Mastering Overall Equipment Effectiveness in Manufacturing
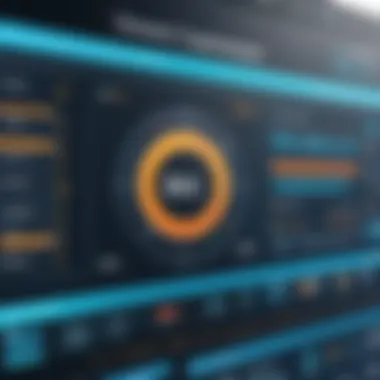
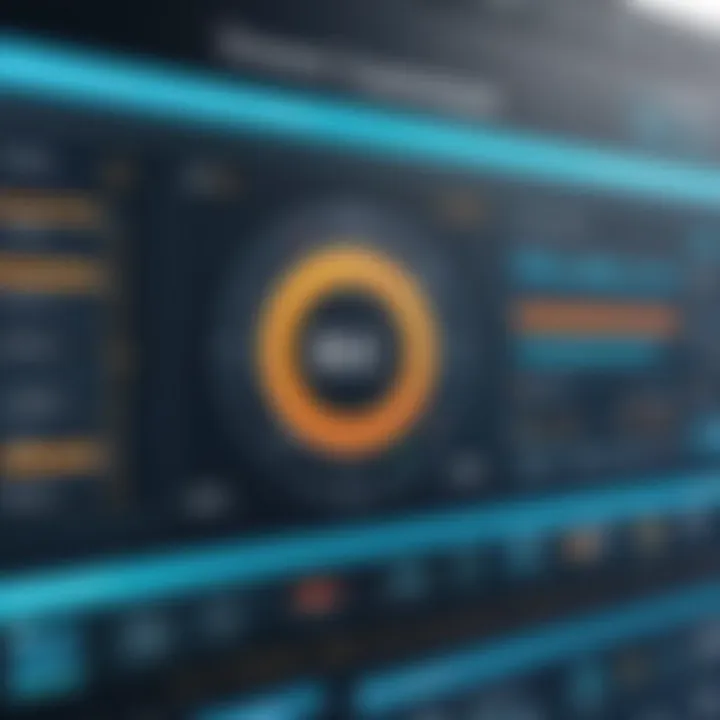
Intro
In the dynamic landscape of modern manufacturing, the quest for efficiency shines brighter than ever. Companies are constantly searching for ways to enhance productivity and reduce waste, making Overall Equipment Effectiveness (OEE) a critical focal point. The role of OEE goes beyond measuring machine performance; it serves as a comprehensive framework that reveals the hidden potential within manufacturing processes. By understanding OEE, practitioners can identify bottlenecks and streamline operations effectively.
This article unpacks the essentials of executing OEE, shedding light on its parameters, practical methodologies for real-world implementation, and how technology interweaves into the process. Each section will guide you through challenges faced by the industry and prescribe actionable solutions, providing a well-rounded perspective for IT professionals, decision-makers, and entrepreneurs alike.
Software Category Overview
Definition and Importance
At its core, the OEE software category encapsulates tools designed to measure and improve manufacturing performance. The importance of these tools cannot be overstated, as they allow companies to spot inefficiencies and prioritize improvements. In many ways, OEE serves as a compass, guiding manufacturers through the rough waters of operational management.
Key Characteristics
The characteristics of effective OEE software encompass several critical attributes:
- User-friendly Interface: Software should be intuitive, ensuring ease of access for users with varying technical expertise.
- Real-Time Data Collection: Instantaneous data support enables quick decision-making, enhancing responsiveness.
- Customizable Dashboards: Tailored dashboards allow users to focus on metrics that matter most to their specific operations.
- Integration Capabilities: Compatibility with existing systems is crucial for seamless data sharing and process coordination.
Comparative Analysis of Top Software Options
Feature Comparison
When selecting OEE software, understanding the features available is vital. Here’s a glimpse into what sets some of the top options apart:
- Fiix: Prioritizes predictive maintenance and advanced reporting tools to proactively manage equipment performance.
- Upkeep: Focuses on mobile accessibility, allowing technicians to input data directly from the production floor, enhancing real-time communication.
- ProShop: Offers an all-in-one solution that streamlines everything from quoting to quality management, aimed at reducing lead time dramatically.
Pricing Models
Pricing models vary significantly among software providers, with approaches including:
- Subscription-Based: Monthly fees typically cover updates and support, prevalent in many cloud-based solutions like Fiix.
- One-Time Purchase: Some vendors offer a one-off fee system, which can lead to lower long-term costs but may require additional investment in upgradability.
- Tiered Pricing: This model allows companies to pay based on the features they choose, making it flexible depending on evolving needs.
"Selecting the right OEE software can significantly influence a manufacturing firm’s bottom line, impacting everything from operational costs to production speed."
By recognizing the characteristics, features, and pricing models of various software options, industry professionals will be better equipped to make informed decisions. Armed with this knowledge, organizations can embark on their journey toward optimizing Overall Equipment Effectiveness, reaping benefits that extend well beyond mere statistical improvements.
Understanding Overall Equipment Effectiveness
Understanding Overall Equipment Effectiveness (OEE) is foundational to fostering efficiency in modern manufacturing. It's not just a management buzzword; it's a critical metric that helps businesses evaluate how effectively their production equipment is utilized. By grasping OEE, professionals can pinpoint areas ripe for improvement, streamline operations, and boost overall production capacity. The significance of OEE transcends mere numbers; it's about fostering a mindset of continuous improvement, ensuring that every cog in the wheel operates smoothly.
Definition of OEE
Overall Equipment Effectiveness, commonly referred to as OEE, is a standard for measuring manufacturing productivity. It combines three key components: availability, performance, and quality. In layman’s terms, OEE measures how much of the manufacturing time is truly productive. To put it simply, if a factory operates at full capacity, is producing goods without defects, and is free from downtime, it achieves a perfect OEE score of 100%. However, real-world operations often reveal different story.
A lower OEE score indicates that there’s room for improvement, whether it’s downtime due to maintenance issues, inefficiencies in production speed, or defects during output. Understanding these metrics allows organizations to diagnose issues clearly, implement solutions rooted in data, and ultimately enhance efficiency.
Historical Context of OEE
The concept of OEE isn’t new; it dates back to the 1960s with the advent of lean manufacturing practices developed by Taiichi Ohno at Toyota. Initially, OEE was a tool used to converse about machine performance in a very structured manufacturing environment. Its roots are intertwined with the philosophies of Toyota Production System, which emphasized waste reduction and streamlined operations.
Over the decades, OEE has morphed into a comprehensive performance indicator embraced across various sectors. Today, it finds usage beyond automotive, making its presence felt in food processing, pharmaceuticals, and electronics manufacturing, among others. With the need for efficiency growing alongside technological advancements, OEE has adapted, becoming a more sophisticated tool for measuring productivity in the face of modern challenges.
Importance in Manufacturing
The importance of OEE in manufacturing cannot be overstated. For one, it provides a clear snapshot of performance, allowing decision-makers to spot long-standing inefficiencies and reallocate resources more wisely.
- Cost Reduction: With insights from OEE, manufacturers can identify areas where they can trim unnecessary costs, whether from excessive machine downtime or poor-quality products.
- Benchmarking: Companies can benchmark their performance against industry standards, fostering healthy competition and driving continuous improvement.
- Enhanced Team Engagement: OEE isn’t just a number; it’s a rallying point for teams. Employees can see the impact of their work on the overall machinery efficiency and feel more connected to organizational goals.
In summary, understanding OEE allows manufacturing leaders to navigate the multifaceted landscape of operational performance with ease. It’s a practical tool that serves not just to analyze past performance but to inspire forward-thinking strategies aimed at enhancing productivity and operational excellence.
Components of OEE
Understanding the components of Overall Equipment Effectiveness (OEE) is vital for manufacturers looking to enhance their operational efficiency. Each component—availability, performance, and quality—plays a distinct role in fabricating a comprehensive view of equipment effectiveness. By dissecting these elements, a clearer path emerges toward improving productivity and increasing profitability. Companies that master these components often find themselves outpacing competitors who overlook their significance.
Availability
Availability is the cornerstone of OEE. It addresses the percentage of time that equipment is actually available for production versus the total scheduled time. To calculate availability, one must consider factors like downtime due to maintenance, breakdowns, and even setup time. A high availability rate indicates that a machine is frequently ready to produce, which is crucial in a fast-paced manufacturing environment.
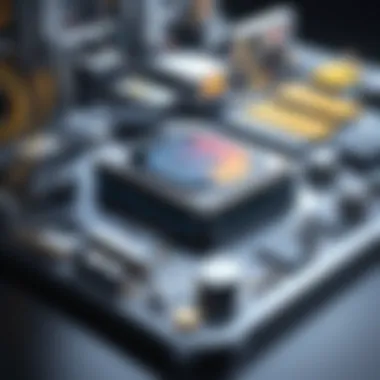
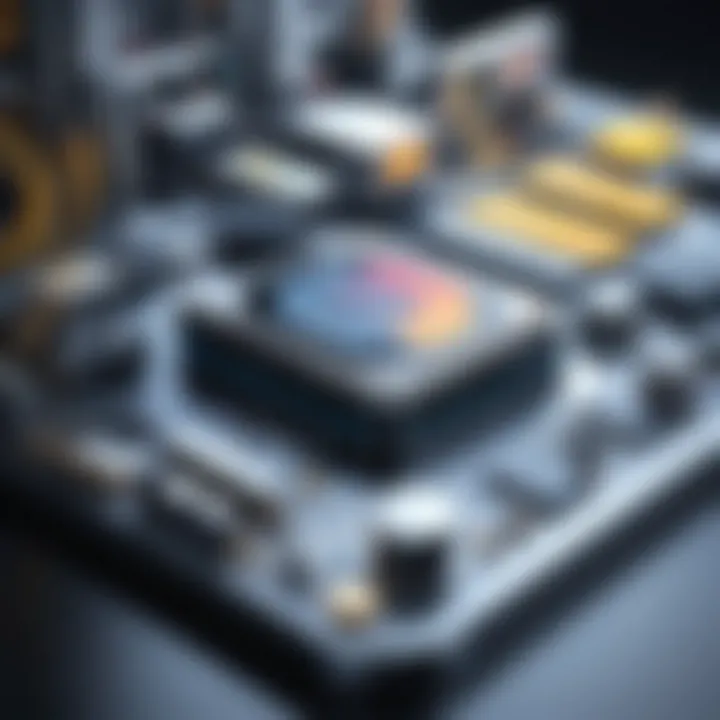
For instance, a factory that runs for eight hours with three hours lost to maintenance struggles with efficiency. Achieving availability requires vigilance in equipment health monitoring and proactive maintenance. Regular inspections and timely repairs can keep machines running smoothly, maximizing the productive hours available. In simple terms:
- Analyze Downtime: Identify reasons for downtime to focus improvement efforts.
- Preventive Maintenance: Implementing a schedule for maintenance can prevent unforeseen breakdowns.
- Training Operators: Well-trained operators can reduce setup time, thus positively impacting availability.
Calculating OEE
Calculating Overall Equipment Effectiveness (OEE) is a pivotal step in the journey toward enhancing manufacturing performance. It enables organizations to gauge the productivity of their equipment and processes, helping pinpoint where improvements are necessary. Accurately calculating OEE assists in identifying inefficiencies and empowers managers to make informed decisions. The simplicity of the formula belies its importance; when utilized effectively, it can lead to significantly improved output and reduced waste.
To grasp the significance of calculating OEE, consider its benefits. First, it provides a clear view of how well equipment is performing compared to its potential. Second, it establishes a standard for performance measurement, which can guide performance improvement initiatives. Lastly, it fosters a culture of continuous improvement within the workforce, as employees become aware of their impact on the overall production process.
Formula Breakdown
The OEE calculation is grounded in a deceptively simple formula, which blends three key components: Availability, Performance, and Quality. These components are expressed as follows:
OEE = Availability × Performance × Quality
- Availability measures the percentage of time that the equipment is actually running versus the scheduled production time. This takes into account downtime due to maintenance or breakdowns.
- Performance refers to the speed at which the equipment operates compared to its maximum possible speed. It highlights how much of the potential output is realized during actual production.
- Quality represents the proportion of good units produced against the total units made, factoring in defects or rework.
To elaborate a bit more:
- Availability = (Operating Time / Scheduled Time) × 100%
- Performance = (Actual Output / Ideal Output) × 100%
- Quality = (Good Output / Total Output) × 100%
These formulas work in harmony to create a succinct representation of how efficiently equipment operates. Keeping these factors in balance requires astute regular monitoring.
Example Calculations
Let's consider a real-world scenario to illustrate how this formula comes into play:
- Scheduled production time for a factory: 500 minutes
- Actual operating time: 400 minutes
- Ideal output: 200 units/hour
- Actual output: 150 units
- Good output (defect-free): 140 units
Now, let’s plug these numbers into our formulas:
- Calculate Availability:
Availability = (400 minutes / 500 minutes) × 100% = 80% - Calculate Performance:
Actual Output = 150 units / (400 minutes / 60) = 22.5 units/minute
Ideal Output = 200 units/hour = 3.33 units/minute
Performance = (22.5 / 33.33) × 100% = 67.5% - Calculate Quality:
Quality = (140 / 150) × 100% = 93.33%
Now that we have each component calculated, let’s compute the OEE:
OEE = % × 67.% × 93.% = 50.%
In this example, an OEE of 50.4% suggests significant room for improvement, pointing to availability issues, performance limitations, and quality control challenges.
By understanding this calculation and its implications, decision-makers can steer their manufacturing processes toward greater efficiency and effectiveness.
Implementing OEE in Manufacturing Settings
Implementing Overall Equipment Effectiveness (OEE) within manufacturing settings serves as a bedrock for any company striving for operational excellence. It's not merely about crunching numbers; it’s about establishing a culture of continuous improvement and ensuring that every cog in the wheel is working harmoniously. The real value of OEE lies in its capacity to unravel inefficiencies that might not be easily visible on the surface. Successfully integrating OEE into everyday operations can lead to substantial benefits, such as enhanced productivity, reduced downtime, and improved quality—all pivotal for staying competitive in today’s fast-paced market.
By focusing on specific elements of OEE implementation, organizations can uncover layers of potential that were previously unexploited. For instance, having a clear understanding of existing performance metrics sets a baseline from which improvements can be identified and measured.
Assessing Current Performance Metrics
Before diving headfirst into optimizing processes, it's crucial to assess current performance metrics. This stage serves as a diagnostic tool, providing visibility into how machinery and workflows are currently performing. Common metrics to consider include:
- Downtime Analysis: Identifying how often and for what reasons equipment is not operational can reveal patterns that require immediate attention.
- Production Rates: Analyzing how much product is being produced versus how much could be produced in an ideal scenario helps in setting realistic goals.
- Quality Metrics: Understanding the rate of defects or rework can give insights into areas that need process refinement.
"The journey of a thousand miles begins with one step."
By collecting and analyzing these metrics, organizations can pinpoint specific areas of waste, allowing for targeted OEE improvement efforts. This focused approach ensures that efforts to boost efficiency are grounded in actual data rather than assumptions, serving as the initial stepping-stone towards further advancements.
Setting Targets for Improvement
Once performance metrics are established and assessed, the next logical step is setting targets for improvement. These targets should be realistic, measurable, and aligned with broader business objectives. When determining targets for OEE enhancement, consider:
- Specificity: Vague targets lead to vague outcomes. Establish clear, specific objectives like increasing production by a certain percentage or reducing downtime by a specific amount.
- Achievability: Targets should push the envelope yet remain within reach. Setting unrealistic goals may lead to frustration and loss of morale.
- Time-bound: Deadlines instigate action. Setting timelines for achieving these targets creates a sense of urgency and accountability.
An example might be increasing OEE to 85% within the next quarter by focusing on reducing breakdowns and enhancing quality. Such clarity ensures everyone understands what success looks like and what they must do to contribute.
Training Employees on OEE Practices
The best strategies don't mean much without the people empowered to execute them. Training employees on OEE practices is not merely a checkbox activity—it’s essential for embedding OEE into the organization’s DNA. This involves:
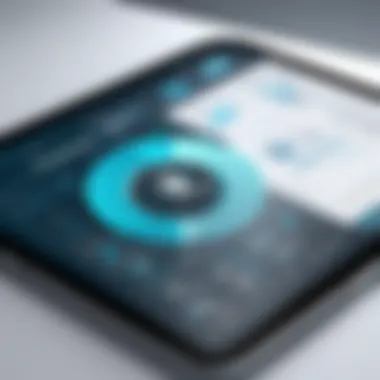
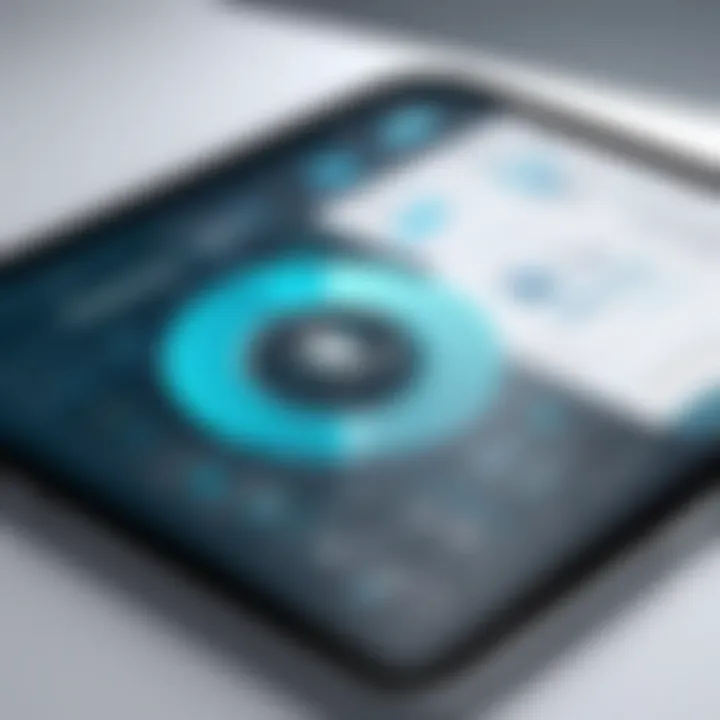
- Workshops and Seminars: Host comprehensive training sessions that not only cover what OEE is but also why it’s important, fostering a culture of ownership.
- Hands-On Training: Equip employees with direct experience in monitoring and calculating OEE, using their own data to cultivate a practical grasp of concepts.
- Feedback Loops: Establish mechanisms for employees to provide feedback and suggestions on OEE practices, ensuring that improvement remains a two-way street.
When employees are well-informed and engaged, they are more likely to buy into the process and contribute meaningfully to OEE goals. By embedding these practices into daily routines, OEE becomes a natural part of the workflow rather than an imposed initiative, making it more likely to succeed.
Challenges in OEE Execution
Executing Overall Equipment Effectiveness (OEE) effectively means navigating a minefield of potential challenges. These challenges can not only hinder the accuracy of OEE measurements but also stall progress toward achieving operational excellence. Recognizing these obstacles is imperative for those in the trenches of manufacturing. Understanding the difficulties surrounding OEE execution is equally as vital as grasping its components and metrics.
Tackling these issues head-on encompasses a multi-faceted approach, acknowledging that while OEE offers valuable insights, it’s not a silver bullet. This section examines the major challenges that can crop up when applying OEE in the modern manufacturing landscape.
Data Collection Issues
One of the most significant hurdles in mastering OEE is the reliability and accuracy of data collection. OEE relies heavily on three core components: availability, performance, and quality, which in turn depend on precise data. Without reliable data, any effort put into calculating OEE can be akin to chasing shadows.
- Inconsistent data sources: Many manufacturers still utilize outdated systems to track production data. If data isn’t capturing real-time changes on the ground, discrepancies will emerge, leading to skewed OEE percentages.
- Manual data entry errors: Companies often still rely on humans to input data, and mistakes can create a cascade of inaccuracies. It’s all too easy for typos or lapses of concentration to skew performance metrics.
- Measurement bias: Sometimes, personnel might intentionally or unintentionally underreport downtime or quality issues to enhance the OEE figures. This can lead to inflated metrics that do little to drive true performance improvement.
To combat these issues, manufacturers should invest in automated monitoring systems and Internet of Things (IoT) technologies, which can drastically enhance the reliability of collected data.
Resistance to Change in Workforce
Implementing OEE is as much a human challenge as a technical one. Many workers and management alike can display a resistance to change, viewing new practices through a lens of skepticism. This natural hesitation isn’t simply about the tool itself, but can often stem from a lack of understanding.
- Cultural inertia: Established routines are often comfortable and predictable. Encouraging a shift to a more data-driven environment may be perceived as intrusive, fostering resistance among employees.
- Fear of job displacement: The introduction of new technologies, especially automation, can spark anxiety among employees who fear their roles may become redundant.
- Training gaps: Without effective training programs to equip the workforce with knowledge and skills related to OEE, employees might feel overwhelmed and reluctant to embrace the changes.
To overcome this resistance, it’s crucial to cultivate an organizational culture that values continuous improvement. Open dialogues, regular training sessions, and demonstrating the benefits of OEE can help pave the way for smoother transitions.
Integration with Legacy Systems
For many organizations, especially established firms, the road to OEE optimization is filled with the remnants of legacy systems. These older systems can pose significant complications in collecting, analyzing, and reporting OEE data effectively.
- Compatibility issues: New technologies may need to work alongside legacy systems—a challenging proposition. Many older systems may not support the integration of advanced analytics or IoT solutions, creating barriers in the data flow.
- High costs: Upgrading or replacing legacy systems can come with a hefty price tag. Many manufacturers weigh the immediate benefits of OEE against the costs of such investments, often leading to the decision to stay with the status quo.
- Data silos: Legacy systems often operate in isolation, preventing the seamless flow of information across departments. This lack of centralized data significantly hampers meaningful OEE calculations.
Effective strategies for overcoming these integration hurdles include taking a gradual approach to technology upgrades and investing in middleware solutions that facilitate communication between disparate systems.
"Navigating the roadblocks in OEE execution is not just about fixing problems; it’s about transforming the entire cultural and technological landscape of manufacturing.
By proactively addressing these challenges, companies can not only enhance their OEE initiatives but also build a stronger foundation for future process improvements. Understanding and tackling these hurdles opens the door to a more efficient and responsive manufacturing environment."
Scrutinizing challenges surrounding OEE execution reveals vital considerations to help ensure its success.
Technological Support for OEE
In today's fast-paced environment, having a robust technological framework is indispensable for effectively executing Overall Equipment Effectiveness (OEE). The integration of technology streamlines processes, enhances data accuracy, and significantly boosts productivity levels or so it appears. But, let’s break it down further to understand the specific elements that make technological support a cornerstone for OEE.
Technological tools can bring forth multiple benefits. Collaboration of automation, the Internet of Things (IoT), data analytics, and specialized software solutions helps in capturing real-time data, making informed decisions, and fundamentally reshaping how manufacturers operate. The importance of these tools cannot be overstated, as they enable organizations to assess performance accurately, discover issues as they arise, and pivot quickly when necessary.
Automation and IoT in OEE Monitoring
Automation, enhanced by IoT technology, serves as the eyes and ears of OEE monitoring. By employing automated systems, manufacturers can keep tabs on the machines in real time. This means that instead of waiting for scheduled maintenance checks, problems can be identified and addressed before they cause significant downtimes.
Think of it as having a personal trainer; you can tweak your routine based on immediate feedback rather than waiting for results weeks down the line. Some examples of how automation and IoT reshape monitoring include:
- Sensors: Smart sensors collect data on equipment performance, identifying inefficiencies at the drop of a hat.
- Alerts: Real-time alerts notify operators about machine malfunctions or underperformance, speeding up repairs.
- Predictive Maintenance: This enables proactive adjustments based on data analytics, reducing the likelihood of breakdowns.
As manufacturers continue to embrace these technologies, it becomes easier to gather comprehensive insights directly from the equipment. The outcome is a more agile operation where adjustments can be made in near real-time.
Role of Data Analytics
Data analytics play a pivotal role in distilling large volumes of machine data into actionable insights. The capacity to analyze performance trends and uncover underlying issues translates into a significant competitive edge. It allows decision-makers to see the forest for the trees. Here’s why data analytics is vital for OEE:
- Performance Evaluation: Analyzing past performance enables businesses to identify which machines are performing optimally and which require attention.
- Root Cause Analysis: When declines in OEE are observed, digging into the data helps discover the underlying issues rather than treating symptoms.
- Forecasting: Historical data can also predict future performance, guiding resource allocation and management decisions.
Leveraging advanced analytical tools like machine learning can facilitate deeper insights that humans might overlook. By understanding these patterns, organizations can take action before issues escalate.
Software Solutions for OEE Calculation
Software specialized in OEE calculation is critical for a structured approach to performance management. These solutions take the often daunting task of gathering and processing data and streamline it with user-friendly interfaces. Key benefits include:
- Centralization of Data: Instead of pulling from multiple sources, comprehensive dashboards allow for easy access to performance metrics in one place.
- User-Friendly Interfaces: Most modern software solutions come equipped with intuitive designs that make it easy for staff to input data and analyze key performance indicators without a steep learning curve.
- Customizable Metrics: Businesses can tailor metrics based on their specific operational needs, leading to more relevant insights and decisions.
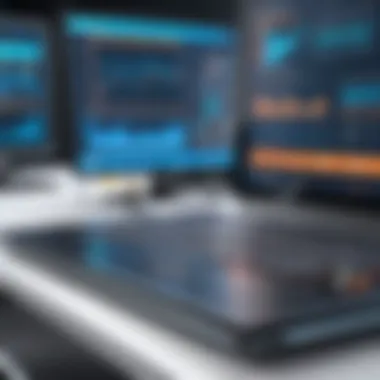
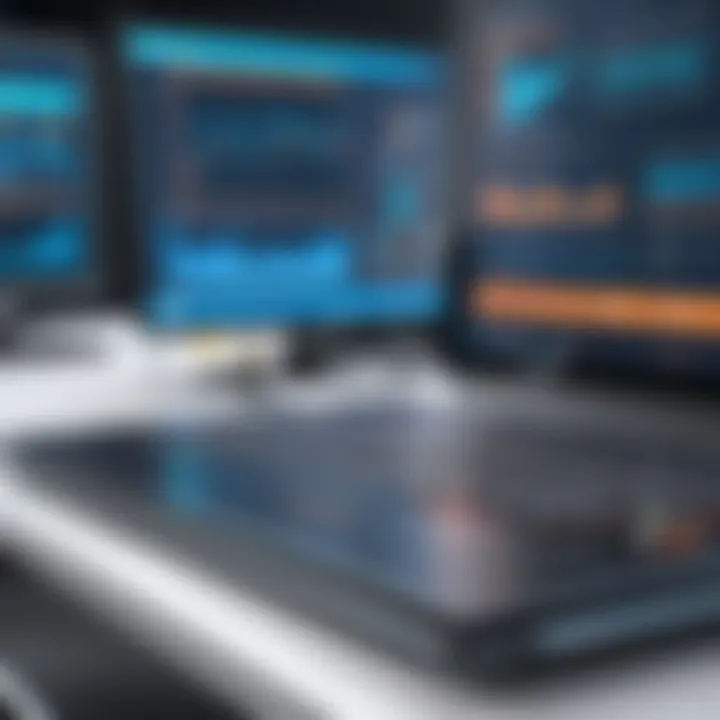
With software solutions, organizations can boost transparency and ensure that everyone is aligned with OEE goals. This not only enhances accountability but allows teams to focus more on strategies that lead to improvement.
The intersection of technology and OEE execution is not merely a trend; it’s a fundamental shift in how manufacturing operates. Those who harness this potential can expect enhanced efficiency and greater resilience in a competitive landscape.
Evaluating OEE Results
In the world of manufacturing, evaluating Overall Equipment Effectiveness (OEE) results stands as a critical step in assessing productivity and efficiency. Understanding the nuances of OEE results helps businesses identify areas for improvement and facilitates strategic planning. It's not merely about crunching numbers; it’s about deriving actionable insights that steer operational excellence.
Reviewing Performance Trends
Analyzing performance trends is essential for any manufacturing operation looking to tighten its processes. When we examine OEE results over time, patterns begin emerging. This review can reveal how equipment performance fluctuates under different conditions, signaling when things went awry during production runs.
- Identifying Consistencies: It's crucial to look for regular trends. For instance, a factory might notice that their machinery consistently underperforms during specific shifts. Recognizing these trends can help managers allocate resources more effectively.
- Spotting Irregularities: While consistent patterns are important, spotting anomalies is equally vital. An unexpected drop in OEE performance might signify emerging problems that need immediate attention. For example, if a machine typically runs at 80% efficiency but suddenly drops to 50%, it warrants a deeper investigation to identify the cause.
- Benchmarking: Manufacturers can establish performance benchmarks by reviewing historical data. These benchmarks can offer a point of reference that guides future performance targets and improvement strategies.
In this light, reviewing performance trends becomes not just a thermometer but a compass for decision-makers in manufacturing. By evaluating these trends consistently, organizations can pivot swiftly and implement solutions that bolster productivity.
Adjusting Strategies Based on Data
Data-driven adjustments are the lifeblood of any effective manufacturing strategy. Once OEE results are evaluated and performance trends reviewed, the next logical step is to recalibrate strategies based on insights garnered from this analysis.
- Fine-Tuning Operations: Utilizing specific data points to tweak operational procedures can lead to significant efficiency gains. Say OEE calculations reveal that certain machines are underutilized during peak hours; reallocating tasks or switching schedules may better harness those resources.
- Feedback Loops: Another important aspect lies in the creation of feedback loops. Connecting performance evaluations to ongoing operational strategies ensures that improvements are continual rather than one-off adjustments. For instance, a manufacturer can set a standard for periodic assessment of processes and equipment, adjusting in response to findings – creating a culture of continuous improvement.
- Integrating Cross-Departmental Insights: Sometimes, the answers aren’t just in one area. Getting input from sales, maintenance, and production teams when analyzing OEE results can lead to a more holistic perspective. These cross-departmental insights can inform better decision-making, such as understanding the impact of order volumes on machine efficiency.
"Continuous evaluation based on solid data is the roadmap that allows manufacturers to stay ahead, iterating on processes until they achieve operational excellence."
Ultimately, refining strategies according to OEE evaluation results isn’t just an exercise in number-crunching; it's about fostering a responsive and agile manufacturing environment that embraces ongoing improvement.
Real-World Case Studies
In the intricate world of manufacturing, theory alone doesn't cut it. The importance of real-world case studies in understanding Overall Equipment Effectiveness (OEE) cannot be overstated. They serve as tangible evidence not just of the potential benefits of OEE, but also of the challenges that organizations might face when implementing these systems.
By studying the experiences of various industries, manufacturers can draw lessons and adapt strategies that work best for their unique circumstances. These case studies illustrate best practices, highlight common pitfalls, and reveal how businesses can harness OEE to achieve remarkable improvements in productivity and efficiency. They provide insights that can only come from living through the processes, failures, and triumphs of OEE execution.
Successful Implementation in Automotive Industry
Take, for instance, the automotive industry—a sector where efficiency is king. Companies like Toyota have long been pioneers in OEE application. Their famous Toyota Production System emphasizes minimizing waste while maximizing productivity. The implementation of OEE allowed Toyota to analyze machine downtime, production speeds, and product quality closely.
By focusing on availability, Toyota identified machines that had high idle times due to maintenance issues. They revamped their scheduled maintenance strategies, leading to improved availability rates. The incorporation of data analytics not only contributed to real-time monitoring but also spurred a culture of continuous improvement. As a result, Toyota achieved significant gains in their production line efficiency and ultimately, in their profit margins.
This success didn’t come without bumps along the road. Employees had to undergo training to understand OEE metrics and their relevance in daily operations. Resistance was met initially, but as teams began to recognize the impact of their efforts on output quality and their own work environment, buy-in was secured.
Challenges Faced in Food Processing Sector
Meanwhile, the food processing sector faces its own set of hurdles when it comes to OEE execution. A well-known case involves a large food manufacturing company that struggled to maintain consistent quality while ramping up production. The industry itself is laden with unique challenges, such as regulatory constraints and a high level of product variability based on seasonal ingredients.
One significant challenge the food processor faced was integration with legacy systems, which housed outdated data. This lack of technological synergy made it difficult to collect accurate data for OEE calculations. Operators had no real-time insights into machine performance, leading to misunderstandings and missed opportunities for addressing inefficiencies.
Additionally, training employees on OEE practices posed its own difficulties. The workforce was accustomed to traditional methods and skeptical of adopting new technologies and processes. It took a concerted effort from management to establish a clear communication strategy that educated the workforce on how OEE could not only optimize production but also enhance product quality and safety.
Ultimately, the company started leveraging automated IoT solutions that provided real-time data analysis. This empowered operators with actionable insights, allowing them to make immediate adjustments in production—which resulted in increased OEE values.
In summary, analyzing these case studies reveals a wealth of knowledge that emphasizes adaptability and a clear understanding of internal and external factors that can affect OEE execution. Learning from others’ experiences can drive decisions that optimize production in any field.
Future of OEE in Manufacturing
The landscape of manufacturing is rapidly shifting due to technological advancements and changing market demands. The focus now is on achieving greater efficiency and sustaining competitive advantage. Therefore, the future of Overall Equipment Effectiveness (OEE) becomes increasingly relevant. As companies strive to boost productivity, OEE presents not just metrics, but also a framework guiding them into a smarter, more efficient operational realm.
Emerging Trends and Technologies
As we gaze into the future of OEE, a slew of emerging trends and technologies shape its evolution. One notable trend is the integration of Artificial Intelligence (AI) and Machine Learning. These technologies enable predictive maintenance capabilities, reducing unplanned downtime by accurately forecasting equipment failures before they occur. For instance, a manufacturing plant using AI-driven alerts can save significant costs and maintain operational continuity.
Moreover, Internet of Things (IoT) devices are revolutionizing the data collection process, allowing real-time monitoring of equipment performance. With the connected devices, companies can gather vast amounts of data, providing a clearer picture of inefficiencies and where improvements are needed. Automating these processes not only increases accuracy but also reduces the human error factor.
Additional technologies like Augmented Reality (AR) and Virtual Reality (VR) are gaining traction in training scenarios. They offer hands-on training experiences without interrupting production workflows. Employees can engage with equipment in a simulated environment, increasing their readiness and understanding of OEE practices.
The relevance of these technologies cannot be overstated:
- Improved Real-Time Data Collection: Enhanced insights into equipment performance leads to better decision-making.
- Informed Predictive Insights: Understanding when maintenance should take place minimizes operational hiccups.
- More Engaged Workforce: Utilizing immersive tech for training can bolster employee commitment to OEE initiatives.
The Shift Towards Continuous Improvement
The future of OEE also signifies a cultural transition within organizations. The shift towards continuous improvement demands that businesses adopt a growth mindset. Rather than merely aiming for immediate gains, the focus shifts to sustainable progress. Continuous improvement is not just a process; it’s a philosophy that every team member must embrace.
The integration of OEE in a continuous improvement framework has several implications:
- Regular Performance Reviews: Companies are encouraged to constantly analyze their OEE scores and operational data, allowing them to identify small inefficiencies that build up over time.
- Employee Empowerment: Individuals from the production floor to management are encouraged to contribute to improvement initiatives. When employees see their input valued, it further drives a culture of innovation.
- Collaboration Across Departments: OEE success hinges on effective collaboration among various teams. Maintenance, production, and management must work hand-in-hand to identify problems and propose solutions.