Top CMMS Software: Features and Strategies for Success
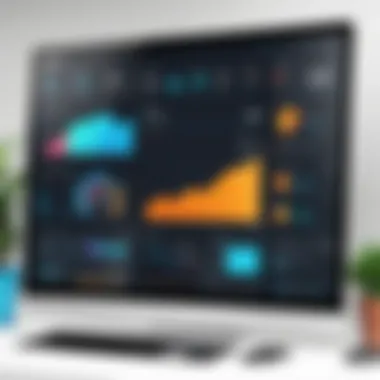
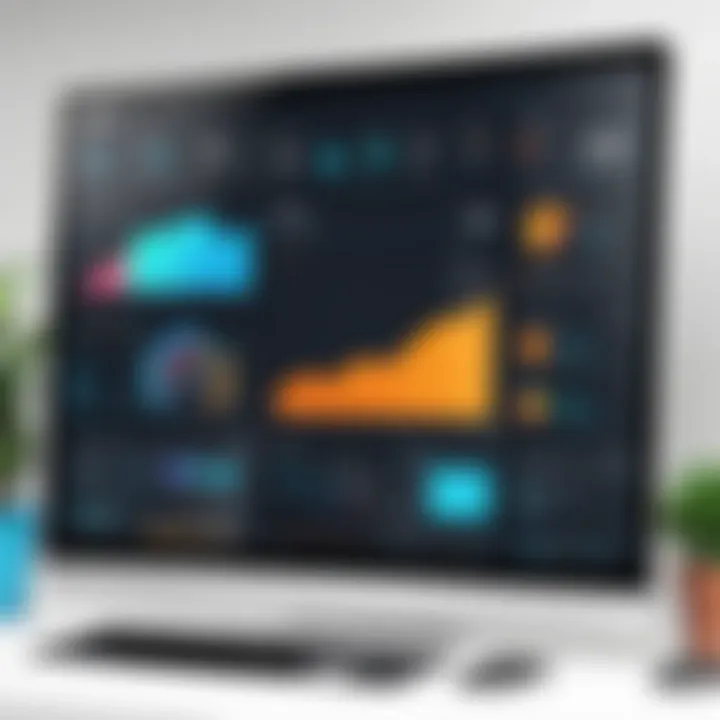
Intro
In today's fast-paced business landscape, the ability to maintain and optimize operations can be the difference between thriving and merely surviving. Computerized Maintenance Management Systems (CMMS) offer a crucial solution for organizations aiming to streamline maintenance processes and improve asset management. The goal of this article is to provide a detailed exploration of the top CMMS software available, examining their features, benefits, and the various strategies organizations can adopt.
Maintenance management isn't just a back-office task anymore; it’s integral to achieving the kind of operational efficiency that turns heads in competitive industries. In fact, the right CMMS can significantly impact productivity, reducing downtime and stretching maintenance budgets further than previously thought possible. This exploration will serve as a roadmap, guiding decision-makers, IT professionals, and entrepreneurs through this intricate landscape.
Software Category Overview
Definition and Importance
At its core, a CMMS is a software solution that assists in managing maintenance operations. This includes scheduling maintenance tasks, tracking work orders, monitoring inventory, and fostering overall asset management. The provision of timely data means that organizations can foresee issues before they escalate, effectively shifting from reactive to proactive maintenance.
In many ways, implementing a CMMS is akin to fitting an organization with state-of-the-art navigational technology; it arms businesses with information essential for steering wisely through the potentially murky waters of mechanical failures and inefficiencies. The importance of such systems cannot be overstated, as they lay the groundwork for smoother operations, reduced operational costs, and increased lifespan of assets.
Key Characteristics
Not all CMMS solutions are cut from the same cloth. Here are some key characteristics to look out for when assessing different options:
- User-Friendly Interface: A straightforward and intuitive design can massively reduce training time and increase user adoption.
- Mobile Compatibility: As the workforce becomes increasingly mobile, the ability to access data on-the-go is essential.
- Customization Options: Different industries have divergent needs, so the flexibility to customize features can be a game-changer.
- Integration Capabilities: The ability to smoothly integrate with other software systems can enhance efficiency. Stakeholders need to ensure that the CMMS can share data with existing ERP or CRM systems.
- Reporting and Analytics: Powerful reporting tools offer insights that can inform management decision-making.
"A CMMS you can’t adapt to your industry won’t get you where you need to go."
Comparative Analysis of Top Software Options
Feature Comparison
When analyzing CMMS solutions, one size certainly doesn’t fit all. Users should consider what core features are non-negotiable for their specific needs. Common features across many leading CMMS products include:
- Work Order Management: Managing and tracking maintenance tasks efficiently.
- Asset Management: Keeping tabs on equipment lifespan, maintenance history, and depreciation.
- Preventive Maintenance: Scheduling routine maintenance to prevent unexpected breakdowns.
- Inventory Management: Monitoring and tracking maintenance supplies and parts.
- Reporting Tools: Generating insightful reports to analyze data over time.
Pricing Models
Understanding the pricing models for different CMMS products is paramount for informed decision-making. Pricing often varies based on:
- Subscription-Based Models: Typically involve monthly or annual fees.
- One-Time License Fees: A more traditional model requiring a single upfront payment.
- Freemium Models: Basic services free of charge, with options to upgrade for more advanced features.
The choice of pricing structure can greatly influence budget allocations and overall financial planning.
In summarizing our findings, it becomes clear that choosing the right CMMS software extends beyond just assessing features and costs. What’s really needed is a careful analysis of how these systems align with organizational goals, much like tuning an engine to ensure it runs at optimum levels. As we delve deeper, we’ll continue to dissect how various CMMS solutions stack up against each other, offering a comprehensive understanding that aids strategic decision-making in a complex technological landscape.
Understanding CMMS Software
Understanding CMMS software is a pivotal component in the operational efficiency of modern businesses. With organizations striving for seamless workflows and effective resource management, grasping the essence of these systems becomes paramount. CMMS, or Computerized Maintenance Management System, is not just another acronym in the toolbox of enterprise solutions; it signifies a transformative approach to managing assets, enhancing productivity, and driving overall business success.
Definition and Purpose
At its core, a CMMS serves as a digital platform that centralizes maintenance management tasks. The fundamental purpose of CMMS is to streamline maintenance operations, which can otherwise be fragmented and chaotic. By leveraging this tool, businesses can schedule maintenance, track assets, and manage work orders all from one user-friendly interface.
There’s more to it than just scheduling. CMMS software can collect valuable data that informs decision-making, helping organizations to preempt issues before they escalate. For instance, if a production line regularly experiences downtime due to faulty machinery, a CMMS can analyze maintenance logs and usage patterns to uncover the root causes. This, in turn, enhances asset longevity and ensures operational continuity. In simple terms, it’s like having a crystal ball for impending technical headaches.
Historical Context
The evolution of CMMS software mirrors the industrial landscape's transformation over the decades. Initially, many companies relied on manual logs and paper trails, which were laborious and often prone to errors. Imagine having to sift through mountains of paperwork just to find a service history of an elevator - tedious doesn’t even cut it.
The dawn of computer technology in the late 20th century introduced the first CMMS solutions. These early systems were basic, often focusing solely on work order management without the comprehensive features we see today. As industries advanced and technology improved, CMMS evolved into more robust systems, incorporating features like predictive maintenance, integrated inventory control, and mobile accessibility.
The journey from paper spreadsheets to sophisticated cloud-based systems shows a clear trend: businesses are recognizing the value of embracing technology, not for the sake of trendiness but as a strategic approach to grow and adapt in a competitive environment.
Knowing this context sets the stage for current innovations and capabilities of CMMS software. As we delve deeper into its significance, features, and future trends, the backbone of this software choice becomes more pronounced, making it a must-have for any organization aiming to keep pace in today’s fast-moving economy.
Importance of CMMS in Modern Business
In today’s fast-paced business environment, Computerized Maintenance Management Systems (CMMS) have emerged as essential tools. They don’t simply help maintain machines; rather, they enhance overall operational efficiency. This section delves into critical aspects that underline the significance of CMMS in modern enterprises.
Efficiency Enhancement
A CMMS can significantly optimize workflow. By automating maintenance tasks, organizations can avert unnecessary downtime. Think about a facility without a proper system: when a machine breaks down, operations halt, leading to lost revenue. With a CMMS, alerts and schedules for preventive maintenance become the norm instead of the exception.
Moreover, real-time data access allows technicians to make informed decisions on immediate repairs. When an issue arises, having historical data can mean the difference between a quick fix and prolonged downtime. By streamlining these processes, businesses can focus on their core activities instead of scrambling to fix problems as they crop up.
"An effective CMMS not only addresses maintenance needs but cultivates a culture of proactive management."
Cost Management
Cost control is always on the radar for decision-makers. A well-implemented CMMS aids in monitoring expenditure on maintenance, parts, and labor. By evaluating these factors closely, companies can identify areas for improvement. For instance, if a particular piece of equipment requires frequent repairs, it may be more cost-effective to replace or upgrade it instead of pouring money into continuous maintenance.
Additionally, CMMS provides a platform for ordering needed parts efficiently. By keeping track of inventory levels, firms can avoid overstock and unnecessary expenditures while ensuring that essential components are always on hand. The savings accrued can be substantial in the long run.
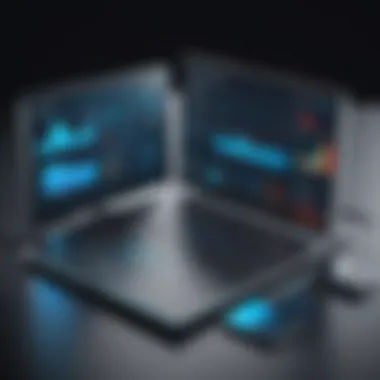
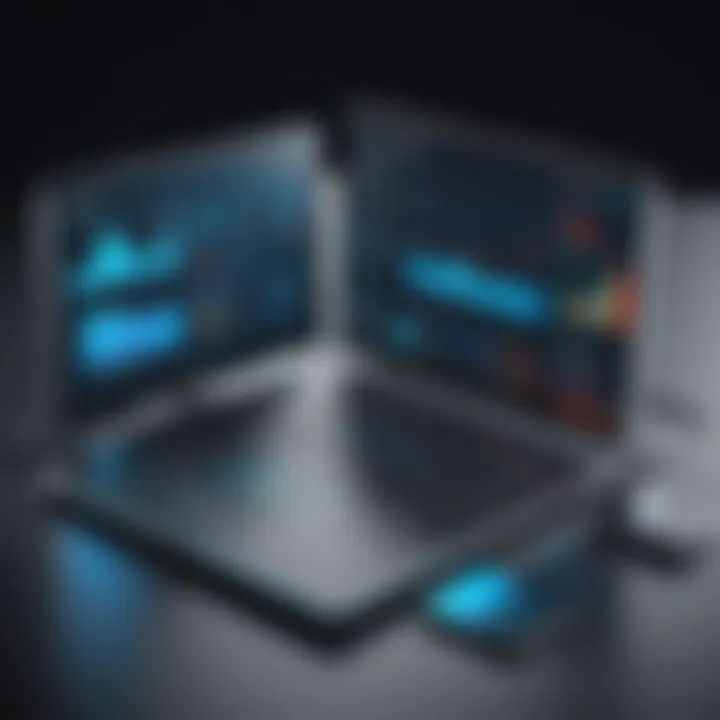
Regulatory Compliance
Regulatory obligations are an often-overlooked aspect of maintenance management. Companies in certain sectors must adhere to strict regulations. A CMMS keeps track of compliance schedules and can generate reports for audits easily. For example, in the pharmaceutical industry, maintaining equipment according to regulatory standards can be the difference between a product passing inspection or receiving a hefty fine.
By maintaining detailed records of maintenance activities, organizations can demonstrate their compliance credibly. This documentation is invaluable during audits or reviews, showcasing a commitment to operational standards and safety.
Key Features of Top CMMS Software
In the vast ocean of Computerized Maintenance Management Systems, certain features stand out as essential for organizations aiming to streamline their maintenance operations and achieve optimal efficiency. The key features of effective CMMS software not only facilitate daily tasks but also align with broader business objectives, enhancing productivity and reducing costs.
Understanding the significance of these features is crucial for decision-makers, IT professionals, and entrepreneurs. Key functionalities such as Asset Management, Work Order Management, Inventory Management, and Reporting and Analytics are integral to a CMMS's value proposition, driving organizations to make informed decisions that suit their distinct operational needs.
Asset Management
Asset management is the backbone of any strong CMMS. It allows organizations to maintain a comprehensive inventory of all assets, including tools, machinery, and equipment. A robust asset management feature provides insights into the condition, location, and lifecycle of each asset. By focusing on journey over tasks, users can foretell when an asset will need maintenance or replacement, making it a proactive approach rather than a reactive one. This foresight leads to reduced downtime and extends the lifespan of equipment.
Moreover, tracking asset performance can facilitate budgetary decisions as organizations can identify underperforming assets that require improvement or replacement. Thus, a clear and organized asset management system not only streamlines operations but can also lead to significant financial savings over time.
Work Order Management
Work order management is pivotal as it governs how tasks are created, assigned, and tracked. A well-structured work order feature ensures that maintenance requests are efficiently handled and completed in a timely manner. Moreover, it allows managers to prioritize tasks based on severity or urgency.
For example, let’s consider a manufacturing facility where equipment failure can halt operations. Here, quick and efficient handling of work orders is essential. A CMMS with effective work order management can facilitate communication between teams, assign responsibilities to specific individuals, and even automate common tasks, making maintenance workflows smoother.
Effective work order management not only addresses immediate maintenance issues but also contributes to long-term operational improvement.
Inventory Management
A critical area that often gets overshadowed is inventory management. A solid CMMS will allow businesses to keep an accurate, real-time view of spare parts and supplies. This is vital for preventing both overstocking and stockouts. The ability to manage inventory levels closely means resources can be allocated efficiently, which directly impacts profitability.
Incorporating features like automatic reordering can help maintain optimal inventory levels. This reduces the chances of running low on crucial parts when they are needed most. With precise inventory tracking, businesses can quickly assess their current stock and plan for future purchases, minimizing any potential disruption to operations.
Reporting and Analytics
Reporting and analytics features empower businesses with data-driven insights for informed decision-making. These functionalities allow organizations to assess performance metrics, track maintenance activities, and analyze cost versus benefit on various maintenance operations. With this data at their fingertips, decision-makers can identify trends, evaluate the effectiveness of maintenance strategies, and make adjustments as necessary.
Having access to a customizable reporting module also proffers a significant advantage. Users can generate reports that focus on the metrics most relevant to their specific organizational goals. This kind of flexibility fosters a culture of continuous improvement and agility.
In summary, the key features of top CMMS software are not just about maintaining machines or assets. They play a larger role in how businesses formulate strategies, manage resources, and implement cost-saving measures. Recognizing the importance of these functionalities can lead any organization to the next level of efficiency and productivity.
Evaluating Different CMMS Solutions
In the world of computerized maintenance management systems, there’s no one-size-fits-all solution. This makes the process of evaluating different CMMS solutions a vital one for any organization seeking to streamline its operations. A careful evaluation not only ensures that you get the right tool for your needs but also helps in maximizing value from your investment.
When diving into this evaluation, aspects like functionality, scalability, and ease of integration become paramount. Each system comes with its unique set of features, and discerning the best match for your operational challenges can mean the difference between success and stagnation. With the right approach, you can systematically sift through options, aligning them with your specific goals.
Vendor Comparisons
When faced with many CMMS options, vendor comparisons serve as a cornerstone for informed decision making. Each vendor typically has its quirk and edge, which can influence the overall effectiveness of your maintenance strategy. A side-by-side examination of vendors will shed light on aspects such as pricing models, sales support, and ongoing service offerings.
Here are a few essential elements to consider:
- Functionality Fit: Does the vendor’s CMMS offer features that specifically address your operational requirements?
- Cost: Take a close look at features included in different pricing tiers. Sometimes vendors have hidden fees that can inflate costs over time.
- Customer Support: Good support is crucial. Check if they offer 24/7 service and if there are extra charges for premium support options.
- User Experience: Is the software intuitive? A cumbersome interface can lead to frustration and deteriorate the intended benefits.
Ultimately, by conducting thorough vendor comparisons, you can avoid pitfalls that arise from ill-fitting systems or misleading vendors, ensuring a smooth operational journey.
User Reviews and Feedback
Listening to the voice of the user offers invaluable insights when evaluating CMMS solutions. User reviews and feedback provide a window into the real-world performance of software. It’s one thing to read about what a product promises to deliver; it’s quite another to hear about the actual experiences from peers.
You can leverage these reviews to gain insight on:
- Performance: Does the software truly deliver on speed and functionality?
- Support: Users often share their experiences regarding the responsiveness of the vendor's support team.
- Usability: The learning curve is a big factor. Feedback can indicate whether real users find the system easy to adapt to their workflows.
Sources like Reddit or software comparison platforms can be treasure troves for nuanced insights. Moreover, integrating peer feedback not only boosts confidence in your choice but can also highlight unique use cases or challenges you may not have considered initially.
By engaging deeply with both vendor comparisons and user feedback, you position yourself to make a more comprehensive and informed decision that aligns well with both current and future organizational needs.
Implementation Strategies for CMMS
When it comes to implementing a Computerized Maintenance Management System (CMMS), the strategy you adopt can determine the difference between a smooth transition and a chaotic rollout. An effective implementation strategy doesn’t just ensure that the software gets installed; it strategically integrates it into your organizational workflow and culture. Understanding this importance is crucial for decision-makers who are ready to enhance their operational efficiency. The following elements are pivotal in shaping a successful CMMS implementation:
- Clarity of Objectives: Establish clear goals for what you hope to achieve with the CMMS. This could range from reducing downtime to streamlining maintenance requests. Without specific objectives, it’s easy to lose sight of what’s important.
- Stakeholder Engagement: Bringing everyone on board is key. Engage with stakeholders at every level, from upper management to maintenance staff. Everyone should understand the value of the new system and be on the same page regarding its usage.
- Change Management: Expect resistance. People tend to stick with what they know. Preparing your team for the changes that CMMS brings will set a gentle pace for the adoption process.
Assessment of Current Processes
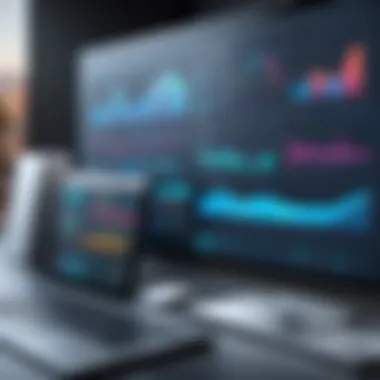
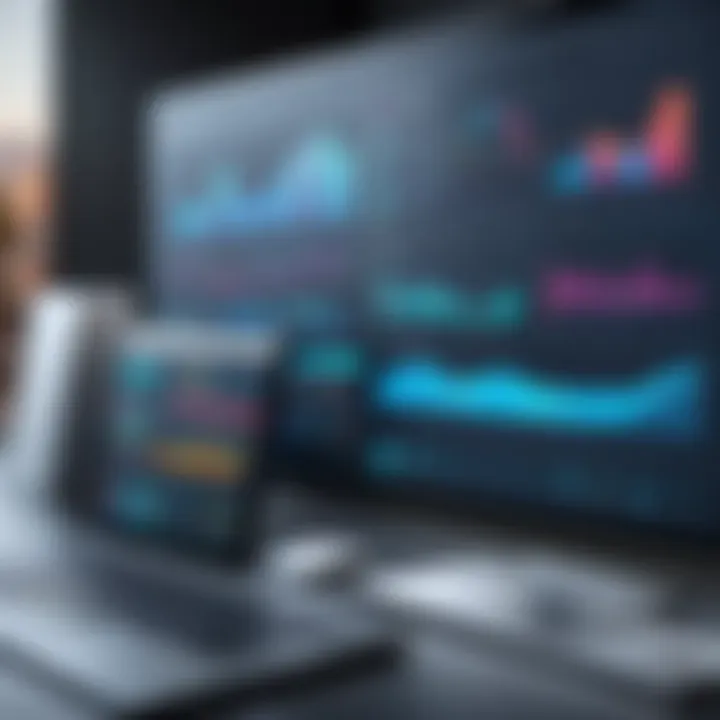
Before diving headfirst into a CMMS implementation, conducting a thorough assessment of current processes is essential. This involves mapping out existing workflows and identifying inefficiencies. Understanding how maintenance requests flow through your organization will highlight bottlenecks and areas that could benefit from automation or improvement.
Here’s how to carry out an effective assessment:
- Document Current Workflows: Write down how tasks are currently completed to serve as a baseline.
- Identify Pain Points: Look for delays, repetitive tasks, or communication breakdowns that could be alleviated with a CMMS.
- Gather Feedback: Don't just rely on your observations; invite input from users and stakeholders. Their insights can offer a more rounded picture of where challenges lie and what solutions might be suitable.
Integrating with Existing Systems
Integration of a CMMS with existing systems is a common hurdle that organizations face—but it can be managed. Many businesses utilize various software for different functions. Ensuring that your new CMMS communicates seamlessly with these existing systems is essential for fostering a unified operation.
- API Utilization: Check whether your current software can communicate through Application Programming Interfaces (APIs). This allows for smoother data transfers between systems.
- Data Migration: Safeguarding your historical data is important. Plan how existing data will be transferred into the new system without losing accuracy or integrity.
- Iterative Testing: Conduct pilot tests with integrated systems before the full rollout. This allows you to identify any issues and resolve them before they affect the entire operation.
Training and Support
A powerful CMMS is only as good as the people utilizing it. Thus, training and support play a critical role in the implementation process. Skipping or shortening this step could lead to underutilization of the software and a less-than-optimal return on investment.
To create an effective training program:
- Tailored Training Sessions: Design training sessions that suit different user levels. Not every user needs to know every detail about the system.
- Hands-on Workshops: Encourage practical workshops where users can engage with the software in real-time. This hands-on approach often leads to faster mastery.
- Ongoing Support: Provide continuous support through resources like user guides, FAQs, and dedicated support teams to resolve issues as they arise.
"Investing in robust training and support helps solidify user confidence, making them champions of the new system rather than reluctant participants."
In summation, the success of CMMS implementation largely hangs on careful planning, comprehensive training, and robust integration strategies tailored to meet your organization's unique needs.
Challenges Associated with CMMS Adoption
Adopting a Computerized Maintenance Management System (CMMS) isn't just about picking the right software; it's about navigating hurdles that can muddy the waters of implementation. These challenges can impact not only how well a CMMS performs but also how the team adapts to it. Understanding these obstacles is crucial for decision-makers and IT professionals who are keen on leveraging the full potential of CMMS solutions to enhance their operations.
One significant element is resistance to change. Often, employees may feel hesitant or uncomfortable about altering established routines, especially if they have been doing things a certain way for a long time. This kind of sentiment can lead to pushback against new systems, creating friction that undermines the effort to implement a CMMS.
Integrating a new CMMS with existing systems poses another major challenge. Many organizations run multiple software solutions simultaneously, and ensuring that all these systems can communicate effectively is often no small feat. [
Resistance to Change
Resistance to change is as old as time. When faced with the prospect of adopting a new CMMS, many employees can become skeptics teetering between the push for modern efficiency and the comfort of familiarity. This reluctance can stem from various sources. Some may worry about their ability to learn the new system. Others might believe that the current processes, even if inefficient, are "good enough." Here’s a closer look at this phenomenon:
- Fear of Job Security: Many individuals may associate new technology with job loss or diminished roles.
- Learning Curve Concerns: Employees may dread the thought of undergoing training sessions, fearing that they won't grasp the new system quickly enough.
- Old Habits Die Hard: Once people settle into a rhythm, changing that rhythm feels like trying to teach an old dog new tricks.
Organizations can counteract resistance by involving team members during the selection phase. Allowing potential users to provide input fosters a sense of ownership. Additionally, presenting data or case studies that highlight the benefits of CMMS adoption can help to soften resistance. Creating effective communication channels during the transition period can also be a game changer.
Integration Issues
Integrating a CMMS with pre-existing systems is akin to fitting a square peg in a round hole; it’s sometimes tricky, more often than not requires creative solutions. Many organizations have legacy systems that have been in place long before modern CMMS options emerged. Missing out on integration means missing out on crucial efficiencies. Here are some common integration challenges:
- Data Compatibility: Different systems may not speak the same language, leading to data inconsistencies or errors.
- Timing Conflicts: When a CMMS is integrated with systems that operate in real-time, any lag can cause operational snags, impacting productivity.
- Resource Constraints: Sometimes there may be insufficient IT resources to manage the integration, leading to potential delays and frustrations.
Organizations should conduct thorough audits of their existing systems before fully committing to a CMMS. By doing this, they can identify potential integration points and gaps. Consulting with technology experts who specialize in integrations can also save time and effort, ensuring a smooth transition from old systems to the new CMMS. In the end, addressing resistance to change and integration issues head-on can pave the way for a successful CMMS adoption that truly benefits an organization.
Future Trends in CMMS Technology
The landscape of Computerized Maintenance Management Systems is evolving swiftly, and it’s crucial for businesses to keep an eye on future trends that could significantly enhance their operational efficiency. By focusing on emerging technologies, organizations can better equip themselves to handle maintenance challenges effectively. Understanding these trends is paramount as they bring not only enhancements in functionality but also new avenues for operational savings and productivity gains.
Artificial Intelligence in CMMS
Artificial Intelligence is making waves across industries, and CMMS software stands to benefit significantly from its integration. AI can analyze vast amounts of data much faster than any human could. For maintenance teams, this means predictive maintenance strategies can be employed, enabling them to anticipate equipment failures before they happen.
- Predictive Analytics: Using historical data and predictive algorithms, AI can help foresee maintenance needs, which can reduce downtime and the associated costs.
- Automated Scheduling: AI enables automatic adjustments to maintenance schedules based on real-time data. This adaptive response can help in managing workloads more efficiently.
- Smart Inventory Management: AI helps in fine-tuning inventory management by predicting when supplies will run low, building a more streamlined process that minimizes waste.
Integrating AI into CMMS will not just make processes smarter but also frees up human resources to focus on strategic tasks rather than routine monitoring.
Mobile Accessibility
In today’s fast-paced world, mobile accessibility for CMMS is not just a luxury; it’s a necessity. Technicians and maintenance teams often operate on-the-go, moving between various jobs. Therefore, a robust mobile CMMS offers several advantages:
- Real-time Updates: Being able to update work orders or check inventory from a mobile device ensures that teams are always working with up-to-date information.
- Field Data Collection: Technicians can take immediate notes and upload images or videos straight into the system while at the site. This data can be invaluable later for reference or analysis.
- Improved Communication: Mobile access can facilitate quick communication between fieldworkers and the central management team, fostering a collaborative environment that is essential for problem-solving.
Embracing mobile accessibility can empower teams to operate more efficiently, reducing the time spent on administrative tasks and increasing the time dedicated to actual maintenance work.
Cloud-Based Solutions
The shift towards cloud-based solutions marks a pivotal trend in CMMS technology. By deploying CMMS in the cloud, organizations can achieve several benefits that cater to the needs of modern enterprises:
- Scalability: A cloud-based CMMS allows organizations to easily adjust their resource utilization based on current needs without upfront investments in hardware.
- Accessibility: Being web-based means that personnel can access the system from virtually anywhere. This flexibility is especially advantageous for companies with multiple locations.
- Cost-Effective Upkeep: Software updates, security measures, and server maintenance are handled by the provider, reducing the internal IT workload and associated costs.
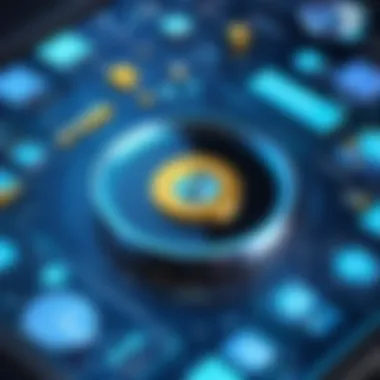
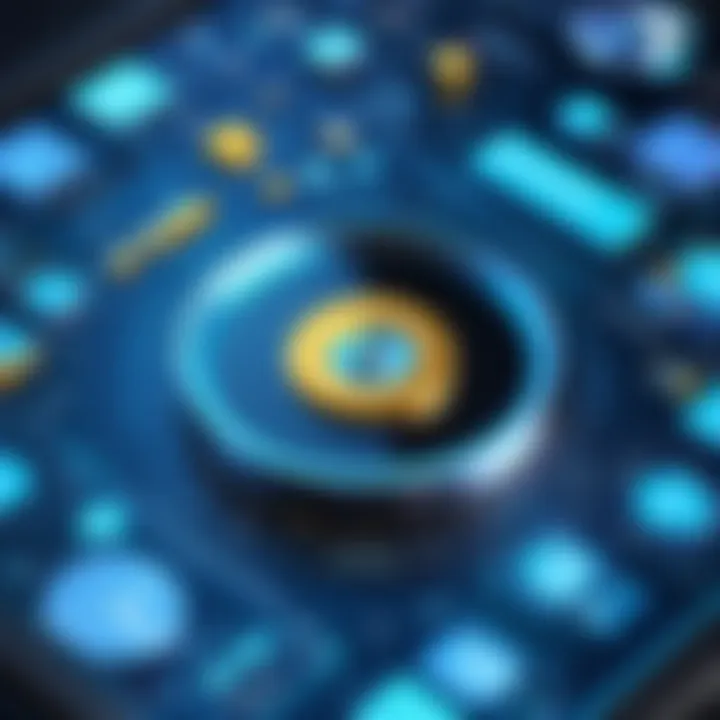
Moreover, the integration of cloud-based CMMS with other cloud applications can yield powerful solutions, creating a comprehensive data ecosystem that can be harnessed for deeper insights.
"Investing in future trends like AI, mobile accessibility, and cloud-based solutions is not just smart; it’s a game changer for maintenance management success."
In summary, keeping pace with such trends ensures that organizations not only improve their efficiency today but are also prepared for the challenges of tomorrow. The future of CMMS is bright, bursting with potential to transform how maintenance is approached across industries.
Selecting the Right CMMS for Your Organization
Choosing the right Computerized Maintenance Management System (CMMS) is not just a decision made on a whim; it's a pivotal step that can shape the operational efficiency of an organization. The right CMMS can streamline processes, enhance communication, and ultimately lead to significant cost savings. Diving deep into the options available isn't merely beneficial—it's essential.
One primary factor to keep in mind when selecting a CMMS is the specific needs and workflows of your organization. Different industries have their own unique challenges and requirements, and underestimating this can lead to unfruitful implementations. For instance, a manufacturing firm may prioritize asset management features whereas a facility management company might need comprehensive reporting tools. The ability to customize and adapt the CMMS to fit organizational needs is invaluable.
Furthermore, embracing a CMMS translates directly to productivity gains, as it promotes effective maintenance scheduling and resource allocation. With this in mind, the decision-makers need to thoroughly assess their requirements to ensure the selected system aligns with their operational objectives.
Establishing Requirements
A thorough assessment of your organizational needs is the starting point for CMMS selection. Begin by gathering input from various departments, from maintenance crews to upper management. Each department may have distinctive insights into what features would serve them best. A collaborative approach in determining requirements helps ensure that the final choice has buy-in and meets the diverse needs of the organization.
Some critical elements to consider when defining these requirements include:
- Core functionalities such as work order creation, tracking, and asset management.
- Integration capabilities with existing systems to avoid redundant data entry and ensure seamless information flow.
- User-friendliness, as a system that is complicated or clunky can hinder productivity.
- Scalability to support growth as business needs evolve over time.
Engaging with stakeholders across the organization ensures that all perspectives are taken into account, ultimately resulting in a more favorable outcome.
Budget Considerations
When it comes to choosing a CMMS, financial aspects can heavily influence decision-making. Understanding the total cost of ownership is essential, as it goes beyond just the initial purchase price. There are ongoing costs such as maintenance fees, potential upgrades, and training expenses that need to be factored in as well.
Additionally, organizations should consider how the CMMS can provide returns on investment. Will it reduce downtime of critical assets? Can it extend the lifespan of equipment? Evaluating these factors can help justify the costs.
Some tips for budget considerations include:
- Prioritizing essential features over luxury ones. Knowing what is crucial allows for more focused spending.
- Exploring various pricing models, like subscription vs. one-time fees, to find what fits your situation better.
- Researching different vendors often leads to discovering cost-effective solutions that also meet your organizational needs.
Overlooking the budget can derail even the best-planned CMMS implementations, so it is critical to approach this step thoughtfully, ensuring alignment with the organization's financial capabilities.
"Selecting the right CMMS is akin to laying the foundation for your operational success. Choose wisely, for the return can be substantial."
Real-life Case Studies of CMMS Implementation
Real-life case studies offer valuable insights into how organizations across various industries navigate the implementation of Computerized Maintenance Management Systems (CMMS). These case studies serve not only to showcase practical applications but also to illuminate potential pitfalls and best practices. For decision-makers and IT professionals, understanding these real-world scenarios can greatly inform their own strategies, leading to smarter choices and smoother transitions.
Manufacturing Sector
In the manufacturing sector, the need for an efficient maintenance management system is often amplified by the complexity of operations and the high cost of downtime. One notable case study comes from a large automotive parts manufacturer, which faced significant challenges with equipment reliability. Previously relying on fragmented spreadsheets and paper-based systems, the organization struggled to track assets, leading to delayed repairs and reactive maintenance strategies.
Upon implementing a cloud-based CMMS, the organization managed to centralize all maintenance activities. The system facilitated real-time updates on equipment status, streamlined work order processes, and improved inventory management of spare parts. It may not seem like much, but this centralized approach resulted in a 30% reduction in downtime over six months. Employees were also required to undergo minimal training due to the user-friendly interface, which mitigated resistance during the transition.
"Adopting the CMMS was like switching from dial-up to high-speed internet. The change was drastic, and it paid off in ways we couldn't have imagined."
This particular case highlights the importance of selecting a CMMS that aligns well with an organization's existing processes. Integration with other systems, like ERP, was also a critical consideration in this transition. Ultimately, a targeted focus on asset reliability coupled with consistent training proved to be a winning strategy.
Facility Management
Facility management encompasses a broad range of responsibilities, from maintaining HVAC systems to overseeing building safety. A compelling example of effective CMMS implementation is seen in a university's campus facilities management operation. The institution managed multiple buildings with diverse systems in place, which made tracking maintenance requests and schedules cumbersome.
After choosing a robust CMMS solution, the university witnessed significant transformative changes. The software enabled a more proactive maintenance approach, allowing the facilities team to prioritize preventative maintenance tasks and schedule routine inspections. More importantly, the CMMS facilitated communication between departments, ensuring that requests and issues reported by faculty and students were promptly addressed.
The outcome was noticeable; service request response times were reduced by 25%, and the overall efficiency of the facility management team improved markedly. This case emphasizes that successful CMMS implementations not only rely on the technology itself but also on the organizational culture that embraces change and values inter-departmental collaboration.
Culmination and Recommendations
The conclusion and recommendations section serves as the linchpin of this article, consolidating insights on Computerized Maintenance Management Systems (CMMS) gleaned throughout our exploration. It synthesizes the broader implications of implementing a CMMS, emphasizing not only the technological considerations but also the strategic business impacts.
Summarizing Key Points
Through our detailed examination of various CMMS software options, it’s clear that several key factors emerge as pivotal in the decision-making process:
- Tailored Features: Different industries require distinct functionalities. What works for manufacturing may not suit facility management. It’s vital to align software capabilities with specific operational needs.
- User-Friendly Interfaces: High adoption rates often hinge on how intuitive the software is. Solutions that are straightforward to navigate can significantly enhance workflow efficiency.
- Integration Capabilities: The ability of a CMMS to mesh seamlessly with existing systems can’t be underestimated. Organizations should assess how well a potential CMMS will integrate with their current processes and infrastructure.
- Cost-Benefit Analysis: While a higher initial investment may seem daunting, the long-term savings in maintenance and operational efficiency can often justify the expense.
In a nutshell, the choice of CMMS software should reflect a thorough understanding of both organizational needs and market offerings, ensuring a sound long-term investment.
Final Words on CMMS Selection
Selecting the right CMMS is not merely about picking software; it’s about carving a path toward enhanced operational resilience and efficiency. Decision-makers should consider the following:
- Assessment of Long-Term Goals: Align the chosen software with long-term strategic objectives. Will it help in scaling operations as the organization grows?
- Engage Stakeholders: Getting feedback from end-users can uncover vital insights on preferences and usability that decision-makers may overlook.
- Trial Periods and Demos: Many vendors offer trial versions. Use these trials to involve staff in real-world scenarios to gauge the software fit.
- Stay Updated with Trends: The realm of CMMS is rapidly evolving with technologies like AI and mobile access. Organizations should prioritize solutions that stay ahead of the curve, ensuring adaptability in the face of change.
"The only way to do great work is to love what you do." - Steve Jobs
This philosophy should resonate within organizations as they embark on the journey of adopting a CMMS.