Effective Material Inventory Management Strategies
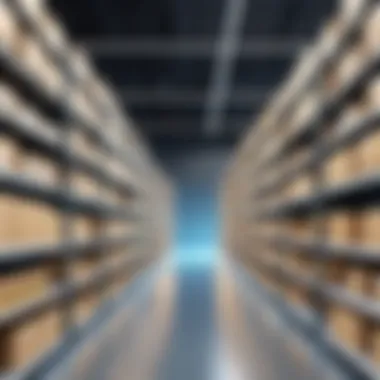
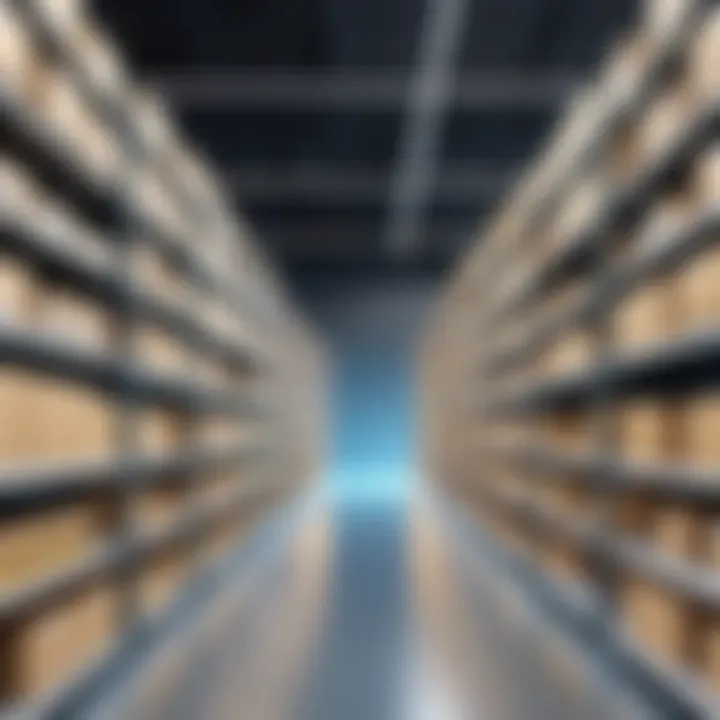
Intro
Effective material inventory management is a critical aspect of sustaining operational efficiency in any organization. It is not merely about tracking items but involves a systematic approach that ensures the right materials are available at the right time. This process can significantly influence cost control, customer satisfaction, and overall productivity.
Material inventory management encompasses various strategies, practices, and tools designed to optimize how organizations handle supplies. Challenges always arise, from overstocking to stockouts, and each issue can have cascading effects on the business. By understanding the strategies detailed in this article, decision-makers can enhance their inventory practices and align them with organizational goals.
Moreover, the advent of technology has transformed inventory management practices, introducing tools that aid in monitoring and controlling material flows effectively. This article seeks to illuminate these strategies, provide insight into the application of modern inventory solutions, and discuss several key performance indicators (KPIs) that gauge inventory success. The overall aim is to equip organizations with essential knowledge for improving their inventory systems, leading to sustainability and long-lasting efficiency.
Software Category Overview
Definition and Importance
In the realm of material inventory management, software solutions act as powerful allies. They streamline processes, provide real-time data, and enable better decision-making. Such software assists organizations in tracking inventory levels, orders, deliveries, and forecasts. As businesses grow, manually managing inventory can result in significant challenges, underscoring the need for effective software.
Key Characteristics
When evaluating inventory management software, the following characteristics are essential:
- Real-Time Tracking: The ability to see inventory levels as they change is crucial for informed decision-making.
- Reporting Features: Comprehensive reporting can provide insights into trends, helping organizations forecast needs better.
- Integration Capabilities: The software should integrate well with existing systems, such as ERP or accounting software, for seamless data flow.
- User-Friendly Interface: An intuitive interface ensures that all staff can use the software efficiently, reducing training time.
- Scalability: The software should adapt to growing business needs without requiring a complete overhaul.
"The choice of inventory management software directly impacts an organization's ability to efficiently manage its resources and ultimately drive growth." – Industry Expert
Comparative Analysis of Top Software Options
When comparing various software options available in the marketplace, it is important to identify their key features and pricing models.
Feature Comparison
Notable software solutions often include:
- Oracle NetSuite Inventory Management: Offers robust features such as multi-location tracking and integration with e-commerce platforms.
- Fishbowl Inventory: Known for its flexibility and strong manufacturing features tailored for small to medium-sized enterprises.
- Zoho Inventory: Focuses on user experience with comprehensive functionality at a competitive price point.
Each software solution has its strengths, depending on the specific needs of the organization.
Pricing Models
Understanding pricing models is also crucial. Many inventory management systems operate on:
- Subscription-Based Pricing: Organizations pay a monthly or annual fee to use the software.
- One-Time License Fee: A single payment for lifetime access, ideal for those who prefer not to deal with recurring fees.
Ultimately, selecting the right inventory management software requires thoughtful consideration of your organization’s goals, existing systems, and budget constraints.
Understanding Material Inventory Management
Material inventory management is a critical aspect of business operations that directly influences productivity and profitability. Effective management of materials ensures that organizations maintain an optimal level of stock, aligning supplies with production schedules and customer demand. The goal is to minimize waste, reduce costs, and enhance efficiency.
Definition and Importance
Material inventory management can be defined as the systematic approach to overseeing and controlling the flow of materials within a company. It involves planning, organizing, directing, and controlling the storage and movement of materials, from the stage of acquisition to the final point of use.
The significance of this process cannot be understated. Proper inventory management provides a framework for ensuring that materials are available when needed while avoiding excess inventory. This balance is crucial. Excess stock ties up capital and incurs carrying costs, while stockouts can lead to production delays and lost sales.
By understanding and implementing effective inventory management strategies, businesses can achieve:
- Reduced costs: Effective inventory management leads to lower holding costs and improves cash flow.
- Enhanced customer satisfaction: Adequate inventory ensures timely fulfillment of customer orders, fostering trust and loyalty.
- Informed decision-making: Accurate data collection and analysis allow for better forecasting and inventory control decisions.
Key Components
Several key components underpin material inventory management:
- Inventory Levels: Understanding the different types of inventory levels required for business operations is fundamental. This includes safety stock, reorder points, and maximum stock levels.
- Inventory Tracking: Effective tracking methods, whether through manual counts, barcode systems, or advanced software, are pivotal. Without accurate tracking, knowing the status and location of materials becomes challenging.
- Supplier Management: Reliable supplier relationships can affect material availability. Managing supplier performance and communication ensures timely deliveries.
- Ordering Processes: Streamlined ordering processes minimize delays and enhance efficiency. This involves deciding on reorder levels, order quantities, and lead times for suppliers.
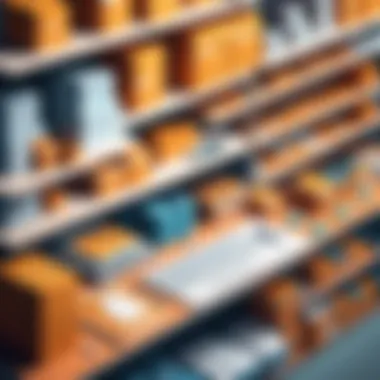
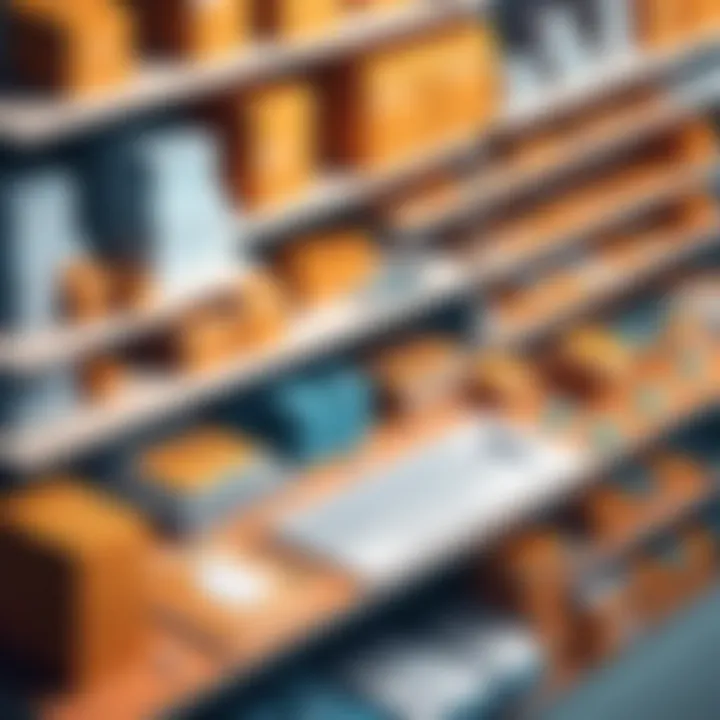
Incorporating these components into a coherent material inventory management strategy is essential. They work in tandem to create a system that not only meets current operational needs but is also adaptable to future changes.
"Effective material inventory management can be the difference between operational efficiency and chaos."
Types of Inventory
Understanding the different types of inventory is fundamental to effective material inventory management. Each category serves a unique purpose and has its own set of challenges and considerations. Organizations often manage multiple types of inventory simultaneously, making it crucial to recognize the distinctions between them. Doing so can enhance not only operational efficiency but also customer satisfaction and overall profitability.
Raw Materials
Raw materials represent the basic inputs used in the manufacturing process. These materials are typically unprocessed or minimally processed goods required for production. Managing raw materials efficiently ensures that production processes are not interrupted due to shortages. It is vital to maintain optimal stock levels to avoid overstocking, which may lead to increased holding costs.
Considerations around raw materials include:
- Supplier reliability and lead times
- Costs associated with storage and transportation
- Quality assurance measures during procurement
Effective tracking of raw materials can streamline operations and reduce waste. By implementing robust inventory management techniques, businesses can avoid common pitfalls such as an excess of obsolete materials which can tie up resources.
Work-in-Progress (WIP) Inventory
Work-in-Progress inventory includes items that are in the production process but are not yet finished. This type of inventory can be challenging to manage due to its inherently dynamic nature. Frequent changes in production schedules, machine breakdowns, and labor availability can all influence WIP levels.
Benefits of managing WIP effectively include:
- Improved production flow
- Better allocation of resources
- Enhanced scheduling accuracy
A key strategy is to implement just-in-time practices that align production with demand, thus minimizing WIP. Regular reviews of work in progress can help maintain balance, and timely adjustments can prevent bottlenecks or excess inventory.
Finished Goods
Finished goods are products ready for sale to customers. This type of inventory is often the most visible to stakeholders, making its management particularly crucial. Effectively handling finished goods inventory aids in fulfilling customer orders promptly, thereby enhancing customer satisfaction.
Important aspects of finished goods management include:
- Demand forecasting accuracy
- Inventory turnover rates
- Storage limitations and logistics
Monitoring finished goods levels ensures that sales opportunities are not lost due to stockouts. Additionally, high turnover rates can indicate strong sales performance and clear trends in customer preferences.
Maintenance, Repair, and Operations (MRO)
MRO inventory encompasses all the tools, supplies, and materials required for maintenance and repair tasks within the operational infrastructure. This inventory type, while not directly linked to the production of goods, plays a critical role in supporting overall operations.
Key considerations for managing MRO inventory consist of:
- Readily available parts to minimize downtime
- Keeping track of supplies used in maintenance activities
- Evaluation of reorder points and quantities
An efficient MRO inventory system can help prevent production halts and maintain smooth operations. By utilizing software solutions that integrate with broader inventory management practices, organizations can ensure that MRO items are always on hand when needed.
"Proper inventory control is a crucial element that affects the profitability and effectiveness of an organization."
Through clear categorization and proactive management of these inventory types, businesses can ultimately achieve better operational efficiency and greater financial performance.
Challenges in Material Inventory Management
Material inventory management is a complex and critical aspect of supply chain operations. Identifying and addressing the challenges within this area is essential for companies aiming to enhance efficiency and reduce costs. Inadequate inventory management can lead to severe operational setbacks, thus understanding these challenges is not just beneficial but necessary. Poor inventory practices can hinder productivity and can significantly affect customer satisfaction. Those in decision-making roles must prioritize overcoming these challenges to ensure sustainability and growth.
Overstocking and Stockouts
Overstocking occurs when excess inventory is held, often leading to higher carrying costs. This situation can create a myriad of issues, including increased warehousing fees, spoilage, and diminished cash flow. Conversely, stockouts arise when inventory levels drop to zero, potentially resulting in missed sales opportunities and dissatisfied customers. Managing the delicate balance between these two extremes is crucial.
Organizations leverage various strategies to mitigate both challenges. Regular inventory audits can uncover discrepancies and guide decisions on purchasing. Additionally, implementing strong forecasting methodologies can help predict trends, thus reducing instances of both overstock and stockout.
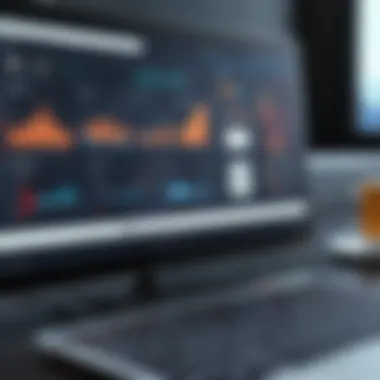
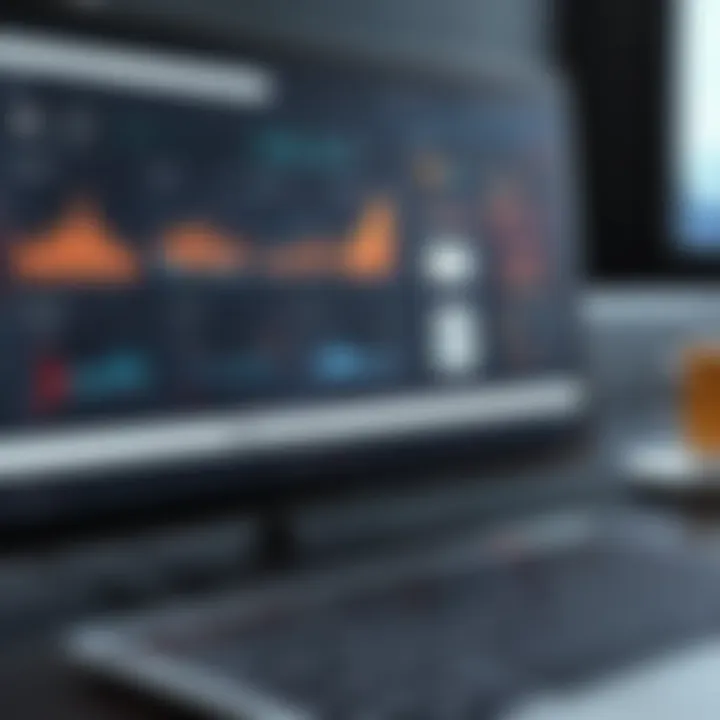
Moreover, adopting Just-in-Time (JIT) inventory practices assists firms in aligning orders closely with production schedules. This push towards efficiency emphasizes the importance of understanding market demand and proper timing in procurement processes.
Demand Forecasting Issues
Accurate demand forecasting is integral to effective inventory management. Poor forecasts can lead to either surplus inventory or shortages. The lack of precision in predicting customer needs often results from outdated data or inadequate analytical tools. This problem is compounded in industries with volatile markets, where consumer preferences can shift rapidly.
Investing in advanced data analytics tools can improve forecast accuracy. Decision-makers should consider using software solutions that analyze market trends, seasonal fluctuations, and historical sales data. Regularly reviewing and adjusting forecasting models based on current trends is also essential. By addressing forecasting inaccuracies, businesses can make informed decisions that lead to optimized inventory levels.
Inefficient Tracking Systems
Inefficient tracking systems can severely hinder inventory management. Relying on outdated methods, such as manual logs or spreadsheets, can lead to errors and lost information. This inefficiency results in difficulties in identifying stock levels, locations, and statuses. The consequences include unnecessary delays in order fulfillment and inaccuracies in inventory records.
Modern technology presents solutions to these challenges. Utilizing barcode systems and RFID technology can significantly enhance tracking abilities. These tools allow for real-time data collection and better visibility into inventory flows. Additionally, implementing comprehensive inventory management software can centralize data, streamline processes, and ultimately reduce human error.
Efficiency in tracking not only saves time but also reduces the costs associated with mismanaged inventory.
By addressing the core challenges in material inventory management—overstocking and stockouts, demand forecasting issues, and inefficient tracking systems—businesses position themselves for improved operational execution. These aspects are intertwined and addressing each contributes to a holistic solution for more effective inventory management.
Strategies for Effective Material Inventory Management
In the context of material inventory management, effective strategies are pivotal for enhancing operational efficiency. These strategies not only help organizations optimize their inventory levels but also enable them to respond more swiftly to market demands. By implementing well-defined strategies, companies can minimize costs while ensuring product availability. Such approaches are crucial for sustaining competitive advantage in a fast-paced economic environment.
Just-in-Time (JIT) Inventory
The Just-in-Time (JIT) inventory approach is a powerful strategy designed to reduce inventory costs. This method aims to increase efficiency by receiving goods only as they are needed in the production process. This limits the inventory that is held, which in turn reduces holding costs, minimizing waste. JIT requires strong communication with suppliers and a high level of coordination along the supply chain. Companies utilizing JIT must be adept in demand forecasting and agile in their operational practices. When implemented effectively, JIT can lead to significant cost savings and enhance production flexibility.
ABC Analysis
ABC Analysis is a vital technique used for categorizing inventory items based on their importance. This method classifies items into three groups: 'A' items, which are highly valuable but in low quantity; 'B' items, which are moderate in both value and quantity; and 'C' items, which are low in value but often purchased in high quantity. The rationale behind this classification is to prioritize management efforts and resources where they can achieve the greatest impact. Regular review and adjustment of these categories can align inventory management with evolving business goals. For decision-makers, ABC Analysis provides a clear lens through which to view inventory efficiency and effectiveness.
First-In, First-Out (FIFO) Method
The First-In, First-Out (FIFO) method is an essential inventory management strategy that ensures the oldest stock is sold first. This approach mitigates the risk of spoilage, especially in industries dealing with perishable goods or products with expiration dates. FIFO also supports more accurate financial reporting and aligns with international accounting standards. Adopting this method helps maintain fresh inventory and assures customers that they receive high-quality products. Continuous review of inventory levels is important to implement FIFO effectively, ensuring that stock rotation is consistent and reliable.
Effective material inventory management directly influences overall business profitability by optimizing resource allocation and reducing waste.
Technology and Tools for Inventory Management
The integration of technology and tools into inventory management has profoundly changed how businesses operate. In an age where efficiency and accuracy are paramount, leveraging technology becomes not just beneficial, but essential. This section focuses on key elements, advantages, and considerations that businesses must keep in mind when adopting modern inventory management systems.
Inventory Management Software
Inventory management software is central to optimizing material control. This software allows businesses to track inventory levels in real-time, automate reordering processes, and generate reports that can provide insights into usage trends. Notably, software solutions can significantly reduce human error and enhance decision-making capabilities.
When choosing software, decision-makers should consider factors such as scalability, user-friendliness, and integration capabilities with existing systems. A robust inventory management system can facilitate better forecasting of demand, ultimately leading to more informed purchasing decisions. Some popular inventory management software options include Zoho Inventory, TradeGecko, and Cin7. They offer a range of features tailored to different business sizes and needs.
Barcode and RFID Technology
Incorporating barcode and RFID technology into material inventory management can lead to increased efficiency and accuracy. Barcodes provide a straightforward method for tracking products. Scanning items upon receipt or dispatch ensures accurate data entry, streamlining the inventory process. Furthermore, the ability to automate data capture minimizes manual labor and reduces errors significantly.
RFID (Radio Frequency Identification) takes this a step further, enabling businesses to track inventory without needing a direct line of sight. This technology can improve real-time visibility of stock and enhance security measures against theft or loss. However, implementing RFID systems can be more costly than barcodes. Therefore, it is essential to assess the specific needs of the business before investing in this technology.
Cloud-Based Solutions
Cloud-based solutions for inventory management offer businesses flexibility and accessibility. Unlike traditional software that necessitates on-premise installations, cloud systems allow users to access data from anywhere with an internet connection. This is particularly valuable for businesses operating across multiple locations.
One major benefit of cloud inventory management is that it often includes automatic updates, ensuring businesses are using the latest technology without incurring additional costs. Moreover, these solutions typically offer enhanced scalability. As a business grows, the cloud system can expand seamlessly to accommodate increasing inventory needs without extensive hardware investments.
However, companies must evaluate the reliability and security of potential cloud providers. Data breaches can lead to significant repercussions and, therefore, choosing a reputable provider is crucial. Considerations might include reviewing compliance with data protection regulations and assessing service level agreements (SLAs).
Using the right technology and tools can significantly enhance the effectiveness of inventory management practices.

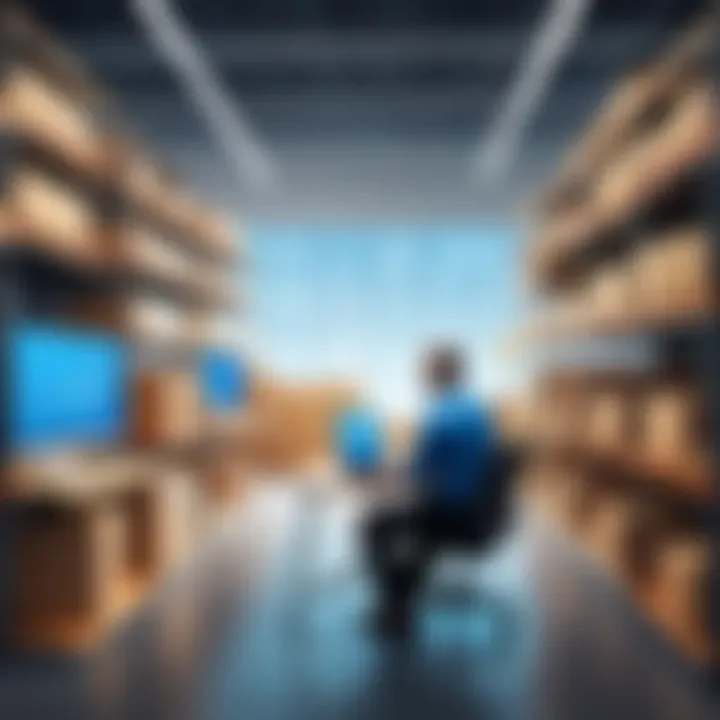
In summary, employing suitable technology and tools is indispensable for effective material inventory management. With proper software, advanced tracking solutions, and cloud systems, businesses can achieve a level of efficiency that positions them well in competitive markets.
Key Performance Indicators (KPIs) for Inventory Management
Key Performance Indicators (KPIs) serve as essential metrics in inventory management. They provide critical insights into the effectiveness and efficiency of inventory processes. Assessing KPIs enables decision-makers to pinpoint areas needing improvement, thus facilitating informed choices that lead to enhanced operational performance.
Understanding these indicators is vital. For instance, KPIs reveal the relationship between maintaining adequate stock levels and minimizing costs. This balance is crucial for any business aiming to maintain competitiveness. KPIs can highlight trends over time, show how resources are allocated, and impact overall profitability. Every organization should carefully align its KPIs with its broader business goals to maximize their utility.
Some benefits of utilizing KPIs include:
- Improved decision-making: By analyzing data, companies can make educated choices regarding purchasing, production, and sales.
- Enhanced operational efficiency: Regular monitoring fosters process improvements and resource optimization.
- Increased customer satisfaction: Meeting demand effectively reduces stockouts, ensuring customers receive their products on time.
However, it is essential to consider which KPIs are most relevant to the specific business model. Different organizations may prioritize different measurements based on their unique goals and challenges.
"The right KPIs transform data into actionable insights, leading organizations toward sustained success."
Inventory Turnover Ratio
The Inventory Turnover Ratio is an important measure of how often a business sells and replaces its stock within a specific period. It is calculated by dividing the cost of goods sold by the average inventory for the same period. A high turnover ratio indicates efficient inventory management, suggesting products are selling well. Conversely, a low ratio could point to overstocking or poor sales performance.
- Formula:
Inventory Turnover Ratio = Cost of Goods Sold / Average Inventory
Maintaining an optimal turnover ratio is crucial for liquidity and to minimize holding costs. Low turnover may lead to excess inventory, increasing storage costs and possible obsolescence. Therefore, regularly reviewing this KPI is advisable to identify trends and areas for efficiency improvement.
Stockout Rate
The Stockout Rate indicates how often items are out of stock when customers demand them. A high stockout rate can harm customer satisfaction and ultimately affect business reputation and revenue. It’s essential for businesses to measure and analyze this rate regularly.
- Why it matters: A persistent stockout can signal inadequate inventory levels or supply chain challenges. Reducing the stockout rate improves customer retention and reduces the likelihood of lost sales.
Companies can benefit from setting clear benchmarks for acceptable stockout levels based on historical sales data. Implementing effective inventory management practices can help mitigate this issue.
Carrying Cost of Inventory
The Carrying Cost of Inventory encapsulates all expenses associated with storing unsold goods. These costs include warehousing, insurance, taxes, spoilage, and opportunity costs. A high carrying cost can negatively impact net profitability.
Understanding these costs is vital not only for pricing strategies but also for optimizing inventory levels. To reduce carrying costs, businesses should regularly assess their inventory and adopt strategies like demand forecasting and Just-in-Time methodologies.
- Components of carrying costs:
- Storage costs
- Insurance costs
- Depreciation costs
- Ordering costs
- Opportunity costs
By carefully analyzing the carrying cost, companies can make adjustments to their inventory policies that enhance overall financial health.
In summary, KPIs are invaluable for managing material inventory effectively. By focusing on specific metrics like Inventory Turnover Ratio, Stockout Rate, and Carrying Cost of Inventory, businesses can establish a robust inventory management system that drives growth and efficiency.
End
Material inventory management is a crucial aspect of any business operation. Effective management improves not only cost efficiency but also enhances the ability to meet customer demands. It ensures that resources are available when needed, which ultimately leads to increased satisfaction and longer-term client relationships.
Summarizing Best Practices
To implement successful material inventory management, organizations should adopt several best practices:
- Regular Inventory Audits: Inventory checks should be performed frequently. Regular audits help identify discrepancies and address them accordingly.
- Forecasting Demand: Use historical data to anticipate future needs. Accurate forecasts help in maintaining optimal stock levels and minimize waste.
- Adoption of Technology: Utilizing tools such as inventory management software can streamline processes and improve accuracy. This technology minimizes human error and enhances tracking capabilities.
"Organizations that apply consistent best practices in inventory management achieve better efficiency, which translates to reduced costs and improved service delivery."
- Supplier Relationship Management: Having strong relationships with suppliers can aid in better terms and responsiveness to changes in demand.
- Employee Training: Staff should be well-trained in inventory processes and systems to enhance operational efficiency.
Future Directions in Inventory Management
The landscape of material inventory management continues to evolve. Emerging trends show that several areas will become increasingly important:
- Data Analytics: Access to real-time data will allow businesses to make informed decisions quickly and efficiently.
- Artificial Intelligence: AI can predict inventory needs with greater accuracy and help in automating reorders.
- Sustainability Practices: More businesses are adopting sustainable practices that focus on reducing waste in inventory management. This shift is crucial not only for cost savings but also for compliance with evolving regulations.
Investing in future technologies and methodologies will likely lead to enhanced management practices that benefit both the organization and its customers. The understanding of how inventory works and how to optimize it will remain key in the coming years.