Strategies for Effective Management of Raw Material Inventory
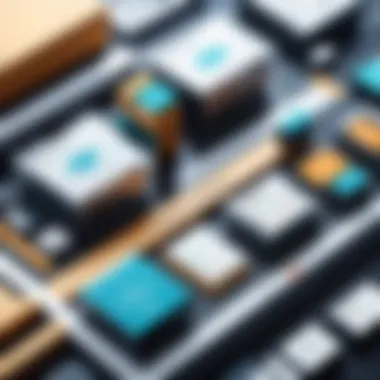
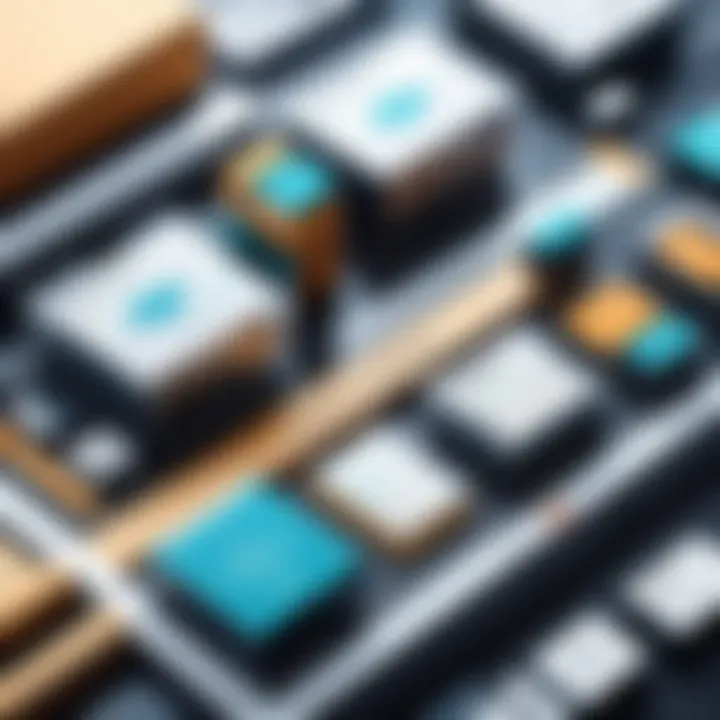
Intro
Efficient management of raw material inventory is not just a challenge but a critical element for businesses looking to thrive in todayâs competitive marketplace. Companies often grapple with the unpredictable nature of supply chains, which is further complicated by fluctuations in demand and market volatility. Understanding and implementing effective strategies for raw material inventory management can significantly optimize operational processes, reduce costs, and enhance productivity.
In this discussion, we will delve into various strategies that aid in managing inventory effectively. We will highlight the necessity of accurate forecasting to anticipate needs, explore the technological tools that improve efficiency, and observe the best practices for organizing and maintaining records. These elements are crucial for mitigating risks and optimizing the entire supply chain process, making them essential considerations for decision-makers in any organization.
Furthermore, we will also evaluate software options that facilitate efficient inventory management by providing crucial insights and tools. As we navigate through these strategies, expect to receive a comprehensive understanding that will empower you to refine your organization's practices.
Let us embark on this insightful exploration of raw material inventory management.
Preamble to Raw Material Inventory Management
Effective management of raw material inventory is a backbone in the structure of any thriving business. This section digs into the core concepts of this intricate process and emphasizes its relevance in this fast-paced business environment.
Understanding raw material inventory management goes beyond merely counting the items in a warehouse. It encompasses strategies that ensure materials are available when needed, thus avoiding delays in production and ultimately impacting the bottom line. With the increasing complexity of supply chains and the volatile market dynamics, decision-makers must prioritize inventory management to remain competitive.
Defining Raw Material Inventory
Raw material inventory refers to the raw materials and components that a company holds to use in its production process. Think of it like the ingredients in a chef's kitchen â without the right materials on hand, you can't whip up the dish that customers crave. These materials could include everything from metals for manufacturing, fabrics for clothing, to ingredients in food production.
By keeping tabs on raw materials, businesses can better forecast their needs, make more informed purchasing decisions, and ultimately enhance their operational efficiency. From a tactical standpoint, having accurate inventory data helps in minimizing waste and improving cash flow, which is crucial for any organization.
Significance in Modern Business
In today's business world, effective raw material inventory management has become more critical than ever. It's not just about keeping the shelves stocked; it's about understanding the intricate dance between supply and demand. When managed well, inventory serves as a reliable safety net against unforeseen fluctuations in the market.
Reasons why managing raw material inventory is crucial:
- Cost Efficiency: Reducing excess inventory prevents money from being tied down in unsold goods, which could be better utilized elsewhere.
- Supply Chain Stability: Seamless inventory management allows for smooth transitions across the supply chain, ensuring that production runs like a well-oiled machine.
- Enhanced Productivity: When materials are managed correctly, it boosts production schedules, leading to timely deliveries and satisfied customers.
Effective raw material inventory management shapes not only operational efficiency but also the potential for growth and innovation in modern business.
By recognizing the importance of raw material inventory management, companies position themselves not merely to survive but to thrive in an ever-evolving market landscape. In the upcoming sections, we will explore the inventory management cycle, the role of technology, best practices, and other strategies that can significantly enhance management of raw materials.
The Inventory Management Cycle
The Inventory Management Cycle is a cornerstone in the domain of raw material inventory management. It is the continuous process that governs the flow of materials, from procurement to the final stages of production and beyond. For decision-makers, understanding this cycle is vital as it directly ties into optimizing operational efficiency and minimizing costs. By mastering this cycle, companies gain an edge, ensuring that materials are available when needed without overshooting budgets.
Understanding the Lifecycle of Inventory
Every company should be aware of the lifecycle of inventory to maintain a steady flow of operations. This lifecycle comprises several stages:
- Procurement: This marks the beginning, where raw materials are acquired from suppliers. During this phase, relationship building with suppliers becomes key, as it lays the groundwork for future negotiations and reliability.
- Storage: Once procured, materials are stored until they are required for production. Keeping an organized and systematic storage area helps in quick identification and retrieval of goods, thus reducing delays.
- Production: In this stage, the raw materials enter the production line, transforming into finished products. It's critical that the right materials are available at the right time to prevent bottlenecks.
- Distribution: Finally, the finished goods reach the market. Efficient distribution maximizes sales opportunities, making the timing of inventory release crucial.
Understanding these phases facilitates better decision-making and allows businesses to anticipate potential issues before they escalate.
Stages of Inventory Management
The stages of inventory management provide a clearer roadmap for businesses aiming to enhance their raw material processes. These stages include:
- Planning and Forecasting: This involves predicting the demand for materials and making informed decisions about what and how much to order. Accurate demand forecasting minimizes the risk of overstock or stockouts.
- Replenishment: This stage looks at maintaining optimal inventory levels. Using just-in-time methods can help reduce carrying costs while ensuring materials are there when required.
- Tracking and Monitoring: Keeping tabs on inventory levels allows companies to spot trends and respond quickly. Tracking systems can flag discrepancies or lack of consistency, so action can be taken immediately.
- Review and Analysis: Regular audits are necessary to assess how inventory is being managed. This stage often identifies opportunities for cost savings or process improvements that could streamline operations further.
The inventory management cycle is not a set-it-and-forget-it system; it demands ongoing adjustments based on market conditions and business needs.
In summary, a comprehensive understanding of the Inventory Management Cycle and its stages allows businesses not only to respond to the immediate needs of production but also to strategize for long-term efficiency and resilience in a dynamic marketplace.
Forecasting Demand
Effective management of raw material inventory hinges significantly on accurate demand forecasting. Understanding future material needs allows businesses to maintain the delicate balance between overstocking and understocking, both of which carry their unique set of challenges. Overstocking can result in inflated holding costs and spoilage, while understocking might lead to production delays and lost sales opportunities. Therefore, forecasting is not merely a numerical exercise; it's a strategic imperative that directly impacts operational efficiency and overall cost management.
Techniques for Accurate Forecasting
To achieve precise forecasting, various techniques can be employed.
- Quantitative Methods: These involve statistical analyses that rely on historical data and numerical models. Methods, such as time series analysis or regression models, help identify trends based on past movements.
- Qualitative Approaches: In certain scenarios, especially in new market conditions or when data is scarce, qualitative methods become vital. This could involve expert opinions or market research.
"A stitch in time saves nine; accurately predicting demands today prevents bigger issues tomorrow."
Employing a mix of both quantitative and qualitative methods can yield a more rounded approach to forecasting, allowing for adaptability amidst changing conditions.
Utilizing Historical Data
Historical data serves as the backbone of any effective forecasting strategy. By examining past inventory turnover rates, sales cycles, and seasonality, businesses can uncover patterns that hint at future demand.
- Sales Patterns: Knowing when sales peaked and troughs occurred can guide decisions for future stock levels.
- Inventory Turnover Rates: Understanding how long materials typically stay in inventory can inform reordering schedules.
For instance, a business that sells winter clothing may observe increased sales during specific months. This data, when analyzed properly, can shape decisions about inventory orders leading into that season.
Adapting to Market Trends
Being aware of and responding to evolving market trends is essential for effective demand forecasting. Industry shifts, customer preferences, and even global events can influence material needs.
- Market Research: Regular analysis of market reports can keep businesses informed about emerging trends. This provides invaluable insights that can reshape inventory strategies.
- Consumer Behavior: Engaging directly with customers through surveys or feedback can reveal changing needs that aren't always apparent through numerical data alone.
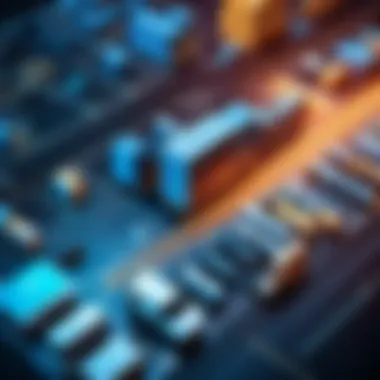
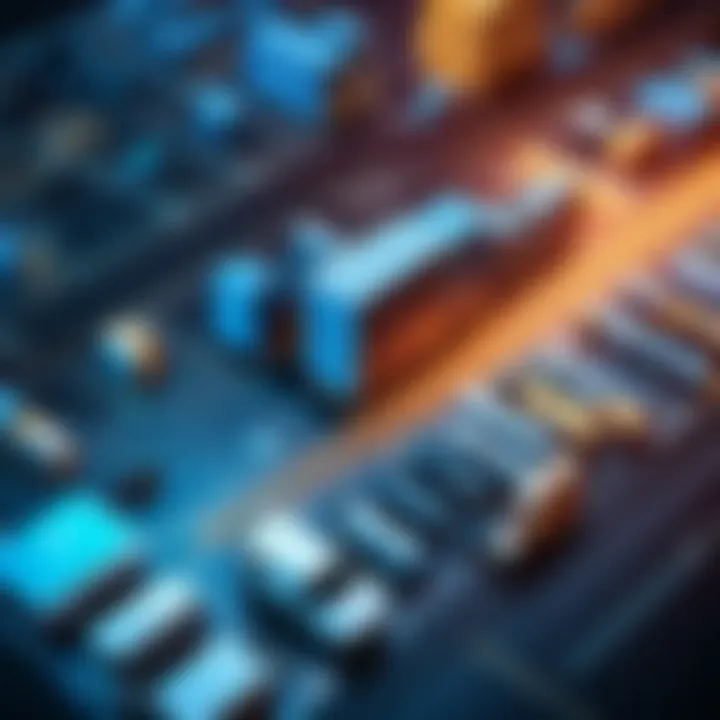
Having a finger on the pulse of the market allows companies to pivot their strategies swiftly, ensuring they remain competitive and responsive to customer demands.
Technology in Inventory Management
In todayâs rapidly evolving marketplace, leveraging technology in inventory management is no longer a luxuryâit's a necessity. As businesses look to refine their operations, technology serves as a pivotal tool. It not only helps streamline processes but also enhances visibility and accuracy across the entire inventory lifecycle. By integrating technological solutions, organizations can tackle inefficiencies head-on and make informed decisions backed by data-driven insights.
Software Solutions for Inventory Control
The variety of software solutions available today makes it easier than ever to keep track of raw material inventory. From cloud-based platforms like NetSuite and Fishbowl to specialized applications such as Zoho Inventory, each has its own set of features tailored to different business needs.
These software solutions often come equipped with robust functionalities that allow businesses to:
- Monitor stock levels in real-time, helping avoid situations of overstocking or stockouts.
- Automate reorder triggers when items reach a predetermined threshold, reducing manual intervention.
- Integrate with other enterprise systems, such as ERP or CRM, to ensure data coherence across departments.
Taking the time to evaluate and implement these software solutions can result in significant operational benefits and cost savings. The right software can make all the difference in transforming an inefficient inventory system into one that runs like a well-oiled machine.
Automation Techniques
Automation goes hand-in-hand with software solutions and is crucial for reducing human error and improving efficiency. Employing automation techniques in raw material inventory management can streamline various tasks:
- Barcode scanning allows for quick and accurate recording of stock movements, eliminating tedious manual entry errors.
- Automated inventory tracking systems can keep tabs on stock levels without the need for constant oversight, hitting the right balance between availability and wastage.
- Alert systems can notify managers when thresholds are reached or when anomalies arise, providing opportunities for proactive measures.
Using automation not only saves time but can also significantly boost employee productivity. By freeing staff from repetitive tasks, they can focus more on higher-value activities that drive business growth.
Using Data Analytics for Insights
Data analytics is at the forefront of organizational decision-making. When it comes to inventory management, utilizing data analytics can unveil deeper insights into inventory trends, customer preferences, and supply chain performance. This involves:
- Analyzing historical sales data to forecast demand accurately. Predictive analytics can help in planning for seasonal spikes or declines, ensuring that inventory levels meet customer needs.
- Identifying patterns in purchasing behavior which can shed light on how certain materials are used or consumed, leading to smarter inventory strategies.
- Assessing supplier performance by analyzing lead times and delivery accuracy, thus allowing for more informed relationship management.
By tapping into these analytical insights, decision-makers can optimize inventory levels and improve responsiveness to market changes.
"Incorporating technology within inventory management represents a strategic shift that can redefine operational efficiency and accuracy across various sectors."
By embracing these technological advancements, companies position themselves not just to survive but to thrive in an increasingly competitive landscape.
Best Practices for Inventory Organization
Efficient organization of inventory plays a critical role in raw material management. With the tides of business constantly shifting, adopting best practices can make a world of difference. Good organization helps to minimize waste, streamline processes, and ultimately leads to enhanced productivity. The underlying idea is to create an environment where inventory is easily accessible, manageable, and accounted for.
Methods for Effective Storage
Storage methods vary widely, and the right choice can make all the difference. Simple approaches like stacking can work, but they are often not enough. Utilizing shelving systems can maximize vertical space, allowing for better inventory segregation. Mobile racking systems are also revolutionary, as they offer the ability to reconfigure your storage layout as needed. This flexibility can adapt to changing inventory needs.
For those handling smaller items, consider bin systemsâoften clear, which provides visibility. This eliminates the need for rummaging through piles; no one wants to waste time on that. Finally, don't overlook climate controlâcertain materials need specific conditions to remain viable. Itâs not just about putting material on a shelf; it should be the right environment that counts too.
Labeling and Categorization Techniques
Proper labeling can reduce confusion even at busy times. Think of it like putting up road signs; they guide you through the inventory maze. Color-coded labels can highlight different categories at a glance. For instance, red could indicate items that need replenishment, while green could signify stable inventory. The aim here is usefulness and quick comprehension.
Categories should align with your business structure. This means understanding how materials are used and having a system that resonates with actual workflows. Consider software tools that help in both categorization and visual management. Systems like ERP or inventory management software can offer additional insights into label applications. This tech integration reduces the chances of misidentification and loss.
Regular Audits and Reviews
The saying "out of sight, out of mind" holds true in inventory management. Conducting regular audits helps in two major ways: it ensures accountability and highlights irregularities. Audits can be done monthly, quarterly, or even annually depending on the scale of your operations. You wouldn't believe the number of discrepancies that can be uncovered simply by taking the time to verify.
Implementing a rotating audit system can ensure that everything is checked periodically without completely pulling resources away from daily operations. Not only do you save headaches later, but you can also identify trends in your inventory dynamics. Are certain materials often short or overstocked? A proactive approach can mitigate the risks of stockouts or excess, helping you fine-tune purchasing decisions.
A well-organized inventory isn't just about immediate ease; it's about setting up long-term efficiency protocols and creating a roadmap for inventory success.
In summary, the best practices for inventory organization revolve around storage methods, effective labeling and categorization, and consistent audits. These seemingly simple practices compel one to think critically about how to address and enhance inventory practices effectively.
Risk Management in Inventory Control
Effective management of raw material inventory is crucial for any organization looking to maximize productivity and minimize disruptions. Among the many elements that come into play, risk management stands out as a vital part of the equation. By identifying and managing various risks associated with inventory, businesses can not only protect their assets but also enhance overall operational efficiency.
Risk management in inventory control involves the systematic process of identifying potential hazards that can affect inventory levels, assessing their likelihood and impact, and establishing strategies to mitigate these risks. This proactive approach helps firms to avoid costly surprises and maintain a steady flow of materials critical for their operations.
Identifying Potential Risks
Inventory management isn't just about keeping tabs on stock levels. Itâs essential to recognize potential risks that can disrupt inventory flows. Here are a few common risks:
- Supplier Reliability: Not all suppliers uphold their end of the bargain. Late deliveries or sudden price increases can catch companies off guard.
- Market Demand Fluctuations: The market can be fickle. A sudden drop in demand might lead to overstocked inventory, which ties up capital that could be used elsewhere.
- Storage Issues: Poor storage conditions can damage raw materials, leading to waste. This is particularly important in industries like food or pharmaceuticals.
- Regulatory Changes: New regulations can affect the types of materials that can be sourced, requiring businesses to adapt swiftly.
Recognizing these risks is an ongoing process. Regular audits and assessments can help unveil emerging risks, enabling firms to act swiftly and decisively.
Developing Contingency Plans
Once risks have been identified, the next step is to create effective contingency plans. These act as the safety nets for companies when things donât go according to plan. A well-thought-out contingency plan might include:
- Alternative Suppliers: Establishing relationships with multiple suppliers ensures that if one falls short, another can step in. This reduces reliance on any single source.
- Flexible Inventory Levels: Consider maintaining safety stock for critical materials that face supply uncertainties. This can cushion the impact from unexpected demand spikes.
- Regular Training: Ensure that staff are equipped to handle disruptions. Knowledge about the contingency plan can empower employees to act swiftly when needed.
- Crisis Management Protocols: Having clear protocols for various scenarios can streamline responses during emergencies, ensuring minimal downtime.
"Failing to prepare is preparing to fail.â This old adage rings especially true when it comes to contingency planning in inventory management.
Monitoring Supply Chain Vulnerabilities
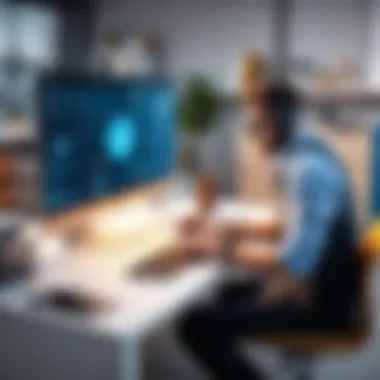
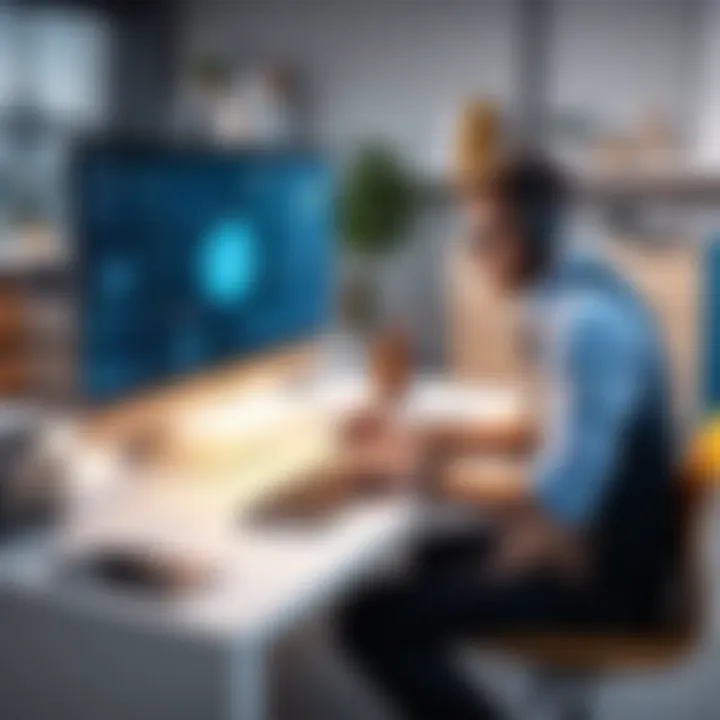
Finally, it is essential to keep an eye on supply chain vulnerabilities. Supply chains are complex networks, and understanding their intricacies can offer significant benefits. Practicing vigilant monitoring through:
- Supplier Audits: Regular assessments of suppliersâ reliability can help spot problems before they escalate. A bad apple can spoil the barrel, so itâs best to keep a close watch.
- Inventory Analytics: Utilize data analytics to track inventory levels in real time. This can highlight trends and potential vulnerabilities before they affect production.
- Consumer Insights: Pay attention to market trends and customer feedback. This data can be invaluable for anticipating changes in demand or unexpected shifts in purchasing behavior.
Integrating Suppliers into Inventory Management
The management of raw material inventory can often feel like trying to herd catsâlots of moving parts and unpredictability at every turn. One key element that can greatly influence this complexity is the integration of suppliers into the inventory management process. In todayâs competitive landscape, itâs not just about keeping stock; itâs about smart stocking, which often requires a close partnership with those who supply the goods. When suppliers are integrated into the inventory management system, businesses can experience many benefits, including improved communication, reduced lead times, and enhanced responsiveness to market changes.
Building Strong Supplier Relationships
It all starts with building strong relationships. You canât squeeze blood from a stone, and expecting cooperative behavior from suppliers without a robust relationship is setting yourself up for disappointment. When suppliers feel valued and respected, they are more inclined to offer flexibility, reliability, and competitive pricing.
Here are some strategies for nurturing these relationships:
- Open Communication: Establish open lines for regular communication. This includes sharing forecasts, discussing potential challenges, and addressing concerns upfront.
- Trust and Respect: Trust is a two-way street. Show respect for their capabilities and expertise, which helps in creating a fertile ground for collaboration.
- Long-term Partnerships: Instead of transactional relationships, focus on long-term partnerships. This fosters loyalty and can lead to negotiations for better terms.
"Good relationships can lead to preferential treatment during crunch times, which is critical when youâre managing inventory."
Negotiating Terms and Conditions
Once a relationship is established, the next step is to negotiate terms and conditions that benefit both parties. This may seem like an uphill battle, but wielding negotiation skills can turn the tide in your favor.
Here are aspects to consider when negotiating:
- Pricing Structures: Understand the pricing models used by suppliers. Itâs not just about getting the lowest price; itâs about ensuring price consistency and predictability for budgeting and forecasting.
- Minimum Order Quantities: Discuss MOQs that not only work for your business but also for theirs. This balance helps manage inventory without straining the cash flow.
- Delivery Terms: Discuss delivery windows and terms that align with your inventory management cycles. Ensure that these terms are clearly outlined in any agreements to avoid misunderstandings later.
- Quality Assurance: Stress the importance of quality control measures. Clear standards should be established from the get-go to minimize issues down the line.
By integrating suppliers more effectively into inventory management, companies can eliminate much of the guesswork involved in stock replenishment, leading to smoother operations overall.
The Role of Inventory Metrics
Inventory metrics serve as the backbone of effective raw material management. They provide businesses with quantitative insights that inform decision-making, helping to streamline operations and maximize profitability. By focusing on accurate monitoring and analysis of these metrics, companies can maintain optimal inventory levels, reducing excess stock while ensuring sufficient materials are always available. This balance is crucial in avoiding production delays and minimizing carrying costs.
Moreover, the use of inventory metrics enables organizations to respond adeptly to fluctuations in demand, thereby fostering agility in their supply chain. Businesses that prioritize metrics can glean patterns over time that govern their operational strategies, ranking them higher in competitive markets.
Key Performance Indicators to Track
When it comes to inventory metrics, a handful of key performance indicators (KPIs) are particularly noteworthy. These KPIs are essential to measure the efficacy of inventory management practices, including:
- Inventory Turnover Ratio: This metric gauges how effectively inventory is being converted into sales. A high ratio indicates strong sales and effective inventory management, while a low ratio may suggest overstocking or stagnation.
- Gross Margin Return on Investment (GMROI): This KPIs measures the profit generated for every dollar spent on inventory. It's vital for understanding the profitability of inventory investments.
- Days Sales of Inventory (DSI): This indicates the average number of days it takes to sell the entire inventory. Lower values suggest a quicker sales cycle, indicating efficient inventory use.
Regularly tracking these KPIs allows businesses to stay on top of their inventory situation, leading to a more proactive approach rather than a reactive one.
Analyzing Inventory Turnover Ratios
Analyzing inventory turnover ratios can yield vital insights into a companyâs operational health. An optimal inventory turnover not only indicates efficient management but also enhances cash flowâfreeing up capital for investment in other areas of the business. A steady turnover ratio tells you that products are selling well, while a declining turnover may hint at obsolete or excess inventory that needs addressing.
It's crucial to benchmark against industry standards to get a clearer picture. For example:
- In the retail sector, turnover ratios can vastly differ. A quick-service restaurant might aim for a turnover of 60 or more times a year, while a specialty goods retailer may settle for 6-12 times.
"Understanding how to interpret turnover ratios is akin to reading the pulse of your business. It tells you whether your stock is a boon or a burden."
Culmination
In summary, the role of inventory metrics is indispensable in navigating the complexities of raw material management. Whether assessing performance through key indicators or demystifying inventory turnover ratios, these tools empower businesses to make informed decisions. Sustaining a keen eye on these metrics could very well be the difference between flourishing operations and a chaotic inventory system.
Challenges in Raw Material Inventory Management
Managing raw material inventory is akin to walking a tightrope. On one side, businesses aim to maintain sufficient stock to meet production demands, while on the other, they seek to minimize waste and costs. When it comes to managing this critical component, there are numerous challenges that can derail even the best-laid plans. Understanding these challenges is essential for decision-makers, as they can significantly affect operational efficiency and profitability.
Common Issues Faced by Businesses
Many organizations grapple with various issues that can complicate raw material inventory management. Here are some of the most prevalent problems:
- Inaccurate Demand Forecasting: One major hurdle is the inability to accurately predict the demand for products. When forecasts are off, businesses face either overstocking or stockoutsâboth detrimental.
- Supply Chain Disruptions: Natural disasters, geopolitical tensions, and even unforeseen events like the pandemic can disrupt the supply chain. This unpredictability forces companies to adapt quickly, often leading to inventory shortages or excess stock.
- Variability in Raw Material Prices: Fluctuations in pricing can cause financial strain. Companies may be left scrambling if prices spike unexpectedly, forcing management to make difficult buying decisions.
- Storage and Handling Issues: Ineffective storage practices can lead to damage or spoilage of materials. Proper organization is crucial for optimizing space and ensuring that inventory remains in good condition.
These issues, while common, can create a ripple effect throughout the entire organization, impacting everything from production schedules to cash flow.
Strategies for Overcoming Barriers
Fortunately, there are well-crafted strategies to navigate these challenges effectively. Here are some approaches that decision-makers can utilize:
- Implement Robust Demand Planning: Leverage advanced forecasting tools that analyze historical sales data and market trends. This allows businesses to align inventory levels with actual consumer demand more closely.
- Diversify Suppliers: Relying on a single supplier increases vulnerability. By diversifying, companies mitigate risks associated with supply chain disruptions. Establishing relationships with multiple suppliers can provide more flexibility in times of crisis.
- Monitor Market Trends: Keeping a close eye on raw material prices and market conditions enables businesses to make informed purchasing decisions. For instance, if the price of a critical material is rising, buying in bulk before the increase can be a sound strategy.
- Optimize Storage Solutions: Investing in effective storage solutions can diminish handling errors and material spoilage. Techniques such as FIFO (first-in, first-out) and using inventory management software can streamline operations.
"Effective inventory management is not just about maintaining stock, but protecting the companyâs cash flow and resources."
Sustainability Considerations
In todayâs environment, sustainability has become a point of no return for businesses, and managing raw material inventory effectively is no exception. To grasp why this is critical, one must look at the intricate relationship between resource management and environmental health. Optimizing the way that raw materials are sourced, stored, and utilized doesnât just help a companyâs bottom line; itâs an integral part of ensuring the planet can sustain future generations.
Effective sustainability measures often lead to several substantial benefits. These include reducing waste, conserving energy, and minimizing the carbon footprint associated with inventory practices. Adopting a sustainable approach enhances corporate social responsibility (CSR) initiatives, which can improve brand image and customer loyalty. For decision-makers, the choice to prioritize sustainability is not merely an ethical obligation; it's also a pragmatic business strategy that aligns closely with modern consumersâ values.
Impact of Resource Management on Environment
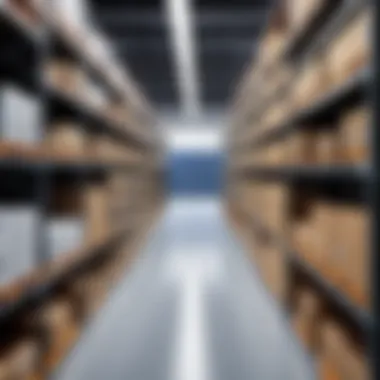
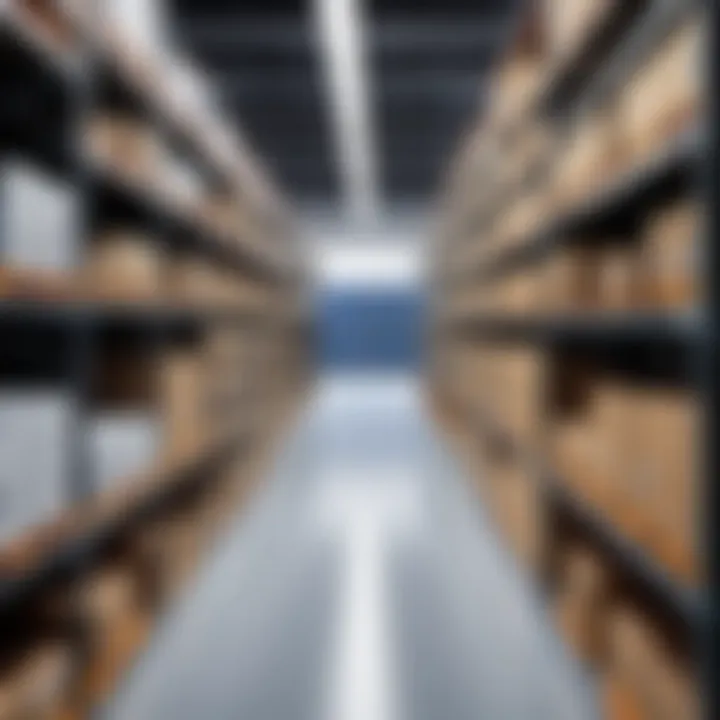
When it comes to resource management, every decision carries weight. Poor management not only leads to the depletion of resources but also contributes to environmental degradation. For instance, when a company overestimates its need for raw materials, excess inventory often leads to spoilage, waste, and extended storage times, all of which could have been avoided with a more tailored approach.
Besides wastage, thereâs the aspect of emissions. The transportation of raw materials involves logistics which, if not managed sustainably, can lead to elevated greenhouse gases. On the flip side, companies that implement efficient inventory practices can significantly reduce transportation's environmental impact.
- Buffer Stock Management: Carefully managing the levels of raw materials reduces the need to frequently transport goods, which in turn lowers fossil fuel consumption.
- Supplier Selection: Choosing suppliers who adhere to sustainable practices can further minimize the environmental footprint of raw materials.
Monitored and proactive resource management can create a ripple effect, encouraging an ecosystem of sustainability that stakeholders will prioritize.
Implementing Sustainable Practices
Implementing sustainable practices isnât just a trend; itâs a fundamental shift in how organizations operate and perceive their impact on the world. Companies looking to lead in this arena should prioritize integrating sustainability into their core supply chain strategies. Here are some avenues to explore:
- Lifecycle Assessment (LCA): Assessing the environmental impacts of raw materials from extraction through to disposal provides a comprehensive view of their sustainability. This approach helps organizations make informed decisions on material choices.
- Inventory Optimization Tools: Leveraging technology can aid in creating more efficient inventory levels. Tools that analyze production schedules and historical data allow businesses to maintain just-in-time inventory systems, which reduces excess.
- Material Innovation: Seeking out sustainable alternatives to traditional materials can decrease dependency on environmentally harmful resources. For example, many manufacturers are moving towards bio-based materials.
- Employee Training: Education is crucial. Empowering employees with knowledge about sustainability practices fosters a culture of responsibility towards resource management.
In closing, implementing these practices isn't a one-size-fits-all but rather a continuous journey toward improvement. Each step taken can lead to a more sustainable inventory management process, ultimately benefiting both the company and the environment.
"Sustainability is no longer a choice; itâs a necessity for businesses looking to thrive in the future."
By fostering a keen understanding of sustainability in raw material inventory management, businesses can not only enhance their operational efficiency but also contribute to a more sustainable planet for generations to come.
Case Studies and Industry Insights
Case studies are invaluable when dissecting the landscape of raw material inventory management. They provide real-world examples that underscore the challenges and successes experienced by various companies in their quest for optimal inventory control. Understanding these industry insights not only aids in identifying best practices, but it also equips decision-makers with the knowledge to implement effective strategies tailored to their unique business contexts.
By delving into case studies, companies can learn from both the triumphs and missteps of others. Insights gained from diverse industries facilitate the adaptation of successful inventory strategies, ultimately leading to improved operational efficiencies and cost reductions. The practical knowledge derived from these examples encourages an analytical approach, fostering continuous improvement in inventory management practices.
Moreover, case studies illustrate how specific sectors tackle unique challenges. The strategies employed by a large automotive manufacturer, for instance, might differ dramatically from those used by a local textile producer. These insights shed light on the significance of customizing inventory management strategies to align with industry-specific demands and supply chain nuances.
Examples from Leading Companies
Leading companies have remarkably demonstrated effective raw material inventory management through innovative approaches that can serve as a blueprint for other organizations.
- Toyota: Utilizing the Just-In-Time (JIT) methodology, Toyota has successfully minimized inventory holding costs while ensuring materials arrive precisely when needed in production. This strategy requires extraordinary synchronization with suppliers, reducing waste and improving overall efficiency.
- Zara: This fashion retailer operates on a unique inventory model that enables rapid response to consumer trends. By streamlining its supply chain and maintaining close relationships with suppliers, Zara can quickly adapt to changing styles while ensuring minimal excess inventory.
- Boeing: The aerospace giant has implemented advanced technology for real-time tracking of raw materials throughout its complex supply chain. This not only allows for greater visibility but also enhances decision-making processes related to inventory levels and supplier engagements.
These examples illustrate how organizations across different sectors can implement strategic initiatives to improve their raw material inventory management effectively.
Lessons Learned and Best Practices
The analysis derived from these case studies reveals several lessons learned and best practices that can significantly influence raw material inventory management strategies.
- Embrace Technology: The integration of technology, such as inventory management software and analytics, can drastically improve tracking accuracy and decision-making.
- Supplier Collaboration: Building strong relationships with suppliers enhances communication and reliability, ensuring timely delivery of materials. This partnership is pivotal for timely production and minimized stockouts.
- Implementation of Best Practices: Companies should adopt policies surrounding inventory organizational methods, regular audits, and data analysis to continuously refine their strategies.
- Flexibility and Adaptability: The ability to pivot in response to market changes remains essential. Companies must be prepared to adjust their inventory levels based on fluctuations in demand.
- Continuous Learning: Organizations can benefit from regularly revisiting their strategies and looking externally at what leading companies are doing for improvements.
"Case studies serve as a compass, guiding organizations to better inventory management practices."
By synthesizing these insights and lessons learned from industry leaders, businesses can better design their raw material inventory management strategies to ensure a state of readiness in a constantly evolving marketplace.
Future Trends in Inventory Management
Keeping a finger on the pulse of inventory management is crucial for todayâs businesses. As companies try to keep their heads above water amidst competition, staying ahead of the curve with future trends in inventory management is not just beneficial; itâs essential. This section dives into how emerging technologies and the evolution of inventory strategies can steer organizations toward greater efficiency. The better businesses grasp these trends, the better positioned they will be for sustained success.
Emerging Technologies and Innovations
In the world of inventory management, technology shapes the landscape faster than ever before. Integrating cutting-edge solutions into raw material inventory processes can transform operations significantly. From cloud-based solutions to Internet of Things (IoT) devices, these innovations offer a wealth of benefits.
- Cloud Computing: With the ability to access inventory data from anywhere at any time, cloud systems enable real-time updates and foster collaboration. Managing stock has never been easier.
- IoT Devices: Sensors track inventory levels automatically, communicating needs back to the system before stock run low. This proactive approach can minimize disruptions.
- Artificial Intelligence: Forecasting demand using historical data through AI minimizes the guesswork. Businesses that employ this technology can make informed decisions, reducing both excess inventory and shortages.
These advancements don't just make life easier; they also provide a competitive edge. As these technologies continue to evolve, companies must remain flexible, adapting to maintain relevance in the marketplace.
"Emerging technologies are not just tools; they are bridges to a smarter, more efficient workflow in inventory management."
The Evolution of Inventory Strategies
The landscape of inventory strategies has shifted as businesses move from traditional methods to more sophisticated approaches. Understanding these evolving strategies is imperative for effective inventory management. Adaptability is key.
- Just-in-Time (JIT): This approach minimizes inventory levels by aligning orders with manufacturing schedules. JIT reduces storage costs but demands precise timing.
- Vendor-Managed Inventory (VMI): This partnership shifts inventory management responsibility to suppliers, allowing for more effective replenishment. Vendors keep an eye on stock levels and handle distribution.
- Total Inventory Visibility: Companies are increasingly seeking transparency throughout the supply chain. Tools that enable visibility allow for better planning and inventory control, enhancing decision-making.
The evolution of these strategies underscores the need to be proactive rather than reactive. For decision-makers, staying updated on how these strategies transform will enable better alignment with market demands and optimize resource allocation.
As inventory management continues to evolve, embracing these trends can position businesses for not just survival, but success in an increasingly competitive environment. With the right strategies, companies will be equipped to tackle future challenges and leverage opportunities as they arise.
Closure
In the ever-evolving landscape of business, managing raw material inventory effectively has become a cornerstone of operational success. As we peel back the layers of inventory management, several key elements emerge that underscore its importance. First and foremost, efficient inventory management is not just about keeping track of materials; it encompasses a strategic approach to aligning supply with demand, minimizing waste, and streamlining operations.
With the insights gleaned throughout this article, decision-makers can appreciate the interconnectedness of accurate forecasting, technological advancements, and well-organized storage solutions. These factors contribute significantly to reducing operational costs and enhancing productivity. The readers must recognize that effective inventory management is like a well-tuned engine; if one component falters, it can lead to inefficiencies that ripple through the supply chain.
Moreover, addressing potential risks and uncertainties in the inventory process can build resilience against market fluctuations. Setting robust contingency plans, maintaining strong supplier relationships, and continuously monitoring supply chain vulnerabilities can safeguard against disruptions.
"The strength of a supply chain lies not just in its materials but in its management."
In summary, careful management of raw material inventory presents numerous benefits.
- It simplifies processes,
- reduces costs, and
- cultivates reliability across the operation.
Thus, the culmination of all strategies discussed here reflects a roadmap for businesses aiming to not just survive but thrive in competitive markets. By focusing on these elements, organizations can position themselves as leaders in their respective industries, crafting a future built on informed decisions and strategic foresight.
Summarizing Key Points
- Importance of Raw Material Inventory: Proper management is crucial for operational efficiency and cost control.
- Tech-Driven Solutions: Technology plays a pivotal role in optimizing inventory processes and providing accurate data for decision-making.
- Best Practices for Organization: Strategies like labeling, categorization, and periodic audits help create a more efficient inventory system.
- Risk Mitigation: Identifying potential risks and devising contingency plans can enhance operational resilience.
- Long-Term Strategic Vision: A comprehensive approach that combines the strategies discussed can lead to sustainable operational improvements.
Ultimately, by integrating the strategies outlined in this article, organizations can elevate their inventory management practices, ensuring they meet changing market demands while controlling costs and boosting overall efficiency.