Understanding eMaint CMMS Software: A Comprehensive Review
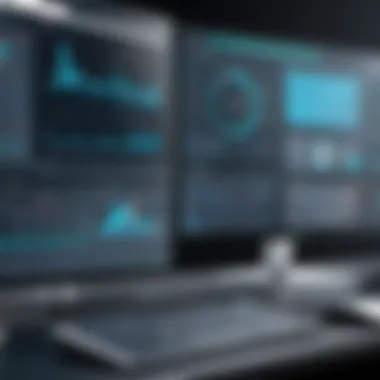
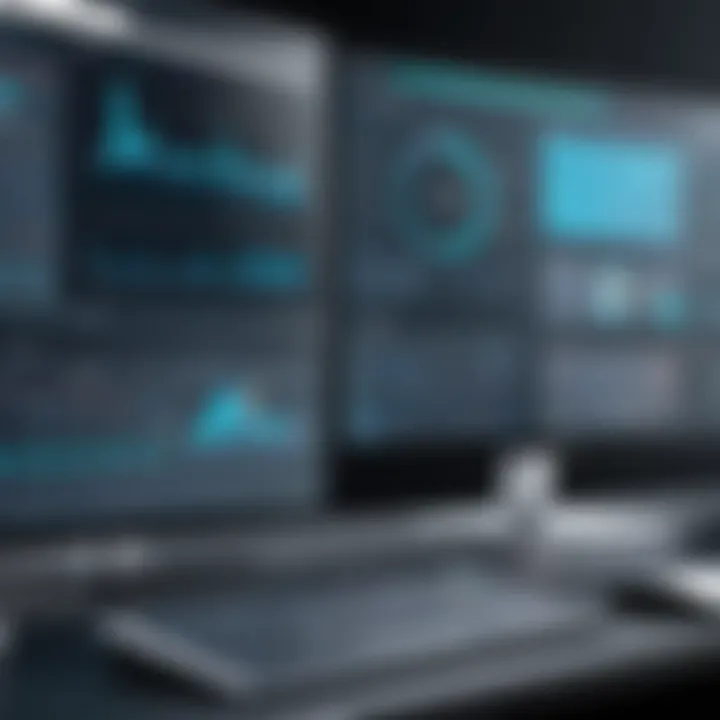
Intro
In today's fast-paced business environment, efficient maintenance processes are crucial. A Computerized Maintenance Management System (CMMS) like eMaint serves to streamline these processes, enhancing productivity and minimizing downtimes. Understanding such software not only helps maximize resources but also can significantly improve operational efficiencies.
This article will dive into the specifics of eMaint CMMS software, exploring its features and benefits, along with practical implementation strategies. In addition, it will provide a comparative analysis of top CMMS software options, focusing on what distinguishes eMaint in the marketplace.
Software Category Overview
Definition and Importance
CMMS is a type of software that assists organizations in managing maintenance operations. This includes tracking maintenance tasks, inventory management, and scheduling preventive maintenance. The importance of CMMS lies in its ability to help businesses reduce operational costs, enhance asset management, and increase overall efficiency.
Proper implementation of a CMMS leads to significant benefits. These may include improved equipment lifespan, reduced unexpected failures, and optimized maintenance strategies which ultimately contribute to increased productivity across the board.
Key Characteristics
Some key characteristics of eMaint CMMS software include:
- User-Friendly Interface: Designed to be intuitive, allowing for quick onboarding and efficient usage.
- Customizable Dashboards: Users can tailor their dashboards to display relevant information, enhancing decision-making.
- Mobile Accessibility: Enables personnel to access vital data remotely, ensuring they can manage tasks on the go.
- Reporting and Analytics Tools: Provides in-depth insights into maintenance trends and equipment performance.
- Integration Capabilities: Can connect with other enterprise systems, improving workflows and data continuity.
"Implementing a CMMS can transform maintenance from a reactive approach to a proactive strategy, enhancing overall operational effectiveness."
Comparative Analysis of Top Software Options
Feature Comparison
When choosing a CMMS solution, it's critical to compare the features across various options. eMaint stands out for its robust asset management functionalities, including:
- Comprehensive preventive maintenance scheduling
- Work order management tools
- Inventory control and tracking
- User-defined workflows
Other CMMS options like Maintenance Connection or Fiix have their own unique attributes, providing different functionalities that some businesses may prefer.
Pricing Models
Pricing for CMMS software generally varies based on features and user count. eMaint offers tiered pricing plans suitable for different business sizes, from small startups to large enterprises. While some software might work on a subscription model, others could have one-time licensing fees. Evaluating the pricing models helps in decision-making based on budget constraints and expected ROI.
Prologue to eMaint CMMS Software
The significance of eMaint CMMS software cannot be overstated in today’s business landscape. Maintenance management is a critical function that influences not only the operational efficiency of an organization but also its bottom line. Without effective maintenance systems in place, organizations risk increased downtime, lost productivity, and inflated costs. This is where eMaint, as a Computerized Maintenance Management Software (CMMS), plays a crucial role.
Defining CMMS
CMMS stands for Computerized Maintenance Management System. It is software that assists in setting up, planning, tracking, and managing maintenance operations. The main purpose of a CMMS is to streamline maintenance management across various sectors. By centralizing data related to maintenance activities, CMMS aids in identifying issues before they escalate, ensuring that equipment operates efficiently and reliably.
In essence, a CMMS provides users with:
- Work order generation: Creating tasks for maintenance teams to address.
- Preventive maintenance scheduling: Planning inspections and repairs to avoid unexpected breakdowns.
- Asset management functionalities: Keeping track of inventory and asset history.
- Reporting capabilities: Offering insights and analytics to assist in decision making.
- Compliance tracking: Helping organizations meet regulatory requirements related to equipment safety and performance.
Role of eMaint in CMMS
eMaint is a leading CMMS solution that provides a suite of tools designed to enhance maintenance operations. Its platform offers features that cater to different industries, allowing for customized solutions to meet specific needs.
The role of eMaint in CMMS can be outlined as follows:
- Centralization of Data: eMaint consolidates all maintenance-related data into a single platform, making it easy for users to access and analyze information.
- Improving Communication: The software enhances communication between maintenance teams and other departments, facilitating smoother operations.
- Real-Time Tracking: Users can monitor work orders and asset statuses in real-time, allowing for quick responses to emerging issues.
- Customization and Scalability: eMaint offers flexible options to tailor workflows and reports to an organization’s unique needs and scales with business growth.
- Enhanced Decision-Making: With powerful analytics tools, eMaint empowers stakeholders to make informed maintenance decisions.
eMaint CMMS serves as an essential tool for organizations aiming to improve efficiency, prolong equipment lifespan, and reduce operational costs. By providing a centralized approach to maintenance management, it lays the foundation for smarter asset management and a more sustainable operational strategy.
Key Features of eMaint
Understanding the key features of eMaint CMMS software is crucial for any organization aiming to optimize its maintenance operations. The functionality offered by eMaint is not just a set of tools; these features are critical components that elevate the overall efficiency and effectiveness of maintenance management. Each feature addresses specific needs, from day-to-day operations to strategic decision-making. In the following subsections, we will explore these features, their importance, and how they can be leveraged to drive better results in maintenance environments.
Work Order Management
Work order management is a foundational element of eMaint. It allows users to create, assign, and track work orders seamlessly. This feature ensures that work is prioritized effectively and completed in a timely manner. With intuitive user interfaces and a variety of options to customize workflows, teams can adapt the system to their specific requirements.
Key benefits include:
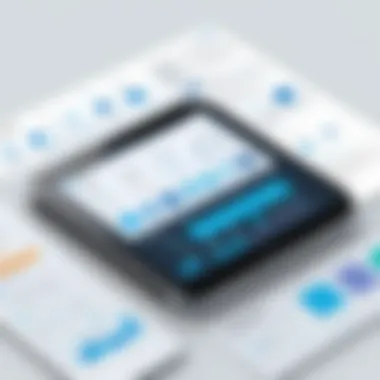
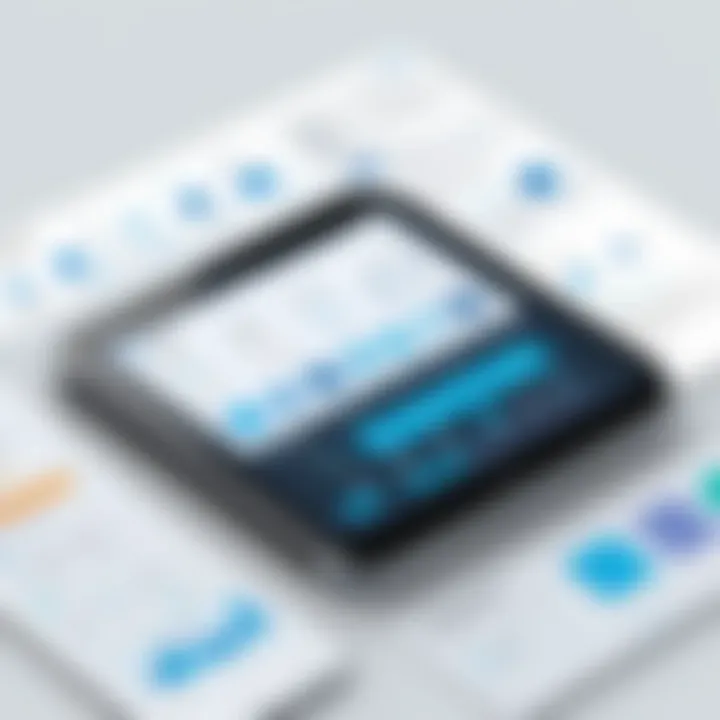
- Enhanced accountability among team members.
- Real-time tracking of job status.
- Ability to prioritize tasks based on urgency.
Effective work order management minimizes downtime and optimizes resource allocation, leading to improved operational performance.
Preventive Maintenance
Preventive maintenance in eMaint helps organizations avoid costly repairs and unplanned downtime. This feature allows users to schedule regular maintenance activities for assets, promoting longevity and reliability. By setting reminders and alerts, managers ensure that all tasks are performed as planned.
The importance of this feature lies in:
- Reducing repair costs through consistent upkeep.
- Lengthening the lifespan of equipment.
- Enhancing safety by ensuring compliant operations.
Incorporating preventive maintenance into a company's routine can lead to significant improvements in both productivity and asset utilization.
Asset Management
Asset management is about knowing what you have and ensuring it is functioning at its best. eMaint provides tools for tracking assets throughout their lifecycle. This feature includes details like purchase dates, warranties, and maintenance histories. Efficient asset management helps organizations make informed decisions about maintenance and replacement.
Critical aspects of asset management include:
- Monitoring asset performance to identify issues before they escalate.
- Facilitating informed purchasing decisions based on historical data.
- Supporting compliance with regulatory requirements.
An efficient asset management strategy ensures that resources are used effectively, enabling organizations to plan their budgets better and avoid unnecessary expenditures.
Inventory Control
Inventory control is essential for managing spare parts and supplies effectively. eMaint enables organizations to maintain accurate inventory levels, preventing stockouts and excess inventory. This feature includes tracking parts usage, automating reordering processes, and optimizing storage solutions.
Advantages of efficient inventory control:
- Ensures critical parts are on hand when needed.
- Reduces holding costs associated with excess inventory.
- Improves financial management through better cash flow.
By understanding and utilizing the inventory control features, organizations can not only support their maintenance activities but also enhance overall supply chain management.
Reporting and Analytics
The reporting and analytics features in eMaint offer insights that are invaluable for decision-makers. With the ability to generate various reports on equipment performance, maintenance costs, and work order history, organizations can identify trends and areas for improvement.
Key benefits include:
- Data-driven decision making supported by real-time analytics.
- Transparency in maintenance operations.
- Enhanced ability to forecast future maintenance needs based on historical data.
These insights allow companies to fine-tune their maintenance strategies, streamline operations, and allocate resources effectively.
Overall, the key features of eMaint CMMS are designed to enhance operational efficiency, reduce costs, and simplify maintenance management. With a clear understanding of what these features offer, organizations can better assess how eMaint will integrate into their operational framework.
Benefits of Implementing eMaint
Implementing eMaint CMMS software can profoundly impact an organization's maintenance processes. The benefits are not just limited to one aspect but span operational, financial, and regulatory dimensions. Business owners and IT professionals must weigh these factors when deciding on a CMMS solution. eMaint provides a structured approach to maintenance that may lead to significant improvements in various areas.
Cost Reduction
One of the primary advantages of adopting eMaint is its potential for cost reduction. Organizations often face escalating maintenance costs due to unplanned downtime and emergency repairs. By utilizing eMaint to schedule preventive maintenance, businesses can shift from reactive to proactive strategies. This means that machinery and assets are maintained regularly, reducing the chances of unexpected failures and the associated costs.
Additionally, eMaint allows for better inventory management. Businesses can track parts and supplies more accurately, reducing excess inventory and avoiding the costs associated with stockouts or overstocking. Accurate reports and analytics within eMaint help identify spending patterns, enabling more informed financial decisions.
"Investing in preventive strategies saves money in the long run, making eMaint a smart choice for organizations aiming to reduce expenses."
Increased Operational Efficiency
Operational efficiency is enhanced when maintenance management is streamlined through eMaint. The software automates tasks such as work order creation, scheduling, and tracking. This automation reduces the manual work required from maintenance teams, freeing up time for more critical tasks.
With its user-friendly interface, eMaint allows team members to quickly access necessary information. This accessibility facilitates faster response times to maintenance requests and issues. Moreover, real-time analytics inform decisions about asset performance, allowing managers to optimize operations effectively. Consequently, efficiency in workflows can lead to more productive work environments.
Improved Compliance and Safety
Regulatory compliance and safety management are paramount in industries that rely heavily on equipment and machinery. eMaint provides tools that help ensure compliance with industry regulations by keeping accurate records of maintenance activities. Adhering to scheduled maintenance requirements protects both the organization and its employees.
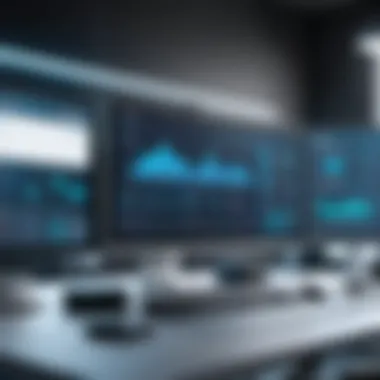
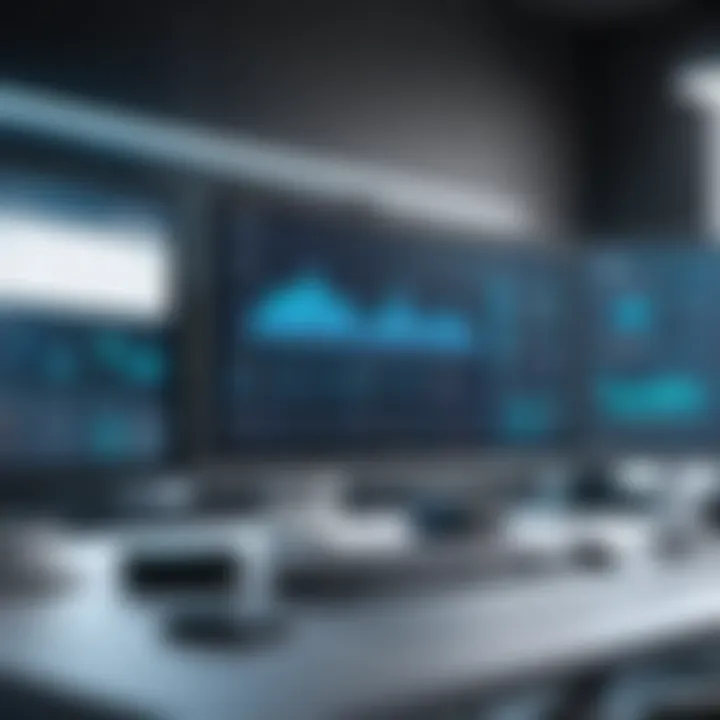
Safety is invariably tied to proper maintenance practices. By ensuring that equipment is functioning correctly, eMaint helps mitigate risks associated with equipment failure. Regular maintenance logs can support safety audits and inspections, thus contributing to an overall safer work environment. Users can be assured that they are meeting regulatory demands, which can also reduce liability and enhance reputation.
Integrating eMaint with Existing Systems
Integrating eMaint CMMS with existing systems is vital for organizations seeking to enhance their maintenance management processes. This integration facilitates a seamless flow of information between eMaint and other software applications employed within the organization. It ensures that users can access all relevant data from a single interface, which simplifies operations. Moreover, it eliminates redundancies and increases accuracy across the board. In a competitive landscape, organizations that effectively connect their systems can achieve greater operational efficiency, leading to improved productivity and reduced costs.
APIs and Data Import
Application Programming Interfaces (APIs) are crucial for integrating eMaint with other applications. They allow different software systems to communicate with each other dynamically. For instance, an organization may wish to link its eMaint CMMS with an ERP system like SAP or an inventory management system. By utilizing APIs, data such as work orders, inventory levels, and asset information can be automatically exchanged. This reduces the risk of manual errors that can arise from data entry and ensures that all systems are updated in real-time.
Data import is another vital aspect of integration. Before initiating eMaint, organizations may have existing data scattered across various systems. This data needs to be carefully migrated to eMaint without loss of integrity. A systematic approach to data import includes:
- Data cleansing: Ensure all data is accurate and up-to-date before migration.
- Mapping fields: Align existing data fields with those in eMaint for consistency.
- Testing: Conduct tests to confirm data accuracy post-migration.
The integration is also about simplifying operations. By connecting eMaint to existing systems, users can instantly access past work orders or maintenance records. This can lead to better decision-making and quicker response times when issues arise.
User Training and Support
User training is necessary for successful integration of eMaint. Even with the best systems in place, if users are not educated about how to use them effectively, the integration will not yield its full benefits. Organizations must recognize that user resistance can be a significant barrier to successful implementation. Hence, a thoughtful training program addressing the needs and workflows of the users is essential.
Training should encompass:
- Initial orientation: Introducing users to the functionalities of eMaint.
- Ongoing training: Regular training sessions to keep staff updated on new features.
- Hands-on workshops: Practical sessions that allow users to engage with the software in real-life scenarios.
Support also plays a crucial role. Organizations must provide continuous technical assistance to users. This can come in the form of:
- Helpdesk support: A dedicated team available to resolve technical issues.
- Online tutorials: Step-by-step guides available on the company's intranet or eMaint's website.
- Community forums: Encouraging users to participate in discussions for shared learning.
Use Cases of eMaint CMMS
Understanding the use cases of eMaint CMMS is crucial for organizations seeking to implement it effectively. The application of this software goes beyond mere maintenance management. It addresses various sectors, proving to be a versatile tool that enhances operational efficiency. Organizations can tailor its implementation based on specific needs, ensuring maximum benefit.
Manufacturing Applications
In the manufacturing sector, eMaint CMMS plays a pivotal role. It helps streamline operations by ensuring that machinery is maintained regularly, thus reducing downtime. Proper maintenance schedules can be established, helping to avoid costly breakdowns.
Moreover, the software allows for detailed tracking of equipment history. Users can easily access information about previous repairs, which aids in decision-making. With eMaint, the manufacturing process becomes not only more reliable but also more efficient. The integration of preventive maintenance practices can lead to increased productivity.
Facility Management
Facility management is another area where eMaint shows its value. Managing multiple facilities efficiently can be a daunting task, but eMaint provides tools that simplify this process. Users can monitor maintenance tasks for different locations all from a single platform. This centralized approach helps in maintaining consistency and accountability.
Additionally, eMaint supports tracking of work orders, which can help streamline communication among team members. Facility managers can oversee all activities, ensuring that every task is documented and completed. This improves safety and compliance, which is essential in any facility management operation.
Fleet Management
Fleet management also benefits significantly from eMaint CMMS. The maintenance of vehicles is critical to reducing operational costs and enhancing safety. Using eMaint, fleet managers can create maintenance schedules for each vehicle effectively. This includes tracking oil changes, tire rotations, and inspections.
A structured maintenance approach ensures that vehicles remain in top condition, decreasing the chances of accidents or unexpected failures. Furthermore, real-time data analytics provided by eMaint helps in identifying cost trends associated with fleet operations. This insight enables better financial planning and resource allocation, which is vital for any organization managing a fleet.
"Using eMaint in manufacturing, facility management, and fleet management leads to more structured operations and enhanced productivity."
Challenges in eMaint Implementation
Implementing eMaint CMMS software is not without its challenges. Understanding these challenges is crucial for any organization considering the transition. Neglecting these factors can hinder the benefits expected from the implementation and can lead to increased costs or delays. Companies need to navigate two significant hurdles: data migration issues and user adoption barriers. Addressing these challenges effectively can set the stage for a successful implementation.
Data Migration Issues
Data migration is one of the most critical tasks during any software upgrade or transition to a new system like eMaint. The process involves transferring existing data into the new CMMS platform. Errors can occur at various stages, leading to data loss or corruption if not handled with care. Improper data mapping can cause discrepancies, which may affect system functionality and reporting accuracy.
- Data Quality Assessment: Before migration, organizations must evaluate the quality of the existing data. Poor-quality data can skew results in the new system. This assessment should include identifying outdated, incomplete, or duplicate data.
- Data Mapping and Cleanup: Mapping the data correctly is fundamental to maintaining integrity. This might require thorough data cleansing efforts to ensure consistency and accuracy.
- Testing: It is advisable to conduct thorough testing before going live with the new system. Testing can help identify any potential issues that may arise from the migration process.
"A successful data migration strategy will consider not just the transfer but the continuous integrity of the data within the new system."
Overall, companies must allocate adequate resources and time for this phase. Failure to do so can lead to extended downtimes or increased operational disruptions.
User Adoption Barriers
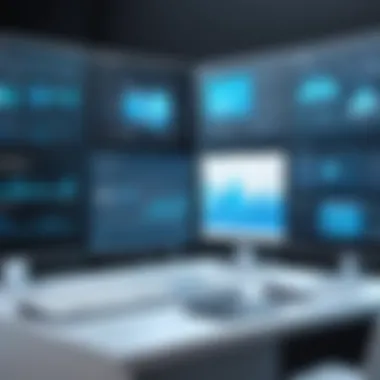
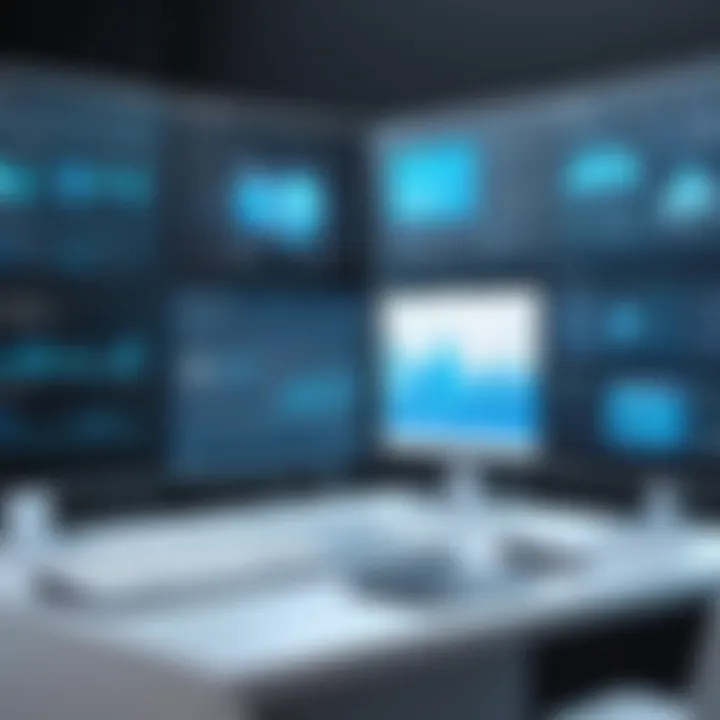
Even if the data migration is flawless, user adoption remains a paramount concern. A new system may offer advanced features and improved efficiency, but if employees are resistant or struggle to adapt, the potential benefits may never be realized.
- Training Programs: Comprehensive training programs should be prepared in advance. Effective training is key to ensuring that users feel confident and competent in using the new system. This often requires a blend of formal training sessions and ongoing support resources.
- Change Management: Organizations must implement a change management strategy to guide employees through the transition. Communication about the benefits of the new system is essential to alleviate fears regarding job security or increased workload.
- Feedback Mechanisms: Establishing open channels for feedback can help address concerns as they arise. Listening to users allows organizations to refine training and support efforts, ensuring better adoption rates.
Evaluating eMaint CMMS Alternatives
The decision to implement a Computerized Maintenance Management System (CMMS) like eMaint is significant. However, it is equally essential to understand other available options in the market. Evaluating eMaint CMMS alternatives allows organizations to make informed decisions that align with their specific operational needs.
When assessing alternatives, consider the following key elements:
- Feature Set: Not all CMMS solutions offer the same functionalities. Each system may emphasize different aspects, such as preventive maintenance, asset management, or reporting. Analyze whether an alternative covers the functionalities that are most crucial for your organization.
- Scalability: Can the software grow with your organization? A system that meets your needs today might not suffice in the future. Ensure the alternatives can accommodate potential expansion.
- User Experience: A user-friendly interface impacts adoption rates. Consider the learning curve for employees and how intuitive the alternative systems are.
- Integration Capabilities: The ability to work smoothly with existing systems, like ERP solutions or inventory management tools, is vital. Check how each alternative integrates with current software ecosystems.
- Cost: Financial considerations are always crucial. Compare not just the initial costs but also ongoing expenses, like subscription fees and maintenance costs. A lower initial price may lead to higher costs later on.
Evaluating alternatives is not merely about finding something cheaper; it’s about finding the best fit for your organization.
By thoroughly analyzing these areas, decision-makers can identify platforms that might suit their maintenance management needs better than eMaint. This targeted approach can prevent future complications that arise from suboptimal software choices.
Understanding the variety of options makes the process more insightful and constructive instead of just comparing features.
Comparative Analysis of Popular CMMS Solutions
In a crowded marketplace, several popular CMMS solutions vie for attention. Each offers unique advantages tailored to different business sizes and sectors. When conducting a comparative analysis, consider the following:
- Hippo CMMS: Known for its straightforward user interface, Hippo focuses on user experience. Its cloud-based system allows easy access from anywhere, making it appealing for teams who work remotely.
- Fiix: This solution is robust in its reporting and analytics features. Fiix also facilitates the automation of maintenance tasks, allowing organizations to maximize uptime and resource management.
- Motive: A newer player in the space, Motive excels in mobile management, offering sophisticated features for fleet and field management. This can be particularly relevant for organizations with mobile assets.
- MPulse Software: MPulse offers a wide range of features that include both preventive and corrective maintenance capabilities. It is suitable for diverse industries and provides various customization options.
By outlining these solutions along with their unique benefits, organizations can pinpoint a CMMS that not only meets operational standards but also conforms to the organizational culture and workflows.
Choosing the Right Software
Selecting the right CMMS requires thorough due diligence. Start by defining your specific maintenance management needs, identifying the challenges faced in your current processes.
Consider the following steps when choosing the right software:
- Identify Your Needs: Examine what you hope to achieve. Is the focus on reducing downtime, improving asset tracking, or streamlining workflows? Knowing these will narrow down your options significantly.
- Request Demos: Most software providers offer demos or trials. Utilize these opportunities to explore functionalities and user interfaces firsthand. It grants clarity on whether the software can fulfill your specific requirements.
- Consult Stakeholders: Engage end-users and stakeholders from various departments. Their input can surface potential obstacles or provide insights that may enhance the eventual usage of the software.
- Analyze Reviews and Testimonials: Seek out feedback from current users. Reviews often reflect recurring themes regarding strengths and weaknesses that can guide you toward making a more informed choice.
- Evaluate Support Services: A robust customer support system is essential. Determine how accessible and helpful the support team is for troubleshooting or continuous guidance post-implementation.
By systematically assessing these aspects, organizations can confidently choose software that aligns closely with their unique maintenance management strategies.
The Future of CMMS Technology
As organizations increasingly embrace digital transformation, the future of Computerized Maintenance Management Systems (CMMS) like eMaint is still evolving. The importance of this topic lies in understanding the ongoing trends and technological advancements that promise to reshape maintenance management. Companies that stay ahead of these trends can gain not just operational efficiencies, but also a competitive edge. Adapting to the future of CMMS will affect how maintenance tasks are executed, how resources are allocated, and how businesses interact with technology.
Emerging Trends in CMMS
New trends in CMMS are significantly impacting how maintenance is conducted across various sectors. The following points highlight some of the most notable trends:
- Cloud-Based Solutions: Many companies are moving to cloud-based CMMS platforms. This shift allows easier access to data from various locations. It enhances collaboration across teams and improves service delivery.
- Mobile Accessibility: The rise of mobile technology enables technicians to access CMMS applications on-the-go. This real-time access allows for quicker decision-making and response times to maintenance needs.
- Internet of Things (IoT): The integration of IoT with CMMS enables better data collection and predictive maintenance. Sensors on equipment can send real-time data to the CMMS, facilitating proactive maintenance decisions.
- Data Analytics and Reporting: Enhanced data analytics features in CMMS provide actionable insights. Organizations can track performance metrics and maintenance costs, allowing for informed decision-making.
- User-Centric Design: Modern CMMS interfaces focus on user experience. Simplified navigation and intuitively designed dashboards can improve user adoption and satisfaction.
These trends represent a shift toward greater efficiency and responsiveness in maintenance management. Organizations that utilize these innovations effectively can enhance their operational capabilities.
Impact of AI on Maintenance Management
Artificial Intelligence is poised to transform the landscape of CMMS fundamentally. It enables predictive maintenance that can foresee equipment failures before they occur. The implications of integrating AI into maintenance management are profound:
- Predictive Maintenance: By analyzing historical data and real-time information, AI can predict equipment failures and suggest maintenance schedules. This minimizes unexpected downtime and extends the lifecycle of assets.
- Automated Work Orders: AI can create and assign work orders based on data analysis. This reduces manual effort, streamlining processes and ensuring nothing is overlooked.
- Enhanced Decision-Making: AI algorithms can interpret data trends, helping managers make informed decisions quickly. This leads to better resource allocation and operational efficiency.
- Smart Alerts: With AI, CMMS can send alerts based on specific conditions or anomalies detected in equipment performance. This feature empowers maintenance teams to respond promptly to issues and reduce potential risks.
In summary, the future of CMMS technology is intimately linked with emerging trends and the growing impact of AI. These advancements not only optimize maintenance processes but also set a higher standard for what businesses can achieve with their maintenance strategies. The integration of such technologies will likely define the effectiveness of maintenance management as we move forward.
Finale
The conclusion serves as a significant element of this article, encapsulating the essence of the preceding discourse on eMaint CMMS software. It is not merely a summary but a critical synthesis of how this tool impacts maintenance management processes. Evaluating the core benefits such as enhanced efficiency, reduced costs, and improved compliance provides a compelling case for its implementation.
In the fast-paced business environment, decision-makers, IT professionals, and entrepreneurs must recognize the value of efficient maintenance management. eMaint's capabilities revolve around providing clarity and support in maintaining assets effectively. A clear understanding of its features allows organizations to leverage the software to its fullest potential.
Key considerations include:
- Operational efficiency: eMaint facilitates a structured approach to maintenance, leading to streamlined operations.
- Cost management: Implementing this software can reduce unnecessary expenses associated with unplanned downtimes.
- Enhanced decision-making: With robust analytics and reporting tools, businesses can make informed decisions based on real data.
The implementation of eMaint CMMS software can offer substantial competitive advantages to organizations that prioritize efficient maintenance procedures.
Final Thoughts
Reflecting on the discussion throughout this article, it is evident that eMaint CMMS software represents a pivotal solution in the landscape of maintenance management. The importance of selecting the right CMMS cannot be overstated, as it directly impacts operational effectiveness and cost management.
Ultimately, the choice of eMaint as part of an organization’s maintenance strategy can lead to significant improvements in productivity and reliability. As maintenance technology continues to evolve, staying informed about trends and features becomes essential for decision-makers. Adoption of eMaint CMMS not only aids current operations but also prepares business for future challenges in maintenance management.