Understanding Manufacturing Management Software
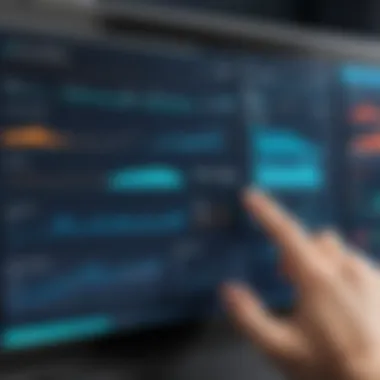
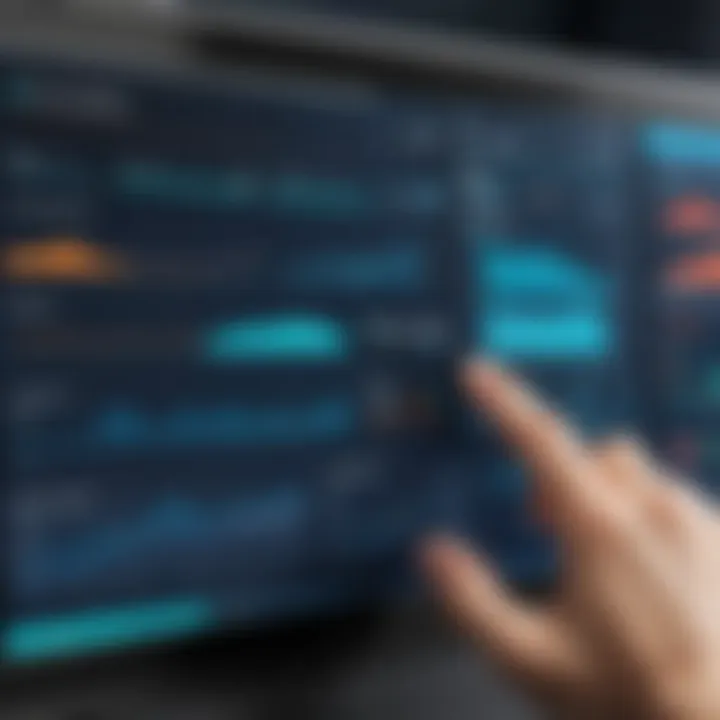
Intro
The modern manufacturing landscape has grown increasingly complex. In this environment, manufacturing management software (MMS) is crucial for maintaining operational efficiency. This software provides frameworks and tools to streamline processes, ensuring that production meets the demands of both speed and quality.
Decision-makers and IT professionals must understand what manufacturing management software entails, including its core components and potential impacts on their operations. The importance of these systems cannot be overstated, as they help organizations stay competitive in a rapidly evolving market.
Software Category Overview
Definition and Importance
Manufacturing management software refers to applications designed specifically to assist in the planning, execution, and management of production processes within manufacturing.
The importance of this type of software lies in its ability to integrate diverse functions ranging from inventory management to production scheduling. This integration helps to minimize waste, improve product quality, and ultimately lower costs.
Key Characteristics
Manufacturing management software typically exhibits several key characteristics:
- Integration Capabilities: The ability to connect other systems such as supply chain management and enterprise resource planning (ERP) is crucial.
- Real-time Data Processing: MMS allows for immediate data access, helping businesses make informed decisions quickly.
- User-friendly Interface: Good software is easy to navigate, enabling employees to adapt quickly without extensive training.
These characteristics collectively enhance the overall efficiency of manufacturing operations.
Comparative Analysis of Top Software Options
Feature Comparison
When evaluating manufacturing management software, a variety of features should be considered. Typical features include:
- Production Scheduling: Tools that help in organizing tasks efficiently.
- Inventory Management: Systems to track raw materials and finished goods.
- Quality Control: Programs designed for monitoring product quality throughout the manufacturing process.
Pricing Models
Pricing for manufacturing management software varies widely. Generally, models may include:
- Subscription-Based: Monthly or annual fees that provide continuous access to software updates and customer support.
- One-time Purchase: A fixed price paid upfront, which may entail additional fees for future updates.
Choosing the right pricing model depends on the organization’s needs and budget.
"Investing in manufacturing management software can yield significant returns by optimizing processes and reducing costs."
Preface to Manufacturing Management Software
In the contemporary industrial landscape, the demand for manufacturing management software has reached unprecedented levels. This software is critical as it streamlines operations and optimizes resources, which are vital for maintaining competitiveness in the market. Understanding its role is essential for decision-makers, IT professionals, and entrepreneurs who aim to enhance their operational efficiency.
Delving into the subject, one can observe several specific elements that underscore its importance. First, manufacturing management software consolidates various aspects of production, from planning to execution. This integration minimizes manual tasks that can be prone to error and inefficiency. For instance, software solutions often include features for scheduling, inventory control, and quality assurance, which collectively enhance productivity.
Moreover, the benefits of deploying such software extend beyond immediate operational improvements. A notable advantage is the surge in data accuracy and availability. With real-time data analytics, businesses can make informed decisions swiftly, ensuring alignment with market demands. This capability is particularly critical in industries where time-sensitive responses can greatly affect profitability.
However, the consideration of manufacturing management software also encompasses some challenges. These may include the costs associated with software acquisition and implementation, as well as the need for ongoing training of staff. Recognizing these hurdles is vital when evaluating the potential return on investment.
The right manufacturing management software not only enhances operational efficiency but also supports long-term strategic goals.
In summary, the introduction to manufacturing management software lays the foundational understanding of how such tools can propel organizations forward. From improving workflow efficiencies to enabling smarter decision-making, manufacturing management software is thus integral to achieving sustained operational excellence.
Overview of Manufacturing Management Concepts
Manufacturing management software is a significant aspect of modern production environments. It serves as the backbone for managing diverse processes efficiently. Ensuring these processes are well-managed is crucial for optimizing resource allocation and maintaining operational effectiveness. Thus, understanding manufacturing management concepts is essential for stakeholders.
Defining Manufacturing Management Software
Manufacturing management software refers to systems designed to streamline and optimize production processes. Such systems offer tools for planning, scheduling, and monitoring manufacturing activities. By applying these tools, businesses can improve productivity, quality, and consistency in their operations. This type of software integrates various functions, such as project management, inventory control, and supply chain oversight, into a single platform. This integration minimizes the time spent on administrative tasks, allowing managers to focus on strategic initiatives instead.
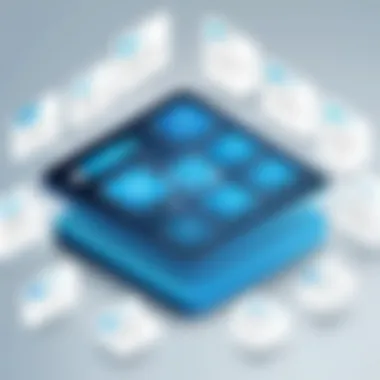
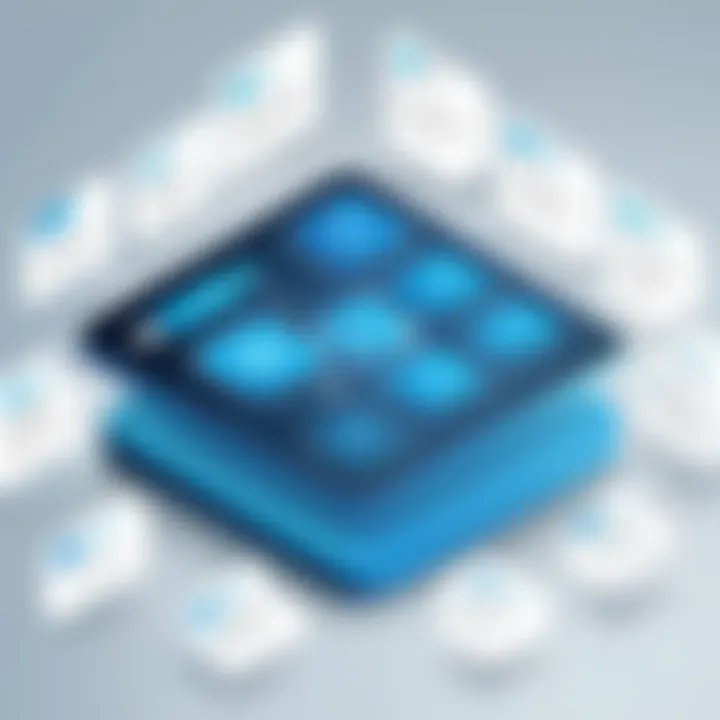
These systems also differentiate between various forms of manufacturing, including discrete, batch, and process manufacturing. A clear understanding of these distinctions aids organizations in selecting the appropriate software to match their specific needs. The flexibility of manufacturing management software caters to various industry requirements.
Key Features of Manufacturing Management Software
Key features of manufacturing management software include:
- Production Planning and Scheduling: This allows for efficient allocation of resources. It ensures that production meets demand without overcommitting resources.
- Inventory Management: This feature helps track raw materials and finished goods. Accurate tracking prevents stockouts and excess inventory.
- Quality Control: Embedded quality assurance modules monitor production to maintain standards. This inclusion reduces the risk of defects and recalls.
- Reporting and Analytics: Advanced reporting capabilities provide insights into operational performance. Dashboards and metrics help decision-makers evaluate processes and drive improvements.
- Supply Chain Management: This feature facilitates seamless communication between suppliers and manufacturers. It assists in synchronizing the supply chain with production schedules.
- User Interface: An intuitive user interface ensures ease of use for all personnel. A user-friendly system encourages adoption and reduces training time.
In sum, the evolution of manufacturing management software introduces sophisticated methodologies and efficiency standards. The software assists businesses in navigating challenges and improving overall performance.
Benefits of Manufacturing Management Software
Manufacturing management software provides numerous advantages that significantly enhance operations across various sectors. For decision-makers and professionals, understanding these benefits aids in optimizing manufacturing processes. This software has become crucial in increasing productivity, cutting costs, and improving overall satisfaction for both management and employees.
Enhanced Production Efficiency
One of the primary benefits of manufacturing management software is the boost in production efficiency. By automating processes, this software reduces the need for manual input and minimizes human error. Production timelines become more predictable, enabling factories to meet deadlines consistently. Moreover, these systems offer tools to analyze workflows, identify bottlenecks, and implement solutions effectively.
For example, software like SAP S/4HANA allows manufacturers to streamline their operations from order receipt to production and delivery. It integrates various elements of production and provides real-time visibility, making it easy to adapt quickly to changing demands.
Key aspects include:
- Automation of routine tasks: Saves time and reduces errors.
- Real-time tracking: Enables quick adjustments in production flow.
This efficiency often translates to increased output, allowing companies to capitalize on market opportunities quickly.
Improved Inventory Management
Effective inventory management is critical in manufacturing settings. Manufacturing management software facilitates improved inventory control by providing visibility into stock levels and demand forecasts. This enables businesses to maintain optimal inventory, avoiding both overstock and stockouts.
Using specific tools, organizations can analyze trends and demand patterns. Solutions like Oracle NetSuite provide advanced inventory capabilities, ensuring that materials are available when needed for production. Accurate inventory management directly correlates with cost savings and a reduction in waste, thus positively impacting the bottom line.
Consider these points:
- Accurate tracking: Reduces discrepancies and improves order fulfillment.
- Demand forecasting: Aligns inventory levels with market needs.
Improved inventory management enhances customer satisfaction because products are ready to ship when ordered.
Data-Driven Decision Making
Data-driven decision-making is imperative in today’s business landscape. Manufacturing management software offers organizations access to real-time data analytics, enabling informed choices based on up-to-date information. Decision-makers can leverage insights gleaned from production data to guide strategic planning, optimizing resources effectively.
Systems like Microsoft Dynamics 365 integrate analytics directly into the manufacturing process. This integration allows businesses to understand performance metrics and identify areas for improvement.
Benefits include:
- Informed strategies: Develop responses based on robust data.
- Risk management: Anticipate market shifts effectively.
By utilizing data-driven insights, manufacturers can maintain a competitive edge in a rapidly evolving industry.
Challenges in Implementing Manufacturing Management Software
Implementing manufacturing management software comes with a set of challenges that organizations must navigate effectively. Understanding these challenges is crucial for businesses aiming to harness the full potential of such systems. Missteps in this area can lead to wasted resources, inefficiencies, and even project failure. Hence, addressing the various challenges is a step towards ensuring successful integration of the software into existing processes.
Integration with Existing Systems
Integrating manufacturing management software with current systems is often a complex task. Firms frequently operate using various legacy tools and platforms that may have been in place for years. Each of these systems potentially houses critical data and processes that the new software must access or replace. The challenge lies in ensuring seamless data migration and interoperability between new and existing systems.
Common issues encountered include:
- Data Compatibility: Different systems may store data in incompatible formats, requiring transformation processes. This could delay implementation and increase costs.
- Diverse Software Environments: Utilizing multiple software solutions can create fragmentation. The new software must be able to function in conjunction with other tools effectively.
- Technical Roadblocks: Legacy systems might lack the flexibility needed for integration, leading to additional customization and development work.
Addressing these integration issues early in the planning stages is vital. Conducting a thorough system audit can reveal elements that warrant particular attention during integration processes.
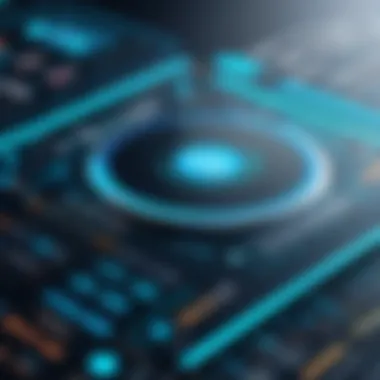
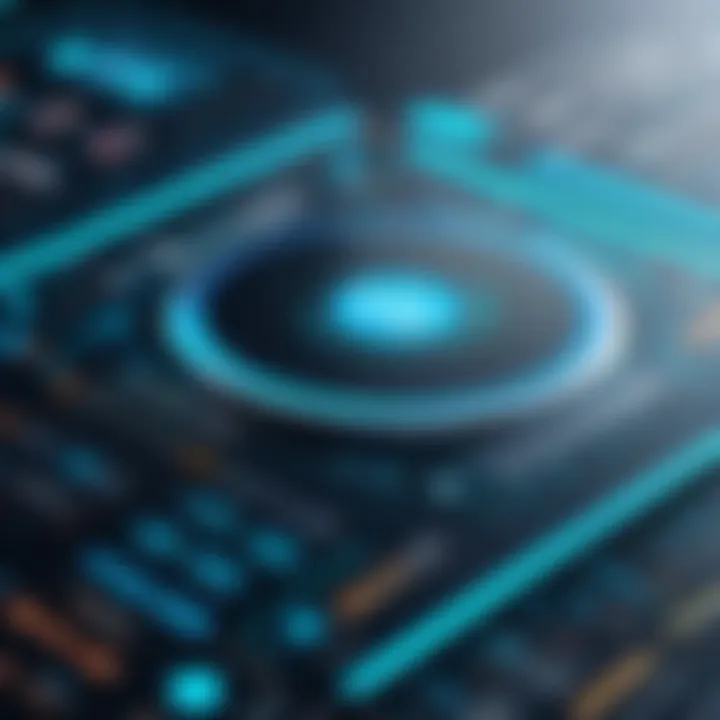
User Training and Adoption
Even the best software is only as good as its users. A critical challenge in implementing manufacturing management software is ensuring that all users are adequately trained and ready to adopt the new system. Resistance to change can derail initiatives and decrease productivity if not managed properly.
Essential aspects include:
- Training Programs: Develop comprehensive training sessions tailored to different user roles. Hands-on workshops can be more effective than just theoretical lectures.
- Change Management: Cultivate a culture that is open to change. Employees should understand the benefits and be encouraged to adapt positively.
- Ongoing Support: Post-implementation support is crucial. User forums, helplines, or dedicated support staff can make the transition smoother.
Training aimed at enhancing adoption not only improves overall satisfaction with the software but also maximizes the return on investment.
Cost Considerations
Financial implications of implementing manufacturing management software can be significant. Cost considerations are often a primary factor in decision-making and can influence the success of the implementation. Analyzing costs involves more than just the purchase price of the software. Organizations must also consider:
- Implementation Costs: These might include hardware upgrades, system integration, and potential consulting fees.
- Training Expenses: Preparing the workforce comes at a cost, and businesses need to budget for training materials and sessions.
- Ongoing Maintenance: Software requires regular updates and maintenance, which incurs recurring costs.
- Opportunity Costs: Consider the potential disruption during the transition period. Allocating staff time for training can impact productivity.
Overall, careful budgeting and a clear understanding of total costs can help mitigate financial risks associated with implementation.
"Managing the challenges of implementing software systems requires foresight and comprehensive planning."
Addressing these elements creates a foundation for effectively maneuvering through any challenges that arise during the implementation of manufacturing management software.
Current Trends in Manufacturing Management Software
The realm of manufacturing management software is continuously evolving, driven by the need for efficiency, speed, and precision in production. Staying updated on current trends is not merely beneficial; it is essential for decision-makers aiming to enhance operational capabilities and maintain competitiveness in a fast-paced market environment. This section delves into the pressing trends shaping manufacturing management software today, emphasizing their implications for businesses.
Cloud-Based Solutions
Cloud-based manufacturing management software enables companies to access their systems remotely, facilitating real-time collaboration and data sharing. A significant benefit of cloud solutions is the reduction in infrastructure costs. Businesses do not need to invest heavily in on-premises hardware or maintenance. Instead, they can leverage the capabilities of providers like Salesforce or Microsoft Dynamics 365, which offer scalable solutions tailored to specific manufacturing needs.
Moreover, the flexibility of cloud systems allows organizations to adapt quickly to changing demands. For instance, during unexpected surges in production, they can easily upscale resources without the lengthy process associated with traditional setups.
In addition, data security is enhanced through cloud services, as leading providers employ sophisticated encryption methods and compliance protocols to safeguard sensitive information. This aspect is crucial in a time when data breaches can have dire consequences. End-users can trust that their information is protected while benefiting from the latest software updates and features consistently.
"Cloud adoption is pivotal for businesses not only to increase operational efficiency but also to enhance their agility in responding to market changes."
Artificial Intelligence and Automation
The integration of artificial intelligence (AI) and automation technologies in manufacturing management software is reshaping how organizations operate. AI enhances decision-making by providing predictive analytics that can forecast demand, optimize supply chains, and identify potential bottlenecks before they impact production.
Automation, on the other hand, streamlines various processes, reducing human error and increasing productivity. For example, using robotic process automation (RPA) allows companies to automate repetitive tasks such as data entry or inventory checks. This enables human resources to focus on more strategic activities, thereby maximizing workforce potential.
Companies like Siemens and IBM are leading the way in AI research, providing tools that can adapt and learn from manufacturing processes. Such innovative approaches not only offer immediate efficiency gains but also position firms to compete effectively in an increasingly automated landscape.
Real-Time Data Analytics
Real-time data analytics is another trend gaining traction in manufacturing management software. This capability allows organizations to collect and analyze vast amounts of data instantly, leading to quicker and more informed decision-making processes.
With real-time analytics, manufacturers can track key performance indicators (KPIs) and operational metrics as they occur, enabling them to respond promptly to any fluctuations or issues. For instance, if there is a sudden decrease in productivity levels, immediate actions can be taken to investigate and resolve the problem. Tools like Tableau and Power BI are commonly used to visualize these insights, making complex data easier to digest.
Importantly, the implementation of real-time analytics can enhance transparency across the organization. Stakeholders can monitor progress and garner insights into operational performance, fostering a culture of data-driven decision-making.
Evaluating Manufacturing Management Software Options
Evaluating manufacturing management software options is a crucial step in selecting the right tools to enhance operational efficiency. The manufacturing sector is diverse and presents unique challenges that require tailored solutions. Decision-makers must consider various factors when assessing software options to ensure that they align with their specific operational needs.
A methodical evaluation can lead to improved productivity, better resource management, and more informed decision-making. Organizations that approach the selection process with rigor can minimize disruptions in their operations and harness the full potential of their investments.
Criteria for Selection
When it comes to selecting manufacturing management software, several key criteria should guide a decision-maker's choice. These include:
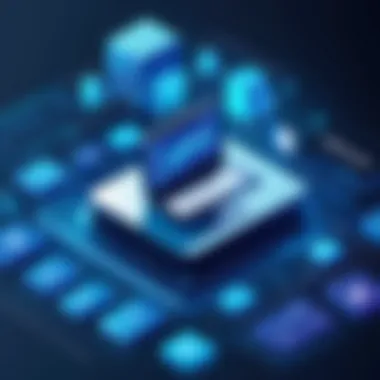
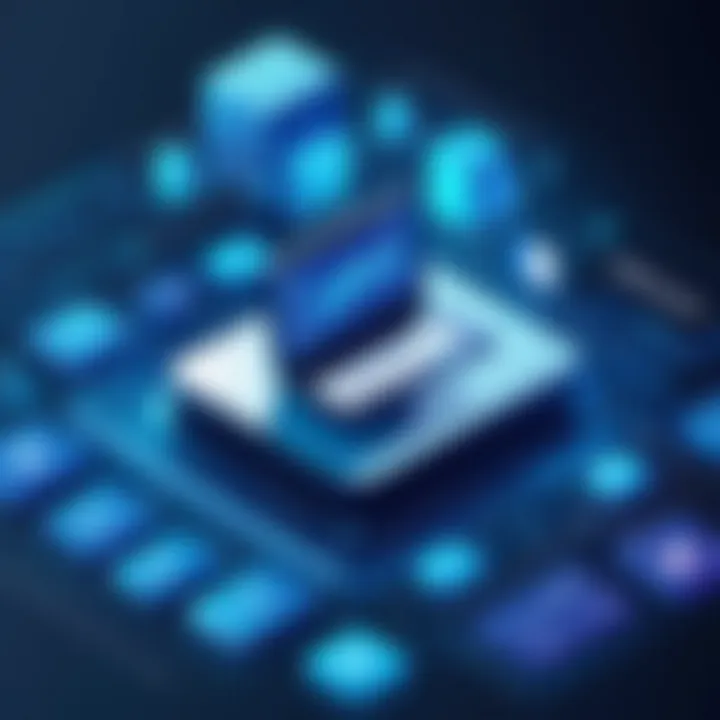
- Functionality: The software should support essential functions such as inventory management, production planning, and scheduling. Identifying core needs is vital.
- Scalability: A good software solution can accommodate growth. Businesses should consider whether the software can scale up as their operations expand.
- Integration Capabilities: The ability to integrate with existing systems such as ERP and CRM solutions is important. This ensures seamless data flow and reduced operational silos.
- User Experience: A user-friendly interface facilitates easier adaptation for employees, reducing the learning curve associated with new software.
- Support and Training: Vendors should offer robust support and training resources. This is essential to maximize utilization and reduce reliance on external support.
- Cost: A comprehensive understanding of total cost is significant. This includes licensing fees, maintenance costs, and potential costs for additional features.
These criteria ensure that the selected solution not only meets current demands but is also flexible enough to adapt to future challenges.
Vendor Comparison
A meaningful vendor comparison involves in-depth analysis across different software providers. Businesses should evaluate vendors based on:
- Reputation: Investigating the vendor's market presence and credibility helps in understanding their reliability and consistency.
- Reviews and Case Studies: Analyzing feedback from existing customers can provide insight into a vendor's strengths and weaknesses. Look for detailed case studies that illustrate successful implementations.
- Customization Options: Some companies require tailored solutions specific to their operations. Understanding how flexible a vendor is in terms of customization can provide a competitive edge.
- Technology Stack: Evaluating the underlying technology is essential. This includes reviewing the architecture, cloud capabilities, and potential for integrating advanced tools like AI.
- Demonstrations and Trials: Most reputable vendors provide demos and trial periods. Engaging in these opportunities allows decision-makers to gauge system performance and user friendliness.
The selection process for manufacturing management software is more than just a technical exercise; it reflects a business's strategic aspirations. Thorough evaluation ensures a smoother implementation phase, leading to long-term operational success.
Case Studies and Real-World Applications
Understanding how manufacturing management software can be applied in real-world scenarios offers valuable insights into its effectiveness and versatility. Case studies highlight practical implementations across various industries, showcasing tangible results and best practices. These real-world examples not only illustrate the software’s capabilities but also serve as a learning tool for decision-makers seeking to optimize their own manufacturing processes.
"Case studies reveal the real impact of technology in manufacturing, showcasing paths to success and cautionary tales of pitfalls."
Successful Implementation in Different Industries
The successful application of manufacturing management software can be observed in various sectors. For example, automotive manufacturers like Toyota employ sophisticated management software to streamline their production lines. This implementation supports real-time inventory management, yielding significant efficiency gains and reduced waste.
Another notable instance is in the electronics industry, where companies like Samsung leverage this software to regulate their supply chain. By integrating data from suppliers and production facilities, they can respond swiftly to demand fluctuations. This improves not only production efficiency but also customer satisfaction, as products are delivered timely.
In the food and beverage sector, companies such as Coca-Cola utilize manufacturing management systems to enhance quality control and compliance with regulations. This contributes to maintaining product integrity while optimizing production schedules.
Lessons Learned from Failed Implementations
Despite the advantages, there are cases where implementations of manufacturing management software have not gone as planned. For instance, a large textile manufacturing firm faced numerous challenges when integrating new software into outdated systems. Lack of proper training and users' resistance to change led to underutilization of the software's features, resulting in minimal improvements in productivity.
Another challenging case involved a company in the pharmaceuticals industry. The intention was to enhance traceability in their supply chain. However, poor communication with stakeholders and inadequate vendor support during the transition phase led to disruptions in the production process. As a result, they not only faced increased operational costs but also a decline in product quality.
These lessons underscore the importance of thorough planning, stakeholder engagement, and proper training. Without these elements, even the most advanced manufacturing management software can fail to deliver its promised benefits.
The Future of Manufacturing Management Software
The landscape of manufacturing management software is evolving rapidly due to advancing technologies and changing market needs. Staying informed about the future of this software is crucial for decision-makers. It offers insights into strategies that can enhance operational efficiency and drive growth. This section highlights key predictions regarding the evolution of the industry and examines emerging technologies that may revolutionize manufacturing management practices.
Predictions for Industry Evolution
Several trends indicate how manufacturing management software will transform in the coming years. First, the integration of Internet of Things (IoT) devices is expected to play a significant role. These devices can collect real-time data from machines and processes, allowing for better monitoring and control. As connectivity improves, manufacturers will leverage this data to enhance automation and predictive analytics.
Second, a shift towards personalization is anticipated. This means that manufacturing software will offer tailored solutions to meet specific business needs. Customization will allow organizations to create workflows that align closely with their operational requirements. Thus, the flexibility of the software will become a valued trait.
Furthermore, sustainability will be a key focus in the evolution of manufacturing management software. As environmental concerns grow, manufacturers will seek software solutions that minimize waste and optimize resource usage. The ability to track environmental impact through software will become crucial for compliance and corporate responsibility.
In sum, the future of manufacturing management software will likely revolve around IoT integration, personalized solutions, and sustainability considerations, shaping the way companies operate in a competitive marketplace.
Emerging Technologies
The rise of several emerging technologies will have substantial implications for manufacturing management software. One notable advancement is artificial intelligence (AI). AI algorithms can analyze vast amounts of data to forecast demand, optimize operations, and improve supply chain decisions. Utilizing these insights can lead to increased productivity and reduced costs.
Another trend is the growing use of blockchain technology. Blockchain can enhance transparency and traceability in supply chains. With secure and immutable records, stakeholders can trust the data, reducing disputes and errors in transactions. Manufacturers can utilize this technology to validate the authenticity and provenance of products, which is highly beneficial in regulated industries.
Moreover, augmented reality (AR) is making its way into the manufacturing sector. AR tools can provide real-time information and instructions to workers, improving training and enhancing maintenance procedures. By overlaying digital information onto the physical environment, AR can streamline processes and reduce errors.
Advancements in robotics and automation will also reshape manufacturing management. Companies will increasingly adopt collaborative robots or cobots that work alongside human workers. This synergy will enhance productivity and safety in the workplace, enabling companies to meet growing demands efficiently.
Closure
Key Takeaways
- Operational Efficiency: Leveraging this software allows companies to streamline processes, reduce waste, and ultimately improve overall productivity.
- Data-Driven Insights: The ability to harness data effectively leads to informed decision-making. Organizations that adopt this software can pivot strategies based on real-time analytics, a pivotal advantage in today's fast-paced markets.
- Scalability and Adaptability: Modern manufacturing management solutions offer flexible frameworks that can grow with the business. This adaptability is essential as industries face constant shifts in consumer demand and operational challenges.
Adopting manufacturing management software signals a strategic commitment to enhancing competitiveness. Nevertheless, it requires careful consideration of integration factors and thorough training for personnel to ensure a seamless transition.
"Investing in manufacturing management software is not just a choice; it is a necessity for companies wishing to remain relevant in an evolving landscape."
As organizations look ahead, staying attuned to emerging technologies and industry trends becomes increasingly important. Continuous evaluation of software solutions ensures that businesses do not merely keep pace but also lead in innovation within their sectors.