Essential Preventive Maintenance Checklist for Machines
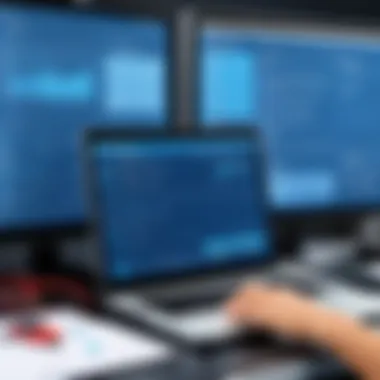
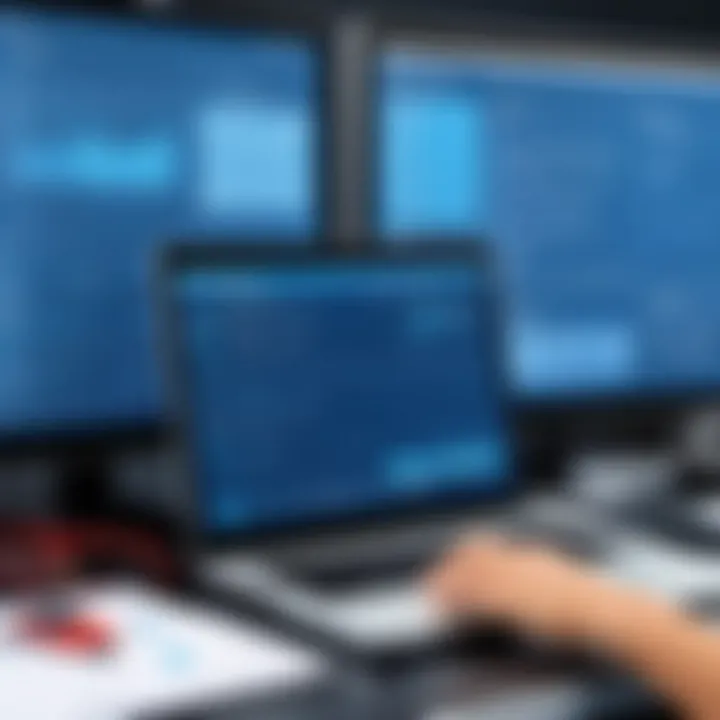
Intro
In our fast-paced industrial environment, the efficiency of machinery plays a vital role in determining an organization's success. A well-structured preventive maintenance checklist can significantly enhance operational reliability. These checklists serve as essential tools, guiding operators and maintenance teams through the essential tasks needed to keep machines functioning at optimal levels. In this article, we dive into the numerous aspects of preventive maintenance checklists, focusing on their importance, creation, and implementation.
Software Category Overview
Definition and Importance
Preventive maintenance software is designed to help organizations streamline their maintenance processes. This type of software not only facilitates scheduling and tracking of maintenance tasks but also assists in planning and prioritizing them. The importance of such software cannot be overstated. It minimizes equipment downtime, extending the lifespan of assets, and ultimately leads to improved productivity.
Key Characteristics
When assessing preventive maintenance software, certain characteristics stand out:
- User-Friendly Interface: Ensures that all team members can easily understand and navigate the software.
- Customizable Checklists: Allows users to create and adapt checklists to meet specific needs and requirements.
- Integration Capabilities: Should seamlessly connect with existing ERP and inventory management systems.
- Reporting Tools: Provides insights and analytics to help decision-makers track performance and capitalize on best practices.
Creating an Effective Preventive Maintenance Checklist
An effective preventive maintenance checklist must be thorough and actionable. It should guide users through daily, weekly, monthly, and annual maintenance tasks, tailored to the machinery in question. Key components often included are:
- Inspection Schedules: Regular checks for wear and tear on essential components.
- Lubrication Requirements: Ensuring that all moving parts remain properly lubricated.
- Safety Checks: An assessment to confirm compliance with safety regulations, protecting personnel and assets alike.
Best Practices for Checklists Implementation
For organizations seeking to implement preventive maintenance checklists successfully, following these best practices can prove beneficial:
- Involve Team Members: Collaborate with those who operate and maintain the machinery.
- Review and Update Regularly: Keep the checklist current by updating it based on latest insights or technological advancements.
- Training and Awareness: Ensure all involved parties are trained to use the checklist effectively.
- Feedback Loop: Establish channels for receiving feedback on the effectiveness of the checklist to iteratively improve.
"An effective preventive maintenance checklist can be the difference between production delays and operational excellence."
Culmination
Preventive maintenance checklists are crucial in enhancing machine reliability and performance. Organizations that prioritize such checklists not only maximize productivity but also create a culture of continuous improvement. By understanding their significance, creating tailored checklists, and implementing them effectively, businesses can ensure they remain competitive in their respective industries.
Understanding Preventive Maintenance
Understanding preventive maintenance is crucial for any organization operating machinery. This approach helps ensure that equipment runs smoothly and efficiently over its lifespan. A well-structured maintenance strategy reduces unexpected breakdowns and consequently minimizes production downtime.
Preventive maintenance involves regularly scheduled checks and services. This differs from simply waiting for a failure to occur. By taking proactive measures, companies can not only extend the life of their machines but also optimize performance. Regular maintenance leads to improved productivity as machines function at their best.
Definition and Importance
Preventive maintenance is defined as a maintenance strategy that aims to prevent equipment failures through routine inspections, adjustments, and replacements. Its importance is evident in various aspects of operational management.
- Cost Efficiency: Investing in preventive maintenance reduces long-term costs. While there are upfront expenses for routine servicing, the savings from reduced repair costs can be significant.
- Increased Equipment Lifespan: Regular maintenance helps avoid major breakdowns. Machines that are well-maintained tend to have a longer operational lifespan.
- Improved Safety: Regular checks help identify and rectify potential hazards before they pose a risk to the workforce.
Overall, preventive maintenance is a cornerstone of efficient operational practices, resulting in a safer and more productive work environment.
Preventive vs. Reactive Maintenance
Preventive maintenance is often compared to reactive maintenance. Understanding the distinction between these two approaches can help businesses make informed decisions about their maintenance strategies.
- Preventive Maintenance: This is planned and scheduled maintenance. It occurs at regular intervals, aiming to address wear and tear before they lead to failure.
- Reactive Maintenance: In contrast, this approach reacts to machine failures after they have occurred. While it may appear cost-effective initially, the long-term implications can include increased downtime and higher repair costs.
Some key differences to note:
- Predictability: Preventive maintenance involves scheduled work, making it easier to plan resources. Reactive maintenance, however, is unpredictable and often rushed.
- Cost Modelling: The costs associated with preventive maintenance are usually more stable and predictable, while reactive maintenance can lead to spikes in costs due to emergency repairs.
- Operational Impact: Preventive maintenance aids in maintaining continuous operation, while reactive maintenance can severely disrupt operations.
In summary, a comprehensive understanding of preventive maintenance will significantly enhance the capability of industries to optimize machine operations. By implementing effective preventive measures, organizations not only save costs but also improve safety and efficiency.
Components of a Preventive Maintenance Checklist
The effectiveness of a preventive maintenance strategy relies heavily on the components of its checklist. A well-structured checklist serves as a foundational tool in ensuring that machines operate efficiently, remain reliable, and adhere to safety regulations. The components should be meticulously crafted to suit each specific machine and its operational context. Each item on the checklist is more than just a task; it signifies a commitment to operational excellence and risk mitigation.
A comprehensive checklist has several critical elements, each contributing distinct advantages to the maintenance process. The key components often include the manufacturer's specifications, operational guidelines, and safety regulations. Understanding these aspects illuminates their importance in crafting an efficient preventive maintenance checklist, ultimately leading to enhanced performance and reduced downtime.
Manufacturer's Specifications
Manufacturer's specifications are crucial when creating any preventive maintenance checklist. These specifications provide specific guidelines from the machine's developer regarding the maintenance and operating parameters tailored to that equipment. This includes frequency recommendations for servicing various components, such as filters, belts, and lubricants, which are integral to the machine's longevity.
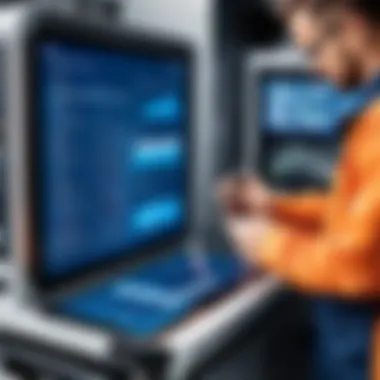
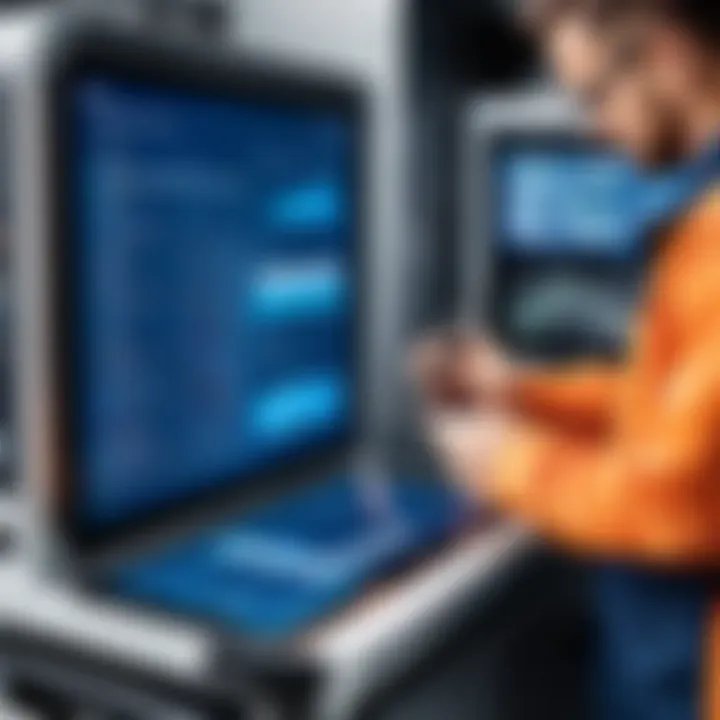
Adhering to these guidelines ensures that machines perform to their maximum capacity, thereby fostering reliability. For instance, failing to follow the manufacturer's recommendations could result in abnormal wear and tear, which might not only reduce lifespan but could also void warranties. Thus, consulting these specifications is essential for maintaining compliance and obtaining optimal functionality.
Operational Guidelines
Operational guidelines supplement the technical specifications by providing context specific to the working environment. These guidelines might encompass daily or weekly checks, such as monitoring fluid levels, examining gauges, and ensuring proper ventilation for machines that operate under certain conditions.
These elements are essential to address the practical realities faced by operators. They guide the workforce on how to interact safely and efficiently with machines. Also, integrating operational guidelines into a preventive maintenance checklist enhances the overall safety culture within organizations, assuring decision-makers that proactive measures are being taken to mitigate potential hazards.
Safety Regulations
Safety regulations are a vital part of any preventive maintenance checklist. These regulations encompass legal and organizational practices aimed at safeguarding personnel and equipment. A checklist that includes safety considerations ensures compliance with industry standards, thereby reducing liability risks.
For example, procedures related to locking out machines during maintenance, wearing appropriate protective gear, and ensuring that safety guards are in place are not just recommendations; they are requirements. A checklist that incorporates these elements signifies a deeper commitment to safety. It demonstrates to employees that their well-being is a priority, which can enhance morale and productivity.
"A thorough preventive maintenance checklist is an investment in both safety and efficiency."
Creating an Effective Checklist
Creating an effective preventive maintenance checklist is crucial for anyone managing machinery within a business. Such a checklist does not only provide structure but also promotes consistency in maintenance tasks. This consistency can lead to better performance efficiencies and lower operating costs. When a checklist is thorough and tailored to specific machines, it becomes a vital tool in reliability engineering, allowing for proactive management of machinery rather than merely reacting to failures.
Identifying Key Maintenance Tasks
The first step in developing your checklist is identifying the key maintenance tasks. Each machine has unique requirements based on its function, design, and manufacturer specifications. Key maintenance tasks may include:
- Lubrication schedules: Regular lubrication is vital for reducing friction and maintaining machine components.
- Routine inspection: Systematic assessments of machine components for wear and tear help forecast potential issues.
- Cleaning protocols: Removing dust and debris not only keeps machines running smoothly but also prevents corrosion and overheating.
It is essential to collaborate with experienced operators and maintenance technicians to ensure that all necessary tasks are captured. This collaboration grounds the checklist in practicality and effectiveness.
Frequency of Maintenance Activities
The frequency of maintenance tasks must be clearly defined in your checklist. A well-structured schedule will prevent both overmaintenance and undermaintenance. Establishing a balance based on:
- Manufacturer recommendations: Follow the intervals suggested by manufacturers for optimal performance.
- Operational data: Analyze historical performance data to adjust frequencies according to actual machine usage.
- Environmental factors: Consider how external factors such as temperature and humidity might necessitate adjustments in maintenance activities.
A properly calibrated frequency ensures machines remain operational, significantly reducing downtime caused by unexpected repairs.
Assigning Responsibilities
Once maintenance tasks and their frequencies are established, clear responsibilities must be assigned. Each task should have a designated individual or team accountable for its completion. Responsibilities can be distributed based on:
- Expertise: Allocate tasks to personnel who are best suited for the job based on training and skill sets.
- Workload balancing: Ensure that tasks do not overwhelm any single employee; fair distribution of tasks fosters accountability and morale.
- Regular feedback: Encourage an environment where personnel can report back on task completion and any further needs identified during maintenance.
Formalizing responsibilities not only keeps maintenance activities on schedule but also fosters a culture of ownership over equipment care.
"An effective checklist streamlines maintenance processes and leads to improved equipment longevity and performance."
In summary, creating an effective preventive maintenance checklist involves careful planning around key tasks, their frequency, and the assignment of responsibilities. By focusing on these elements, organizations can improve machinery reliability, enhance productivity, and ultimately achieve operational excellence.
Common Maintenance Tasks in the Manufacturing Sector
In the realm of manufacturing, common maintenance tasks play a crucial role in ensuring that machinery operates at peak efficiency. A well-structured preventive maintenance checklist significantly reduces unexpected downtimes, which can be detrimental to productivity and profitability. The focus on maintenance tasks such as lubrication, inspection, and calibration not only safeguards equipment longevity but also bolsters workplace safety. Each task addresses potential failures before they escalate, making them essential components of a robust maintenance strategy.
Lubrication Procedures
Lubrication is a foundational aspect of preventive maintenance in manufacturing. Proper lubrication minimizes friction between moving parts, which reduces wear and tear on machinery. Without suitable lubrication, machines can overheat and malfunction, leading to costly repairs and production delays. Regular checks ensure that lubricants are at appropriate levels and that they are suitable for the specific machines being used. The right type of lubricant depends on variables like temperature, workload, and machine type. Implementing scheduled lubrication tasks helps maintain consistent performance and extends the service life of equipment.
Inspection and Cleaning
Routine inspection and cleaning are vital in sustaining equipment efficiency. A thorough inspection can identify signs of wear or potential issues before they lead to system failures. Inspections often cover belts, chains, gears, and other components to check for any abnormalities. Cleaning machinery regularly eliminates dust and debris that may interfere with operations or hinder performance. Keeping machines clean also improves safety by minimizing hazards related to grime or spills. Moreover, a clean machine allows for more accurate inspections, as dirt can mask potential problems that require attention.
Calibration of Equipment
Calibration ensures that equipment operates within specified limits and gives accurate readings. In manufacturing, precision is often paramount. For instance, machines must produce parts that meet stringent tolerances. Calibration checks should be scheduled consistently, and adjustments should be made when deviations from standard measurements are detected. Regular calibration enhances product quality and reduces waste, ultimately saving costs. Additionally, having properly calibrated equipment can enhance safety, as incorrect readings can lead to hazardous working conditions.
"Investing time in routine maintenance tasks is not just a good practice; it’s essential for the operational success of any manufacturing enterprise."
In summary, these common maintenance tasks are integral to a comprehensive maintenance strategy. They not only preserve the functionality and reliability of machines but also contribute to a safer and more efficient workplace. Adopting these practices ensures that manufacturing operations run smoothly and economically.
Industry-Specific Considerations
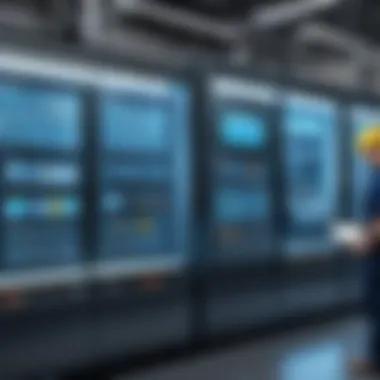
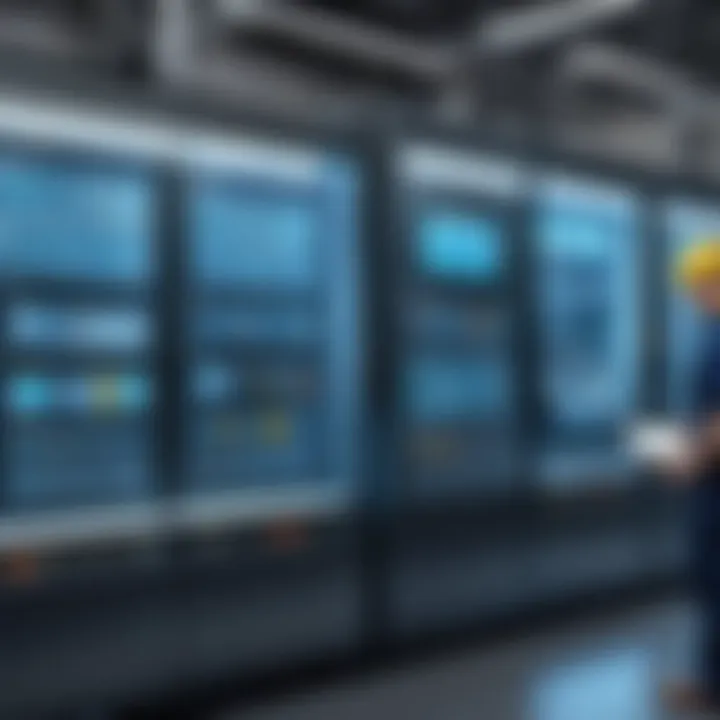
Industry-specific considerations play a crucial role in developing preventive maintenance checklists tailored for different environments. Every sector has unique demands and machinery types, making it essential to address these specific criteria when formulating a checklist. This ensures maintenance strategies are effective and relevant, promoting operational efficiency and minimizing unplanned downtime.
HVAC Systems
The HVAC systems are vital for regulating climate in residential and commercial buildings. A preventive maintenance checklist specifically for HVAC systems includes monitoring components like filters, coils, and fans. Regularly replacing filters is essential not only for system efficiency but also for maintaining air quality. Components that require inspection include thermodynamic controls and electrical connections.
An effective checklist could be structured as follows:
- Inspect filters: Change every one to three months based on usage.
- Clean coils: Ensure both evaporator and condenser coils are free of dirt and debris.
- Check refrigerant levels: Low levels can affect efficiency and increase energy costs.
By acknowledging the unique needs of HVAC systems, companies can prevent system failures and optimize performance, which can lead to significant energy savings over time.
Production Machinery
In the context of production machinery, the checklist must focus on both operational efficiency and product quality. Typical maintenance tasks include lubrication, calibration, and safety checks. Understanding the machinery’s operating environment and specific performance metrics is critical.
Key tasks may include:
- Lubricate moving parts: Reduces wear and tear and minimizes operational friction.
- Inspect and maintain safety devices: Ensures that machinery operates without risks to employees.
- Monitor vibration levels: High vibrations can indicate underlying mechanical issues that require timely attention.
Utilizing industry-specific checklists enhances productivity, extends machinery lifespan, and ensures compliance with safety standards.
Transportation Equipment
The maintenance checklist for transportation equipment such as trucks, forklifts, and conveyor systems requires vigilance to keep operations smooth. Effective preventive maintenance helps in reducing breakdowns and extends asset life.
It is vital to include:
- Regular tire checks: Ensuring tires are inflated to the correct pressure is crucial for safety and fuel efficiency.
- Brake inspections: Critical for operator safety, perform regular checks to avoid failures.
- Fluid levels: Regularly check and replace fluids to maintain vehicle performance.
Tailored checklists facilitate proactive maintenance, preventing delays in transportation and subsequent impact on overall production timelines. By focusing on these industry-specific elements, organizations can foster a culture of safety and maintenance excellence.
Technology in Preventive Maintenance
Technology plays a vital role in enhancing preventive maintenance strategies across various industries. As machines become more complex, the integration of technological solutions has grown in significance. This section will discuss the importance of technology in preventive maintenance, focusing on software solutions, the use of IoT and sensors, and the analysis of data for predictive maintenance.
Software Solutions
Utilizing specialized software is essential for effective preventive maintenance. These programs help streamline maintenance schedules, document tasks performed, and track machinery performance. Field service management software can assist in managing service requests efficiently. Examples include Hippo CMMS and MPulse Software. By ensuring tasks are tailored to each machine's requirements, organizations can reduce the likelihood of errors.
Moreover, these software solutions often feature dashboards that visualize key metrics. This allows decision-makers to monitor the overall performance and health of their machinery in real-time. The improved transparency helps companies allocate resources more effectively.
Utilizing IoT and Sensors
The Internet of Things (IoT) has revolutionized how machines are monitored. By implementing sensors, organizations can collect valuable data regarding machine performance. These sensors can detect various parameters like temperature, vibration, and humidity levels. This information plays a crucial role in predicting machine failures before they occur.
The data gathered does not just assist in maintenance planning but also enables proactive adjustments in operations. For example, predicting a motor's breakdown allows for scheduling maintenance at a time when equipment is least likely to be impactful for the production process. Enhanced visibility into machine health progresses organizations to ensure safety and operational efficiency.
Data Analysis for Predictive Maintenance
Data analysis is another cornerstone of modern preventive maintenance programs. By leveraging advanced analytics, organizations can mine large volumes of data to identify patterns and trends. This helps in understanding when and why machinery is likely to fail, guiding maintenance tasks toward higher priority items.
Using algorithms and machine learning, companies can develop models that predict maintenance needs based on historical data. More accurate predictions reduce both unnecessary downtime and maintenance costs.
"Predictive maintenance extends the life of machines and boosts production."
Adapting to these innovations is no longer an option but a necessary step toward maintaining a competitive edge in an ever-evolving marketplace.
Implementing a Preventive Maintenance Program
Implementing a preventive maintenance program is vital for the successful operation of machines. This aspect enhances not only the longevity of equipment but also the efficiency of production processes. By establishing a structured maintenance plan, organizations can proactively address wear and tear, mitigating potential breakdowns before they occur. A proactive approach reduces unexpected downtime, consequently optimizing productivity.
Training Staff
Training staff is a cornerstone of an effective preventive maintenance program. Workers should understand the significance of the tasks they perform and how they affect machine performance. This involves comprehensive workshops and hands-on training sessions focused on specific equipment. Staff must be educated about the maintenance schedule and the correct procedures for each task. Knowledgeable employees are less likely to overlook crucial steps, which can prevent minor issues from escalating into critical failures. Investing in training is not just a cost but a strategic advantage that pays dividends in reduced maintenance expenses over time.
Monitoring and Evaluation
Monitoring and evaluation must occur continuously to ensure the preventive maintenance program’s effectiveness. Organizations should gather data on maintenance activities, track equipment performance, and identify patterns that indicate potential problems. This information can be analyzed to determine the effectiveness of the maintenance intervals and make adjustments where necessary. Regular audits help verify that the prescribed tasks are being completed and set the stage for necessary adjustments. Without consistent monitoring, a program can become stagnant, resulting in increased risk of equipment failure.
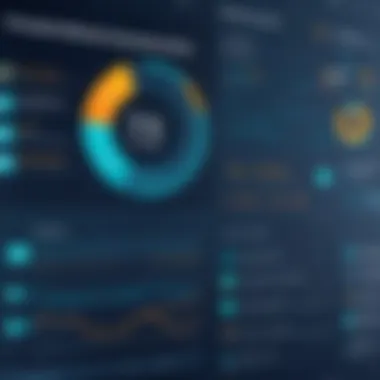
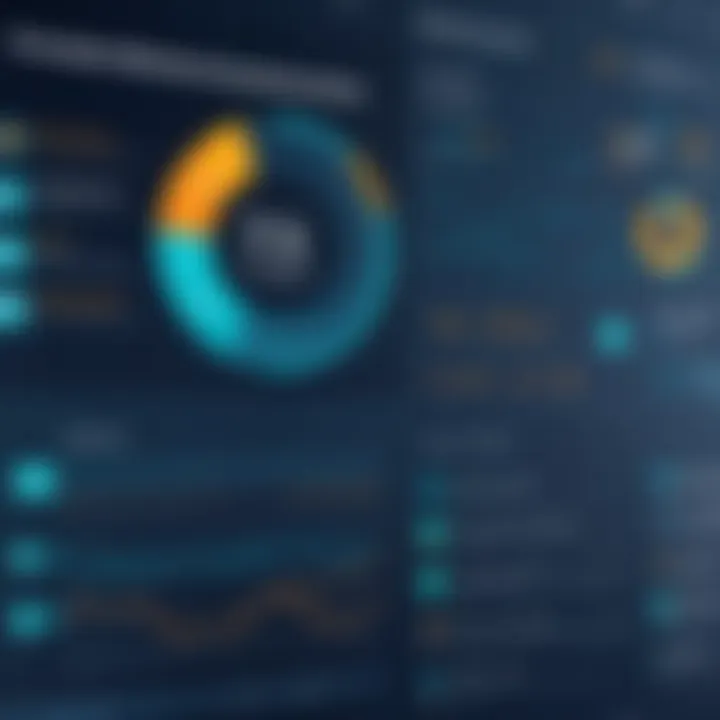
Continuous Improvement
Continuous improvement is an essential principle in implementing a preventive maintenance program. Regularly revisiting the maintenance checklist allows organizations to adapt to changes in operations or equipment. This can involve integrating new technology, incorporating feedback from staff, or reassessing maintenance frequency. Cultivating an environment of improvement promotes innovative thinking among maintenance teams. By valuing feedback and allowing team members to contribute, businesses can streamline their processes and enhance overall reliability.
"The goal of preventive maintenance is to ensure that machines run smoothly and efficiently, preventing costly downtimes and ensuring a safe working environment for staff."
In summary, implementing a preventive maintenance program is a multifaceted process that requires focused training of staff, diligent monitoring, and a commitment to continuous improvement. By prioritizing these elements, businesses can elevate their operational efficiency and reliability.
Challenges in Preventive Maintenance
Preventive maintenance, while critical to operational success, encompasses various challenges that organizations must navigate. Understanding these challenges helps in developing effective strategies to mitigate their impact. Issues such as resource allocation, employee involvement, and proper documentation are paramount. Addressing these can enhance the reliability of machines, reduce downtime, and improve overall productivity.
Resource Allocation
Effective resource allocation is fundamental for a successful preventive maintenance program. This involves not only financial resources but also human capital and time. Companies must invest appropriately in training staff, acquiring tools, and scheduling maintenance tasks without disrupting production. Failure to allocate resources efficiently can lead to unexpected equipment failures and increased repair costs. Moreover, understaffing or misallocation of tasks can result in maintenance activities being overlooked or not performed to required standards.
Getting the right balance is essential. Companies should analyze their existing resources and ensure that maintenance tasks can be consistently performed without jeopardizing other operations. A comprehensive understanding of resource needs is vital in forging a successful preventive maintenance plan.
Employee Buy-In
Securing employee buy-in is another significant challenge. For preventive maintenance strategies to be effective, team members must understand their roles and responsibilities within the program. Resistance to change can hinder progress if workers are not adequately engaged or if they perceive maintenance activities as a burden rather than a benefit.
To cultivate buy-in, organizations can conduct seminars or workshops to explain the importance of preventive maintenance. Employees should see how these practices contribute to their individual safety and to the overall efficiency of the operation. Encouraging feedback and involving team members in the planning can also boost morale and acceptance of preventive maintenance.
Maintaining Documentation
Proper documentation is crucial yet often overlooked. Keeping detailed records of maintenance activities, inspections, and repairs provides a historical perspective that can guide future actions. Incomplete or inconsistent documentation may lead to repetitions of mistakes or skipped maintenance tasks.
Organizations should implement systems that facilitate easy data entry and retrieval. Regular audits of maintenance records can help identify discrepancies and promote accountability. Effective documentation supports compliance with safety regulations and helps demonstrate operational efficiency to stakeholders.
"Documented procedures serve not only as a guide for tasks but also as a useful benchmark for assessing the overall effectiveness of maintenance strategies."
Measuring the Success of Preventive Maintenance
Measuring the success of preventive maintenance is crucial for understanding its effectiveness and impact on operations. It is not just about implementing a checklist but also about evaluating its influence on machine performance and overall business efficiency. A structured approach to measuring can help organizations identify areas for improvement and optimize their maintenance strategies.
Key Performance Indicators
Key Performance Indicators (KPIs) serve as benchmarks to evaluate the performance of preventive maintenance programs. They provide quantitative data that can highlight achievements and areas needing attention. Common KPIs include:
- Downtime Reduction: This assesses the decrease in machine downtime due to effective maintenance practices. Less downtime often translates to higher production output.
- Maintenance Costs: Tracking expenses related to maintenance helps in evaluating if preventive measures are financially sustainable. Comparing these costs against reactive maintenance costs can provide insight into cost savings.
- Work Order Completion Rates: Identifying the percentage of scheduled maintenance tasks completed on time can inform how well the maintenance program is implemented.
- Mean Time Between Failures (MTBF): This metric measures the average time between machine failures, indicating reliability improvements from preventive efforts.
Monitoring these KPIs can effectively communicate the value of maintenance efforts to stakeholders and guide strategic decisions.
Return on Investment Analysis
Return on Investment (ROI) analysis is an integral part of measuring preventive maintenance success. It involves comparing the costs associated with preventive maintenance against the financial returns realized through reduced breakdowns and enhanced productivity. When organizations invest in preventive maintenance, they expect not just to minimize failures, but also to extend equipment life and improve operational efficiency.
To analyze ROI effectively, consider the following:
- Initial Costs: Calculate the upfront costs of establishing a preventive maintenance program, including training and software solutions.
- Savings: Estimate the savings from reduced emergency repairs and shorter downtimes.
- Increased Production: Determine the additional revenue generated from high operational uptime.
- Equipment Lifespan: Evaluate how the program extends the lifespan of machines which factors into long-term savings.
By systematically assessing these elements, businesses can justify their maintenance investments and reinforce the importance of a preventive approach. Integrated effectively, these measures create a framework for continuous improvement in machine reliability and operational productivity.
Future Trends in Preventive Maintenance
The landscape of preventive maintenance is rapidly changing. As industries evolve, the methods and technologies utilized for maintenance are becoming more sophisticated. Understanding these trends is crucial for organizations looking to maintain a competitive edge. The focus on predictive rather than merely preventive methods is becoming essential. This shift allows for more accurate forecasting of maintenance needs and better resource allocation.
Artificial Intelligence and Automation
The integration of Artificial Intelligence (AI) into preventive maintenance practices offers numerous advantages. AI can analyze vast amounts of data and identify patterns that humans might overlook. This capability allows organizations to predict when a machine is likely to fail. Not only can AI enhance decision-making, but it can also automate routine maintenance tasks. Automation minimizes human error and ensures that maintenance is carried out consistently.
- Enhanced Monitoring: AI-powered systems can provide real-time monitoring of machinery, identifying potential issues before they escalate.
- Predictive Analytics: By analyzing historical data, AI helps in predicting future maintenance needs, thus preventing unexpected downtimes.
- Resource Management: Automation allows better allocation of resources. Maintenance tasks can be scheduled during non-peak hours, maximizing operational efficiency.
To implement AI tools effectively, decision-makers must invest in training staff. Employees should understand how to interact with AI systems and interpret their findings. Knowing how to leverage AI maximizes its potential benefits while reducing risks associated with handling complex data.
Sustainability Practices
Sustainability in preventive maintenance is not just a trend; it is a necessity. Businesses are becoming increasingly aware of their environmental impact. Energy-efficient machines and practices are taking center stage.
Implementing sustainable maintenance practices can lead to several benefits:
- Reduced Environmental Impact: By scheduling maintenance when needed, organizations can reduce waste and improve energy efficiency.
- Cost Effectiveness: Sustainable practices often lead to lower operational costs in the long run. Investing in efficient machinery may have higher initial costs but will pay off through energy savings and lower maintenance costs.
- Regulatory Compliance: Many countries are tightening regulations on energy consumption. Adopting sustainable practices ensures compliance, avoiding potential fines.
Investing time in sustainability can improve an organization’s reputation. Customers increasingly favor companies committed to environmentally friendly practices. Thus, sustainability should be a key consideration in any preventive maintenance strategy.
"Integrating AI and sustainability into preventive maintenance is not just about improving efficiency; it’s about ensuring long-term viability in an ever-changing landscape."