Exploring JDA Factory Planner: A Comprehensive Analysis
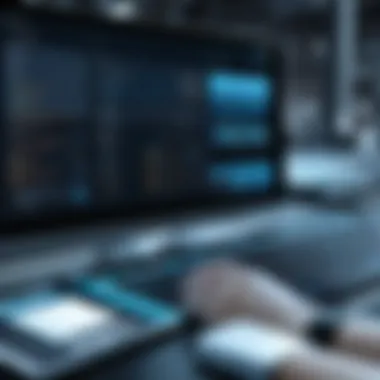
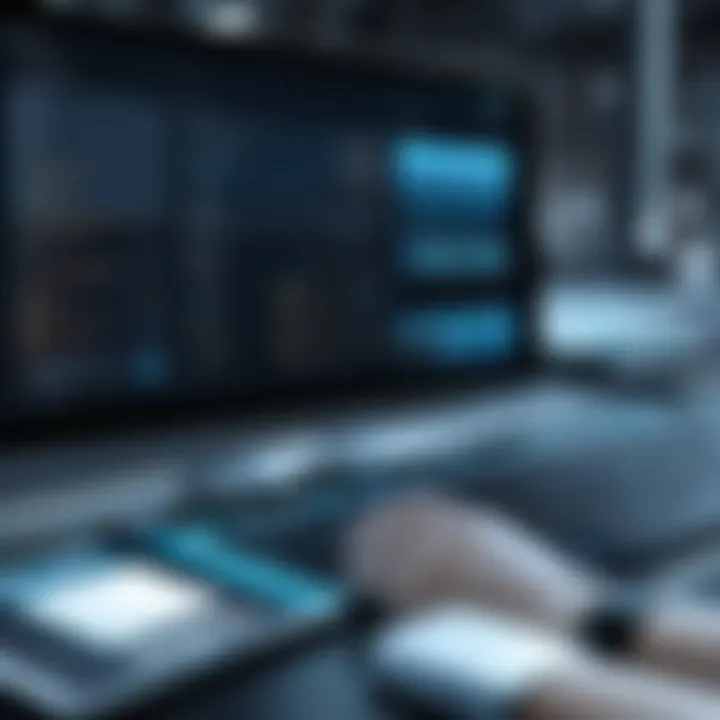
Intro
In an increasingly competitive manufacturing landscape, efficiency is paramount. Organizations need tools that streamline operations, optimize resources, and enhance productivity. JDA Factory Planner emerges as one such tool designed to meet these growing demands. This analysis looks closely at its multifaceted capabilities, offering a range of insights into its functions, benefits, and possible challenges that may arise in its deployment.
Software Category Overview
Definition and Importance
JDA Factory Planner is a specialized software solution that assists manufacturers in managing their production schedules and resources. It plays a crucial role in the orchestration of manufacturing processes. This tool integrates various components of production planning, allowing organizations to react swiftly to changes in demand and resource availability.
The significance of such software lies in its ability to minimize waste and maximize operational effectiveness. In today’s fast-paced environment, the right software can be the difference between meeting customer expectations and falling short of market demands.
Key Characteristics
JDA Factory Planner encompasses several core features that distinguish it in the realm of manufacturing software:
- Advanced Planning Algorithms: The software utilizes sophisticated algorithms that forecast demand and generate efficient production schedules.
- Resource Allocation: It facilitates optimal allocation of resources ensuring minimal downtime while maximizing throughput.
- Integration Capabilities: JDA Factory Planner can seamlessly connect with other enterprise solutions like ERP systems, enhancing its utility across various operational dimensions.
- User Interface: Its design prioritizes user-friendliness, enabling teams to navigate the functionalities with relative ease, even with minimal training.
Comparative Analysis of Top Software Options
Feature Comparison
When evaluating manufacturing planning tools, it is beneficial to compare features. Many tools on the market offer similar functionalities, but each has unique aspects:
- JDA Factory Planner: Focused on dynamic planning with real-time adjustments and extensive integration capabilities.
- SAP Integrated Business Planning: Known for its strong analytics but may be less flexible in terms of adjustment speed.
- Oracle Supply Chain Management: Offers robust functionalities but can be complex for users not well-versed in supply chain fundamentals.
Pricing Models
Understanding the pricing model is crucial for decision-makers:
- JDA Factory Planner generally employs a subscription-based model, allowing for flexibility in costs as business needs change.
- SAP solutions may come with higher up-front costs but offer extensive features that can justify the investment over time.
- Oracle tends to vary pricing depending on the scale of deployment, which may lead to budgeting complexities.
"Selecting the right planning tool can lead to transformational changes in efficiency and productivity within any manufacturing environment."
Epilogue
This exploration intends to illuminate the various facets of JDA Factory Planner. By understanding its functionalities and how it compares to competitor solutions, decision-makers can more effectively gauge its alignment with their operational goals. Comprehensive evaluations will aid organizations in making informed selections that enhance their production capabilities.
Prelims to JDA Factory Planner
The JDA Factory Planner serves a significant purpose in the realm of manufacturing and supply chain management. Its relevance stems from the growing complexity of production processes and the need for precise planning tools that can adapt to dynamic market conditions. In this section, we will explore the historical context of JDA Software Solutions and the specific aims of the Factory Planner tool.
Background of JDA Software Solutions
JDA Software, now known as Blue Yonder, was founded in 1985. It began with a focus on helping companies optimize their supply chain and logistics functions. Over the years, the company has developed a broad range of software solutions designed for various sectors, which include retail, manufacturing and distribution. As businesses have increasingly leaned on technology to improve efficiency, JDA has evolved, providing advanced predictive analytics and intelligent automation features within its applications.
The development of the Factory Planner was a response to industry demands for more effective production planning solutions. Companies faced unique challenges, such as fluctuating raw material prices, labor shortages, and stringent regulations. JDA recognized the necessity of helping organizations streamline their operations to stay competitive.
Purpose of Factory Planner
The primary aim of the JDA Factory Planner is to enhance production planning. It allows manufacturers to accurately forecast demand, optimize their production schedules, and allocate resources effectively. This software solution seeks to align production capabilities with market needs. The Factory Planner considers numerous variables, such as machine capacities, labor availability, and inventory levels, to provide a holistic view of the manufacturing process.
Furthermore, JDA Factory Planner assists decision-makers in making informed choices by presenting data-driven insights. By incorporating real-time data, it supports agile responses to changing conditions. In a world where market dynamics can shift rapidly, tools like the Factory Planner are essential for sustaining operational efficiency.
Overall, understanding the background of JDA Software Solutions and the purpose of the Factory Planner lays a crucial foundation for appreciating its features and benefits. This analysis aims to provide insights into how this software contributes to modern manufacturing landscapes.
Key Features of JDA Factory Planner
JDA Factory Planner stands out as a robust tool tailored for modern manufacturing needs. Understanding its key features provides insight into its potential impact on operations. In today’s highly competitive environment, firms must leverage sophisticated software solutions for production efficiency and agility. JDA Factory Planner addresses these challenges through its distinct functionalities.
Production Planning
Effective production planning is the backbone of any successful manufacturing process. JDA Factory Planner offers a comprehensive suite that allows firms to schedule and manage production activities effectively. The software uses advanced algorithms to optimize production schedules based on real-time data. This ensures timely fulfillment of orders while maximizing resource utilization. The solution integrates seamlessly with existing systems, enabling scenario planning and forecasting to account for variability in demand.
Key Benefits:
- Optimized Scheduling: Reduces lead times and enhances throughput by aligning production schedules with demand fluctuations.
- Scenario Analysis: Facilitates decision-making during disruptions, helping management to evaluate various outcomes based on input adjustments.
Inventory Management
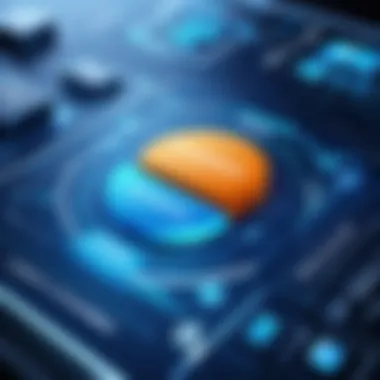
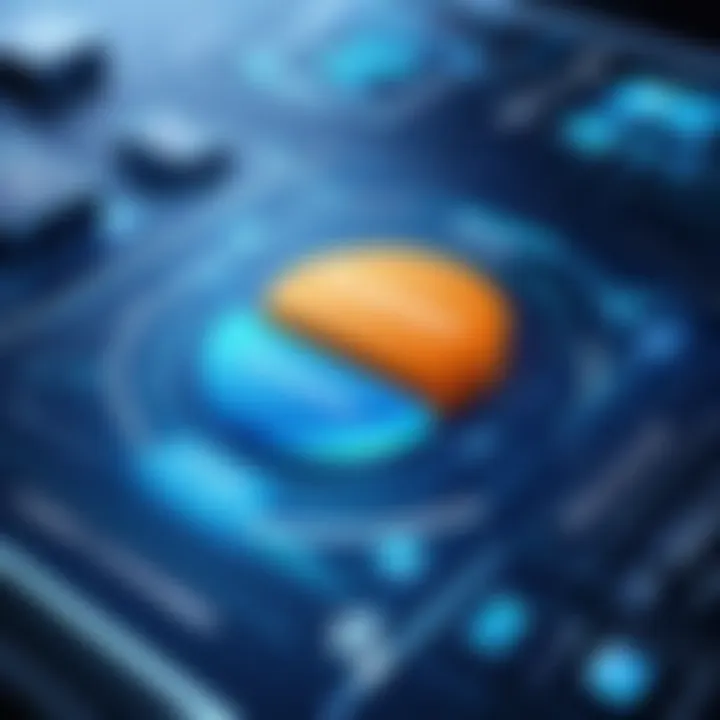
JDA Factory Planner provides powerful inventory management capabilities. This feature is critical for maintaining the delicate balance between supply and demand. Incorrect inventory levels can result in lost sales or increased holding costs. The software automates inventory tracking and replenishment processes, reducing human error while ensuring accurate stock levels.
Important Aspects:
- Real-Time Tracking: Allows insights into inventory levels, which helps in planning and minimizing wastage.
- Demand Forecasting: Integrates advanced analytics to predict future inventory needs, optimizing stock on hand.
Resource Allocation
Efficient resource allocation is vital for operational excellence. JDA Factory Planner assists businesses in optimally deploying human and material resources. By analyzing production workloads and resource availability, organizations can allocate resources where they are needed most. This feature enhances productivity and mitigates bottlenecks in the production process.
Noteworthy Features:
- Dynamic Resource Matching: Matches workforce skills with production demands, ensuring the right employees are assigned to the right tasks.
- Material Requirements Planning (MRP): Calculates the materials needed for production, aligning inventory levels with production schedules.
Performance Monitoring
A distinctive characteristic of JDA Factory Planner is its performance monitoring capabilities. This feature enables manufacturers to track key performance indicators (KPIs) that are essential for assessing operational efficiency. By offering real-time insights, the software allows decision-makers to identify trends and areas for improvement before they escalate into issues.
Elements to Consider:
- KPI Dashboards: Visual summaries of production metrics aid in quick decision-making.
- Alerts and Notifications: Automatic notifications for anomalies or underperformance support proactive management of operations.
Benefits of Implementing JDA Factory Planner
The implementation of JDA Factory Planner offers significant advantages that can enhance manufacturing processes and operational workflows. For decision-makers and stakeholders, understanding these benefits is crucial in determining the strategic fit of this software within their organizations. The following subsections outline key advantages derived from using JDA Factory Planner, focusing on elements such as operational efficiency, cost reduction, and improved decision-making processes.
Operational Efficiency
Operational efficiency refers to the ability of an organization to deliver high-quality products while minimizing waste and costs. JDA Factory Planner helps achieve this through advanced scheduling and planning tools. These features allow manufacturers to optimize production schedules, streamline workflows, and manage resources effectively.
- Real-time Data Utilization: JDA Factory Planner emphasizes real-time data analysis. This capability ensures that production decisions are based on accurate, up-to-date information, resulting in better responsiveness to market demands.
- Minimized Downtime: The platform's planning capabilities lead to fewer bottlenecks and reduced downtime. By identifying and resolving potential issues before they escalate, productivity levels can remain consistently high.
- Workflow Automation: Automated features in JDA Factory Planner enable repetitive tasks to be managed with minimal manual input. This reduces the likelihood of human error and allows employees to focus on higher-value tasks, ultimately improving overall efficiency.
Cost Reduction
Implementing JDA Factory Planner can lead to substantial cost savings for companies. In a competitive landscape, controlling operational costs is essential for maintaining profitability. Key factors contributing to cost reduction include:
- Optimized Inventory Management: The software aids in managing inventory levels efficiently. By closely monitoring stock levels and demand forecasts, manufacturers can reduce carrying costs and minimize excess inventory.
- Reduced Waste: By optimizing production processes, JDA Factory Planner helps identify areas where waste can be cut. This not only lowers costs but also contributes to sustainability efforts within the organization.
- Improved Resource Allocation: Effective resource allocation ensures that labor and materials are used efficiently. This maximizes the return on investment for each production run, leading to lower overall costs.
Enhanced Decision-Making
Enhanced decision-making is one of the most pivotal benefits associated with JDA Factory Planner. With robust analytics and reporting capabilities, the software provides insights that help managers make informed choices. Specific aspects include:
- Data Analytics Report Generation: JDA Factory Planner allows users to generate detailed reports. These can illuminate trends, inefficiencies, and areas for improvement, providing management with the necessary tools to make strategic decisions.
- Scenario Planning: The software supports scenario planning, allowing organizations to evaluate different strategies' potential outcomes. This foresight ensures that decisions made are well-informed and aligned with broader business objectives.
- Collaboration Tools: Enhanced communication features facilitate collaboration across teams, contributing to a unified decision-making process. All stakeholders can access relevant data and insights, ensuring that decisions reflect a comprehensive understanding of the production landscape.
Investing in JDA Factory Planner is not just about adopting a software; it is about transforming how an organization approaches manufacturing challenges.
In summary, the benefits of implementing JDA Factory Planner are manifold. From driving operational efficiency to achieving cost savings and enhancing decision-making capabilities, the software equips organizations to navigate the complexities of modern manufacturing with greater ease and effectiveness.
Technical Specifications of JDA Factory Planner
Understanding the technical specifications of JDA Factory Planner is vital for several reasons. These specifications outline the framework that enables effective operation within various manufacturing environments. By thoroughly assessing these components, decision-makers can determine how well the software aligns with their organizational needs.
System Requirements
The system requirements for JDA Factory Planner are critical to ensure optimal performance. The software demands a robust hardware configuration, which typically includes:
- A multi-core processor to handle complex calculations and data processing.
- A minimum of 16 GB of RAM, providing adequate memory for running multiple processes simultaneously.
- Sufficient storage capacity, usually at least 500 GB of SSD, to facilitate quick access to data.
- A reliable network connection, as data exchange often occurs in real-time.
Operating System Compatibility is another key aspect. JDA Factory Planner integrates seamlessly with Windows servers and occasionally supports Linux environments as well. Proper alignment with these requirements can lead to enhanced system speed and user satisfaction.
Integration Capabilities
Integration capabilities are indispensable for a manufacturing software solution like JDA Factory Planner. The software is designed to work harmoniously with other enterprise systems. Key integrations typically include:
- ERP Systems: Integration with enterprise resource planning solutions like SAP or Oracle ensures that data flows smoothly across departments.
- Supply Chain Management Tools: Linking with these tools allows for better coordination of inventory and procurement processes.
- Shop Floor Systems: This capability helps in monitoring real-time production activities and unlocking insights into performance and efficiency.
The JDA Factory Planner also supports application programming interfaces (APIs) that allow custom integrations, enhancing flexibility and adaptability. This aspect is especially beneficial for organizations already using tailored systems to meet specific operational requirements.
User Interface Design
The user interface design of JDA Factory Planner plays a significant role in user adoption and effectiveness. An intuitive layout can greatly reduce the learning curve for new users. Key features of the user interface include:
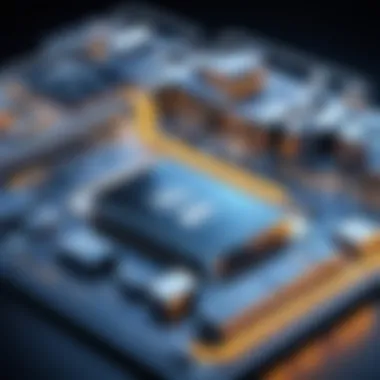

- Dashboard Customization: Users can create personalized dashboards, enabling quick access to critical metrics and information.
- Visual Analytics: Tools for data visualization help stakeholders interpret complex data, empowering better decision-making.
- Responsive Design: This ensures compatibility across different devices, allowing managers to monitor processes from anywhere.
User feedback often highlights the software's straightforward navigation, which simplifies complex processes and aligns with the diverse needs of various users in the manufacturing sector.
"Understanding technical specifications is essential for ensuring that JDA Factory Planner not only fits the current landscape of an organization but also has the potential to scale with growth."
In summary, these technical specifications serve as a benchmark for evaluating the software's usability and effectiveness. Each component—system requirements, integration capabilities, and user interface design—contributes to the overall functionality of JDA Factory Planner, making it a favorable choice for modern manufacturing operations.
User Experiences and Case Studies
Understanding user experiences and examining case studies is critical when evaluating JDA Factory Planner. These elements offer insight into the practical application of the software in real-world contexts. They reveal how organizations have utilized the tool to overcome various challenges, optimize their operations, and enhance overall performance. Moreover, they provide a nuanced view, illustrating both the successes and limitations users have encountered. Such knowledge can guide potential users in assessing whether JDA Factory Planner aligns with their specific needs and operational goals.
Industry-Specific Applications
JDA Factory Planner finds application across a multitude of industries, each benefiting from its tailored capabilities.
- Manufacturing: In manufacturing, the software assists in coordinating intricate production schedules, ensuring optimal resource utilization while meeting demand. It supports complex product structures, which is vital for industries that produce goods in various configurations.
- Retail: Retailers leverage the planner to synchronize inventory levels with forecasted sales. This ensures product availability while minimizing excess stock. Effective inventory management is essential in retail where consumer preferences can shift rapidly.
- Automotive: In the automotive sector, JDA Factory Planner helps in synchronizing parts manufacturing with vehicle assembly. This coordination is paramount in a just-in-time production environment, where delays in component delivery can lead to significant losses.
The flexibility of JDA Factory Planner allows it to cater to diverse process requirements, adapting to different industry standards and operational nuances.
Success Stories
User success stories provide compelling evidence of the capabilities of JDA Factory Planner. Numerous organizations have reported substantial improvements in operational efficiency and decision-making capabilities after its implementation.
For instance, a large manufacturing company noted a 20% reduction in production lead times due to enhanced planning capabilities. By effectively linking production schedules with inventory management, they minimized downtime, thus increasing throughput. Another example involved a retail company that improved sales forecasting accuracy by 30%, enabling better compliance with customer demand and reducing inventory costs significantly.
These examples illustrate how JDA Factory Planner can transform operational processes, yielding measurable business outcomes.
Challenges Faced by Users
While JDA Factory Planner offers many benefits, users have encountered some challenges that warrant attention.
- Implementation Complexity: One common issue is the complexity involved in implementing the JDA Factory Planner. Depending on existing systems, the integration process can require considerable time and resources.
- User Adoption: There may also be resistance to change from employees accustomed to traditional processes. Comprehensive training and support are essential for smooth transitions and effective use of the software.
Furthermore, some users report the need for more customization options, particularly those with unique operational processes. Organizations must assess their specific requirements against the capabilities offered by JDA to ensure a good fit.
Effective use of JDA Factory Planner hinges on understanding the unique needs of the organization and thorough planning during the implementation phase.
By analyzing user experiences and case studies, decision-makers can make informed choices about integrating JDA Factory Planner into their operations. This understanding can help optimize workflows and minimize resistance during the implementation phase.
Potential Drawbacks of JDA Factory Planner
Understanding the potential drawbacks of JDA Factory Planner is essential for organizations contemplating its implementation. While the software offers numerous benefits, keeping in mind its limitations allows decision-makers to make informed choices. Exploring these drawbacks sheds light on critical areas that may require attention before and after adoption. This section focuses on two primary concerns: the complexity involved in implementation and the associated costs.
Implementation Complexity
The implementation of JDA Factory Planner can be a challenging process. Organizations often face hurdles such as the need for extensive data migration from existing systems and the integration with current software solutions. This complexity arises from various factors, including the size of the operation and the existing IT infrastructure. The following points highlight the main challenges:
- Training Needs: Staff may require significant training to adapt to the new system. The learning curve can lead to temporary drops in productivity as employees familiarize themselves with the software.
- Customization Requirements: Many businesses need to tailor the software to fit specific operational needs. This customization often necessitates additional time and resources, leading to extended project timelines.
- Resistance to Change: Employees may resist shifting from familiar systems to a new platform, complicating the change management process. Addressing these psychological barriers is crucial for a smooth transition.
"Successful implementation is not solely about technology; it also requires effective change management and communication strategies."
In summary, while JDA Factory Planner can enhance operational efficiency, the implementation phase demands careful planning and execution. Addressing these factors early can help mitigate potential setbacks.
Cost Considerations
Cost is a critical factor in evaluating JDA Factory Planner. While the software can deliver substantial long-term benefits, the initial investment may raise concerns among decision makers. Key aspects to consider include:
- Licensing Fees: Organizations must contemplate the ongoing licensing fees, as these can accumulate over time. Understanding the pricing structure is crucial to predicting budget impacts.
- Additional Costs: Beyond licensing, costs can include hardware upgrades, integration with other systems, and potential consultancy fees for implementation.
- Maintenance Expenses: Regular maintenance is necessary to ensure optimal performance. This translates into ongoing expenses, which can strain budgets if not properly planned for.
Comparative Analysis with Other Software Solutions
In today's rapidly evolving technological landscape, a robust comparative analysis of software solutions is critical for organizations aiming to optimize their manufacturing operations. This section focuses on understanding how JDA Factory Planner stands against its primary competitors: SAP, Oracle, and Infor. By evaluating these systems, decision-makers can better navigate their options and make informed choices that align with their operational strategies.
JDA vs. SAP
SAP, a leader in enterprise resource planning, offers a comprehensive suite of software solutions. When comparing JDA Factory Planner to SAP, several factors come into play:
- User Experience: JDA is often praised for its user-friendly interface, which can reduce training time for staff. In contrast, SAP’s complex functionalities might require extended training.
- Functionality: JDA specializes in production planning, making it a strong fit for manufacturers with optimized needs in this area, while SAP's broader focus on ERP may dilute specific manufacturing functionalities.
- Flexibility: JDA allows more customizable options, catering to the specific needs of manufacturing processes. SAP can be rigid, requiring more substantial changes for custom needs.
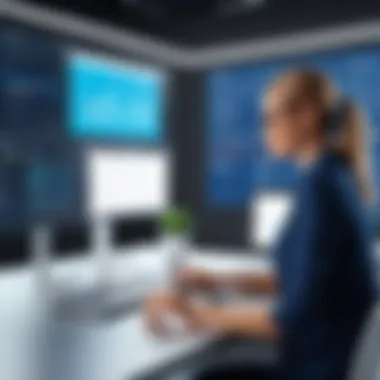
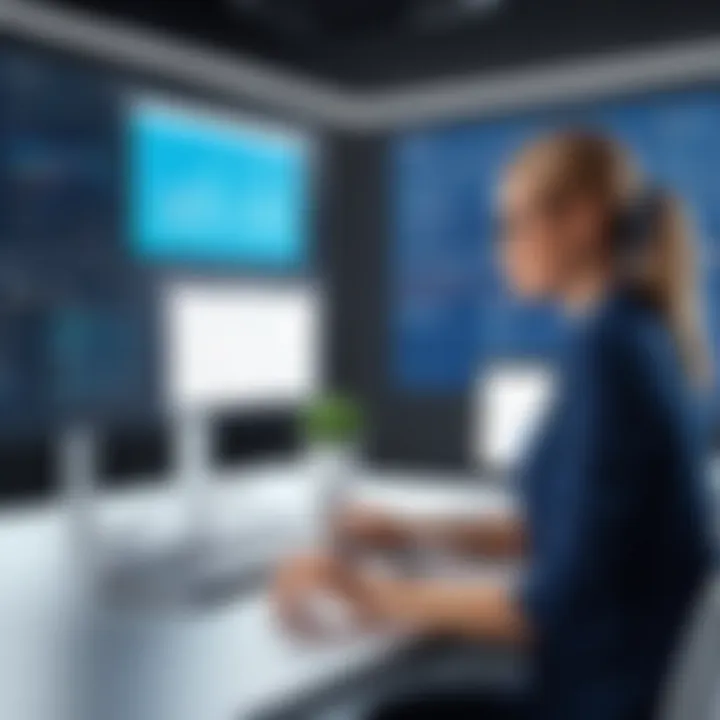
JDA vs. Oracle
Oracle is renowned for its strong database capabilities and cloud solutions. Comparing it to JDA, the following points emerge:
- Integration: Both JDA and Oracle allow integration with various systems. However, Oracle's integration often depends on its extensive database structures, which may not suit every manufacturing environment. JDA's flexibility means it can integrate seamlessly with existing setups.
- Cost: JDA generally offers a more affordable entry point for smaller manufacturers, whereas Oracle can present higher upfront costs, making it less appealing for budget-conscious businesses.
- Implementation Time: JDA's installation and onboarding processes typically take less time than Oracle’s, allowing for a quicker return on investment.
JDA vs. Infor
Infor focuses heavily on vertical solutions tailored to specific industries. In comparing it to JDA, several important considerations arise:
- Industry-Specific Solutions: Infor may provide targeted solutions for niche markets, while JDA is more generalized yet highly efficient in planning and scheduling.
- Technology Stack: JDA’s reliance on modern technologies, such as cloud computing, may appeal to businesses looking for up-to-date solutions. Infor's offerings can sometimes lean on older technology, which could pose risks for future scalability.
- User Adoption: JDA benefits from easier user adoption due to its intuitive design. Infor may require more effort in change management for users to become accustomed to the system.
"Understanding the dynamics between various software solutions is key to selecting the right one that meets operational needs and long-term goals."
Best Practices for Effective Use
Understanding best practices for utilizing JDA Factory Planner is essential for maximizing its capabilities. Implementing the software effectively can significantly enhance operational performance and lead to better decision-making processes. Companies can foster a more reliable production environment by embedding sound practices into daily operations.
Training and Support
Investing in training for staff is crucial when introducing JDA Factory Planner. Without proper knowledge, even the most powerful software can become underused or mismanaged. Organizations should consider comprehensive training programs that cover the software’s various functionalities. This includes production planning methods, inventory management techniques, and effective resource allocation strategies. Providing hands-on sessions can enhance understanding and retention. Moreover, involving key personnel in support roles ensures ongoing assistance.
Additionally, setting up a support framework is vital. Technical issues can arise unexpectedly, hindering productivity. A responsive support system enables users to resolve problems quickly and efficiently. Functions like help desks, user forums, or regular Q&A sessions can help keep users engaged and informed.
Regular Updates and Maintenance
Regular software updates are important for the effective operation of JDA Factory Planner. The technology landscape is rapidly evolving. Hence, staying current with updates ensures users have access to the latest features and security enhancements. Failing to implement updates may cause compatibility issues which could hamper system efficiency.
Organizations should establish policies for routine maintenance checks. This includes reviewing data accuracy, system integrations, and functionality assessments. Scheduled audits can help identify potential problems early on, allowing for timely interventions.
By consistently applying these best practices, organizations can provide an optimized experience with JDA Factory Planner. The result is improved productivity, reduced errors, and comprehensive decision-making capabilities, ultimately leading to enhanced competitive advantage.
Future Trends in Factory Planning Software
The landscape of factory planning is rapidly evolving, driven by advancements in technology and changing market demands. Understanding these trends is essential for any organization looking to maintain a competitive edge. This section outlines major trends affecting factory planning software, particularly Artificial Intelligence integration and Cloud Computing adoption. Both elements bring advantages that can significantly enhance operational efficacy and decision-making processes.
Artificial Intelligence Integration
Artificial intelligence (AI) is reshaping factory planning in numerous ways. Its ability to analyze large datasets in real time offers unparalleled insights into production processes. AI can optimize scheduling by predicting equipment failures, thus reducing downtime. In addition, AI-enhanced forecasting can provide more accurate demand predictions, enabling manufacturers to adjust their production strategies accordingly.
Introducing AI into factory planning can lead to the following benefits:
- Improved Efficiency: Automated processes can reduce human error and streamline workflows.
- Data-Driven Decisions: Insights generated by AI can assist managers in making informed decisions, increasing overall productivity.
- Predictive Maintenance: AI systems can foresee equipment malfunctions, allowing for timely maintenance and preventing costly delays.
Implementing AI isn't without challenges. Companies must invest in training staff to understand AI tools and ensure that data privacy measures are in place to protect sensitive information. A strategic approach to integrating AI can ultimately lead to a more responsive and adaptive manufacturing framework.
"Incorporating AI not only streamlines processes but also paves the way for smart factories, where data-driven decisions drive productivity."
Cloud Computing Adoption
Cloud computing has emerged as an integral component of modern manufacturing. It provides flexibility and scalability, essential for managing complex supply chains and fluctuating demands. The cloud allows companies to access their information from anywhere, facilitating remote work and collaboration between teams.
Key considerations regarding cloud computing in factory planning include:
- Cost Efficiency: Cloud solutions often reduce the cost associated with traditional hardware.
- Real-Time Collaboration: Teams can work together regardless of location, enhancing communication and speeding up decision-making processes.
- Scalability: As a business grows, cloud solutions can be adjusted to meet expanding needs without significant upfront investments.
Despite the undeniable advantages of cloud computing, businesses must navigate issues like cybersecurity and the transition period from on-premises solutions to cloud services. With a cautious approach, organizations can harness the benefits of cloud computing while managing risks associated with it.
In essence, both AI and cloud computing represent a shift towards more intelligent, flexible, and efficient factory planning processes. Companies adopting these trends stand to gain considerable advantages in the fast-paced manufacturing environment.
Culmination
The conclusion serves a vital role in contextualizing the findings and implications of JDA Factory Planner within the spectrum of modern manufacturing solutions. It encapsulates the core insights garnered from the detailed examination throughout the article, reinforcing the practicality and relevance of the software in today's dynamic environment.
Summary of Key Insights
In reviewing the key elements, a few insights surface prominently:
- Versatility: JDA Factory Planner presents an adaptable solution that caters to various industry needs, making it relevant across different types of manufacturing scenarios.
- Enhanced Efficiency: The software’s robust capabilities, especially in production planning and resource allocation, can significantly heighten operational efficiency.
- Integration: It integrates smoothly with other tools, a critical factor for organizations operating within complex ecosystems.
- User Experience: Real-world experiences showcase a variety of industry-specific applications, highlighting both successes and common challenges faced by users.
Collectively, these insights show how JDA Factory Planner not only addresses current operational challenges but also prepares businesses for future developments in manufacturing.
Final Thoughts on JDA Factory Planner
Ultimately, the JDA Factory Planner stands out as a comprehensive tool that aligns with the evolving needs of manufacturing processes. Its potential to improve decision-making and foster operational efficiencies cannot be overstated. Organizations looking to enhance production capabilities must consider the strategic advantages it conveys. However, it is imperative to also acknowledge the complexities and costs associated with implementation. Careful planning and resource allocation are necessary to truly harness its benefits.
As the landscape of factory planning continues to evolve, JDA Factory Planner remains a critical player. Decision-makers and IT professionals should engage with its offerings to assess its fit within their operational frameworks, ensuring they are well-positioned to capitalize on the benefits of advanced planning technologies.