Exploring Inventory Management Software with BOM Features
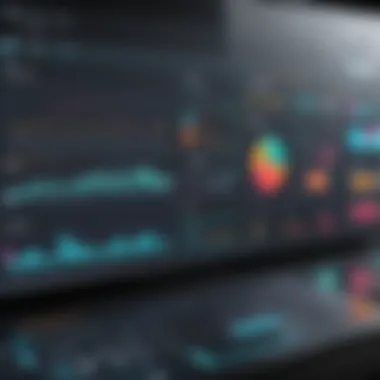
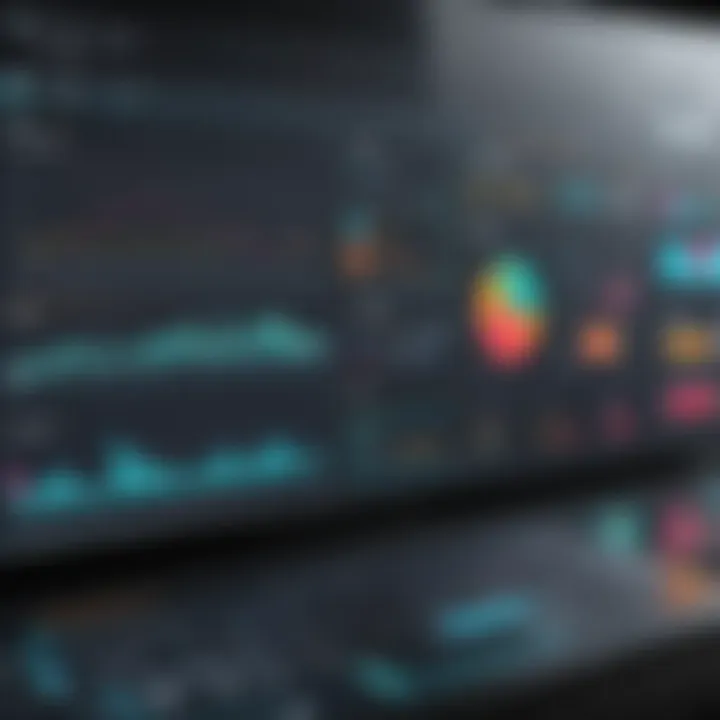
Intro
In today’s complex business landscape, a firm grasp of inventory management can mean the difference between profit and loss. As industries become more interconnected, the need for precision in managing stock levels, demand forecasting, and production scheduling has increased exponentially. Enter inventory management software—powerful tools designed to streamline operations and enhance decision-making.
One of the standout features of many of these software solutions is the integration of a bill of materials (BOM). This component acts as a roadmap, detailing the materials and components required to produce a finished product. It not only simplifies the production process but also ensures that every cog in the machine is running smoothly, which is vital for maintaining efficiency.
Understanding the intricacies of both inventory management software and the role of BOM is essential for decision-makers and IT professionals looking to improve operational efficiency. This article aims to dissect these tools, examining their characteristics, comparing leading options, and analyzing how they can boost production efficiency while aiding in informed decision-making.
By the end of this exploration, readers will have a clear perspective on the landscape of inventory management software and how the integration of BOM functionalities can drive success in their respective fields.
Understanding Inventory Management
Inventory management is the backbone of successful operations in most businesses, no matter their size or industry. It's the art and science of coherently overseeing the storage and flow of goods. The role of inventory management often gets sidelined when one thinks of more glamorous aspects of business like marketing or sales. However, without precise and strategic inventory control, even the best product can gather dust on shelves, incurring costs instead of profits.
In the context of integrating inventory management software with Bill of Materials, the importance magnifies. With a properly structured system, businesses can track their materials, understand supply needs, manage production levels, and meet customer demands more effectively. This alignment saves time and resources while ensuring that operations run smoothly and profitably.
Definition and Importance
To put it plainly, inventory management involves processes that help a company keep the right amount of product on hand, minimizing waste and maximizing profit. It encompasses everything from ordering, storing, and using a company's inventory. When risks like overstocking or stockouts are minimized, businesses can respond better to market demands and fluctuations. Essentially, it acts as a control mechanism. Just like a good captain steers a ship, efficient inventory management steers a business toward its goals.
Given the current fast-paced business climate, effective management of materials isn’t just nice to have—it's a necessity. Consider this: A recent survey suggests that businesses implementing robust inventory systems saw a reduction in carrying costs by nearly 20%. This kind of statistic speaks volumes about what effective inventory management can do for a company’s bottom line.
Key Principles of Inventory Management
When delving into inventory management, it’s vital to grasp several core principles that drive effective practices:
- Forecasting Demand: Predicting customer needs is critical. Businesses need to anticipate demand to manage inventory levels efficiently, ensuring they do not hold excess stock that ties up resources.
- Optimizing Stock Levels: Finding that sweet spot between overstocking and stockouts is vital to maintaining agility and responsiveness in the marketplace. Too much stock means wasted resources, while too little can leave customers high and dry.
- Categorizing Inventory: Not all items are created equal. Companies often segment their inventory into categories, such as high turnover or slow-moving goods. This helps prioritize where focus should be placed, especially when it comes to managing stock levels.
- Regular Inventory Audits: Keeping tabs on stock through frequent audits, whether they be cycle counts or full physical counts, can reveal discrepancies and issues before they balloon into larger problems.
- Utilizing Technology: Leveraging tools and software can facilitate better decision-making through real-time data tracking. The incorporation of Bill of Materials into inventory systems enhances this, providing more visibility into material requirements and production timelines.
"Efficient inventory management is a linchpin for operational success, bringing clarity amidst chaos in the ever-evolving landscape of business."
In sum, understanding inventory management isn’t just about keeping track; it’s fundamentally about enhancing business strategy. The complexities foster adaptability and ultimately define how effectively a company can pivot to market needs.
Defining Bill of Materials
Understanding the Bill of Materials (BOM) is crucial for anyone looking to streamline their inventory management processes. A bill of materials serves as a comprehensive list of raw materials, components, and assemblies needed to create a product. This makes it a foundational piece in both manufacturing and inventory control systems. The BOM not only details what is needed but often involves specifications like quantities, part numbers, and other vital data points.
Incorporating a BOM into inventory management helps to maintain a clear overview of what materials are on hand and what needs to be procured. This clarity can lead to various benefits, such as reducing waste, optimizing stock levels, and enhancing production planning. If you're in a fast-paced industry, having a reliable BOM means you are always a step ahead in decision making, whether that's knowing when to place orders or how to allocate resources efficiently.
By understanding what a BOM entails, businesses can significantly enhance their operational workflows and adapt to the ever-evolving market demands.
Components of Bill of Materials
A typical bill of materials includes several key components that serve as pillars for effective inventory management. Understanding these components is vital for making informed decisions:
- Item Number: Every item in the BOM should be assigned a unique number for easy identification. This helps in tracking and managing inventory without much hassle.
- Description: This provides a clear outline of the item, making it easier for warehouse staff and system users to understand what’s being referenced without ambiguity.
- Quantity: Indicating how many units of each item are required is essential to avoiding shortages or excess in stock.
- Unit of Measure: Whether items are tracked in pieces, kilograms, or liters, this ensures everyone in the organization is on the same page regarding measurements.
- Notes or Specifications: Providing additional information can be invaluable. For example, instructions regarding handling or specific quality requirements may prevent mishaps down the line.
- Parent-Child Relationship: In many cases, items in a BOM will have an hierarchical structure—some items will be components of a greater assembly. Clarifying this relationship helps in better organization and planning.
Types of Bills of Materials
Understanding the different types of bills of materials helps businesses select the right approach based on their operations:
- Engineering Bill of Materials (EBOM): Used during the design phase of a product, this BOM outlines the components needed to create the design.
- Manufacturing Bill of Materials (MBOM): This type focuses on the parts required in the manufacturing process. It's more oriented towards production and includes details on assembly processes.
- Sales Bill of Materials (SBOM): Primarily used for sales purposes, this BOM provides information regarding the final product that is offered to customers. It often highlights features that may be of interest to the buyer.
- Configurable Bill of Materials: Useful for customizable products, this allows selection of various options, which generates a BOM specific to a customer’s requirements.
Understanding these types allows decision-makers to choose the right BOM structure, aligning it efficiently with the company’s operations and goals.
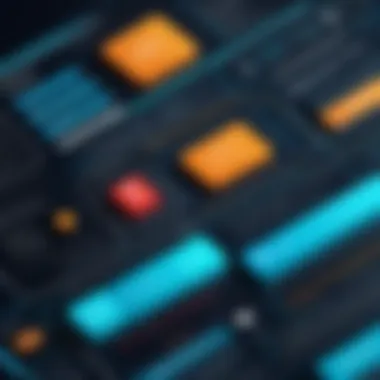

The Interconnection of Inventory Management and Bill of Materials
Understanding the relationship between inventory management and the bill of materials is like piecing together a complex puzzle. Each component plays a vital role in the broader picture of manufacturing and supply chain logistics. Combining inventory management with bill of materials can yield significant benefits, influencing everything from production efficiency to cost control.
Synergy Between Inventory and Production Processes
When one considers the synergy that exists between inventory management and bill of materials, it is clear how they complement one another. Inventory management focuses on maintaining optimal stock levels, while the bill of materials delineates what materials are needed for production. These two elements must work in harmony to ensure that production flows smoothly.
Engaging inventory management software that incorporates bill of materials can lead to seamless coordination. This means that when a production order is created, the software can automatically pull from inventory data to determine which materials are available and which are needed to meet production goals. In turn, by tracking materials through their lifecycle, companies gain insights that help in planning future inventory purchases more accurately.
To illustrate this point further, imagine a toy manufacturing company that uses a specific bill of materials for each type of toy it produces. The software helps in recording the number of toys produced, what materials were used, and how much inventory remains afterward. When the bill of materials gets updated – say, a decision is made to alter the plastic material for environmental reasons – it directly affects inventory levels and ordering patterns. By managing these changes in real-time, the company avoids production delays and excess inventory, saving money in the process.
Impact on Supply Chain Efficiency
The impact of integrating bill of materials into inventory management software reverberates through the entire supply chain. One of the fundamental principles of supply chain efficiency is having the right resources available at the right time. When inventory management systems are able to interact with bill of materials data, the results can be transformative.
For example, when businesses know exactly what materials are required for various production runs, they can better anticipate their purchasing needs and avoid rush orders that often come with inflated costs.
"Data accuracy ensures that what is produced matches the demand, thus keeping waste at bay and customer satisfaction high."
Key advantages include:
- Reduced Overhead: Knowing material requirements helps maintain minimal stock levels, which in turn reduces storage costs.
- Faster Response Times: As inventory levels fluctuate and production needs change, the integrated system provides real-time updates, allowing for immediate adjustments.
- Informed Decision-Making: Real-time data empowers decision-makers to forecast demand accurately, allowing them to adapt quickly as market conditions change.
The ability to visualize and respond to the needs of the supply chain remains imperative in today’s fast-paced market. When companies leverage the relationship between inventory management and bill of materials, they take a significant step towards optimizing their operations.
Benefits of Integrating Bill of Materials in Inventory Management Software
The integration of Bill of Materials (BOM) in inventory management software plays a pivotal role in optimizing various operational aspects. This connection is vital as it not only bridges the gap between material management and production but also helps streamline many processes that contribute to overall business efficiency. Understanding the specific benefits can empower decision-makers to view BOM not simply as a list of components, but as a core ingredient in their operational success.
Enhanced Accuracy in Tracking Materials
One of the key advantages of embedding BOM within inventory management software is the heightened accuracy it brings to tracking materials. This isn't just about knowing what you have on hand; it’s about having a real-time view that reflects actual consumption and stock availability. For instance, imagine a manufacturer creating complex machinery components. If their BOM is integrated with their inventory management software, any time a component is used, that usage is logged automatically. This prevents the dreaded 'out of stock' situation from creeping up, as managers can see precisely what remains in inventory.
Moreover, this integration minimizes manual data entries and the associated errors. Mistakes often occur when humans input data or when multiple systems aren’t synced up properly. With a properly integrated system, the data flows seamlessly between BOM and inventory management, ensuring that everyone is singing from the same hymn sheet, so to speak. Thus, organizations can significantly improve their order fulfillment and inventory turnover rates.
Improved Cost Management
Cost management throws its own set of challenges into the mix, and this is where an integrated BOM shines. By allowing businesses to see exactly how much each component contributes to the overall product cost, it facilitates more informed decision-making when it comes to purchasing and budget control. Imagine a small manufacturer that frequently pays the price for unnecessary overstocking or purchasing materials that are not needed right away. They can utilize BOM data to analyze purchasing patterns, leading to better supplier negotiations and smarter buying habits.
Equally important is the potential for less waste. When inventory management has insight into BOM and material usage, it helps businesses adjust their purchasing rates to better match actual production needs. This awareness can prevent tying up capital in excess inventory, thus freeing up cash flow for other business activities.
Streamlined Production Processes
A seamless interface between inventory management and BOM can drastically streamline production processes. For instance, consider a furniture maker who requires a variety of materials like wood, hardware, and fabrics for each product. When their BOM is directly tied into their inventory management system, any lag in material availability can be detected early, allowing for preemptive measures.
Moreover, this interconnectedness can highlight inefficiencies in the production line. If the system notes that certain components are frequently running low and causing downtime, management can shift resources or modify their production schedule accordingly. Such precision results in a smoother workflow, where each stage of production feeds into the next without unnecessary hiccups.
To reiterate, an integrated BOM can transform inventory management from a mundane task into a strategic advantage for businesses.
Choosing the Right Inventory Management Software
When it comes to choosing inventory management software, the stakes are high. Selecting the right tool can either make or break your operational efficiency. This isn't just about numbers on a screen; it’s about streamlining your entire business process. A well-chosen software can save hours of time, reduce errors, and support your growth. It's a real game-changer.
Critical Features to Consider
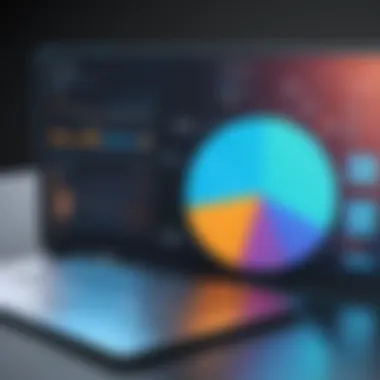
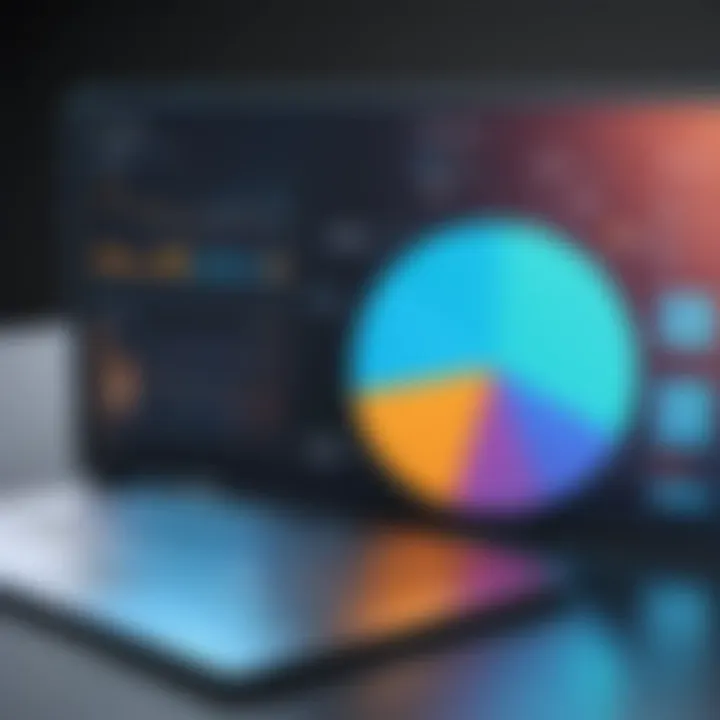
Before diving into the myriad of options out there, it's crucial to identify what features your business actually needs. Here are some key elements to focus on:
- Real-Time Tracking: Your inventory records should reflect real-time stock levels. Knowing precisely what you have on hand can prevent mishaps, like overselling items.
- Reporting and Analytics: A good software solution should provide comprehensive reporting tools. You need to analyze trends, spot discrepancies, and make data-driven decisions.
- User-Friendly Interface: If the software is clunky or complicated, employees won’t use it to its full potential. A clean, intuitive interface is essential.
- Mobile Access: In today's fast-paced environment, having access to inventory data via mobile is a must. It allows for quick updates on-the-go, which can be vital during stock counts or sales.
"Choosing the right inventory management software involves understanding the specific needs of your business while considering the features that will best support those needs."
Integration Capabilities
Another vital aspect to chew on is how well the software integrates with other systems. Whether it's an accounting system like QuickBooks or a sales platform like Shopify, seamless integration can save a world of headaches. Some vital considerations include:
- API Availability: Look for software that offers a robust API. This means you can easily connect it to your existing systems without needing to pull your hair out over complex configurations.
- Third-Party Integration: Consider how well the software works with third-party applications that your team relies on. A great example is connecting your inventory system with an e-commerce platform for automated stock updates.
- Scalability: Your business will grow; your software should grow with it. Ensure that it can accommodate more users, products, and integrations without requiring a complete overhaul.
Customization Options
Every business is unique, so the software should be as well. Having the ability to tailor software to fit specific business processes can set you ahead of the game. Considerations regarding customization options include:
- Flexible Workflows: Ensure the software allows you to modify workflows according to your business processes.
- Custom Fields: A software that lets you add custom fields helps capture unique data points relevant to your operations.
- User Roles and Permissions: Different employees have different needs. Being able to set custom user roles ensures that the right people have access to the right information without compromising security.
Choosing the right software doesn’t have to feel like navigating a minefield. It’s about understanding your business needs and matching them with the tools that can support and drive those needs forward.
Leading Inventory Management Software with Bill of Materials Feature
In today’s fast-paced market, effective inventory management isn’t just a luxury; it’s a necessity. When businesses incorporate bill of materials (BOM) functionality into their inventory management software, they witness significant transformations in their operations. The integration of BOM enables organizations to streamline production processes, enhance tracking capabilities, and ultimately improve cost management across the board.
Comparative Analysis of Top Software Solutions
When it comes to selecting the right inventory management software with BOM features, it’s crucial to conduct a thorough comparative analysis. Here’s a look at some of the leading solutions in the market:
- Fishbowl Inventory: This system provides a robust platform for managing inventory along with BOM. Its intuitive interface appeals to small businesses and larger enterprises alike. Fishbowl seamlessly integrates with existing accounting software.
- NetSuite: Known for its comprehensive enterprise resource planning capabilities, NetSuite’s inventory management includes an integrated BOM feature. It’s ideal for larger organizations needing scalability and advanced analytics.
- Zoho Inventory: A cost-effective choice for small to medium-sized businesses, Zoho includes solid BOM capabilities paired with easy-to-use tools for tracking inventory levels and managing stock.
Each of these solutions presents unique strengths and may cater to different business sizes and needs. A careful examination of their pricing structures, customer support, and scalability options can guide decision-makers in making a well-informed choice.
Features Comparison
To truly understand which inventory management software aligns best with business needs, evaluating specific features is paramount. Here’s a breakdown of crucial elements for consideration:
- Ease of Use: The user interface should be clear and intuitive. A steep learning curve can deter employees from utilizing the software effectively.
- Integration with Other Systems: Look for software that can easily mesh with existing tools, such as accounting systems or e-commerce platforms. The smoother the integration, the better the data flow.
- Customization Options: Each business has unique requirements. The ability to customize BOM details can significantly improve tracking accuracy and reporting capabilities.
- Reporting and Analytics: The software should offer robust reporting features that allow businesses to analyze material usage, inventory turnover, and production costs effectively.
- Scalability: As businesses grow, so do their needs. The chosen software should be able to accommodate expansion without requiring a complete overhaul.
"Choosing the right inventory management software is not just about what it can do today, but how well it will grow with the business tomorrow."
Ultimately, the right software should integrate BOM functionality, drive efficiencies in production, and support better decision-making for stakeholders. This enhances not only the operational side of businesses but their strategic direction as well.
Challenges in Implementing Inventory Management Software
Implementing inventory management software that incorporates functionalities such as the bill of materials can be a game-changer for many organizations. However, navigating the terrain is often fraught with challenges. Recognizing these obstacles early on is crucial. One of the most pertinent issues businesses encounter is resistance to change. Employees might prefer established processes and show reluctance in adapting to new technologies. Moreover, the complexity of integration with existing systems can pose additional hurdles. Whether it’s a legacy system or disparate software tools, ensuring smooth functionality can feel like walking a tightrope.
Alot of times, decision-makers underestimate the training needs involved in deployment. Without proper training sessions, employees might find themselves lost in a sea of new software features. This lack of proficiency can lead to subpar utilization, inadvertently negating any benefits the new system is meant to provide. Additionally, the costs associated with implementation often expand beyond initial budgets when one accounts for hidden fees, consultancy services, and ongoing maintenance. Thus, having a solid understanding of these challenges can pave the way for a smarter, more strategic implementation.
Common Pitfalls
When implementing an inventory management system, several common pitfalls can derail the process. Here are a few to keep in mind:
- Ignoring Stakeholder Input: Failing to involve team members from different departments can lead to a misalignment. Each user has specific needs that should be addressed.
- Underestimating Time Frames: A rushed implementation not only leads to frustration but also higher chances of errors. Expecting a quick rollout is often a recipe for disaster.
- Over-Complicating the System: Sometimes, businesses think that more features mean better solutions. However, overwhelming users with unnecessary complexities can hinder the process.
- Neglecting Data Quality: Transferring data from old systems often uncovers inaccuracies. Ignoring these issues will haunt you later.
These pitfalls can decrease user satisfaction and ultimately affect the return on investment for the organization.
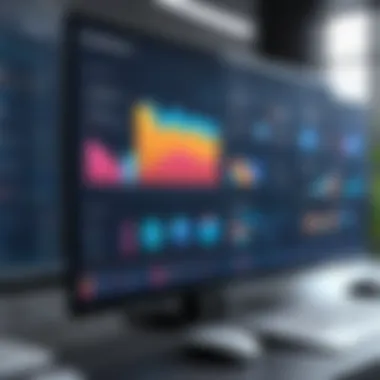
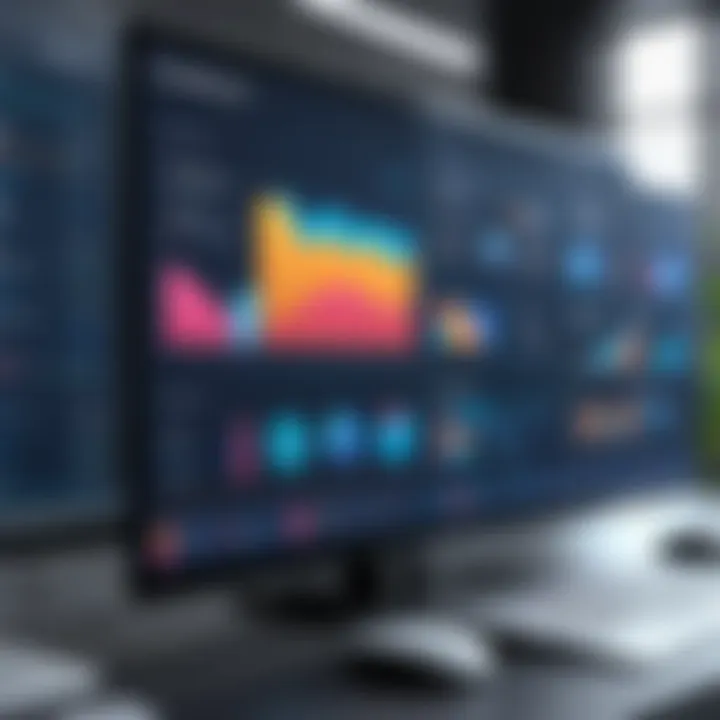
Strategies for Successful Implementation
To ensure a smooth rollout of the inventory management software, consider employing the following strategies:
- Conduct a Thorough Needs Assessment: Before diving headfirst into the software acquisition, gather input from various teams. Understand their specific workflows and needs, ensuring the chosen software aligns well with those requirements.
- Develop a Clear Timeline: Set realistic goals and deadlines. Create a timeline that accommodates training sessions and user feedback, enabling gradual adaptation.
- Invest in Comprehensive Training: Don't skimp on training. Provide several training sessions covering different aspects of the software. Also, ensure that there is ongoing support for new users to ask questions, fostering familiarity and comfort.
- Create a Data Management Plan: Assessment of current data quality is often overlooked. Develop a plan for cleaning and migrating data to ensure accuracy in your new system.
"An ounce of prevention is worth a pound of cure." Seeing to these small details in the beginning can save great headaches later.
- Monitor and Adjust Post-Implementation: After the system goes live, don’t kick back and relax. Monitor the utilization and gather user feedback regularly to tweak and adjust processes as necessary.
By actively engaging these strategies, organizations will not only ease the transition but also set themselves up for long-term success with their inventory management software.
Future Trends in Inventory Management and Bill of Materials Software
In today’s fast-paced economic environment, it’s crucial for businesses to stay ahead of the curve, particularly in inventory management and bill of materials sectors. As technology evolves, there are some trends developing that are bound to reshape how organizations approach these critical functions. Understanding these trends can arm decision-makers with valuable insights that enhance operational efficiency, reduce waste, and drive profitability.
Technological Advancements
One of the most poignant shifts in inventory management software is the steady march of technological advancements. Companies are increasingly leveraging automation and artificial intelligence to streamline their workflows. For instance, predictive analytics is becoming commonplace. This technology helps businesses forecast demand with impressive accuracy, thus allowing them to optimize their inventory levels and reduce excess stock holding.
Another notable trend is integrating Internet of Things (IoT) devices into inventory systems. Sensors attached to inventory items can provide real-time data about stock levels, location, and condition. This real-time monitoring not only enhances visibility but also empowers businesses to make quicker and more informed decisions. The blend of IoT and bill of materials is particularly beneficial as it allows for precise tracking of components, greatly reducing errors in assembly that often arise from manual human input.
Moreover, cloud computing continues to be a game-changer. It enables businesses to access their inventory management systems from anywhere, leading to better collaboration among teams and suppliers. The flexibility offered by cloud-based solutions also means that businesses can scale their operations up or down without worrying about the underlying infrastructure.
"To stay competitive today, companies must embrace a technology-first mindset that emphasizes agility and responsiveness."
These advancements translate into significant cost savings over time. When transitioning to these technologies, organizations should prepare for initial investments, knowing that the long-term rewards will justify them.
Shifts in Industry Practices
As technology progresses, industry practices are evolving too. One ongoing shift is towards sustainability. Businesses are now focusing on environmentally friendly practices not only in production but also within their inventory management strategies. This means adopting systems that reduce waste and improve efficiencies, which can also resonate positively with today’s eco-conscious consumer.
Moreover, there is a growing recognition of the importance of cross-departmental integration. Traditionally, inventory management existed in silos. However, recent trends advocate for open lines of communication between departments like purchasing, sales, and production. This helps in better aligning inventory levels with actual demand, thus minimizing stockouts and overstock scenarios.
In addition, the shift towards agile methodologies impacts inventory management practices. Businesses are, more than ever, prioritizing agility in their supply chain operations. This approach allows them to adapt quickly to shifting market demands. For instance, a company might start sourcing materials from alternative suppliers in response to disruptions in the supply chain. Timely updates to the bill of materials in their systems enable businesses to implement these changes effectively.
Ultimately, recognizing and adapting to these shifts is paramount for any organization looking to maintain a competitive edge.
In summary, staying aware of trends in inventory management software and bill of materials integration enables firms to not only enhance their operational capabilities but also align with industry best practices. As we scrutinize further improvements in the coming years, it becomes increasingly clear that businesses willing to adapt will reap substantial benefits.
Culmination
In the landscape of modern business, mastering inventory management integrated with a robust bill of materials (BOM) functionality is paramount. It isn't merely about tracking items or counting stock; it's about smartly orchestrating resources to augment productivity and efficiency. This article has explored the intricate interplay between inventory management software and BOM functionalities, uncovering the layers of complexity and the wealth of advantages this integration brings.
Summarizing Key Takeaways
A. Enhanced Visibility: The gut feeling that inventory is just right is often misleading. Using advanced inventory management systems that incorporate BOM helps maintain an accurate, real-time picture of stock levels, ensuring businesses are never caught flat-footed.
B. Cost Efficiency: Money doesn't grow on trees, and businesses are certainly aware of this. By optimizing material usage through effective BOMs, organizations can significantly minimize waste and reduce costs.
C. Smoother Production Flow: Nothing derails a production line faster than a missing part. A well-structured BOM embedded within inventory management software can foresee potential bottlenecks, keeping production running like a well-oiled machine.
D. Data-Driven Decisions: Gone are the days when businesses relied on gut instinct. Now, data reigns supreme. The insights gained from sophisticated inventory systems allow decision-makers to strategize, plan, and act with confidence.
Final Thoughts on Software Selection
Selecting the right software isn't just about features on paper—it's about aligning tools with business goals.
- Identify Core Needs: Understand the specific challenges your business faces and seek a software solution that addresses these head-on. Whether it's quantity tracking or procurement strategies, knowing what you need is half the battle.
- Evaluate Integration: Any software can promise convenience, but true prowess lies in how well it integrates with existing systems. An ideal choice will offer seamless connectivity with other tools like ERP systems.
- Consider Customization: No two businesses are exactly alike. Ensure that the software you choose can be tailored to fit your unique processes. Popular tools like SAP Business One or Fishbowl Inventory offer varied customization options.
- Test Before You Commit: A trial period can reveal a lot. It's one thing to hear about functionality; it's another to see it in action within your environment. Don't hesitate to take a test drive.
"The right software is like a well-fitted suit; it should enhance your strengths while accommodating your unique shape."