Quality Management Applications: Impact and Best Practices
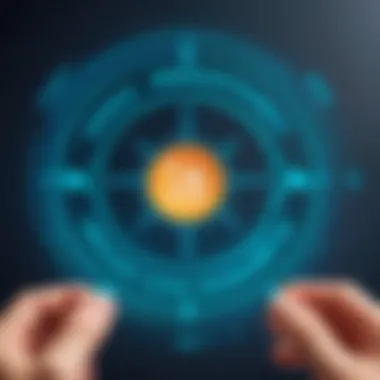
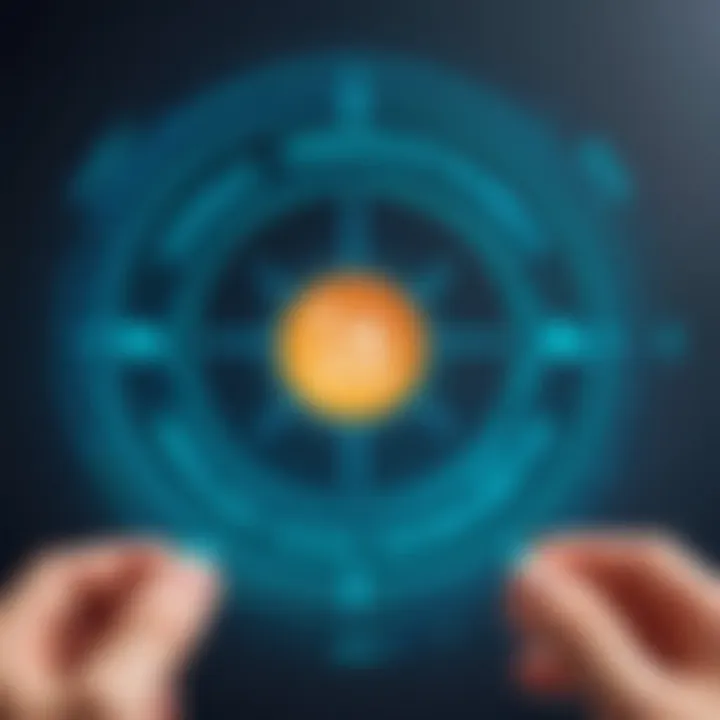
Intro
In today’s fast-paced business landscape, the application of quality management has assumed a pivotal role in ensuring that organizations not only meet but also exceed standards. From manufacturing to service industries, the principles of quality management extend across diverse sectors, forming the backbone of operational success. The selection of robust quality management systems can lead to enhanced product quality, improved customer satisfaction, and ultimately, a significant boost in overall organizational performance.
As companies scramble to differentiate themselves in a saturated marketplace, understanding the intricate details of quality management becomes essential. This exploration emphasizes a thorough dissection of methodologies, tools, and the real-world application of quality management practices, all while facing the unique challenges posed by advancing technologies.
"Quality is never an accident; it is always the result of intelligent effort."
The evolving nature of quality management has also given rise to various digital tools that facilitate the implementation process. Organizations must be acquainted with these tools to navigate their quality assurance journeys effectively and efficiently.
Understanding Quality Management
Understanding quality management is pivotal for organizations striving to enhance their efficiency and customer satisfaction. In today's competitive landscape, where every decision can make or break a business, grasping the nuances of quality management becomes essential. Quality management isn't just about meeting standards; it's about embedding a culture of excellence across all layers of an organization.
Quality management involves a holistic approach to ensuring products or services meet customer expectations and regulatory requirements. The significance of quality management expands beyond mere compliance; it factors into operational efficiency, brand reputation, and ultimately, profitability. A comprehensive understanding of quality management enables decision-makers to identify gaps in processes, mitigate risks, and boost overall performance.
Moreover, understanding the core principles can guide organizations in implementing effective quality management systems tailored to their specific needs. As such, the upcoming subsections will delve deeper into defining quality management, tracing its historical evolution, and exploring its core principles. Each facet provides valuable insights into the framework that shapes quality management practices today.
Defining Quality Management
Quality management refers to the actions and processes that organizations employ to manage and control the quality of their products or services. It encompasses everything from quality planning to quality assurance and quality control. A critical element of quality management is its focus on customer satisfaction—ensuring that offerings not only meet predefined standards but also exceed customer expectations. In this way, quality management adapts and evolves based on consumer insights and feedback, leading to better products and services over time.
Historical Evolution of Quality Management
Tracing the historical path of quality management reveals its transformation from basic inspection processes to a comprehensive approach that emphasizes proactive measures. In the early 20th century, quality control focused largely on inspecting finished products to eliminate defects. Over the years, industry pioneers like W. Edwards Deming and Joseph Juran introduced concepts that shifted perspectives, advocating for quality at every stage of production. This movement paved the way for methodologies like Total Quality Management, which emphasizes continual improvement and involvement from all employees, not just those in production.
As organizations faced globalization and heightened competition, quality management began incorporating more sophisticated tools and frameworks, adapting to the needs of evolving markets. Understanding this history helps illuminate why current quality management practices prioritize proactive over reactive measures.
Core Principles of Quality Management
Quality management rests on several core principles that organizations can leverage to establish a robust quality culture.
Customer Focus
The cornerstone of quality management is customer focus. Organizations must prioritize understanding customer needs and expectations. This principle is often regarded as beneficial because it fosters loyalty and helps companies adjust their offerings based on direct feedback. Unlike a transactional viewpoint, customer focus encourages organizations to deliver exceptional value consistently.
A unique aspect of this principle is its ability to transform data into insights. Organizations frequently gather feedback, yet not all utilize it effectively. Leveraging customer insights can lead to innovative products and services tailored to market demands.
Leadership Commitment
Another fundamental principle is leadership commitment. This aspect emphasizes the role of management in steering the quality agenda. A key characteristic is that proactive leadership fosters an environment where quality initiatives can thrive. When leaders are engaged, it signals the importance of quality throughout the organization, motivating employees at all levels.
The unique advantage of this approach is that it aligns organizational goals with quality imperatives, ensuring that resources are allocated effectively. However, the challenge lies in sustaining this commitment across changing leadership dynamics.
Process Approach
The process approach principle focuses on understanding and managing interrelated processes as a system. This systematic perspective is beneficial because it enhances efficiency—enabling organizations to streamline operations and reduce waste. The key characteristic of this approach is its emphasis on continuous monitoring and analysis of processes to identify improvement opportunities.
This structured view allows organizations to visualize their workflows, fostering a clear understanding of how disruptions can impact overall performance. However, organizations may face difficulties in maintaining consistency across different processes, necessitating robust monitoring systems.
Continuous Improvement
Lastly, continuous improvement is a principle that encourages organizations to regularly assess and enhance their practices. The essence of continuous improvement lies in fostering an agile environment where feedback loops are integral. By embracing small, incremental changes, organizations can adapt more swiftly to market shifts.
A notable feature of this principle is its application of methodologies like Plan-Do-Check-Act (PDCA), which facilitates structured problem-solving. While the commitment to continuous improvement requires sustained effort, its long-term benefits significantly outweigh initial investments by leading to enhanced efficiency and innovation.
Quality Management Frameworks
Quality management frameworks serve as the backbone for structured approaches to managing quality across various sectors. Their importance in enhancing process efficiency and ensuring consistent product quality cannot be overstated. By establishing a systematic approach to quality, organizations can streamline operations, reduce waste, and improve customer satisfaction. Whether you are in manufacturing, healthcare, or any other industry, understanding these frameworks can lead to transformative changes.
In essence, a quality management framework provides a guided pathway—allowing businesses to map out their quality objectives, allocate resources efficiently, and implement necessary adjustments to improve performance. As companies face increasing competition and customer demands, these frameworks become not just beneficial but essential to sustaining growth and resilience in the marketplace.

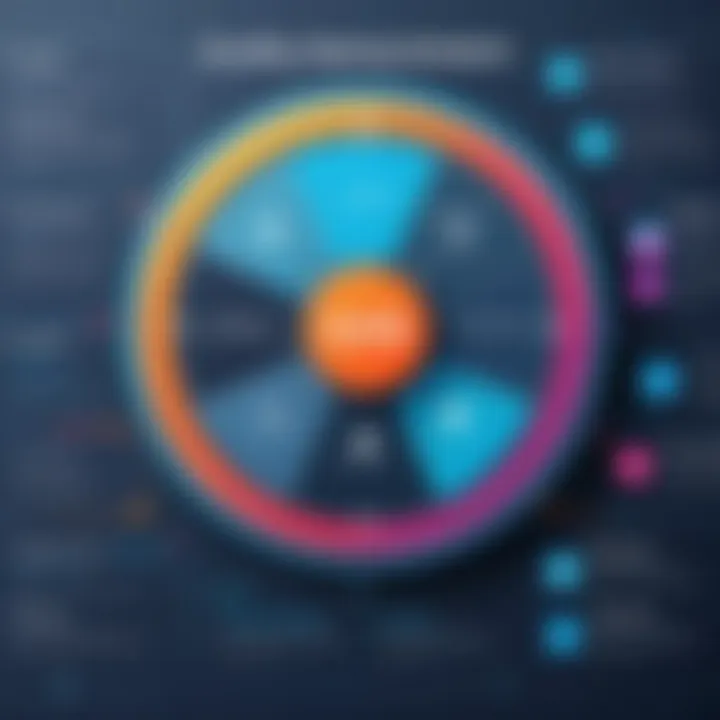
ISO Standards
ISO standards represent an internationally recognized framework for quality management. They lay down guidelines and specifications to ensure that products and services are safe, reliable, and of good quality. For instance, ISO 9001, which focuses on quality management systems, helps organizations implement effective processes that are essential for consistent performance.
Using ISO standards not only aids in achieving operational excellence but can also enhance your organization’s credibility with customers and stakeholders. Moreover, businesses that adhere to these standards often experience better market access, as compliance with ISO guidelines is commonly a prerequisite for entering certain markets.
Total Quality Management
Total Quality Management (TQM) embodies a holistic approach to long-term success through customer satisfaction. It involves every member of an organization—everyone from the top brass down to the frontline workers plays a vital role in enhancing quality. This engaging approach fosters a culture where continuous quality improvement is not just an initiative but a norm.
One critical aspect of TQM is its focus on improving customer experience. By actively seeking feedback and addressing concerns, businesses can pinpoint areas for improvement. In turn, this leads to increased customer loyalty, repeat business, and a stellar reputation. The bottom line is that TQM drives performance by aligning organizational goals with customer needs and expectations.
Lean Management
Lean Management focuses on streamlining processes by minimizing waste while maximizing value. The core idea is simple: eliminate anything that does not add value to the customer. This could be excess inventory, unnecessary steps in a process, or even overproduction. In various industries, this approach has proved invaluable for cutting costs without compromising on quality.
Implementing lean practices involves the use of several proven techniques, such as Value Stream Mapping and the 5S methodology, which stands for Sort, Set in order, Shine, Standardize, and Sustain. These tools can help identify inefficiencies and establish a culture of continuous improvement. The benefits of lean management extend beyond operational efficiency; they ultimately lead to enhanced customer satisfaction by ensuring product availability and quality.
Six Sigma
Six Sigma is a data-driven methodology aimed at reducing defects and improving overall quality. This framework employs statistical tools and methodologies to identify and eliminate causes of errors and variability in processes. The goal is clear; aim for near perfection by minimizing deviation from quality standards.
Key components of Six Sigma include Define, Measure, Analyze, Improve, and Control (DMAIC). By applying this structured methodology, organizations can better understand their processes, make informed decisions based on data, and cultivate a culture that prioritizes quality.
Utilizing Six Sigma can lead to substantial improvements in performance and profitability, making it a strategic tool for organizations seeking to become leaders in competitive marketplaces.
Adopting a quality management framework, whether it is ISO Standards, TQM, Lean Management, or Six Sigma, enables organizations to meet customer requirements rigorously while driving internal efficiency and effectiveness.
Tools and Techniques in Quality Management
In the realm of quality management, the right tools and techniques are akin to a craftsman's tools—each with a specific purpose, and collectively forming the backbone of effective quality assurance. Understanding and implementing these methods can transform how an organization perceives and handles quality. They lend structure to processes, facilitate improvements, and help in deriving insights that can propel an organization towards greater heights. The application of these tools fits seamlessly into various stages of quality management, enabling companies to fine-tune their operations and ensure customer satisfaction remains at the forefront.
Quality Control Tools
Quality control tools are essential in the quest to meet customer expectations and uphold standards throughout the manufacturing, service, or production chain. These tools aid in identifying variations in processes and provide solutions to address them effectively. Let's explore some prominent quality control tools:
Fishbone Diagrams
Fishbone Diagrams, also known as Ishikawa diagrams, are utilized to identify root causes of problems in a structured manner. They resemble a fish's skeleton, where the problem sits at the head and potential causes branch off along the spine. This visual representation makes it easy to dissect issues and discern areas needing attention.
One of the key characteristics of Fishbone Diagrams is their ability to facilitate group brainstorming, bringing together diverse perspectives to unravel the causes of a problem. This collaborative attribute makes it a preferred choice among teams looking for input from varied expertise.
However, while Fishbone Diagrams are effective for detailed analysis, they require proper guidance to avoid becoming overly complicated or unfocused. As such, they demand commitment from the team but yield invaluable insights.
Control Charts
Control Charts serve as a powerful monitoring tool in quality management. They visually display process data over time, allowing teams to evaluate variations and recognize trends. By analyzing these charts, organizations can determine if a process is stable and under control or if there are signals indicating potential issues.
What sets Control Charts apart is their ability to distinguish between common cause variation and special cause variation. This critical understanding allows decision-makers to take informed and timely actions to rectify deviations from the expected outcome. Although they are quite insightful, they come with a learning curve, and incorrect interpretations can lead to misguided decisions.
Pareto Analysis
Pareto Analysis brings the famous 80/20 rule into play—showing how a small number of causes often lead to the majority of problems. Using this tool lets organizations prioritize which issues to address for maximum impact. By focusing on the most significant factors affecting quality, resources can be allocated more efficiently, generating better results with less effort.
Its simplicity is why Pareto Analysis remains a beneficial tool for quality managers. Data-driven insights derived from this approach can lead to high-impact strategic plans. However, it's crucial to remember that without regular updates to data, the analysis might mislead efforts by focusing on outdated or inconsequential issues.
Quality Assurance Processes
Quality assurance processes represent the systematic activities implemented to ensure that quality requirements are met. These processes are foundational in reinforcing the commitment to quality within an organization. Below are some essential quality assurance processes.
Audits
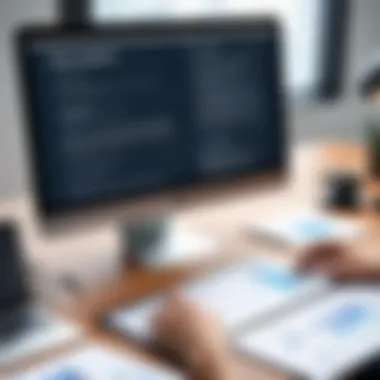
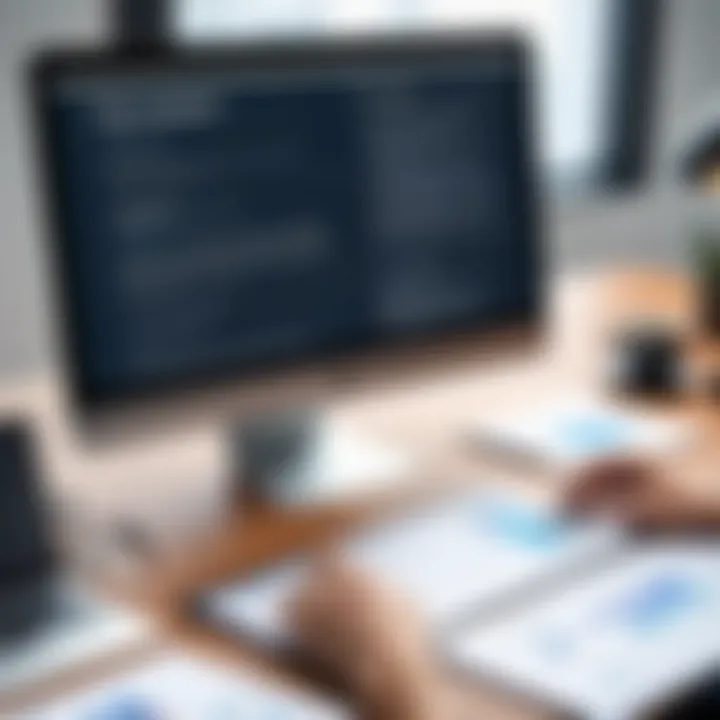
Audits are a keystone in establishing accountability within any quality management system. They provide an objective assessment of whether a quality process is in place and functioning effectively. Regular audits allow organizations to scrutinize their adherence to established quality standards, revealing areas needing rectification or improvement.
The impartial nature of audits marks their significance. They foster transparency, ensuring policies and procedures are being followed, which builds trust within the organization. However, audits may sometimes face resistance from teams fearing scrutiny, and it's vital to communicate their emphasis on improvement rather than punishment.
Inspection Procedures
Inspection Procedures are crucial for ensuring that the products manufactured or services delivered meet predetermined quality criteria. These processes detail the methodology used to examine product attributes, service levels, or process compliance.
One of the pivotal characteristics here is the thoroughness of inspections, which can span from simple random checks to more complex systematic evaluations. A well-structured inspection procedure helps in identifying defects early on. However, a trap organizations might fall into is relying too heavily on inspections instead of fostering quality into the process from the start; thus, integrating a proactive quality philosophy alongside reactive inspections is beneficial.
Documentation Standards
Documentation Standards serve as critical benchmarks in quality management by ensuring that all processes are recorded consistently and coherently. These standards dictate how quality records, assessments, and procedures should be documented to maintain clarity and facilitate review.
Their unique aspect lies in the establishment of a consolidated reference that guides teams in performing tasks consistently. Well-maintained documentation standards can be invaluable, especially during regulatory reviews or internal audits where clarity and compliance are scrutinized. Unfortunately, organizations may face challenges in maintaining documentation integrity, leading to gaps or inconsistencies that could undermine quality efforts.
In summary, employing the right tools and techniques is essential for effective quality management. These methods not only simplify the identification and rectification of issues but also foster a culture of quality across every department.
Application of Quality Management in Different Industries
The application of quality management spans various industries, and it is vital to understand how it unfolds across different environments. Each sector has distinctive processes and customer demands that require tailored quality management systems. When organizations apply quality management principles effectively, they can experience significant benefits, such as improved efficiency, enhanced customer satisfaction, and reduced waste. The relevance of quality management in diverse settings cannot be overstated; it is a foundational element that underpins operational success.
Manufacturing Sector
In the manufacturing sector, quality management is pivotal. It revolves around the quest for precision and reliability in production processes. Effective quality management ensures that products meet established specifications and comply with industry regulations. Organizations often employ strategies like Total Quality Management (TQM) and Lean practices, which emphasize waste reduction and continuous improvement.
By utilizing methodologies such as Six Sigma, manufacturers can identify defects and minimize variability. For instance, a car manufacturing company that adopts Six Sigma may significantly reduce defects in parts, leading to lower costs and higher customer satisfaction. Moreover, the deployment of automation tools for quality monitoring can facilitate timely interventions, thus ensuring a smooth production flow. This sector illustrates how quality management can drive operational excellence while aligning with customer expectations.
Healthcare Industry
The stakes in the healthcare industry could not be higher. Here, quality management plays a crucial role in safeguarding patient health and optimizing clinical outcomes. It’s about delivering not just medical services but exceptional care. Implementation of quality management practices, such as patient safety protocols and rigorous auditing processes, helps healthcare providers maintain high standards.
Hospitals are increasingly adopting the Patient Safety and Quality Improvement Act to create environments that prioritize the well-being of patients. This act promotes transparency and learning from medical errors. For example, a healthcare facility may implement regular training for staff on new procedures, fostering a culture of continuous learning and improvement. By embracing quality management, healthcare organizations enhance patient trust and bolster their reputations in a competitive landscape.
Information Technology
In the fast-paced world of information technology, quality management is essential for delivering robust software and services. IT projects can often veer off track due to scope creep or unclear requirements, making quality management practices vital. Techniques like Agile methodologies and DevOps practices empower teams to ensure that the final product meets or exceeds user expectations through continuous iterations.
Consider a tech startup that employs Agile methodologies. It iterates rapidly on software development while integrating user feedback at every stage. This approach not only enhances product quality but also builds customer loyalty through regular engagement. Additionally, by establishing performance metrics, IT firms can continuously evaluate and refine their processes, ensuring long-term success.
Retail and Service Sectors
The retail and service sectors are primarily about the customer experience. Quality management here translates into understanding customer needs, swift service delivery, and maintaining product quality. Companies often rely on feedback loops, staff training programs, and customer relationship management tools to facilitate high satisfaction rates.
For example, a prominent retail chain may utilize customer surveys to gauge satisfaction levels, while simultaneously investing in staff training programs. This proactive stance on quality management not only improves service delivery but also fosters brand loyalty. In a crowded market, retailers that prioritize quality stand a better chance of retaining customers. The focus on quality management within these sectors demonstrates its direct impact on enhancing customers’ overall experience.
Challenges in Quality Management Implementation
When organizations endeavor to implement a quality management system, they often find themselves navigating a rocky road filled with unexpected hurdles. Understanding these challenges is crucial for the success of quality initiatives. The implications of these challenges stretch far and wide, often affecting the organization's overall performance and customer satisfaction. Sometimes, it feels like trying to catch smoke with your bare hands; the effort is there, but the results can prove elusive.
Resistance to Change
One of the most significant barriers to successful implementation is resistance to change among employees and managers alike. This resistance can manifest for numerous reasons: people naturally cling to familiar processes and might view any change as disruptive. The common refrain, "If it ain't broke, don't fix it!" often echoes in boardrooms.
Addressing resistance starts with clear communication. Organizations must articulate why changes in quality management are essential and visualize the potential benefits. A well-structured change management plan that includes the involvement of employees can ease the transition. Engaging team members from the get-go helps to foster a sense of ownership and accountability toward the new processes. For instance, conducting workshops where employees can voice their apprehensions creates an atmosphere of inclusivity, making them less likely to resist.
Resource Limitations
Another profound hurdle in quality management implementation is resource limitations. Organizations might face tight budgets, insufficient manpower, or lack of technological infrastructure, all of which create constraints on executing quality initiatives effectively. Quality management often demands investment in training personnel, purchasing new software, or even just dedicating time to quality assurance processes. It's a bit like trying to build a house with half a toolbox; trying to make it work while some crucial tools are missing is a recipe for disaster.
When faced with these limitations, companies need to prioritize and strategize effectively. A clear understanding of where quality management aligns with strategic goals can help justify investing necessary resources. Organizations should consider phased implementation, gradually incorporating innovations while ensuring that existing resources are utilized efficiently.
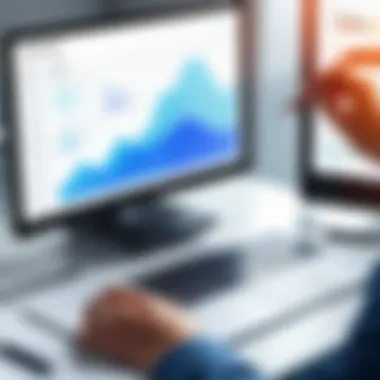

Balancing Quality and Cost
The final, yet critical challenge lies in the balancing act of quality and cost. Striking the right balance is akin to walking a tightrope; a misstep in either direction could jeopardize both quality standards and profit margins. While quality generally improves customer satisfaction and loyalty, it doesn't come without a price. The perception often is that maintaining high quality means incurring higher costs.
Organizations must communicate the value of quality to stakeholders. Understanding that investing in quality can lead to cost savings in the long run—through reduced defects, fewer returns, and heightened customer loyalty—is essential. One approach is to integrate quality management into the existing operations, thus spreading the costs over time rather than having a large, upfront expenditure.
"So, while quality may appear to cost a bit more at first sight, it pays dividends in customer loyalty and operational efficiency."
With these challenges acknowledged, organizations stand a better chance of navigating the often-tricky waters of quality management implementation. Grasping these obstacles, and strategically addressing them, sets the stage for sustainable quality improvements and firm overall performance.
Best Practices for Effective Quality Management
Implementing effective quality management is not just a nice-to-have; it’s a must-do for any organization aiming for success in today’s demanding landscape. By adhering to best practices in quality management, organizations can not only improve product and service quality but also drive operational efficiency. The benefits go beyond compliance and aim at increasing customer satisfaction. This section focuses on key elements that form the backbone of successful quality management systems.
Establishing Clear Metrics
Setting clear, actionable metrics is paramount in navigating the complex terrain of quality management. Metrics serve as a roadmap, guiding organizations towards their quality objectives. Without them, it's like sailing without a compass; one risks drifting into uncharted waters.
- Define Key Performance Indicators (KPIs): Start by identifying what success looks like. KPIs help measure specific outcomes relevant to quality and performance. Typical examples include defect rates, customer complaints, and compliance to regulatory standards.
- Align Metrics with Organizational Goals: It's crucial that the quality metrics are in sync with broader business objectives. This alignment ensures that quality efforts contribute directly to overall organizational success.
- Regularly Review Metrics: Establish a frequency for reviewing these metrics. Things change, and so should the approach to measurement. This practice can uncover new opportunities for improvement or highlight areas requiring immediate attention.
Important Note: Setting metrics is not a one-off exercise. It’s an iterative process. Constantly refining and adjusting them can lead to clearer insights and better outcomes.
Training and Development
Quality management is not just about tools and processes; it’s also about people. Training and development play a vital role in nurturing a workforce capable of maintaining and improving quality standards. Here’s how to approach it:
- Identify Skill Gaps: Conduct assessments to pinpoint where employees may need further training. These gaps could relate to quality tools, processes, or general awareness of quality standards.
- Develop Customized Training Programs: Tailoring training to meet the specific needs of different teams ensures better engagement and retention of information. For instance, while engineers might need hands-on training in process improvement tools, customer service teams may benefit from courses focused on understanding customer feedback.
- Encourage Continuous Learning: Quality management should evolve as workers do. Encourage a culture of learning by providing opportunities for ongoing education. This keeps teams updated on the latest quality practices and innovations.
Training should not be seen simply as a compliance issue, but rather as an investment in the organization’s future.
Fostering a Quality Culture
Creating a culture centered around quality promotes long-lasting change that seeps into every facet of an organization. It’s about more than just hitting numbers; it’s about attitudes and shared values. Here’s how you can instigate such a culture:
- Leadership Buy-In: Leaders should embody the principles of quality management. Their commitment sets the tone for the rest of the organization.
- Incentivize Quality Contributions: Recognize and reward employees who actively contribute to quality improvements. Acknowledging effort fosters engagement and encourages more proactive behavior.
- Encourage Open Communication: Create an environment where employees feel comfortable voicing concerns or suggestions regarding quality. An open-door policy can promote dialogue.
- Celebrate Successes: When quality goals are met or exceeded, take the time to celebrate. This boosts morale and reinforces the importance of quality within the organization.
By nurturing a quality culture, organizations are laying the groundwork for sustained improvements and innovation.
The Future of Quality Management
The world of quality management is rapidly evolving, driven by technological advancements and changing consumer expectations. Understanding the future of this field is vital for organizations aiming to stay competitive in an increasingly complex marketplace. This section examines the critical aspects that will shape quality management moving forward, embracing digital transformation, the role of artificial intelligence and automation, and the essential practices centered around sustainability.
Digital Transformation in Quality Management
In today’s digital age, businesses are increasingly relying on technology to enhance quality management processes. Digital transformation in this context refers to the integration of advanced technologies, such as cloud computing and big data analytics, into quality management systems. This allows for a greater depth of analysis and more effective decision-making.
- Real-Time Monitoring: Organizations can track quality metrics and performance indicators in real time. This responsiveness enables quicker corrective measures and boosts operational efficiency.
- Data-Driven Insights: The analysis of large datasets can reveal hidden patterns and trends, leading to more informed strategies that directly impact product or service quality.
- Enhanced Collaboration: Digital tools facilitate better communication across departments and with external partners. This interconnectedness ensures that everyone is on the same page, fostering a culture of transparency regarding quality initiatives.
In summary, the integration of digital tools transforms traditional quality practices into dynamic systems that can adapt to rapid changes in market demands.
Integration of AI and Automation
Artificial intelligence and automation stand at the forefront of the next wave of quality management. By leveraging these technologies, organizations can streamline operations, reduce human error, and enhance overall effectiveness.
- Predictive Analytics: AI can analyze past data to predict potential quality issues before they arise, allowing preemptive action. This shift from reactive to proactive management is crucial in maintaining superior standards.
- Automation of Routine Tasks: Tasks such as quality inspections and documentation can be automated, freeing up human resources for more strategic interventions. This not only saves time but can also result in higher accuracy rates in quality assessments.
- Improved Customer Experiences: Automated responses and AI-driven suggestions can lead to more personalized interactions and faster resolutions, translating to heightened customer satisfaction.
Adopting AI and automation will likely redefine quality assurance, ensuring that organizations meet and exceed standards efficiently.
Sustainable Quality Management Practices
As businesses become more aware of their environmental impact, the shift towards sustainable quality management practices is essential. Sustainable quality management not only considers economic factors but also prioritizes social and environmental responsibility.
- Life Cycle Thinking: Companies are adopting a holistic approach that evaluates the entire life cycle of a product, from sourcing materials to disposal, ensuring every stage adheres to sustainable practices.
- Resource Efficiency: Focus on minimizing waste and optimizing resource use aligns with broader sustainability goals while also decreasing operational costs.
- Stakeholder Engagement: Including stakeholders in sustainability discussions creates a sense of shared responsibility. This collaboration can lead to innovative solutions that enhance product quality and sustainability efforts.
In the quest for excellence, embracing sustainability will be indispensable, aligning quality management with the growing demand for corporate accountability.
The future of quality management will not just be about meeting standards but rather about thriving in a world that increasingly values ethical practices and innovation.
By embracing digital transformation, integrating AI and automation, and focusing on sustainable practices, organizations can anticipate not just surviving but thriving in a future where quality management continues to be pivotal to success.