to implement a strategy pays dividends in the long run. This isn’t just about adopting new software; it’s about fostering a culture of adaptability and continuous improvement."
By concentrating on both training and a phased rollout, businesses can enhance the efficacy of their ingredient management systems and ensure everyone is equipped for success.
Evaluating Different Software Providers
In the realm of ingredient management software, choosing the right provider can make or break operational efficiency. With various options on the market, it’s crucial for businesses to carefully evaluate potential software providers. This involves looking beyond the flashy marketing brochures and really digging into aspects like functionality, customer support, and scalability. A well-thought-out selection process not only saves time in the long run but also ensures that the software aligns effectively with the specific needs of the organization.
Market Research Considerations
When it comes to market research, a comprehensive approach is key. Decision-makers should survey the landscape of available software, considering factors such as:
- Functionality: What specific features does the software offer? Ensure that it covers essential aspects like inventory tracking, recipe formulation, and compliance management.
- Industry Reputation: Are there case studies or success stories from similar businesses? This can provide insight into how effective the software has been in real-world applications.
- Technology Trends: Be aware of emerging trends and technological advancements. Look for providers that are adapting to changes like automation and AI integration.
- Pricing Structures: Evaluate different pricing models. Ensure that the costs align with your budget and provide value for the features offered.
Finding a software provider is akin to fishing in a vast ocean; one must know where to cast the line to catch the prize desired. Ignoring this step can lead to sinking time and resources into a system that does not deliver.
Reading User Reviews
In addition to formal market research, diving into user reviews can be incredibly illuminating. The insights provided by existing users can paint a clearer picture of what to expect. Key elements to consider when reading user reviews include:
- Real-Life Experiences: Look for reviews discussing how the software performed in day-to-day operations. Highlighted pain points and successes can guide expectations.
- Customer Support Feedback: Many reviews often touch on the quality of customer support. Is it responsive and helpful? Or do users often find themselves in a support desert?
- Adaptability to Change: Reviews might also mention how easily the software adapts to new regulations or market demands. Flexibility can be a deciding factor in the ever-evolving food and beverage industry.
- Longevity: Take note of comments regarding the longevity of the software's effectiveness. Has it remained relevant over time, or have users sought alternatives after a short while?
"In the age of information, the consumer's voice can often steer the direction of a business."
For high-IQ decision-makers and IT professionals, these insights provide an unmatched glimpse into the practical use of software. By synthesizing both structured market research and anecdotal evidence from existing users, businesses can make informed choices that are tailored to their specific operational needs.
Case Studies: Success Stories
When it comes to ingredient management software, real-world examples paint a clearer picture of its impact than any theoretical discussion could. The significance of case studies lies in their ability to illuminate the practical benefits and challenges faced by different types of businesses—small enterprises and large corporations alike—when adopting these software solutions. They provide invaluable insights, showcasing how specific tools have been employed to tackle industry-specific challenges, streamline processes, and achieve measurable results. Understanding these success stories also assists potential users in visualizing how the software could fit into their operational framework, informing their decisions.
Small Enterprises
In the realm of small businesses, agility and cost-effectiveness are paramount. A poignant example is a local bakery named Sweet Delights. Prior to implementing ingredient management software, they faced significant issues with tracking inventory. Ingredients would often spoil, leading to unnecessary waste and financial loss. After adopting a software solution tailored for their specific needs, they were able to monitor inventory levels in real-time. This helped them to make more informed purchasing decisions, ensuring they only ordered what they needed, reducing waste by about 30%.
The software also streamlined their recipe formulation process. The bakery was able to create standardized recipes that were easily accessible to all employees, improving consistency across their product line.
Benefits of the software did not stop there:
- Enhanced Cost Management: By tracking ingredient costs closely, Sweet Delights was able to adjust their pricing strategy, leading to a 15% increase in profit margins within six months.
- Improved Compliance: As local food safety regulations grew stricter, the software facilitated easier tracking of expiration dates and supplier certifications, ensuring they complied with all regulatory requirements.
In this case, it’s clear that ingredient management software can empower small enterprises to not only survive but thrive in competitive marketplaces by bringing efficiency and precision to their operations.
Large Corporations
On the other end of the spectrum, large corporations face a different set of challenges. Consider MajorFoods Inc., a global food manufacturer with a complex supply chain. Their ingredient management woes stemmed primarily from the vast scale at which they operated. After conducting a thorough market analysis, they chose to implement a robust ingredient management software system that integrated with their existing ERP systems.
With this solution, MajorFoods was able to:
- Optimize Supply Chain Management: Real-time visibility across their supply chain enabled them to identify bottlenecks quickly and reduce delays, which is crucial for a company dealing with perishable goods.
- Enhanced Data Analytics: The software provided powerful analytics tools, offering insights that led to a 20% reduction in overall ingredient costs by leveraging bulk purchases and optimizing supplier contracts.
- Streamlined Communication: By integrating ingredient management with their suppliers’ systems, MajorFoods improved communication, ensuring that all stakeholders were on the same page regarding supply availability and shipment timelines.
This integration not only alleviated many logistical headaches but also solidified MajorFoods' reputation as an industry leader in consistent quality and reliability.
In both cases—whether a small bakery or a large food manufacturer—ingredient management software serves as a transformative tool, enabling businesses to navigate their unique challenges effectively. Their success stories provide a roadmap for others seeking to enhance their operations, demonstrating that with the right technology, both small and large enterprises can achieve operational excellence.
Closure
The conclusion of this article serves as a pivotal moment, encapsulating the crux of ingredient management software's significance in the food and beverage sector. With the fast-paced nature of this industry, efficient operations are non-negotiable. The insights garnered throughout our exploration reveal that product quality, compliance with regulations, and cost efficiency hinge on robust ingredient management solutions. It’s more than just software; it’s a holistic approach that can transform kitchen chaos into streamlined operations.
Recap of Key Insights
In our discussion, several key points have emerged that highlight the transformative power of ingredient management software:
- Operational Efficiency: Companies utilizing these tools can expect significant enhancements in how they handle inventory, manage recipes, and process data, ensuring that their systems run like a well-oiled machine.
- Regulatory Compliance: Staying ahead of food safety standards and labeling requirements can seem daunting. However, with the right software, organizations can automatically track compliance measures, thereby reducing the burden on staff.
- Cost Management: Implementing effective ingredient management strategies yields not just savings but also allows businesses to allocate resources smarter.
Indeed, these points underscore the necessity of adopting such software to remain competitive and compliant.
Final Thoughts on Future Developments
Looking ahead, it’s clear that ingredient management software will not just evolve; it will revolutionize how businesses approach their operations. Incorporating artificial intelligence and automating mundane processes are just the beginning of this innovative journey. Companies adopting sustainability practices within these frameworks will likely lead the charge towards a more environmentally conscious industry.
As technology advances, the expectation is that these systems will become increasingly intuitive, harnessing vast data pools to provide deeper insights into ingredient sourcing and quality maintenance.
Ultimately, decision-makers, IT professionals, and entrepreneurs in the field need to keep their fingers on the pulse of these developments. The future may just favor those who can adapt the quickest and think outside traditional methodologies.
"Staying ahead in today's landscape is not just about keeping up; it's about anticipating tomorrow's needs and acting on them today."
In summary, the trend towards more sophisticated ingredient management software represents an exciting opportunity, with benefits that expand far beyond mere compliance and inventory tracking. The real potential lies in the ability to make informed decisions that proactively shape the future of the food and beverage industry.