Plex Manufacturing Processes and Applications Analysis
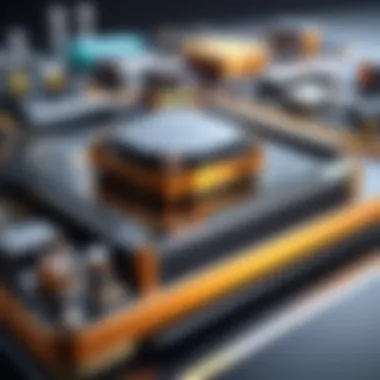
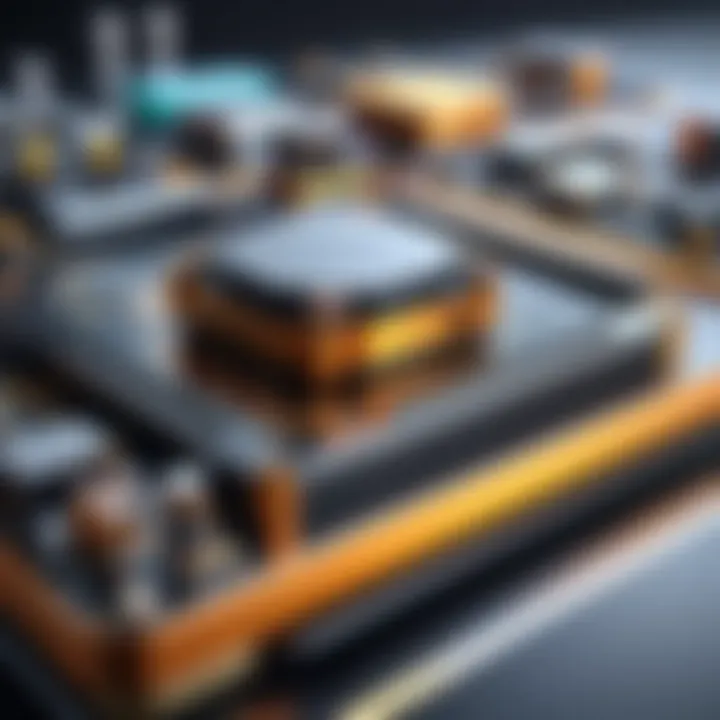
Intro
Plex manufacturing represents a unique niche within the broader landscape of industrial processes. This sector is vital for various applications, including consumer goods, industrial equipment, and architectural designs. Understanding plex manufacturing requires a thorough examination of its components, processes, and emerging trends that define the industry.
This article intends to explore these facets in depth. We will analyze the materials used, the technologies implemented, and the evolving market dynamics that influence decision-making. Each section will delve into the specifics, providing a comprehensive overview designed for industry professionals and decision-makers alike. Importantly, the aim is to present this information in a manner that informs strategic thinking and operational effectiveness.
Software Category Overview
Definition and Importance
Plex manufacturing often relies on advanced software systems to streamline operations. These software solutions encompass various functionalities including inventory management, production tracking, quality assurance, and supply chain integration. Their importance cannot be overstated; they enhance efficiency, reduce wastage, and ultimately contribute to improved bottom lines.
Key Characteristics
The software used in plex manufacturing typically exhibits several defining characteristics:
- Integration: Modern applications must connect seamlessly with existing systems and processes.
- Real-time analytics: These tools provide current data, allowing for timely decision-making.
- Scalability: As businesses grow, their systems must adapt and grow with them.
- User-friendly interfaces: To enable operators at all levels to utilize the software effectively.
Comparative Analysis of Top Software Options
Feature Comparison
Understanding the various software options available in the market is crucial. Each platform offers unique features tailored to specific needs in the plex manufacturing workflow. For instance, some solutions emphasize robust data analytics, while others prioritize supply chain management. Here is a brief overview of notable systems:
- Plex Systems: Known for its comprehensive manufacturing solutions, which include real-time tracking and quality management.
- SAP Manufacturing: Offers extensive functionality for larger operations, particularly in supply chain integration.
- Oracle NetSuite: Focuses on flexibility and scalability, catering to diverse business models.
Pricing Models
When evaluating software options, understanding the pricing models is important. Many suppliers provide subscription-based pricing, which can enhance affordability. The comparison of pricing structures can be summarized as follows:
- Tiered pricing: Different plans based on functionalities and user licenses.
- Usage-based pricing: Costs vary based on the level of features utilized or user access.
- Flat-rate pricing: A single fee for comprehensive access to all features.
Understanding Plex Manufacturing
Plex manufacturing is a crucial domain that integrates modern techniques with traditional materials. By understanding this field, professionals can streamline production processes, enhance product quality, and adapt to market fluctuations. It's important to explore several factors that contribute to efficiency and innovation.
Definition and Scope
Plex manufacturing refers to the utilization of several polymers like polycarbonate, polypropylene, and acrylic in various production methods. This includes techniques such as injection molding, thermoforming, and extrusion. Each method offers distinct advantages depending on the material used and the final application of the product. Defining the scope of plex manufacturing is essential as it also encompasses aspects such as automation, quality control, and emerging market trends.
The definition links tightly with the scope as it outlines the boundaries and capacities of this industrial branch. Decision-makers benefit from understanding the specific functions and characteristics that different materials and manufacturing processes provide.
Historical Context
The historical evolution of plex manufacturing has been driven by technological advancement and the demand for versatile materials. Initially, the industry started with simple processes and limited material types. As industry needs became more complex, advances in polymer chemistry and machinery led to the development of various manufacturing techniques.
In the mid-20th century, industries began to embrace more sophisticated methods of production with the integration of automation. Robotics and Computer Numerical Control (CNC) systems revolutionized efficiency, allowing for more precise work and reduced production times. Understanding this history allows businesses to appreciate the current landscape and anticipate future developments. Historical context lays the groundwork for analyzing current innovations and strategies within plex manufacturing.
"Understanding the historical context is essential for leveraging the advancements within plex manufacturing to ensure future success."
Recognizing these foundational aspects can provide insights that are useful for navigating the complexities of the current market.
Key Materials in Plex Manufacturing
In plex manufacturing, the selection of materials is foundational to the quality, durability, and functionality of the final products. Understanding the key materials used can significantly impact production methods, cost efficiency, and application suitability. Different materials offer unique properties that influence decision-making in product design, environmental considerations, and manufacturing processes. Here, we will explore the types of plex materials, along with their properties and criteria for selection.
Types of Plex Materials
Polycarbonate
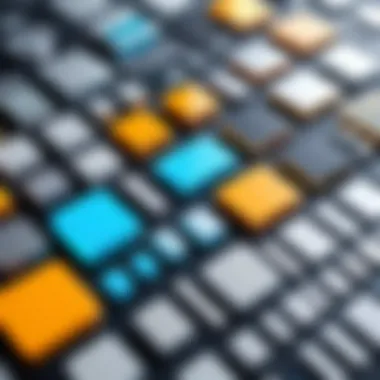
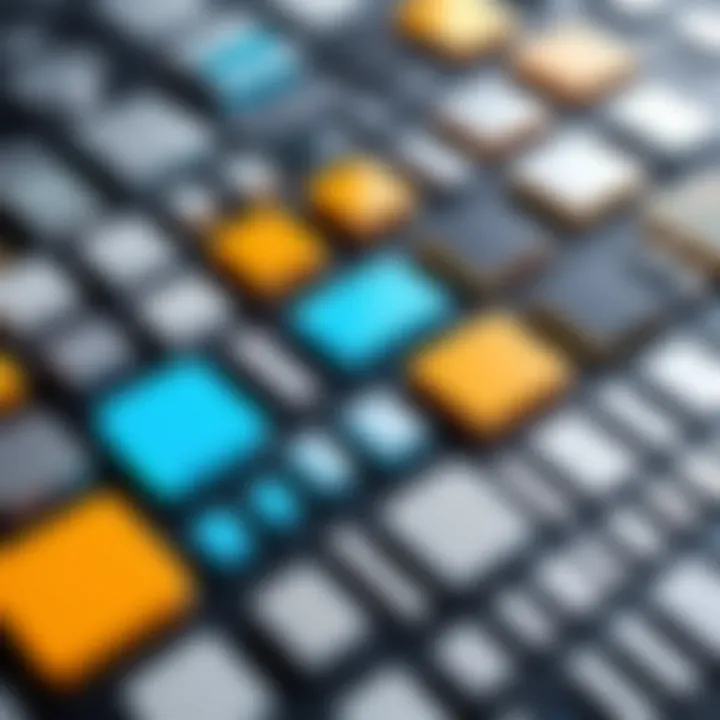
Polycarbonate is a high-performance thermoplastic that is known for its exceptional toughness and impact resistance. It is a lightweight material that provides clarity comparable to glass, which makes it an attractive choice for applications needing visibility and durability. Its durability also enables it to withstand extreme temperatures and weather conditions, making it suitable for outdoor use.
A key characteristic of polycarbonate is its ability to resist high impact without breaking. For industries that prioritize safety and resilience, this property is particularly beneficial. However, polycarbonate can be prone to scratching unless treated, so careful consideration is needed when choosing surface finishes for applications requiring high optical clarity.
Polypropylene
Polypropylene is another major player in plex manufacturing, valued for its chemical resistance and lightweight nature. This material is often used in packaging, automotive components, and medical devices. Its low density allows for cost-effective shipping and handling, contributing to improved logistics.
A prominent feature of polypropylene is its versatility; it can be molded into various shapes and sizes. This adaptability makes it a popular choice in diverse applications. However, polypropylene may have lower structural integrity compared to other materials, and this could limit its use in more demanding settings.
Acrylic
Acrylic, also known as polymethyl methacrylate, is known for its glass-like transparency and lower weight than glass. It is commonly used in displays, signage, and protective barriers due to its aesthetic appeal and clarity. Acrylic can be easily formed and can take on intricate designs, making it a favored choice for creative applications.
One of the unique advantages of acrylic is its ability to be easily fabricated and manufactured, which means niche applications can be explored more freely. Yet, it is more susceptible to UV degradation than polycarbonate, so applications involving direct sunlight might require additional coatings for protection.
Material Properties and Selection Criteria
Material selection in plex manufacturing must consider factors such as mechanical properties, thermal stability, and environmental impact. When choosing materials, decision-makers often evaluate:
- Durability: Resistance to wear, impact, and environmental conditions.
- Cost: Budget implications for sourcing and processing.
- Aesthetics: Visual appeal and clarity requirements.
- Manufacturability: Ease of shaping and forming the material.
- Sustainability: Recyclability and environmental footprint.
These attributes guide the choices made by manufacturers and affect product outcomes in significant ways. Selecting the right material can enhance product life cycle while ensuring compliance with industry standards and user expectations.
Manufacturing Processes
Manufacturing processes are a cornerstone of plex manufacturing. They define how raw materials are transformed into finished products. Each method involves various techniques, equipment, and technologies that are essential for achieving efficiency and quality. Understanding these processes is vital for decision-makers and entrepreneurs as they directly influence production costs, product performance, and time to market.
The significance of manufacturing processes in this sector cannot be overstated. They are critical to optimizing workflows, ensuring quality control, and adapting to market demands. The choice of manufacturing method affects the physical properties of the final products, including dimensional accuracy and surface finish.
Injection Molding
Injection molding is one of the most commonly used methods in plex manufacturing. This method involves injecting molten material into a mold to create specific shapes. It is versatile and suitable for producing complex parts with high precision. Additionally, it allows for mass production, making it efficient for large-scale operations.
The primary advantage of injection molding includes:
- High Efficiency: Short cycle times help in maximizing output.
- Complex Geometries: Capable of producing intricate designs.
- Material Variety: Compatible with several thermoplastics, including acrylics and polycarbonate.
However, there are considerations to take into account, including the high initial cost of molds and the requirement for skilled operators to manage the machinery effectively.
Thermoforming Techniques
Thermoforming is another critical process in plex manufacturing. This technique involves heating a plastic sheet until it becomes pliable and then forming it over a mold. These molds can be simple or complex, allowing for a broad range of product shapes and sizes.
Notable benefits of thermoforming include:
- Lower Tooling Costs: Compared to injection molding, the mold costs are lower, making it feasible for shorter production runs.
- Design Flexibility: Offers greater freedom in terms of design modifications.
- Quick Turnaround: Faster setup times lead to production speed.
Thermoforming is particularly effective for applications such as packaging, automotive parts, and consumer goods. Nonetheless, thickness variations and cooling have to be managed carefully to maintain product quality.
Extrusion Methods
Extrusion methods involve forcing material through a die to create long shapes, such as sheets, tubes, or profiles. This method is especially effective for continuous production, as it allows for consistent shapes in long runs.
The advantages of extrusion include:
- Uniformity: Produces consistent cross-sections.
- Material Efficiency: Minimizes waste by utilizing almost the entire feed material.
- Versatility: Works with a range of materials, suitable for both rigid and flexible products.
Despite its benefits, extrusion may be limited in producing complex shapes and often requires further processing to achieve desired finishes. It is crucial to select the right type of extrusion for the specific application to ensure product integrity and performance.
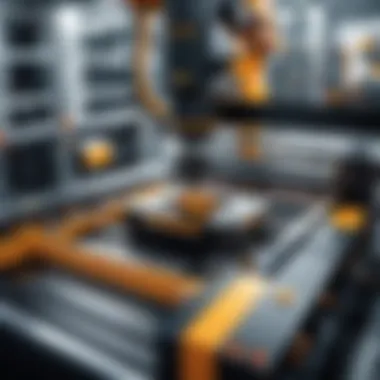
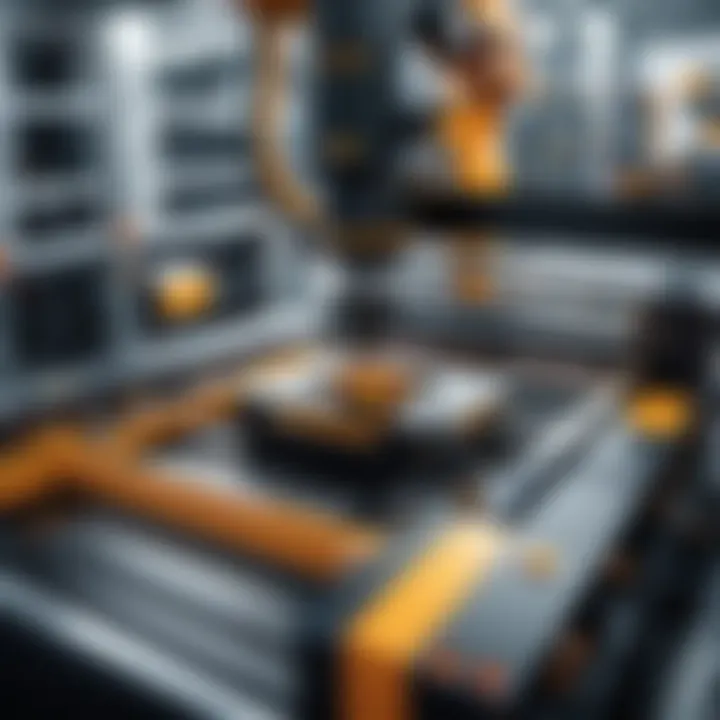
Overall, understanding these manufacturing processes is crucial for strategic planning within the plex manufacturing industry. Each method carries its own set of strengths, weaknesses, and optimal applications, and recognizing these can lead to better decision-making for both new ventures and established businesses.
Automation in Plex Manufacturing
Automation in the realm of plex manufacturing marks a significant shift in operational efficiency and productivity. The integration of automated systems is essential for modern manufacturing processes which demand precision, speed, and consistency. The implementation of automation not only enhances manufacturing capabilities but also reduces the margin for human error, leading to improved quality in production outputs.
Automation encompasses various technologies including robotics, sensors, and advanced software systems that collaboratively work to streamline manufacturing processes. As the industry evolves, these technologies play increasingly pivotal roles, thereby reshaping how manufacturers approach production decisions.
Role of Robotics
Robotic systems are at the forefront of automation in plex manufacturing. These advanced machines can perform repetitive tasks with high accuracy, which is often challenging for human workers. Integrating robotics into the manufacturing process facilitates several key benefits.
- Increased Efficiency: Robotic systems can operate continuously without breaks, leading to significantly higher productivity levels.
- Cost Reduction: Initial investment may seem substantial, but the long-term savings from reduced labor costs and increased output are noteworthy.
- Precision: Robots can achieve more precise cuts and assembly, essential for maintaining the integrity of plex materials.
Moreover, robotics allows for flexibility in production lines. If a new product needs to be manufactured, reprogramming robots can be more efficient than retraining human employees.
Computer Numerical Control (CNC)
Computer Numerical Control (CNC) represents another vital segment of automation in plex manufacturing. CNC machines are controlled via computer programming, allowing for a high level of precision in cutting and shaping materials. The benefits of CNC in plex manufacturing include:
- Customization: CNC technology can easily switch between different designs, accommodating unique customer requests effectively.
- Consistency: Repeated tasks yield identical products, which minimizes variability and meets strict quality standards.
- Enhanced Speed: CNC machines operate much faster than manual methods, translating into quicker turnaround times for projects.
"The adoption of CNC technology in manufacturing processes has catapulted efficiency and product quality to new heights."
Quality Control and Assurance
Quality control and assurance are critical components in plex manufacturing. Ensuring the highest quality in products not only enhances customer satisfaction but also ensures compliance with industry standards. A focus on quality helps in minimizing defects and increasing operational efficiency.
The benefits of implementing robust quality control measures include better reliability of products, reduced waste, and improved process optimization. In an industry like plex manufacturing, where precision is paramount, the ability to consistently control and assure quality can differentiate a company from its competitors.
Considerations surrounding quality control begin with the identification of key performance indicators specific to the manufacturing processes. This includes evaluating the strengths and weaknesses of the production lines and regularly reviewing their outcomes.
"Effective quality control techniques can lead to significant cost reductions and enhanced product integrity in manufacturing processes."
To maintain these standards, a comprehensive testing framework must be established.
Testing and Evaluation Methods
Testing methods play a vital role in quality assurance. These methods not only identify defects but also provide insights into how products can be improved. Some common testing techniques in plex manufacturing include:
- Visual Inspection: A baseline method where products are inspected visually for any obvious defects or inconsistencies.
- Mechanical Testing: This includes hardness tests, tensile tests, and impact resistance tests to examine how materials perform under stress.
- Chemical Testing: Substance analysis ensures that the materials comply with safety and quality standards.
Each of these methods provides valuable data that feeds back into the production cycle, allowing for continual improvement. Regular testing ensures that any deviations from quality are identified swiftly.
Compliance Standards
Compliance with industry standards is non-negotiable in plex manufacturing. Standards set by organizations such as the American National Standards Institute (ANSI) or the International Organization for Standardization (ISO) dictate the necessary quality benchmarks that must be met.
Compliance ensures that products are not only safe but also effective for their intended use. It involves adhering to:
- Performance Standards: Products must meet specified performance criteria to function reliably.
- Safety Regulations: Ensuring products are safe for both the manufacturer and the end user is essential.
- Environmental Compliance: Products should also be manufactured in accordance with regulations aimed at protecting the environment.
By following these standards, companies can maintain a competitive edge. A commitment to quality that meets compliance standards fosters trust among consumers, which is invaluable in today's market.
Market Trends in Plex Manufacturing
Understanding market trends in plex manufacturing is crucial for decision-makers and industry professionals. This section delves into the current growth patterns and emerging technologies that are shaping the future of this sector. By examining these elements, organizations can better position themselves to take advantage of opportunities and mitigate risks associated with market fluctuations.
Current Industry Growth
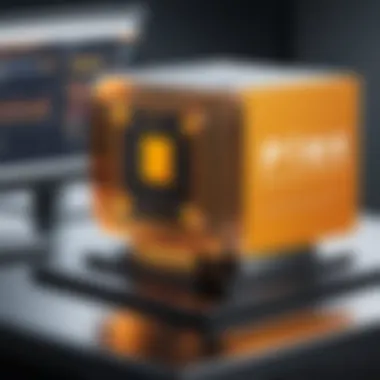
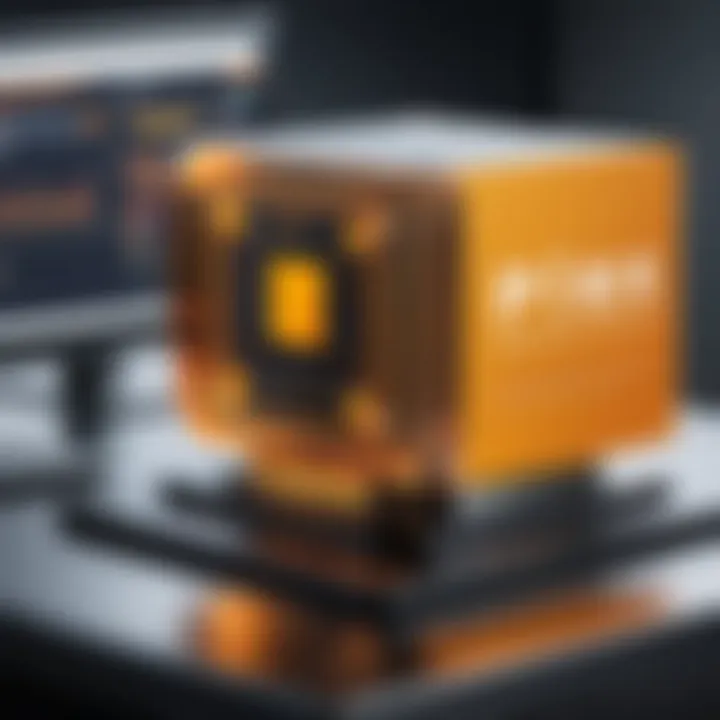
The plex manufacturing industry has witnessed significant growth in recent years. This growth is fueled by increasing demand across various end-use sectors such as automotive, aerospace, consumer goods, and building construction. According to industry reports, the global plex market is projected to expand at a compound annual growth rate (CAGR) of around 4.5% over the next five years.
A few key drivers for this increase include:
- Technological Advances: Innovations in production technologies have enhanced efficiency and reduced costs.
- Economic Recovery: Post-pandemic recoveries have resulted in renewed investments in infrastructure and manufacturing.
- Consumer Preferences: There is a growing inclination toward lightweight and durable materials, which plex products provide.
- Sustainability Concerns: The push for eco-friendly materials has bolstered the demand for recycled plex products.
Thus, the ongoing industry growth signifies a transformative phase for plex manufacturing, with companies needing to adapt swiftly to remain competitive.
Emerging Technologies
Emerging technologies are revolutionizing the way plex materials are produced and utilized. Significant advancements include:
- 3D Printing: This technology is enabling on-demand production of complex components, reducing lead times and waste.
- Smart Manufacturing Systems: Utilizing IoT (Internet of Things) devices for real-time monitoring and control of production processes improves efficiency.
- Advanced Material Research: This research leads to the development of new and improved plex formulations, enhancing performance characteristics such as temperature resistance and transparency.
Overall, these technological developments are not only enhancing product quality but are also paving the way for more sustainable production practices. Companies that adopt these innovations will likely have a competitive edge in an increasingly dynamic market.
Key Takeaway: Staying informed about market trends helps businesses align their strategies with industry changes, ensuring they remain at the forefront of plex manufacturing.
Environmental Concerns
The shift towards sustainable practices in plex manufacturing is increasingly vital. With growing awareness regarding climate change and environmental degradation, addressing the environmental concerns associated with plex manufacturing is not just responsible but imperative. This section delves into key aspects of sustainability and recycling practices within this sector, fostering a healthier balance between industrial advancement and ecological preservation.
Sustainability in Manufacturing Processes
Sustainability is about finding ways that allow plex manufacturing processes to minimize their environmental footprint while maintaining efficiency and productivity. The core principle involves optimizing resource use to ensure that operations do not deplete natural resources or cause unnecessary waste.
- Energy Efficiency: The adoption of energy-efficient machinery can significantly reduce energy consumption during production. Processes that utilize lower temperatures and shorter cycles tend to be more sustainable.
- Raw Material Selection: Sourcing materials that are renewable or recycled can decrease reliance on virgin resources, which is crucial for sustainability. For instance, using recycled acrylics not only conserves raw materials but also reduces energy usage during production.
- Water Conservation: Implementing water conservation measures in manufacturing processes is critical. Techniques such as closed-loop water systems can dramatically minimize waste and ensure efficient use of this vital resource.
In the long run, sustainable practices lead to cost savings and bolster a companyβs image, appealing to environmentally-conscious consumers. It also prepares businesses for stricter regulations that are likely to emerge globally concerning production processes.
Recycling and Waste Management
Recycling in plex manufacturing is a multi-faceted effort that aims to reuse and repurpose materials to reduce waste. It involves several strategies to enhance waste management effectiveness:
- Material Recovery: Advances in technology enable the recovery of materials during manufacturing that would otherwise be discarded. This increases the overall yield from raw inputs.
- Incorporating Recycled Components: Manufacturers can incorporate recycled plex materials into their products, ensuring that waste materials are given a second life. This practice not only helps the environment but also cuts down production costs.
- Waste Diversion Programs: Establishing programs that prioritize recycling and proper disposal of manufacturing waste can play a crucial role in minimizing ecological impacts. Many companies are now integrating waste diversion strategies into their operating procedures.
Adopting comprehensive recycling and waste management strategies allows businesses not only to comply with regulatory standards but also to position themselves as leaders in sustainability within the plex manufacturing industry.
"Incorporating sustainability and recycling into manufacturing isnβt just an option; itβs the future of effective production."
By emphasizing these methods, plex manufacturers can significantly alleviate environmental concerns while meeting the demands of their clientele. Thus, heeding sustainability and recycling not only conserves resources but also enhances overall brand reputation and longevity in the market.
Future Outlook
The future of plex manufacturing is a critical topic for stakeholders who want to remain competitive in this dynamic industry. Understanding the incoming trends, market shifts, and technological advancements will greatly inform strategic planning. Operators and decision-makers must consider a range of factors that could influence long-term business viability.
Forecasts and Predictions
Market analysts predict a steady growth trajectory in plex manufacturing, driven primarily by the increasing demand for lightweight and durable materials across various sectors. Recent reports point to a surge in usage in sectors such as automotive, aerospace, and consumer goods. Based on current data, the global market for plex materials is projected to grow at a compound annual growth rate of around 5% over the next five years.
Key predictive factors include:
- Continued advancements in manufacturing technologies such as 3D printing and CNC machining.
- A rising emphasis on sustainability and eco-friendly manufacturing processes, which will likely reshape material formulations.
- Increased automation level that streamlines operations and enhances quality control measures.
Technological integrations will change operational practices, leading to greater efficiency and reduced environmental impact. As these trends unfold, interest in innovative uses of electronic applications, especially for materials like polycarbonate and acrylic, is likely to expand.
Strategic Recommendations for Businesses
Given the projected direction of the plex manufacturing landscape, businesses must adopt proactive approaches to thrive. Here are some strategic recommendations:
- Invest in Research and Development: Companies should allocate resources to R&D to explore new applications for plex materials. This will help in harnessing the full potential of current innovations.
- Expand Collaboration with Industry Partners: Building partnerships within the industry can lead to shared knowledge and resources. Collaborative efforts can enhance capabilities in recycling technologies or sustainability initiatives.
- Adapt to Market Needs: Businesses must remain agile. This involves closely monitoring market demands and adjusting product offerings accordingly.
"Companies that prioritize adaptability and innovation often have better long-term success rates in dynamic industries like plex manufacturing."
- Enhance Quality Assurance Programs: Implement robust quality control protocols. Focusing on compliance with international standards enhances credibility and attracts clients who prioritize quality.
In summary, the future of plex manufacturing appears promising, but challenges remain. Embracing change and focusing on innovation will be essential for companies aiming to secure their position in this evolving market.