Manufacturing Production Systems: An In-depth Analysis
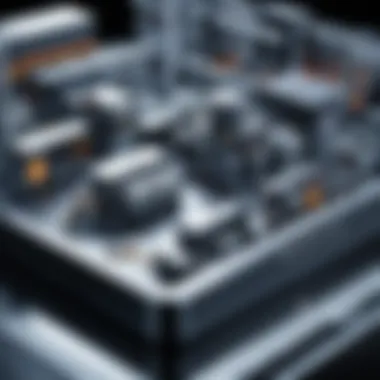
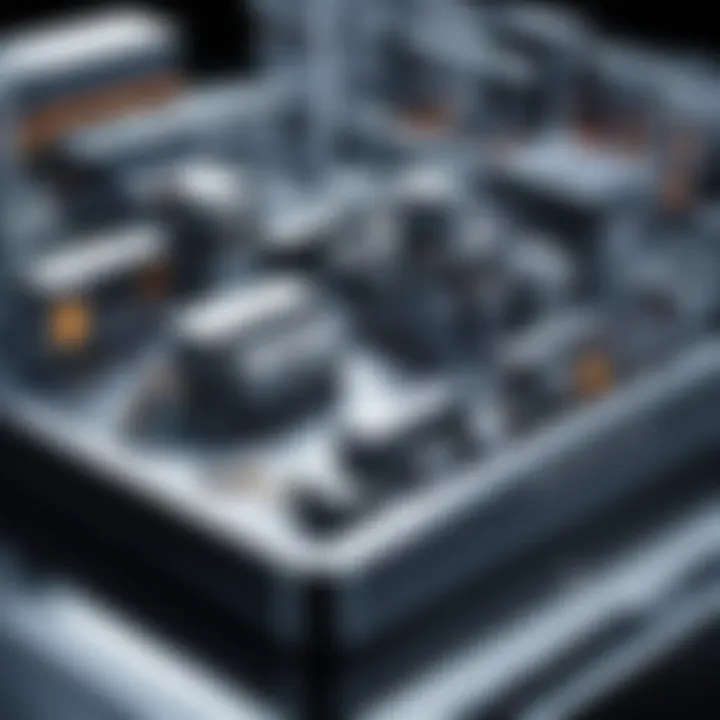
Intro
Manufacturing production systems encompass an array of components, methodologies, and technological advancements that collectively drive efficiency and productivity in modern industries. Understanding these systems is critical for decision-makers, IT professionals, and entrepreneurs who aim to optimize operations. This article will dissect essential aspects of manufacturing production systems and explore the evolving landscape they inhabit.
Software Category Overview
Definition and Importance
Manufacturing production systems refer to integrated frameworks that comprise various software tools used to manage and optimize production processes. These systems play a pivotal role by ensuring smooth operations, minimizing waste, and enhancing resource utilization. As industries face increasing pressure to perform efficiently, understanding and implementing effective manufacturing systems becomes vital. The integration of advanced software solutions allows companies to adapt to market demands while maintaining operational excellence.
Key Characteristics
An effective manufacturing production system is characterized by several key traits:
- Integration: The ability to connect various departments and processes within the production environment.
- Real-time Data: Offering insights into production efficiency, downtime, and resource allocation to facilitate informed decision-making.
- Flexibility: Flexibility allows systems to adapt to changing market needs or production requirements quickly.
- Automation: Incorporating robotics and automation technologies to enhance production capacity and reduce human error.
Comparative Analysis of Top Software Options
Feature Comparison
When evaluating different software options in manufacturing production systems, it is crucial to assess their core features. Here is a brief overview of commonly recognized software:
- SAP S/4HANA
- Oracle NetSuite
- Infor CloudSuite
- Integrated ERP system with robust analytics.
- Supports supply chain management.
- Cloud-based ERP with customizable dashboards.
- Comprehensive financial management tools.
- Industry-specific solutions tailored for various sectors.
- Advanced planning and scheduling capabilities.
Each software has distinctive strengths, enabling organizations to match a solution with their unique operational needs.
Pricing Models
The pricing for these systems can vary significantly, depending on the features, scale, and deployment methods:
- Subscription-based models: Typically monthly or annually, often favored for software like Oracle NetSuite.
- Perpetual licenses: A one-time fee for perpetual use which may apply to solutions like SAP S/4HANA.
- Tiered pricing: Some vendors offer tiered pricing structures to accommodate varying levels of service and features.
"Selecting the right manufacturing production software requires thorough analysis of feature sets and cost structures."
Each pricing model has its advantages. It is important to consider the total cost of ownership and potential return on investment when making a choice.
Finale
This article sets the stage for a detailed exploration of manufacturing production systems, painting a comprehensive picture of their critical components and methodologies. By understanding the nature and functionality of these systems, industry leaders can make more informed decisions that lead to greater efficiency and productivity.
Intro to Manufacturing Production Systems
Manufacturing production systems are the backbone of modern industrial operations. Their design and functionality significantly impact productivity, efficiency, and the overall success of manufacturing entities. Understanding the core concepts and mechanics of these systems is essential for decision-makers, IT professionals, and entrepreneurs looking to optimize their production processes and tackle industry challenges.
Definition and Purpose
Manufacturing production systems can be defined as organized frameworks designed to transform inputs into finished products efficiently and effectively. These systems integrate various components, including machinery, labor, and processes, to create a seamless workflow. Their primary purpose is to increase productivity while minimizing waste through structured operations. The ideal production system not only delivers quality products but also responds adeptly to the dynamic needs of the market.
As industries evolve, so do the objectives of manufacturing systems. They now focus on not just meeting demand but also on sustainability and adaptability. Companies aim for systems that can quickly adjust to changing customer preferences and technological advancements. A clear definition and understanding of the purpose of these systems are therefore fundamental for professionals aiming to implement effective strategies within their organizations.
Evolution of Production Systems
The evolution of manufacturing production systems reflects broader industrial transitions throughout history. Initially, production systems were simple and labor-intensive, relying heavily on manual labor. However, rapid technological advancements and globalization have ushered in more complex and automated systems.
The introduction of assembly line techniques by Henry Ford transformed production by enabling mass manufacturing. This innovation allowed for efficient production of standardized goods. Over the decades, additional methodologies emerged. For instance, the Toyota Production System introduced concepts like lean manufacturing, which focuses on eliminating waste while enhancing flow.
More recently, the rise of Industry 4.0 has integrated digital technologies into manufacturing. This new industrial revolution emphasizes automation, data exchange, and advanced analytics, fundamentally altering the nature of production systems.
"Modern manufacturing production systems are characterized by adaptability, integrating advanced technology to meet rapid market changes."
Understanding the evolution of these systems provides valuable insights into current trends and future developments. It highlights the necessity for companies to remain responsive to ongoing changes in technology and market demand.
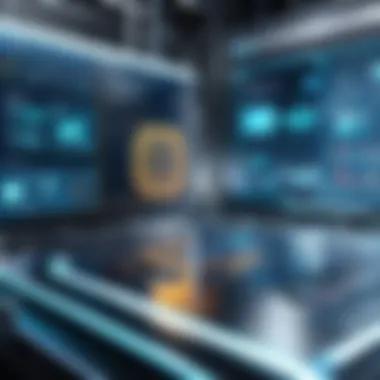
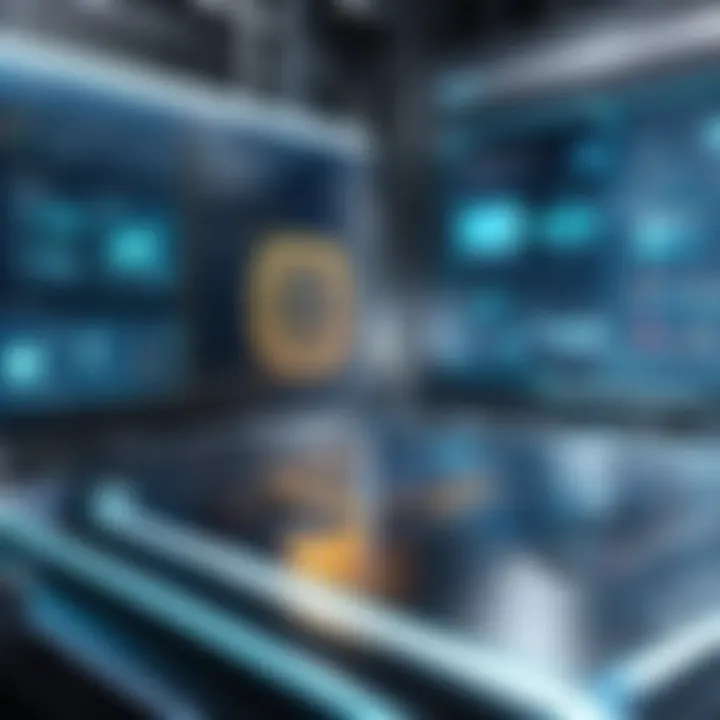
Key Components of Manufacturing Production Systems
Understanding the key components of manufacturing production systems is essential for optimizing efficiency and effectiveness in modern industries. These components play a vital role in determining the overall productivity and quality of output in a manufacturing environment. A comprehensive framework helps to facilitate smooth operations, allowing organizations to respond dynamically to market demands and improve competitiveness. The integration of various elements is necessary for creating a cohesive and functional production system.
Facilities and Layouts
The layout of a manufacturing facility significantly influences workflow and productivity. A well-designed facility maximizes space utilization and ensures that equipment and workstations are positioned to minimize waste and delay. Factors such as product type, production volume, and logistical considerations dictate facility layouts. Common layouts include
- Process Layout: Suitable for job-shop environments where products are customized.
- Product Layout: Efficient for high-volume, repetitive tasks, aligning equipment in a sequence of operations.
- Fixed-Position Layout: Best for large products like ships or airplanes where the product remains stationary.
Proper facility layout not only streamlines operations but also enhances safety and minimizes bottlenecks in the production process.
Machinery and Equipment
Machinery and equipment are the backbone of any manufacturing system. The choice of machinery affects production capabilities, cost efficiency, and quality control. Modern manufacturing often employs advanced technologies such as Computer Numerical Control (CNC) machines, additive manufacturing, and automated guided vehicles (AGVs). These technologies enable more precise manufacturing, faster turnaround times, and the flexibility to adapt to changing production needs. It's crucial to regularly assess machinery for maintenance needs to prevent breakdowns that can lead to production delays.
Investment in cutting-edge machinery typically results in a greater return on investment due to enhanced productivity and quality. However, the initial costs can be significant, so balancing cost with long-term benefits is necessary.
Labor and Workforce Management
A skilled workforce is an integral component of production systems. Effective labor management involves recruiting, training, and retaining employees with the necessary skills. The evolving nature of manufacturing often requires ongoing training programs to upskill workers in new technologies and methodologies.
Engaging employees through proper management practices fosters a sense of ownership and accountability, which can improve output quality. It is also vital to establish clear communication channels among teams to facilitate collaborative efforts across different areas of production.
In summary, mastering these key components allows organizations to build robust manufacturing production systems that can adapt to industry changes while maintaining high levels of efficiency and productivity.
Methodologies in Manufacturing Production
The methodologies employed in manufacturing production play a critical role in enhancing efficiencies and reducing waste in modern industries. Understanding these methodologies helps decision-makers implement effective systems that align with their operational goals. In a market where responsiveness and customization are vital, it is important to recognize the foundational principles that govern production methodologies.
Lean Manufacturing Principles
Lean manufacturing is a methodology focused on minimizing waste while maximizing productivity. This approach encourages organizations to streamline processes, reducing costs and improving efficiency. Some of the key principles of lean manufacturing include:
- Value Stream Mapping: Identifying value-added and non-value-added activities in the production process.
- Continuous Improvement: Fostering a culture of ongoing enhancement, encouraging teams to improve processes regularly.
- Pull System: Producing items based on actual demand rather than forecasts, which helps in maintaining inventory at optimal levels.
The benefits of lean manufacturing are numerous. Implementing this approach can lead to increased employee engagement as staff contribute to process improvements. Additionally, companies often see significant reductions in production lead times, contributing to better overall customer satisfaction.
"Lean manufacturing emphasizes efficiency, which begins by understanding and eliminating waste in all its forms."
Agile Production Techniques
Agile production techniques prioritize flexibility and adaptability in manufacturing processes. With market demands constantly changing, agile methodologies allow firms to respond quickly to those shifts. Key features of agile production include:
- Cross-functional Teams: Teams are made of members with diverse skill sets. This diversity enhances problem-solving capabilities and speed.
- Rapid Prototyping: Instead of extensive pre-production planning, agile manufacturing encourages the swift testing and iteration of new products.
- Customer Feedback Loops: Engaging consumers for feedback during production helps manufacturers adjust products according to market needs.
The importance of agile practices cannot be overstated. They allow for quicker innovation cycles, which can substantially shorten time-to-market for products. This means that businesses can seize opportunities faster than competitors who may be locked into more traditional methodologies.
Just-in-Time (JIT) Practices
Just-in-Time (JIT) practices optimize inventory management by ensuring that materials are available only as they are needed in the production process. JIT reduces waste and lowers inventory costs. Some principles of JIT practices include:
- Demand-driven Production: Manufacturing is based on actual market demand rather than projected needs.
- Supplier Relationships: Strong partnerships with suppliers enable timely delivery of materials.
- Inventory Minimalism: Reducing excess inventory prevents capital from being tied up in stock, allowing for better cash flow management.
The implications of JIT are significant. It encourages synchronization between production and demand while also enhancing quality control. Furthermore, companies adopting JIT often experience fewer disruptions, leading to smoother production schedules.
Technological Impact on Production Systems
The evolution of manufacturing production systems cannot be discussed without acknowledging the profound influence of technology. Innovation in this field has brought forth a multitude of changes, making processes more efficient and responsive to market needs. An integrated approach to technology not only enhances production capabilities but also directly impacts operational costs and product quality. The ability to adapt to technological advancements is crucial for any organization looking to remain competitive.
Automation and Robotics
Automation has transformed manufacturing by enabling tasks to be accomplished with minimal human intervention. Robotics plays a significant role, performing repetitive and hazardous tasks with precision and speed. This not only improves safety by reducing human exposure to dangerous environments but also increases throughput.
Benefits of automation include:
- Increased efficiency: Machines can run continuously without the need for breaks, leading to a significant increase in productivity.
- Consistent quality: Automation reduces the variability associated with human labor, ensuring that each product meets quality standards.
- Cost savings: While the initial investment in automation can be high, long-term savings on labor costs and waste reduction often make it economically viable.
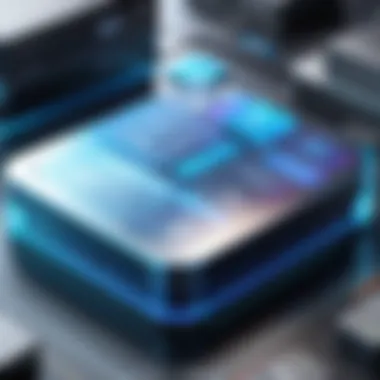
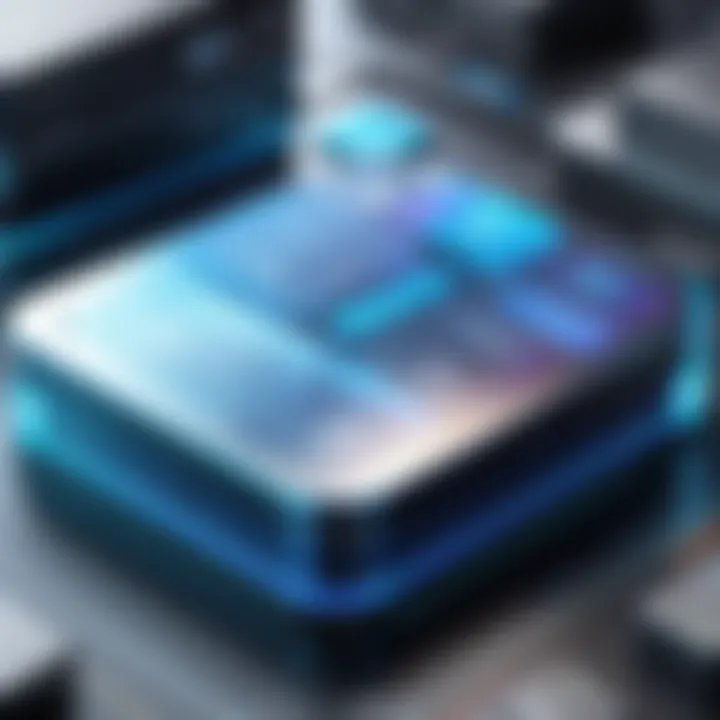
Organizations must consider certain factors before implementing automation. Evaluation of current processes, potential return on investment, and the training requirements for staff are essential.
Data Analytics and IoT Integration
The integration of data analytics and the Internet of Things (IoT) into manufacturing provides a robust framework for continuous improvement. IoT allows machines and devices to communicate and share data, enabling real-time monitoring of production processes. This connectivity leads to informed decision-making based on concrete data rather than intuitions.
Key aspects include:
- Predictive maintenance: Analyzing data patterns helps predict equipment failures before they occur, reducing downtime and maintenance costs.
- Enhanced visibility: Real-time data enhances visibility throughout the supply chain, allowing for quicker responses to changes in demand or supply issues.
- Optimized resource allocation: Proper analysis of production data allows manufacturers to allocate resources more effectively, minimizing waste and maximizing output.
Adopting these technologies requires an understanding of data management and a commitment to upskilling employees to interpret and act on data insights effectively.
Artificial Intelligence Applications
Artificial Intelligence (AI) is increasingly becoming a cornerstone of modern manufacturing. By leveraging AI tools and algorithms, companies can analyze vast amounts of data to drive insights and inform production strategies. Applications of AI in manufacturing systems can take many forms, including predictive analytics, quality control, and supply chain optimization.
The advantages of implementing AI include:
- Improved decision-making: AI systems can analyze data at speeds that far exceed human capabilities, leading to quicker and more accurate decisions.
- Personalization of products: AI enables the customization of products based on consumer preferences, enhancing customer satisfaction.
- Resource efficiency: AI can identify inefficiencies within a process and suggest corrections, leading to reduced waste and better utilization of materials.
Organizations looking to incorporate AI must ensure that they invest in the necessary infrastructure and talent to fully harness its capabilities.
The integration of advanced technologies within manufacturing production systems paves the way for enhanced efficiency, quality, and adaptability in a rapidly changing market.
Challenges Faced by Manufacturing Production Systems
Manufacturing production systems encounter a variety of challenges which significantly affect their efficiency and effectiveness. Understanding these challenges is crucial for decision-makers and industry professionals aiming to streamline operations and enhance productivity. Knowing these key issues can provide a foundation for strategic planning and problem-solving approaches in an ever-evolving market landscape.
Supply Chain Management Issues
Supply chain management is integral to manufacturing success. However, many organizations face disruptions due to several factors including geopolitical tensions, trade tariffs, and logistical constraints. These issues can lead to delays in material procurement and production schedules. Companies must adapt to the fluctuating availability of resources and raw materials.
- Issues such as transportation delays, inadequate inventory controls, or reliance on a single supplier can exacerbate the problem.
- Implementing robust supply chain strategies can significantly mitigate risks. Establishing diversified supplier networks and utilizing real-time tracking systems enhances visibility across the supply chain.
Collaboration with suppliers can also lead to better forecasting and timely delivery of materials, thus smoothing production processes.
Quality Control and Assurance
Quality control is critical for any manufacturing production system. Inadequate quality measures can result in defective products, leading to customer dissatisfaction and increased costs. Companies face challenges in maintaining consistent quality levels due to variations in raw material quality, human error in production processes, and outdated machinery.
To combat these issues, companies can employ various quality assurance methodologies:
- Implementing Six Sigma practices to reduce defects and variability.
- Regular training programs for the workforce to adapt to latest quality standards.
- Leveraging technology such as automated inspection systems to enhance precision in quality checks.
Even slight improvements in quality control processes can yield substantial benefits in product reliability and customer satisfaction.
Workforce Skill Gaps
One of the most pressing issues is the gap in skills among the workforce. As manufacturing processes become more automated and sophisticated, the need for higher-skilled labor has surged. However, many companies struggle to find employees with the requisite skills, which can lead to operational inefficiencies.
Factors contributing to this skill gap include:
- Rapid technological advancements that outpace current training programs.
- Aging workforce nearing retirement, leaving a shortage of experienced professionals.
- Lack of interest in manufacturing careers among younger generations.
To address these issues, organizations should consider:
- Investing in training and development programs tailored to upskill current employees.
- Establishing partnerships with educational institutions to create curricula that prepare students for careers in manufacturing.
Improving the skill levels within manufacturing can drive not only productivity but also innovation and competitiveness in this dynamic field.
Future Trends in Manufacturing Production Systems
Understanding future trends in manufacturing production systems is essential for industry professionals who aim to adapt to the changing landscape of technology and consumer needs. Attention to these trends not only helps manufacturers stay competitive but also enhances operational efficiency. Key aspects such as sustainability, customization, and cutting-edge technologies are reshaping the way production systems are structured and managed.
Sustainability and Green Manufacturing
Sustainability has become a crucial focus within the manufacturing sector. The need to minimize environmental impact is pressing. Manufacturers are increasingly adopting green practices to reduce waste, conserve energy, and utilize renewable materials. By implementing sustainable production systems, companies can improve their public image and reduce costs in the long term.
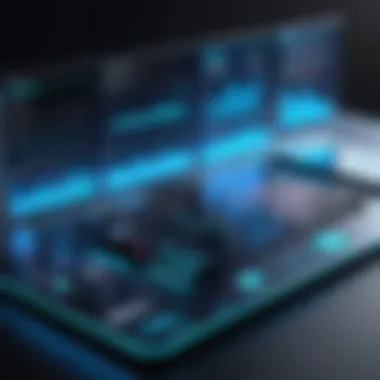
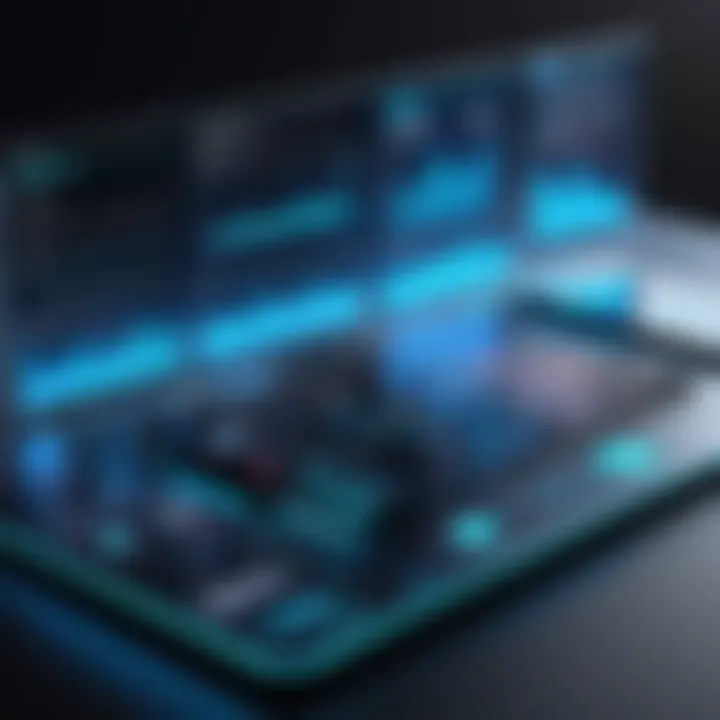
Common approaches in this area include:
- Energy-efficient machinery: Utilizing machines that consume less energy during operations can significantly decrease overall costs.
- Waste reduction practices: Techniques like lean manufacturing help in identifying and eliminating waste, leading to more eco-friendly processes.
- Lifecycle assessments: Companies are conducting assessments to evaluate environmental impacts at each production stage, facilitating better decision-making regarding materials and processes.
"Sustainable manufacturing is not just good for the planet; it's good for business."
Customization and Personalization of Products
Customization has become a competitive advantage in today’s market. Consumers increasingly seek products tailored to their preferences. Manufacturing production systems that implement customization efficiently can attract and retain customers effectively.
Adopting flexible manufacturing strategies is vital for achieving this. Key aspects include:
- Modular production designs: Systems that allow for quick changes in production lines can adapt to new product specifications easily, reducing time to market.
- Demand-driven production: Utilizing data analytics helps in predicting customer preferences, facilitating the production of personalized items.
- Mass customization techniques: Technologies such as 3D printing enable manufacturers to produce individualized products economically.
Digital Twins and Smart Factories
The implementation of digital twins and smart factories signifies a profound shift towards more intelligent manufacturing systems. Digital twins—virtual replicas of physical systems—allow manufacturers to simulate, predict, and optimize performance in a real-time environment. This technology offers several benefits:
- Enhanced data utilization: Real-time analysis of production data helps in identifying bottlenecks and inefficiencies.
- Predictive maintenance: Manufacturers can predict equipment failures before they occur, minimizing downtime.
- Improved collaboration: Smart factories utilize IoT integration for seamless communication between machinery, helping to boost overall productivity.
By embracing these future trends, manufacturing production systems can enhance innovation, efficiency, and sustainability, ensuring long-term success in an ever-evolving market.
Case Studies on Successful Production Systems
In the landscape of manufacturing production systems, case studies offer valuable insights. They illuminate how theories and methodologies translate into practice. By analyzing successful implementations, industry leaders can draw lessons that inform their own operational strategies. The benefits of such case studies are multifaceted, providing a roadmap for efficiency, innovation, and competitive advantage.
Automotive Industry Innovations
The automotive industry serves as a prime example of successful production systems. Companies like Toyota have pioneered the Lean Manufacturing methodology, significantly optimizing their production lines. This approach reduces waste and enhances value by focusing on what customers actually want.
For instance, Toyota's use of the Just-in-Time (JIT) system revolutionized inventory management. The system allows for parts to be delivered right before they are needed on the assembly line. This minimizes holding costs and reduces the risk of excess inventory.
Another notable innovation in the automotive sector is the implementation of automation technologies. Robotics in manufacturing helps increase both speed and precision, which is crucial in an industry where minor errors can lead to significant recalls or safety issues. The success of automotive manufacturing showcases the potential of integrating technology with innovative methodologies.
Electronics Manufacturing Advances
In electronics, companies like Apple and Samsung have introduces revolutionary manufacturing systems that emphasize flexibility and speed. These firms utilize advanced data analytics to forecast demand accurately, allowing them to adjust production schedules accordingly.
Samsung's use of modular production systems allows for rapid changes in their product lines. This adaptability enables them to respond quickly to market trends. By leveraging technology such as IoT (Internet of Things), they maintain streamlined operations and better resource management.
Moreover, the case of Flextronics illustrates how contract manufacturers can optimize operations for multiple clients simultaneously. Their success lies in their ability to scale production efficiently and enhance supply chain resilience through careful planning and strategic partnerships.
Consumer Goods Sector Transformations
The consumer goods sector has undergone significant transformations through innovative production systems as well. Procter & Gamble exemplifies this with its commitment to sustainable practices. By adopting eco-friendly materials and processes, the firm not only addresses regulatory requirements but also appeals to environmentally-conscious consumers.
Furthermore, the integration of customer feedback into production processes has led to the rise of personalized products. For example, Coca-Cola has utilized data analytics to create marketing strategies that tailor offerings to local consumer preferences. As a result, this responsiveness boosts sales and strengthens customer loyalty.
In summary, the case studies across various sectors prove that successful manufacturing production systems are not just theoretical constructs. They are the result of thoughtful implementation and continual adaptation. By studying these examples, decision-makers can apply valuable lessons to their operations, enhancing their overall efficiency and product quality.
Ending and Recommendations
The conclusion of this article focuses on Conclusion and Recommendations as critical elements for the understanding and application of manufacturing production systems. Recognizing the complexities involved in these systems underscores the necessity of strategic insights for their effective implementation and future sustainability. Efficient manufacturing production systems are essential for enhancing productivity and maintaining competitiveness in any industry. Shifts in technology, consumer demand, and operational challenges require constant adaptation and strategizing.
In a landscape characterized by rapid change, organizations need to assess their existing production systems regularly. Here are some critical considerations that should be made:
- Analyze Your Current Processes: This includes evaluating the effectiveness and efficiency of your current production methodologies. Identifying areas where improvements can be made is essential.
- Invest in Training: As technology progresses, so should the skill levels of the workforce. Providing ongoing training keeps staff informed about new technologies and methodologies.
- Embrace Technological Advances: Staying updated with innovations like automation, AI, and data analytics can significantly enhance productivity and simplify operations.
- Develop a Flexible Approach: Flexibility allows organizations to adapt to market changes quickly and can lead to more significant opportunities for customization and personalization of products.
"Investing in strategic insights and recommendations for manufacturing production systems equips organizations to tackle future challenges effectively."
Through ongoing analysis and adaptation, companies can not only survive but also thrive in this competitive arena. The ultimate goal is for decision-makers to leverage these recommendations to create more robust, agile, and efficient production systems.
Strategic Insights for Implementation
When implementing any changes to a manufacturing production system, several strategies can guide decision-makers in achieving their goals. Here are key insights:
- Implement Lean Principles: Streamlining processes to eliminate waste maximizes resource utilization while minimizing costs.
- Monitor Key Performance Indicators (KPIs): Setting measurable KPIs enables organizations to track progress and assess the effectiveness of newly implemented strategies.
- Utilize Customer Feedback: Listening to customer feedback can guide adjustments in production strategies, leading to better alignment with consumer demands.
- Encourage a Culture of Continuous Improvement: Fostering an environment where all employees feel responsible for improving processes can yield significant long-term benefits.
- Collaborate with Suppliers and Partners: Building strong relationships in the supply chain can enhance the flow of information and resources, resulting in a more integrated production system.
Future Outlook
Looking ahead, the realm of manufacturing production systems will likely continue evolving in response to new technologies and societal changes. Here are some projections:
- Increased Automation: As seen in numerous industries, automation will likely become more prevalent, reducing labor costs while increasing accuracy in production tasks.
- Integration of AI: Artificial intelligence will play a central role in optimizing production schedules and predicting equipment issues before they arise, leading to greater efficiency.
- Sustainability Practices: Companies will increasingly focus on reducing their carbon footprint, leading to greener manufacturing processes that emphasize resource efficiency.
- Smart Manufacturing Projects: Digital twins and smart factories will revolutionize how organizations operate, offering real-time data analytics and enhanced control over production processes through interconnected systems.
In summary, the future holds great promise for manufacturing production systems, but it also relies heavily on the strategic decisions made today.