In-Depth Analysis of QAD Warehouse Management System
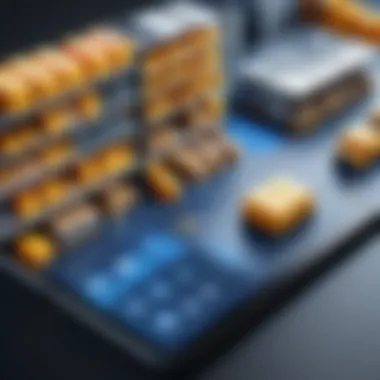
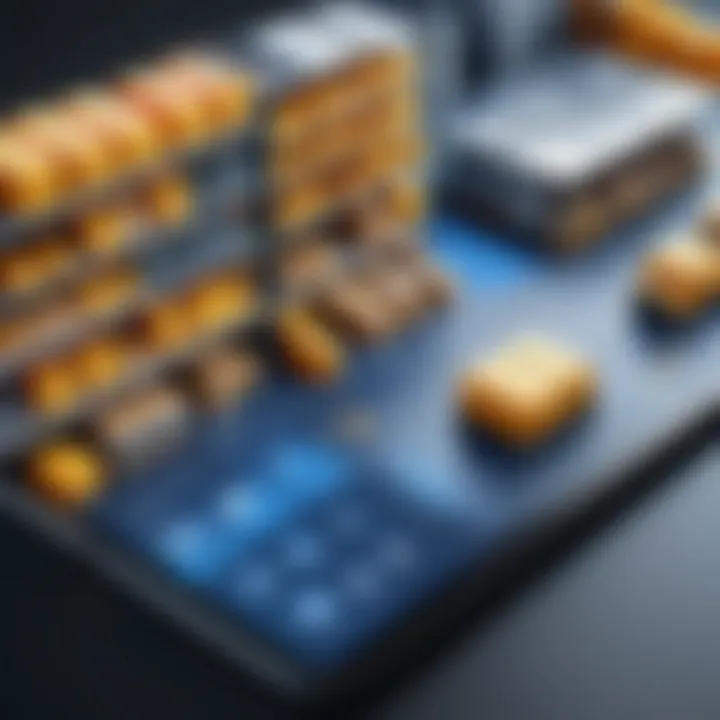
Intro
In today's rapidly changing business landscape, managing warehousing and logistics efficiently has become essential for companies to thrive. Enter the QAD Warehouse Management System (WMS), a robust tool designed to streamline warehouse operations and enhance supply chain efficiency. From its integral features to its seamless integration with enterprise resource planning (ERP) systems, the QAD WMS stands out as a valuable asset for decision-makers and IT professionals aiming to bolster their organizational frameworks.
This article seeks to unpack the intricacies of QAD WMS. We will explore its definition and importance, key characteristics, and how it compares to other software options on the market. With insights into pricing models and feature comparisons, this guide aims to provide stakeholders with the knowledge necessary to leverage this system for improved supply chain strategies.
Intro to QAD Warehouse Management System
In todayās fast-paced business environment, effective management of warehouse operations is more than just a necessity; it is a strategic advantage. The QAD Warehouse Management System (WMS) stands at the forefront in providing solutions tailored specifically to streamline operations. Understanding the functionality and benefits of QAD WMS is crucial for decision-makers and IT professionals wanting to optimize their supply chains.
Definition of QAD Warehouse Management System
The QAD Warehouse Management System is a software platform that governs and oversees various warehousing tasks. This encompasses everything from inventory tracking to order fulfillment and shipping. By integrating this system, businesses can automate processes, reduce errors, and enhance visibility across the supply chain. What is vital here is how QAD WMS adapts to unique organizational needs, thanks to its configurability.
In essence, QAD WMS transforms data into actionable insights, thus aiding in better decision-making. It connects different functional areas, ensuring that every departmentāfrom sales to inventoryāworks on the same page. Itās like having a conductor for an orchestra; every player knows when to come in, resulting in a harmonious outcome.
Purpose and Importance of WMS
The central role of a Warehouse Management System such as QAD lies in its ability to optimize internal processes. Here are some specific elements that highlight its importance:
- Efficiency Improvement: The system efficiently handles logistics tasks, reducing the need for manual intervention, which can lead to human error.
- Inventory Accuracy: With real-time tracking, businesses can keep accurate counts of stock levels, eliminating discrepancies that can disrupt operations.
- Customer Satisfaction: Fast and accurate order fulfillment translates to happier customers. When orders are processed correctly and swiftly, the overall customer experience improves.
- Cost Control: By streamlining operations, organizations can significantly reduce overhead costs associated with labor and storage.
"In many ways, the QAD WMS isnāt just a tool; itās a compass guiding businesses through the often chaotic terrain of supply chain logistics."
In essence, embracing QAD WMS is not merely about adopting a new tool; itās about driving a shift in operational mindset. For modern organizations looking to remain competitive and agile, a solid understanding of QAD WMS and its implications is paramount.
Core Features of QAD WMS
Understanding the core features of the QAD Warehouse Management System (WMS) is crucial for any organization looking to streamline its warehousing operations. These features not only define the system's capabilities but also play a vital role in enhancing productivity, optimizing inventory turnover, and ultimately improving the bottom line. Todayās supply chain is heavily reliant on precision and speed, and QAD WMS aims to deliver on those fronts.
Inventory Management
Effective inventory management is the cornerstone of any successful warehouse operation. QAD WMS offers advanced tools to track inventory levels in real-time, which helps in minimizing stock discrepancies. By leveraging barcode scanning, RFID technology, and automated data capture, organizations can maintain accurate stocked items without breaking a sweat.
Furthermore, features like cycle counting and automated stock replenishment ensure that the warehouse operates smoothly. When stock levels fall below a certain threshold, the system can automatically trigger reorders, which reduces the risk of stockouts. Organizations can run on a just-in-time basis, significantly saving on carrying costs.
"Accurate inventory management is like finding a needle in a haystack, but with QAD WMS, that needle is marked and easy to pluck out."
- The ability to integrate inventory data with sales orders allows for a more synchronized approach to fulfillment, thus improving overall operational efficiency. Automated reporting can forecast demand trends, enabling smarter decisions about inventory purchasing and storage.
Order Processing
Order processing is another key feature that lays the groundwork for customer satisfaction. QAD WMS simplifies the handling of incoming orders, from order acceptance to shipment. One of its standout capabilities is the automation of order picking processes. Algorithms determine the most efficient picking paths, reducing the time spent in aisles. Think of it like having a personal GPS for your warehouse.
Additionally, the system allows for batch processing, meaning multiple orders can be handled simultaneously, further expediting the fulfillment process. Advanced tracking features keep users informed about order statuses, helping to manage customer expectations effectively. Accurate order fulfillment reduces returns, thereby saving both time and resources.
Shipping and Receiving
Shipping and receiving capabilities in QAD WMS are designed to ensure that products move through the warehouse as smoothly as possible. When goods arrive, the system allows for swift processing of incoming shipments. Each item can be scanned upon arrival, updating the inventory database instantaneously, thus closing any gaps in tracking.
Moreover, shipping functionalities include the preparation of shipping labels and the generation of necessary documentation, ensuring compliance with carriers' requirements. Integrated route optimization can also be part of the solution, where the system suggests the best logistical routes based on traffic patterns and delivery timeframes.
In summary, each core feature of QAD WMS complements the others, leading to a cohesive system that can transform warehouse operations. By focusing on inventory management, order processing, and shipping and receiving, organizations can unlock a host of benefits including increased efficiency, reduced costs, and enhanced customer satisfaction. This comprehensive structure offers an accessible roadmap for decision-makers and IT professionals aiming to elevate their operations.
Integration with ERP Systems
In todayās complex and fast-paced business environment, organizations strive to create seamless flows of information across all departments. The integration of QAD Warehouse Management System (WMS) with Enterprise Resource Planning (ERP) systems plays a pivotal role in achieving that goal. When these systems communicate effectively, a business can experience heightened accuracy, optimised processes, and ultimately greater operational agility.
How QAD WMS Integrates with ERP
Integrating QAD WMS with ERP involves connecting various modules, allowing them to share data in real time. This connection fosters a more cohesive operational framework. For instance, information related to inventory levels, order status, and shipment tracking can be accessible simultaneously across both platforms. The integration is generally facilitated through Application Programming Interfaces (APIs), which act as intermediaries enabling different software programs to talk to each other.
It's not just about technical architecture; it's also about understanding business workflows. For instance, when a sales order is entered into the ERP, that information can trigger inventory checks in QAD WMS, ensuring that stocks are available before committing to the sale. The real-time data exchange allows for:
- Improved accuracy in inventory tracking.
- Faster processing of orders.
- Streamlined financial reporting, as all data reflects real-time business activities.
When correctly integrated, tracking items becomes almost effortless, as the barcode or RFID data collected at the warehouse flows seamlessly into the ERP for accounting and analysis.
Benefits of Integration
Integrating QAD WMS with ERP offers far-reaching benefits. These advantages can change the game for many organizations trying to enhance their operations.
"Integration fosters collaboration and helps in aligning data across departments, leading to better decision-making."
Notably, here are the major benefits one can anticipate:
- Enhanced Visibility: Visibility into the supply chain dramatically increases when both systems work in tandem. Decision-makers can gauge the flow of goods from procurement to delivery, thereby informing strategies.
- Operational Efficiency: Streamlined processes reduce time wasted on manual data entry, leading to a quicker response to market demands. An efficient warehouse translates to timely deliveries and elevated customer satisfaction.
- Cost Savings: By minimizing errorsāsuch as overstocking or stockoutsāintegrated systems facilitate better inventory management. These efficiencies can lead to a significant reduction in overhead costs.
- Data-Driven Insights: Unified data pools enable more comprehensive analytics that can reveal patterns and trends leading to informed business strategies. For example, sales forecasts can be better aligned with inventory availability, reducing excess waste.
- Scalability: As a business grows, integrated systems can grow alongside them without extensive overhauls, thereby protecting earlier investments in technology.
In summary, a marriage between QAD WMS and ERP systems doesnāt just enhance functionality; it opens doors to new opportunities for growth, innovation, and competitiveness. Establishing this link requires a considered approach, careful planning, and investment, but the rewards for organizations that pursue this path are well worth the effort.
Benefits of Implementing QAD WMS
The implementation of QAD Warehouse Management System carries significant weight in optimizing warehouse operations. This section outlines how adopting QAD WMS can lead to tangible benefits for businesses. Not just any benefits, but crucial ones that resonate well with their overall supply chain strategy. From efficiency boosts to meaningful cost reductions, these advantages shape the landscape of modern warehousing.
Improved Efficiency
When we talk about improving efficiency, it's like talking about finding a needle in a haystack, except now the haystack is organized. QAD WMS automates various processes, leading to a smoother workflow.
- Inventory Control: By utilizing real-time data, inventory levels always reflect accurate counts. This minimizes the risk of stockouts and overstocking.
- Order Fulfillment: The accuracy of fulfilling orders sees a sharp uptick. By streamlining picking and packing processes, QAD WMS ensures that orders leave the warehouse expeditiously and correctly.
- Resource Allocation: Task management is also significantly enhanced. Staff can be allocated more effectively, ensuring that all resources are utilized optimally.
With these enhancements, businesses find that their operational throughput can increase substantially, which ultimately leads to satisfied stakeholders.
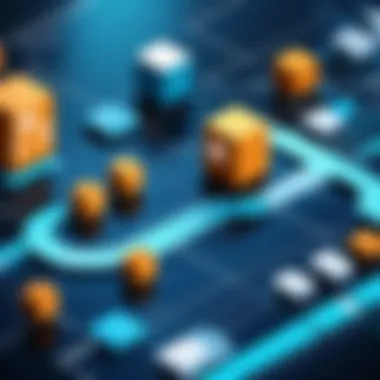
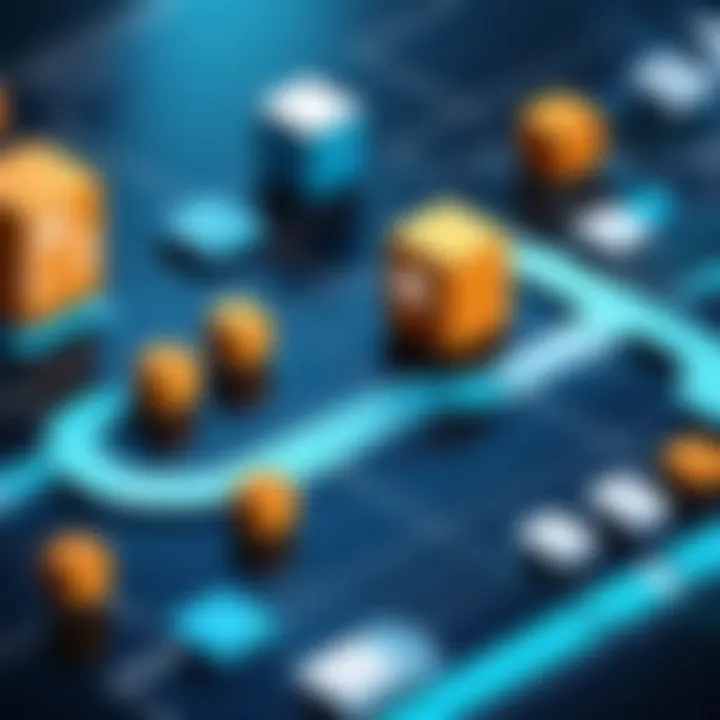
Cost Reduction
Let's not beat around the bush; cost reduction is often a major driving force behind any business decision. Enabling cost-effective practices through a robust WMS, like QAD's, is paramount in achieving better margins.
- Labor Costs: With automated processes, thereās less reliance on manual labor, helping to trim expenses.
- Error Reduction: The decrease in mistakes leads to fewer returns and less waste, which saves money in the long run.
- Inventory Management Costs: Efficient inventory practices lower storage expenses and decrease the capital tied up in unsold goods.
In a nutshell, businesses often discover that implementing QAD WMS translates into noticeable cost savings that allow reallocating budget to more critical areas of growth.
Enhanced Customer Satisfaction
Let's face it, in today's world, customer satisfaction is the name of the game. QAD WMS does wonders in this department by allowing companies to meet customer expectations consistently.
- Faster Delivery Times: With a more streamlined order fulfillment process, customers receive their orders more swiftly than ever.
- Accurate Orders: Fewer errors mean customers get exactly what they ordered, increasing trust in the brand. Customers don't like surprises when it comes to deliveries and orders.
- Improved Communication: QAD WMS provides features that keep customers in the loop. With tracking capabilities, they can know where their orders are, leading to a better customer experience.
As a result, businesses leveraging QAD WMS often find that they attract and retain more customers, driving repeat business and fostering loyalty.
"An efficient warehouse is like a well-oiled machine; components working together lead to success."
Challenges in Warehouse Management
Warehousing is often described as the backbone of supply chain operations. However, it's not without its own hurdles. Understanding the challenges faced in warehouse management is crucial for organizations aiming to maintain an edge in todayās fast-paced business world. These challenges not only affect daily operations but also influence overall efficiency, customer satisfaction, and profitability.
It's essential to discuss the common issues that plague warehouses, as well as the methodologies for overcoming resistance to change, so that leaders can foster a more agile and responsive environment.
Common Issues Faced
Several common issues tend to crop up in the warehouse management landscape. These can stem from several factors including shifting market demands, technology limitations, and operational inefficiencies. Here are some prevalent challenges:
- Inaccurate Inventory Management: Itās a headache when stock levels donāt match whatās in the system. Miscounts can lead to either overstocking or understocking, impacting not just storage costs but also customer fulfillment.
- Labor Shortages: Finding skilled labor can feel like searching for a needle in a haystack. Higher turnover rates often frustrate training efforts, making it hard to keep a consistent team that knows the ropes.
- Inefficient Layout and Picking Processes: A warehouse thatās not organized can waste precious time. If items are stored without thought, it can lead to workers running around like headless chickens, dramatically increasing picking times.
- Equipment Failures: Breakdowns in machinery or software may halt operations, leading not only to delays but also significant financial losses.
- Compliance Issues: Regulations and standards, whether related to safety or inventory practices, are complex. Non-compliance can land businesses in hot water, incurring penalties that do more than just dent a budget.
In short, these obstacles make it essential for businesses to proactively identify and address issues in warehouse management to keep the operations running smoothly and efficiently.
Overcoming Resistance to Change
Change is often met with skepticism in any organization, particularly in operations as established as warehousing. Employees may cling to familiar routines, fearing that new methodologies might disrupt their daily workflow. To navigate these waters, it's crucial to engage employees in the change process. Here are some strategies to help overcome resistance:
- Communicate Clearly: Transparency goes a long way. Keep everyone in the loop about why changes are happening and how they will benefit the operation. Clear communication can help ease fears and foster a sense of ownership.
- Involve Employees in Decision Making: When employees feel their voices are heard, they tend to be more receptive to change. Gathering input on how to implement new systems can be empowering.
- Provide Training and Support: Change can feel overwhelming. Offering ample training and support reassures employees that theyāre not just being thrown into the deep end. Addressing concerns shows a commitment to their professional growth.
- Pilot Programs: Rather than implementing sweeping changes all at once, consider running pilot programs. Small-scale tests can show the merits of new systems without jeopardizing the entire operation.
- Celebrate Small Wins: Recognition boosts morale. Celebrate achievements, big or small, to show that improvements are being made and the effort is paying off.
"The only constant in life is change." Understanding this principle can help organizations strategically embrace shifts in warehouse management, allowing for innovation even amidst uncertainty.
Technological Innovations in QAD WMS
In todayās fast-paced supply chain arena, technological innovations play a vital role in enhancing the efficiency and effectiveness of warehouse management systems (WMS). QAD WMS is no exception. With advancements in technology, QAD has integrated various innovative solutions to streamline operations, thereby allowing businesses to cater better to their customer needs. Understanding these innovations can be the key to unlocking the full potential of warehouse management.
Role of Automation
Automation has become a game-changer in warehouse settings, particularly in the QAD WMS landscape. By automating routine tasks, warehouse staff can focus on more critical functions, thus enhancing productivity.
- Inventory Management: Automated systems help maintain real-time inventory records. This reflects accurate stock levels, reducing the chances of overstocking or stockouts. Itās no longer just about keeping a tally; itās about having the data at oneās fingertips.
- Order Fulfillment: Automation in order processing leads to faster and more accurate picking and packing. This diminishes human error and improves the overall speed of operations. When efficiency is crucial, each second saved adds up.
- Data Analysis: Automated data collection allows warehouses to generate insightful reports. These reports can guide decision-making, indicating trends, and forecasting needs.
While automation introduces substantial efficiency gains, it doesnāt come without its challenges. Warehouse managers must ensure staff are equipped to work alongside new technologies, which sometimes creates reluctance. The key is a balanced approach, embracing the benefits while facilitating a smooth transition for personnel.
Utilization of Artificial Intelligence
Artificial Intelligence (AI) is progressively being recognized as an essential component in modern warehouse operations. QAD WMS capitalizes on AI for delivering intelligent insights and automating repetitive tasks further.
- Predictive Analytics: AI algorithms analyze historical data to forecast inventory needs accurately. Predictive analytics can significantly reduce waste and ensure that businesses are prepared for surges in demand.
- Enhanced Decision-Making: AI assists in making data-informed decisions. By assessing trends and performance metrics, it can recommend operational adjustments, which are pivotal for maintaining efficiency.
- Robotics and Autonomous Vehicles: AI-driven robots can handle materials within the warehouse, reducing manual labor and enhancing safety. These automated systems can operate around the clock, ensuring less downtime and more efficient use of space.
"Technology is best when it brings people together and enhances the work environment, particularly in the bustling world of logistics."
In essence, technological innovations in QAD WMS ā through automation and artificial intelligence ā are not merely enhancements but fundamental shifts in how warehouse operations are run. Such advancements create a more agile supply chain, ready to respond to the ever-changing marketplace. As technology continues to evolve, so too does the need for companies to adapt and harness these changes to remain competitive.
User Experience and Usability
In the realm of warehouse management systems, user experience (UX) and usability are not mere enhancements; they are central to fostering a productive environment. A system that is intuitive and easy to navigate can lead to greater efficiency, less training time, and fewer errors. QAD WMS prioritizes these aspects, understanding that even the most sophisticated functionalities won't see their full potential if users can't engage with them effectively.
By focusing on user experience, QAD WMS ensures that its interface caters to both seasoned professionals and newcomers alike. The ease with which a user can adapt to and utilize the system can significantly impact operational performance. A seamless experience not only boosts morale but also translates directly into enhanced productivity. Therefore, companies looking to implement QAD WMS must pay close attention to these elements.
Interface Design of QAD WMS
The interface design of QAD WMS is a crucial factor that influences the overall user experience. It's crafted with a clean and organized layout that facilitates easy navigation. Icons and menus are logically arranged, enabling users to find the tools and information they need without a hassle. For example, the dashboard provides an at-a-glance view of crucial metrics, helping users to monitor inventory levels, order statuses, and shipping updates without having to dig through multiple screens.
Colors and fonts are chosen carefully to reduce strain, with high contrast ensuring that important information stands out. The interface is responsive, functioning smoothly across various devices, which is vital for users who access the system on tablets or mobile devices while in the warehouse.
Customization options allow users to tailor their interface to their needs, further enhancing usability. This adaptability not only meets different user preferences but also accommodates specific workflow requirements. By involving end-users in the design process, QAD effectively addresses their needs, creating a system that feels intuitive and friendly.
Training for End Users
When it comes to implementing any sophisticated software like QAD WMS, effective training is an essential piece of the puzzle. No matter how well-designed the interface may be, the system's success hinges on the users' ability to leverage it fully. A robust training program prepares users for common tasks, integrates their existing knowledge into new processes, and addresses potential challenges they may encounter during day-to-day operations.
Training should begin with an understanding of user rolesādifferent jobs will engage with the system in varied ways. For instance, inventory managers may need to focus on stock tracking and reporting, while logistics coordinators would concentrate on shipping workflows. A tailored training approach recognizes these differences, offering each user group the tools specific to their functions.
Hands-on training sessions are particularly effective. When employees can interact with the QAD WMS in a controlled environment, they gain the confidence and familiarity needed to explore the system in real scenarios. Additionally, on-demand resources such as video tutorials and manuals can be invaluable for reinforcing training concepts and providing ongoing support.
Successful warehouse management through QAD WMS relies on a well-executed training plan, enabling users to fully realize the softwareās potential.
Case Studies of QAD WMS Implementation
Exploring case studies related to QAD Warehouse Management System (WMS) implementations serves as a powerful tool for understanding the real-world applications and outcomes of this technology. These case studies not only offer insight into what success looks like but also provide valuable lessons on potential pitfalls. By examining varied implementations, decision-makers and IT professionals can glean practical knowledge that helps them navigate their own deployment processes more effectively.
Successful Implementations
Successful deployments of QAD WMS can be seen across different industries, where companies have harnessed its features to optimize logistics, reduce costs, and improve customer service. Take, for instance, a prominent retail company that integrated QAD WMS to streamline its order processing systems. By leveraging the system's capabilities, they reduced order fulfillment times by 40%. The result was not just faster delivery, but also improved customer satisfaction and repeat purchases.
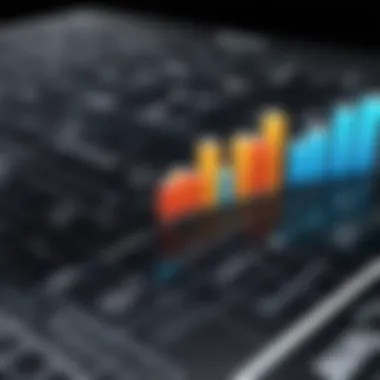
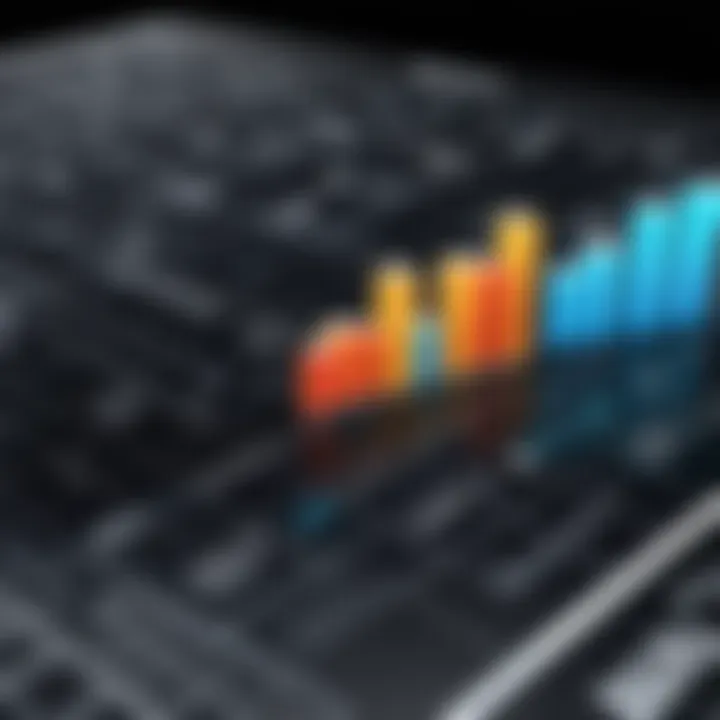
Another noteworthy example comes from an automotive parts manufacturer. Initially struggling with inventory accuracy and excess waste, the organization adopted QAD WMS which allowed for real-time inventory tracking. As a result, they had a much clearer understanding of stock levels, enabling them to reduce holding costs and increase turnover rates. Automation functions facilitated by the system further paved the way for a more agile production schedule, leading to a significant uptick in overall operational efficiency.
These successes highlight the adaptability of QAD WMS and how it can meet diverse operational needs,
"A well-executed implementation not only addresses current problems but also sets the stage for future growth and scalability."
Lessons Learned from Failures
Despite the success stories, itās equally important to consider scenarios where QAD WMS implementations did not hit the mark. One common thread in these failures often ties back to inadequate change management. For instance, a logistics firm attempted to integrate QAD WMS without sufficiently preparing its workforce. Resistance to changing established processes led to delays and confusion during the transition.
Moreover, some companies rushed their implementation process, neglecting crucial testing phases. A food distributor's experience serves as a cautionary tale. They installed QAD WMS but overlooked necessary integrations with their existing ERP systems, which resulted in data discrepancies and operational disruptions.
From these lessons, organizations can learn the importance of thorough planning and involving staff at every step. Clear communication and training are fundamental to overcoming resistance and ensuring a smoother transition.
In essence, studying both sides of the coināsuccess and failureāprovides a deeper understanding of the critical factors influencing the implementation of QAD WMS.
QAD WMS in Different Industries
The versatility of QAD Warehouse Management System (WMS) is evident in its application across various sectors. Tailoring the system's features to suit industry-specific needs not only optimizes operations but also enhances overall supply chain efficiency. As industries grapple with unique challenges, implementing QAD WMS can be a game changer, providing solutions that align with specialized requirements and regulatory demands. Letās delve into how this system plays a pivotal role in three key sectors: manufacturing, retail, and healthcare.
Manufacturing Sector
In the manufacturing arena, QAD WMS can streamline processes that integrate production with warehousing. An effective WMS allows for real-time visibility of inventory levels and movement, making it easier to manage both raw materials and finished goods. For instance, manufacturers can minimize downtime by ensuring that the necessary components are available precisely when needed. This is particularly vital in a just-in-time manufacturing environment, where the efficiency of production lines can hinge on inventory accuracy.
Moreover, QAD WMS can assist in quality control by tracking the provenance of components, ensuring that suppliers meet compliance standards. By embedding quality checks within the warehouse processes, manufacturers can enhance product integrity and reduce the likelihood of costly recalls.
āUnderstanding the flow of goods from the moment theyāre produced until theyāre shipped is critical in manufacturing.ā
Retail Sector
Retailers face their own set of challenges when it comes to inventory management, particularly in meeting consumer demand while managing supply chain complexities. The implementation of QAD WMS allows retailers to keep a pulse on their stock levels across multiple locations. This capability is crucial, especially during peak seasons when demand can surge unpredictably.
Additionally, the system enables a seamless connection between online orders and in-store inventory. Retailers can leverage QAD WMS to fulfill e-commerce orders efficiently, often a difficult task due to the intricacies of managing brick-and-mortar and online operations. By using real-time data analytics, businesses can better understand purchasing trends and adjust their stock accordingly, ensuring that they donāt end up with excess or insufficient inventory.
Healthcare Sector
In the healthcare sector, the importance of accuracy and compliance cannot be overstated. QAD WMS ensures that medical supplies and pharmaceuticals are tracked meticulously, facilitating adherence to stringent regulations. This can include anything from ensuring the right medications are available in hospitals to maintaining the cold chain for temperature-sensitive products.
A key benefit in healthcare is the inventory tracking functionality that helps mitigate the risk of shortages or expirations. It allows healthcare providers to manage their supplies proactively, enhancing patient care by ensuring that essential items are always on hand. Furthermore, the system's ability to generate audits and reports enables organizations to comply with health regulations more effectively.
Future Trends in Warehouse Management Systems
Understanding the future trends in warehouse management systems (WMS) is crucial for businesses aiming to stay ahead of the curve. The logistics landscape is changing rapidly, and organizations are now seeking ways to adapt to these shifts. The examination of upcoming trends not only highlights the advantages that contemporary technologies bring but also provides a roadmap for decision-makers looking to enhance operational efficiency and sustainability.
Sustainability in Warehousing
Sustainability is no longer a buzzword; it's an imperative. Warehousing operations have a significant impact on the environment, from energy consumption to waste production. Adopting sustainable practices can lead to lower costs and improved brand reputation. Emphasizing energy-efficient systems, for example, can reduce the carbon footprint of warehouse operations.
One approach is the integration of solar panels and using energy-efficient lighting. These practices not only cut down on electricity costs but align with global sustainability goals.
- Green Supply Chain: Companies are increasingly adopting green logistics to appeal to eco-conscious consumers. This involves rethinking product packaging and transportation methods, ensuring that the entire supply chain reflects sustainability.
- Data-Driven Decisions: Using data analytics, warehouses can monitor resource consumption and identify areas for improvement. By analyzing the energy usage patterns, companies can make informed changes that promote sustainability without sacrificing efficiency.
Ultimately, these sustainable practices not only address environmental concerns but also provide a competitive edge to companies willing to invest in them.
Further Developments in Technology
As technology continues to evolve, so do opportunities for enhancing warehouse management. Automation, artificial intelligence, and the Internet of Things (IoT) are forging paths toward smarter warehousing.
- Automation: Robotic systems can manage mundane tasks such as inventory retrieval, freeing up human workers for more strategic roles. These machines can increase accuracy and speed, resulting in better throughput.
- AI and Machine Learning: By analyzing historical data, AI can predict inventory needs, streamline order processing, and optimize stock levels. This predictive capability allows organizations to respond to market demands more effectively.
- IoT Integration: Sensors placed throughout the warehouse can track items in real-time. This visibility allows for quicker resolutions to any in-transit issues and improves supply chain transparency.
"Investing in technology isn't just about keeping up with competitors; itās about redefining what's possible in warehouse management."
In summary, the future of warehouse management systems is being shaped by trends that emphasize sustainability and cutting-edge technology. Companies that grasp these shifts stand to gain significant advantages in efficiency, cost savings, and customer satisfaction. Keeping an eye on these trends will empower decision-makers and IT professionals to strategize effectively, paving the way for enhanced logistical performance.
Comparative Analysis with Other WMS Solutions
When it comes to choosing a Warehouse Management System (WMS), the decision is never straightforward. Thereās a vast ocean of options out there, all claiming to enhance warehouse efficiency and streamline operations. In this landscape, a comparative analysis is a crucial aspect for decision-makers, as it allows businesses to sift through the noise and focus on solutions that best fit their needs. Analyzing QAD WMS against its competitors involves understanding key features, integration capabilities, cost-effectiveness, and user experiences which can ultimately inform strategic logistics planning.
Benchmarking Against Competitors
To evaluate QAD WMS effectively, it is essential to look at how it stacks up against similar systems.
- Functionality: Many WMS solutions offer basics like inventory tracking and order processing. However, not all can handle complex inventory scenarios or high-volume operations with the same grace as QAD.
- Integration: A major factor is how QAD integrates with other systems. Unlike some competitors that may only offer limited APIs, QAD streamlines integration with ERP systems, allowing for better data flow and reduced chances of errors. This seamless interoperability is a game-changer in today's fast-paced supply chain environment.
- Scalability: The adaptability of a WMS to grow alongside an organization is vital. QADās architecture supports businesses ranging from startups to large corporations, making it a versatile player. Other systems may falter when scaling operations, leading to bottlenecks and inefficiencies.
- User Experience: The user interface of a WMS can significantly impact its adoption and effectiveness. QADās interface is designed for intuitive use, making it easier for staff to navigate and reduce training time, whereas some competitors are often seen as clunky or outdated.
Unique Selling Points of QAD
There are several aspects where QAD WMS shines particularly bright in the broad spectrum of warehouse solutions.
- Robust Reporting Tools: QAD provides in-depth analytics that help organizations gain insights into their operations. These metrics are invaluable in identifying areas of improvement and optimizing processes.
- Flexibility: Thanks to its modular design, QAD can cater to a diverse range of industries, from retail to healthcare. This flexibility allows businesses to mold the system to their specific needs, enhancing its overall value.
- Strong Support Network: QAD offers comprehensive support and maintenance services that many competitors lack. This reassurance of ongoing assistance enhances user confidence and operational stability.
- Cloud Capabilities: Being cloud-based, QAD allows access from anywhere, ensuring that data is always available at the fingertips of users. This is especially appealing to businesses looking for remote access solutions.
"When evaluating a warehouse management solution, it is essential to go beyond mere features and understand how these systems can adapt to the unique challenges your business faces."
Regulatory Compliance Considerations
In todayās world, where businesses operate under a watchful eye of various regulations and standards, understanding regulatory compliance is key. Regulatory compliance considerations are paramount for any system handling inventory and warehouse management. These regulations ensure that operations are conducted legally and ethically, safeguarding not only the company but also its stakeholders and customers.
A well-structured QAD Warehouse Management System (WMS) considers these frameworks, aiding companies to stay compliant with ever-evolving regulations. The implications of non-compliance can be severe, ranging from hefty fines to loss of customer trust. Therefore, weaving regulatory insights into the fabric of WMS is not merely advisable; itās essential for sustainable operations.
Understanding Compliance Requirements
Each industry comes with its unique set of compliance requirements, and understanding these needs is crucial. Some of the regulatory frameworks that businesses must grapple with include:
- Health and Safety Regulations: These ensure that the working environment is safe for employees, impacting equipment choice and storage methods.
- Environmental Regulations: Companies must adhere to environmental laws governing waste management and resource usage, which can influence warehouse layout and procedures.
- Data Protection Laws: Handling customer and supplier data means following regulations like GDPR, which affect how the WMS collects and secures data.
- ISO Standards: Many industries follow ISO certifications, which guide process quality and consistency.
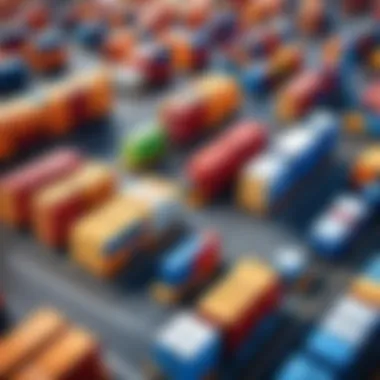
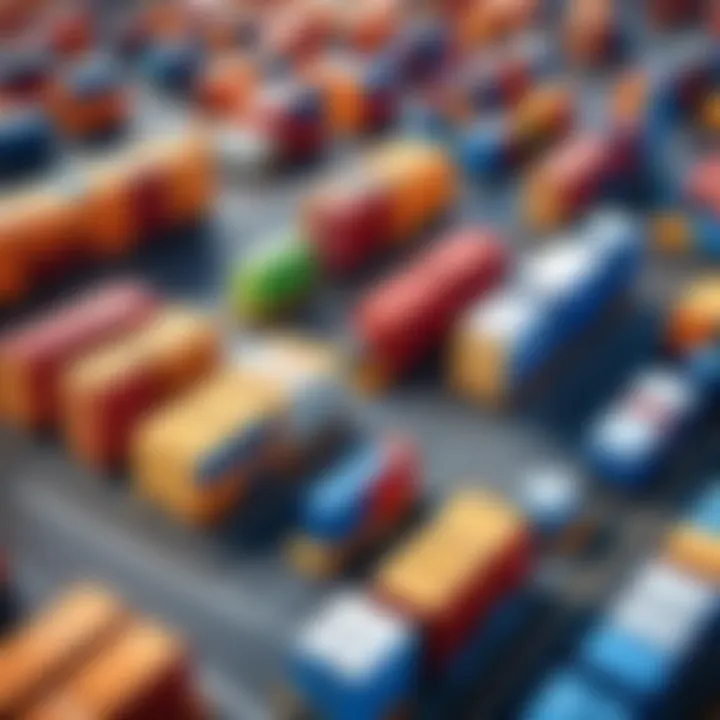
Understanding these regulations helps organizations craft a compliance roadmap. This roadmap defines how QAD WMS can adapt and function within the legal framework needed for specific operational goals.
Ensuring QAD WMS Meets Regulations
To guarantee that QAD WMS aligns with necessary regulations, several steps should be taken:
- Regular Audits: Conducting periodic audits can highlight compliance gaps within the system. This allows businesses to quickly rectify any issues before they escalate.
- Continuous Training: Equipping staff with knowledge about compliance and updates in regulations is vital. Ongoing training sessions will help employees stay alert to risks.
- System Updates: Keeping the QAD WMS software updated ensures it contains the latest compliance features and guidelines.
- Documentation: Proper record-keeping promotes transparency and supports the organization during audits. Documentation helps prove that the business is compliant with regulations.
Ensuring that a QAD WMS meets regulations isnāt just a side note; it plays a significant role in how businesses are perceived by customers and partners.
The implementation of a robust compliance strategy not only protects a company but also fosters trust and integrity in operations.
In summary, regulatory compliance considerations are about more than just following the law; theyāre about building a reputable business that values ethical practices as much as operational efficiency. Knowing the requirements and aligning them with the capabilities of the QAD WMS leads to increased customer confidence and better business performance.
Implementation Strategies for QAD WMS
Implementing a Warehouse Management System like QAD is not just a mere exercise in tech upgrades; itās a strategic move that can influence an organizationās operational efficiency and overall success. The importance of well-thought-out implementation strategies cannot be overstated as they lay the groundwork for a successful transition and long-term effectiveness of the system.
A structured implementation strategy ensures that all aspectsāfrom software setup to staff trainingāare addressed comprehensively. Without these strategies, companies risk encountering challenges like system failures, decreased productivity, and employee resistance. Implementing QAD WMS successfully helps organizations streamline processes, boost communication, and ultimately increase functionality across various departments.
Understanding the dynamics and intricacies involves careful planning and preparation. Key elements to consider include:
- Organizational Readiness: Ensuring the company's structure can support new workflows.
- Stakeholder Engagement: Securing buy-in from employees and management alike.
- Resource Allocation: Sufficient budget, personnel, and tools for implementation.
- Change Management: Preparing the workforce for the transition to minimize resistance.
Step-by-Step Implementation Guide
Implementing QAD WMS should follow a tried-and-true step-by-step process to avoid potential pitfalls. Hereās a simplified guide:
- Assessment of Current Processes: Analyze existing warehouse operations to pinpoint pain points and inefficiencies.
- Define Objectives: Establish clear goals that align with business targets.
- Select Implementation Team: Assemble a dedicated group consisting of IT, management, and warehouse personnel.
- Create a Timeline: Develop a realistic timeline that outlines all phases of implementation.
- Software Configuration: Set up the QAD system tailored to your organization's processes.
- Data Migration: Transfer necessary data from the old system to QAD, ensuring accuracy.
- Training: Provide comprehensive training sessions for end-users.
- Testing: Conduct thorough testing before going live, addressing any issues that arise.
- Go Live: Officially launch the system, monitoring closely for any immediate challenges.
- Post-Implementation Review: Evaluate the implementation and gather feedback for continuous improvement.
Best Practices for Success
To ensure that the implementation of QAD WMS goes off without a hitch and achieves its intended benefits, consider these best practices:
- Engage Stakeholders Early: Involve relevant parties from the onset to garner support and insights.
- Balance Customization with Flexibility: While tailoring QAD to your needs is critical, avoid over-customization that hinders adaptability.
- Regular Feedback Loops: Create channels for users to share experiences and suggest improvements.
- Continuous Training: Post-implementation training is vital to keep staff updated on new features and enhancements.
- Monitor Key Performance Indicators: Regularly track performance to ensure the system meets defined objectives.
"The effectiveness of a Warehouse Management System is directly correlated with the quality of its implementation strategy."
The blend of these steps and practices prepares an organization not just for the shift but sets a sustainable foundation for ongoing growth and adaptability. Therefore, taking the time to meticulously plan and execute the implementation of QAD WMS can yield significant dividends in terms of operational efficiency and customer satisfaction.
Cost Analysis of QAD WMS
When contemplating the adoption of a Warehouse Management System (WMS) like QAD, it's crucial to conduct a thorough cost analysis. This process helps in understanding not just the financial outlay required to implement this software but also its potential long-term benefits. Evaluating costs might seem like peeling an onion at firstāeach layer providing additional insights into the issue. From the initial investment needed to the savings garnered over time, a detailed breakdown offers decision-makers the clarity they need in a competitive landscape.
Initial Investment vs. Long-term Value
At the onset, the initial investment in QAD WMS can appear daunting. This includes not only the software purchase itself but also expenditures related to training, integration with existing systems, hardware upgrades, and any consultancy services needed for seamless implementation.
However, one should not view these costs in isolation. Viewing the long-term value of QAD WMS is essential to get the complete picture. Over time, the system can streamline operations, reduce errors, and enhance productivity. Hence, the return on your initial investment might far overshadow the upfront costs.
- Training and User Adoption: Although incurring costs initially, well-trained staff can operate the system efficiently, leading to improved performance.
- Operational Efficiency: By automating processes through QAD, companies often find a decrease in labor costs and an increase in order accuracy.
- Scalability: The future-ready nature of QAD ensures that as business needs evolve, companies can adjust without undergoing rigorous changes.
In this way, while the upfront costs can be intimidating, the longer-term financial dynamics usually steer decision-makers towards positive outcomes.
Return on Investment (ROI) Metrics
Calculating the Return on Investment (ROI) for QAD WMS involves more than just crunching numbers; it necessitates a nuanced approach to understanding benefits derived from it. Return on Investment can be viewed through multiple lenses, making it a multi-faceted measure of value.
To derive concrete figures, one might consider the following factors:
- Increased Throughput: More orders handled faster can translate to higher revenue.
- Operational Cost Reduction: By minimizing errors and enhancing efficiency, businesses can drastically lower their operational costs.
- Customer Retention: With better service leading to increased customer satisfaction, companies often see a positive impact on customer loyalty and retention rates.
A pivotal aspect is calculating the time frame for recovery of initial costs. Many organizations set a benchmark to evaluate their ROI, emphasizing the need for a strategic timeline.
"The key to a successful ROI calculation lies not only in immediate financial returns but also in long-term strategic alignment with business goals."
For instance, a company may find that after implementing QAD WMS, it experiences a 20% reduction in operational costs within the first year. This can be attributed to better inventory management, enhanced order accuracy, and improved shipping times. If the total cost of implementation is, say, $100,000 and the annual savings are $20,000, the ROI might predict a complete payback within five yearsāa compelling case for the investment.
Ultimately, a well-rounded cost analysis that juxtaposes initial investment against long-term value and ROI metrics will provide enterprises a clearer vision of what to expect. By articulating these elements, stakeholders can make informed decisions rooted in not just costs but also the extensive benefits that the QAD Warehouse Management System promises to deliver.
QAD WMS Support and Maintenance
In the landscape of logistics and supply chain management, the significance of robust support and maintenance for the QAD Warehouse Management System cannot be overstated. Like any cog in a well-oiled machine, a warehouse management system must have continuous care to ensure it operates at peak efficiency. The ongoing support strategies not only protect investments but also keep a company agile in response to market dynamics.
Ongoing maintenance is fundamental for identifying and resolving issues before they escalate, ultimately reducing downtime. With QAD WMS, organizations can expect to maintain a high level of operational performance, which translates to improved order fulfillment and ultimately, customer satisfaction.
To illustrate, imagine a bustling warehouse where even a minor glitch in the system can lead to chaosāorders delayed, wrong shipments sent, and unhappy clients. This emphasizes the need for vigilant upkeep and responsive support structures to mitigate potential disruptions.
"An ounce of prevention is worth a pound of cure." ā This old proverb captures well the essence of proactive maintenance strategies in the context of QAD WMS.
Ongoing Support Strategies
Implementing ongoing support strategies is not just about fixing problemsāitās a comprehensive approach to maintaining the integrity and functionality of the QAD WMS. Companies should prioritize several strategies to foster a sustainable support environment.
- Training and Development: Continual training sessions for staff ensure that users are well-versed in system functionalities. This knowledge empowers employees to troubleshoot basic issues independently.
- Help Desk Services: A dedicated help desk or support team that is available for staff can facilitate rapid response to any potential system hurdles. This support can often prove invaluable in averting downtime.
- Regular System Reviews: Conducting periodic reviews helps identify areas for improvement within the software and its use. These reviews can unveil inefficiencies that, when addressed, can lead to enhanced performance.
Such strategies enable businesses to adapt to challenges quickly while maximizing the value derived from their QAD WMS investment.
Updating the System for New Features
As technology rapidly evolves, so too must the QAD WMS. Staying updated with the latest features represents a critical element of maintenance, ensuring that the system can meet changing business requirements.
Regular updates can offer several key benefits:
- Enhanced Functionality: New features may provide advanced tools for data analytics or automation, streamlining processes and providing deeper insights into warehouse operations.
- Security Improvements: Software updates often include patches for security vulnerabilities. Given how much sensitive information flows through warehouse management systems, maintaining robust security is paramount.
- Compliance Adherence: As standards and regulations evolve, updating the WMS ensures compliance with new requirements, thus protecting the organization from legal ramifications.
Moreover, embracing updates can foster a culture of innovation within the organization. By utilizing all the powerful features available in the QAD WMS, companies can stay ahead of competitors who may still lag behind in their technology adoption.
Ultimately, a proactive approach to support and maintenance not only safeguards the current operational landscape but also aligns the organization for future success in a fast-paced business environment.